今回は、駆動軸の締結方法について考えます。
代表的な駆動軸の締結方法としては、駆動軸に負荷を直接取り付ける方法やカップリングを介して取り付ける方法が考えられます。どちらの場合にも、駆動軸との締結部にはキーや割り締め(スリット)、またメカロックといった動力伝達要素を使用します。
これらの締結方法を動力伝達方式で分類すると、キーによる動力伝達か、摩擦締結による動力伝達かの2つにわけることが出来ます。
最も一般的に使用されるキー締結ですが、問題点もあります。よくある事例についてメカロックを使用して解決する方法を考えていきたいと思います。
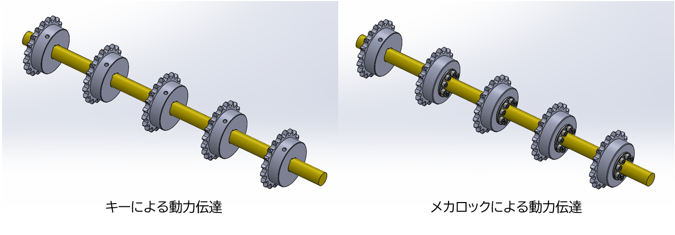
【図1】キーによる動力伝達とメカロックによる動力伝達の例
目次
1.キーによる動力伝達の構造
キーによる動力伝達は長く使用されてきた方法です。特に動力伝達では平行キーが使用されます。
インダクションモーターや減速機の出力軸にはキー溝加工が施されているものが多く、スプロケットやタイミングプーリー等を簡単に取り付けることができるようになっているものが多くあります。
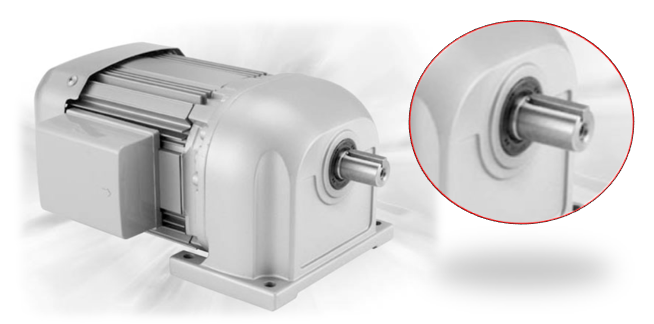
【図2】ギアモーターの出力軸
参考:MISUMI(総合Webカタログ)「ギヤードモータ GM-Sシリーズ」
キーによる動力伝達の仕組みは、軸側とボス側のキー溝に挿入されたキーをせん断する力により伝達されます。軸径によって、使用する平行キーのサイズはJISにより規格化されています。
したがって、図3のようにせん断面積は「キーの長さ×幅」となるので、伝達トルクからせん断力を計算し、キーの長さを決めます。モーターや減速機の出力軸はそれを加味した寸法となっています。締結部の設計では、キーの長さ全部を使って伝達する設計にすることを心掛けてください。
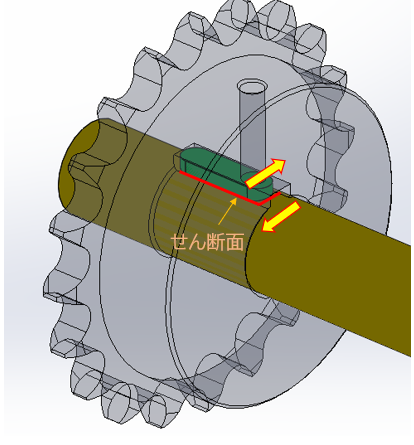
【図3】キーのせん断
2.メカロックによる動力伝達の原理と構造
メカロックは摩擦締結による動力伝達方法です。
内部構造は【図4】のようになっており、円周上に配置されたボルトを締め付けることで、クサビが動き、内輪側と外輪側のリングをそれぞれ軸とボスに押さえつけることで大きな摩擦力を発生させます。許容伝達トルクは型式毎にカタログに記載されていますので、そちらを参照して選定を行います。
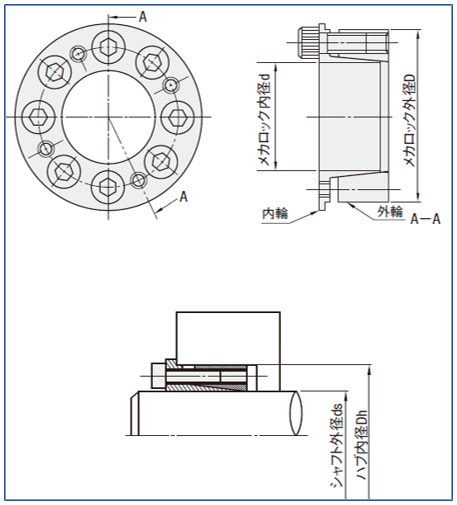
【図4】メカロックの構造
参考:MISUMI(総合Webカタログ)「メカロック スタンダードタイプ」
また、軸及びメカロック挿入部のボスは丸穴加工だけで良いので、キー締結と比較して加工工数も少なくなります。
ただし、強い力で押さえつけますので、ボス側の肉厚が薄いと弾性変形してしまい、摩擦力が小さくなって所定の性能(伝達トルク)を発揮することができません。代表的な材質での最小肉厚寸法もカタログに記載されているので、設計の際には必ず確認をしてください。
一例を図5に示します。
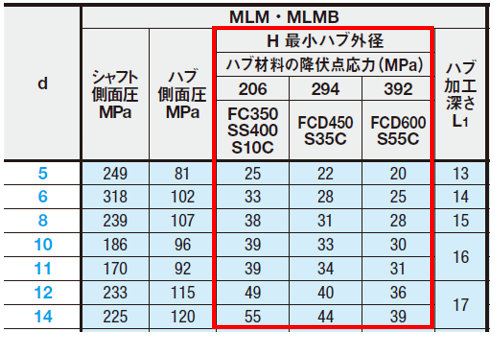
【図5】ボス側の最小肉厚(MLM・MLMB)
材料の降伏応力が低い軟鋼(SS400,S10C)では、ハブの肉厚を厚くしないと、力が逃げてしまい、締結に必要な摩擦力が得られません。硬鋼(S55Cなど)では降伏点応力が高いので、肉厚が薄くても十分な摩擦力が得られます。
3.メカロックの使用方法(取り付け、取り外し)
メカロックは【図4】のように内輪と外輪がロックボルトで繋がっています。
取り付けはロックボルトを緩めた状態で軸とボスに挿入します。この時、ボス側のスプロケットやプーリーには荷重が掛かっていないようにしてください。
挿入後、ロックボルトを対角線方向に順番に締め付けていきます。一度に強く締め付けるとバランスが悪くなり、正しく締結が出来ません。全体を3~4周するような感じで締め付けていくとよいでしょう。
取り外しは、まずスプロケットやプーリーに掛かっているテンションを緩めてください。
テンションが掛かったままだとロックボルトは緩められますが、メカロック内部のクサビ部分の噛み合いを緩めることができません。スプロケット等にテンションが掛かっていない状態に出来たら、ロックボルトを緩めてください。緩める場合には順番はありませんので、好きな順番で緩めて構いません。
緩めても、ほとんどの場合、軸とボスの締結は解かれていないと思います。これは、メカロックのクサビ部分の噛み合いがまだ生きている状態で、ロックボルトだけが緩んで抜けてきた状態になっています。ここから、クサビの噛み合いを解いていきます。
図6のように、ロックボルトの間にねじ穴が4ヶ所(小さいサイズでは2ヶ所)あいています。このねじ穴が抜きタップになっていますので、ねじ穴の隣にあるロックボルトを外して挿入します。
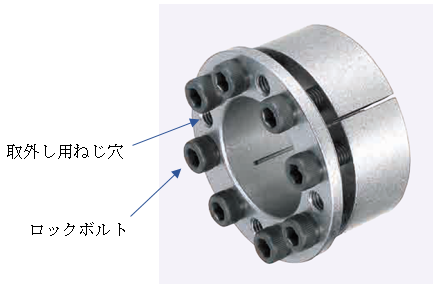
【図6】ロックボルトと取り外し用ねじ穴
均等に締め込んでいくと、「コンッ」という感じの衝撃があり、クサビの噛み合いが解かれます。冒頭でも言いましたが、テンションが掛かっていると、クサビに力が掛かったままになり、噛み合いが解けません。
取り外し用ねじ穴のボルトを締めすぎて、メカロックを破損する場合もあるので、注意してください。
4.キーを使用した場合に起きるトラブル事例
キーを使用した場合のトラブルは色々と考えられますが、中でも代表的な事例を2つ紹介しておきます。
【事例1】長い軸に多数のスプロケットやタイミングプーリーを取り付けた際の位相ずれ
幅広の搬送コンベア等では、前掲の【図1】のように、長い駆動軸の何カ所かにスプロケットやタイミングプーリーを取り付ける構造とする場合があります。
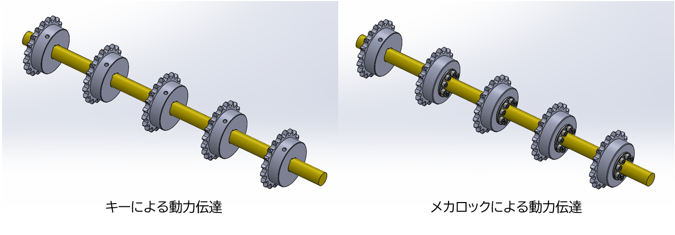
【図1】キーによる動力伝達とメカロックによる動力伝達の例(再掲)
他には、リフター等では軸の両端にレバーを取り付けてレバーの動作で昇降させることがあります。この時、全てキーを使用して動力伝達すると、駆動軸にはキー溝加工をスプロケットの数だけすることになります。
【図1】の左側の例でシャフトだけ取り出すと、【図7】のようになっています。
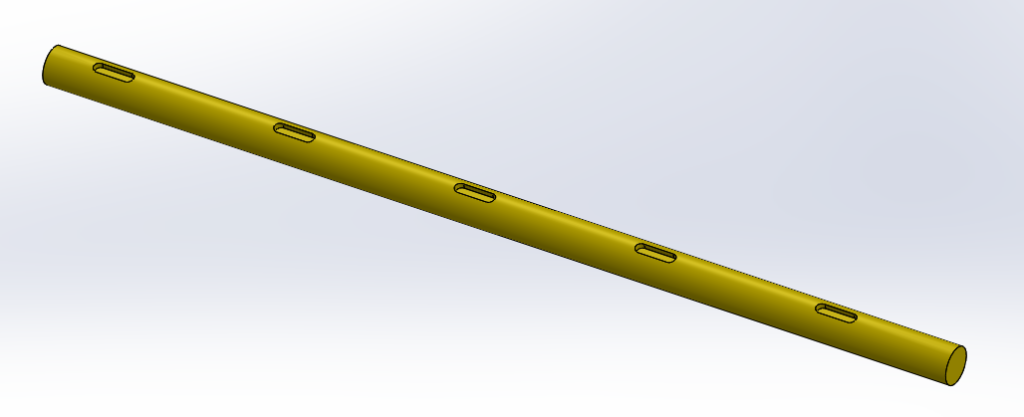
【図7】全てキー締結するシャフト
このシャフトの図面の作図をするとキー溝の図示はすべて同軸上に記載しますが、実際に加工する際にはどのような加工方法となるでしょうか。
軸へのキー溝加工はフライスで行うのが一般的ですが、ベッドのストロークや作業性によってはワーク(この場合は軸)をクランプし直して加工します。
クランプし直すということは、軸が回転してクランプされ、キー溝の円周方向への位置ずれが起きます。作業者がクランプしているので、このずれをゼロにすることは出来ません。
このまま使用した場合、アタッチメント付きチェーンやタイミングベルトでは、アタッチメントの位置が揃わず、正しく搬送出来ません。また、リフターの場合では、レバーの位相がずれますので、水平にならなかったり、片側のレバーに負荷が集中したりします。
【事例2】衝撃荷重を受ける軸
クラッシャーやシュレッダーなどの粉砕機では、粉砕物の噛み込みが一定ではないので、駆動軸には衝撃荷重が発生します。
衝撃荷重により、大きな力が繰返し加わることにより、キー溝が変形し、キーとキー溝の間にガタが発生します。ガタが大きくなると、設計した通りの動きが出来なくなり、機能を十分に発揮できなくなります。また、軸が変形すると、メンテナンス作業で軸をボスから抜くことができなくなり、分解できなくなります。
5.キーのトラブルをメカロックで解消する
前項のトラブルはメカロックを用いることにより、解消することが出来ます。
【事例1】長い軸に多数のスプロケットやタイミングプーリーを取り付けた際の位相ずれの解消
このケースでは、キー溝加工時の問題で位相ずれが発生しました。加工時にワークをクランプし直すと必ず発生する問題であるので、設計段階で対策しておくべき問題です。
加工指示で「同一線上に加工」や「位相ずれなきこと」と指示をする方法もありますが、この指示による加工の場合、複合機や大型の加工機を使用することになり、納期やコストが掛かります。
このような場合には、基準とするスプロケットは―キー締結として、それに従動するスプロケットはメカロックを使用して固定します。
メカロックは摩擦締結ですので、キーのように位相が固定されることはありません。【図1】の右側がこのような取り付け方法にしています。
この場合のシャフトは【図8】のようになります。
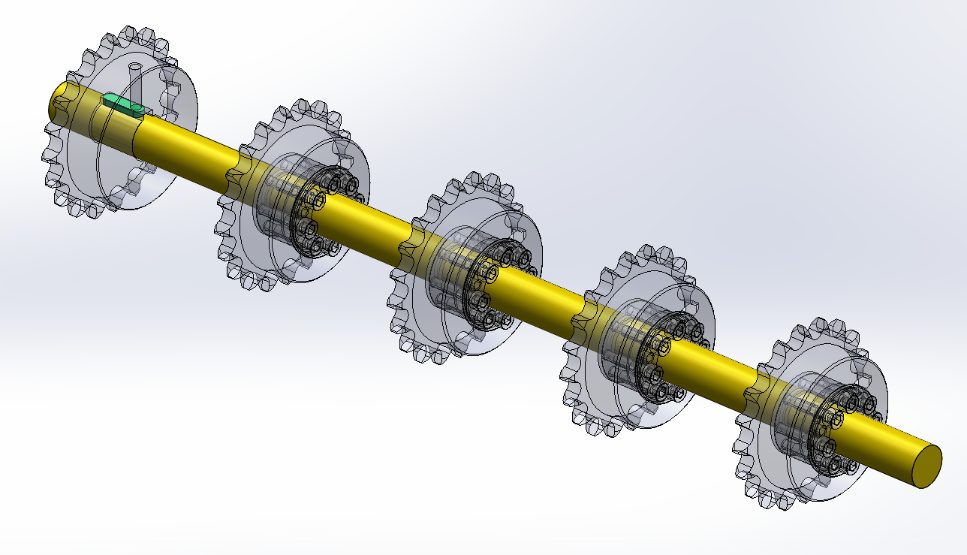
【図8】メカロックを使用する場合のシャフト
基準とするスプロケットはキー締結、それ以外のスプロケットはメカロックで締結します。したがって、軸へのキー溝加工は1ヶ所のみとなります。
【事例2】衝撃荷重を受ける軸への対策
前述のとおり、キーを使用した締結では、衝撃荷重などの大きな荷重を繰り返し受けると、キー溝の変形やキー材の破損が発生します。このような場合、キー溝に焼入れをして表面硬度を上げるような対策を取る方法もあります。
出力軸が中空の減速機と駆動軸の締結はどうしてもキーによる締結となるので、仕方ないですが、中実軸とアクチュエーター等の接続部ではキーの代わりにメカロックを使用するとこのような問題は解消されます。また、メカロックの許容伝達トルクが決まっているので、過負荷を防止するトルクリミッタの役割も果たしてくれます。
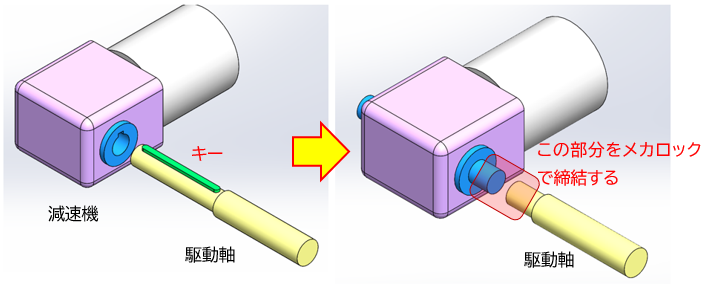
【図9】減速機出力軸との接続方法
6.まとめ
今回は駆動軸の動力伝達の方法として、キーを使用した時に発生する問題点である位相ずれと衝撃荷重によるキー溝の変形について考え、解決策としてメカロックを利用するという結論に達しました。
キーはコンパクトでシンプルな動力伝達の手段ではありますが、キー溝とキーの間でのせん断力で動力伝達を行うため、そこに負荷が集中します。そのため、衝撃荷重などの大きな荷重が加わるとキー溝の変形などが発生しやすくなります。
また、長尺のシャフトにキー溝の加工をする場合、位相合わせは出来ないと考えておくべきです。
このようなキー締結の問題を解消するのがメカロックです。
メカロックは摩擦締結による動力伝達ですので、軸側にキー溝のような加工を行いません。したがって、キー溝の変形も発生しませんし、位相合わせも自在に行えます。ただ、全部をメカロックにすると基準が分からなくなるので、基準とするものだけキーにするとよいと思います。
まとめると、キーを使用する場合の注意点は次のようになります。
※フライス加工の際、ワークであるシャフトのクランプが1回では済まない。
これに対して、メカロックの利点は次のようになります。
2.軸にキー溝加工が不要なので、加工費の削減が可能。
3.許容伝達トルク以上の負荷が掛かると、滑るので、トルクリミッタの役割を持つことができる。
4.バックラッシがゼロなので、精密位置決めが可能。
キー、メカロックともにメリット、デメリットがあります。用途に合わせて選択するようにしてください。
次回は、マニホールド電磁弁の構造と発生する不具合と回避方法について考えていきます。
それではまた。