第10回では、ボールネジを使用した搬送装置で「搬送速度を速くしたい」という要望に対して、「ボールネジの回転数を上げる」という解決策を考えました。この場合には「危険速度(危険回転数)」の検討が必要であるということが分かりました。
今回は「装置(サーボモーター駆動部)の運転パターンを変更したい!」というお客様の要望に対し、その注意点と検討事項を見ていきます。装置改造せずにタクトタイム短縮するには、運転パターンの変更が必要になります。このような場合にはモーターの負荷が変わってきます。ここではモーターの実効負荷トルクについて考えています。
【図1】はシリーズ第7回までの間に設計した搬送装置ユニットです。X軸のモーターは200Wで設計しましたが、容量に余裕があったので、再検討し50Wに変更してあります。モーター仕様については【表1】に記載します。
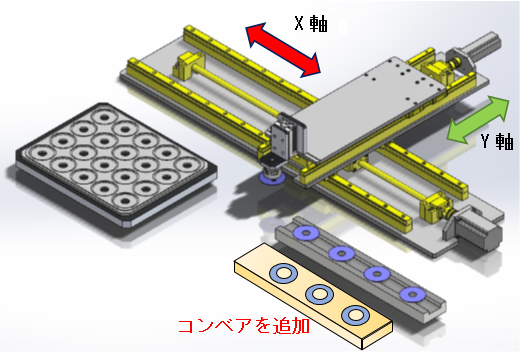
【図1】ボールネジ駆動の搬送装置ユニット
【表1】X軸サーボモーター仕様
定格出力 | W | 50 |
定格回転数 | min-1 | 3000 |
最高回転数 | min-1 | 6000 |
定格トルク | N・m | 0.159 |
最大トルク | N・m | 0.557 |
慣性モーメント | ×10-4 kg・m2 | 0.0395 |
今回、上流設備の改修が行われ、ワーク供給条件が変更になりました。現状の供給コンベアと同じコンベアが1台追加され、単位時間当たりのワーク供給量が増加となります。(【図1】中に記載した橙色部分)。
そして、増加した供給量に対応するために搬送装置をもう1台設置したいのですが、装置レイアウトの制約から現状では設置することができません。恒久対策は後々に行うものとして、現状での対策は、X軸の加速時間を0.2秒から0.1秒に変更することにします。こうすることで、タクトタイムは1/2まではならなくとも60%程度にすることは可能であろうと思います。時間当たり処理量としては、約1.5倍になります。
このように装置を改造すると、タイムチャートも変わってきます。こうした場合にはタイムチャートをもう一度作成し、実効負荷トルクの検討を行います。
ここでは、タイムチャートの作成からすると、長くなるので、実効負荷トルクの検討のみを見ていくことにします。
目次
1.実効負荷トルクとは
自動化された機械は一般的に1つのワークに対しての処理で1サイクルの動作を行います。これに必要な時間がタクトタイムとなります。この1サイクルの間に、モーターは止まっていたり、回転したり、また回転していなくてもワークを支えるために力(トルク)を発生させています。
この1サイクルの間にモーターがどのくらいのトルクを発生させているか平均値を求めたものが実効負荷トルクになります。
実効負荷トルクがモーター定格トルクに収まっていればオッケーですが、収まっていない場合はモーターの再選定を行います。
計算の精度にもよりますが、実効負荷トルクがモーター定格トルクを超えている場合、ほぼ確実に装置運転中にエラー停止します。
生産計画に重大な影響が出ることになり、設計者としては絶対に避けたい事案です。
2.実効負荷トルクの計算が必要なケース
実効負荷トルクの計算は時間がかかるので、全ての場合において計算をすると設計時間が長くなってしまいます。明らかにモーター容量に余裕がある場合は計算する必要はありませんが、目安として下記に当てはまる場合は必ず計算をしてください。
- 負荷トルクが定格トルクの80%以上になっている。
- 加速トルクが定格トルクの100%以上になっている。
- 加速、減速の回数が多い。
1~3のいずれか1つでも当てはまる場合は実効負荷トルクを求めてください。2つ当てはまる場合はエラー停止する可能性がかなり高いです。
3. 実効負荷トルクの計算
実効負荷トルクは下記の計算式で求めることができます。
つまり、モーターの運転状態それぞれのフェーズにおける二乗平均平方根のようなものを求めます。二乗していますので、計算結果は必ず正(+)の値をとります。
簡単な例で見ていきたいと思います。
【図2】はタイムチャートから加減速時間が0.2秒、走行速度250mm/s、移動距離140mmの動作時を抜き出してきたものです。
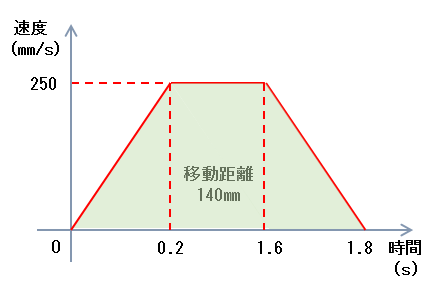
【図2】走行時のタイムチャート(抜粋)
水平走行の場合で考えると、モーターが大きなトルクを発生させるのは、加速時と減速時になります。一定速度で走行している間は加速度が存在しませんので、リニアガイドを使用した装置では摩擦が少ないので、トルク(負荷トルク)はほとんど必要ありません。
加速時と減速時のトルク(加速トルク、減速トルク)を求めてみたいと思います。第5回「サーボモーターを選定してみよう」で紹介した計算式を使います。
第5回では200W で計算をしましたが、モーターが変更されているので、再計算します。モーターのみ変更されていますので、第5回で計算した内容から変更になる部分を赤字で記載します。
変更となるのは、モーター慣性モーメントのみとなります。
モーター定格トルクが0.159 N・mですので、この条件ではモーター定格トルクの55%程になります。実効負荷トルクを計算する必要はありませんが、計算の手順を確認するためにこのまま計算を進めていきます。
上で示した実効負荷トルクの計算式に当てはめていきます。
モーター定格トルク内に十分収まっていることが分かります。実際には1サイクルの間について考えますので、タイムチャートから動作を確認し、1サイクルの間の総和を求めます。
加速時間を変更するとどうなるか
では、加速時間を0.1秒にした今回の場合を考えてみたいと思います。
実効負荷トルクが大きくなる運転パターンは装置が停止もしくは一定速度で移動している時間がサイクルの中で短い場合になりますので、そのような場合を考えます。そうすると、搬送距離が一番短くなる条件、つまりコンベアから一番近い位置にワークを置きにいくケースになります。
この時の実効負荷トルクを求めていきます。
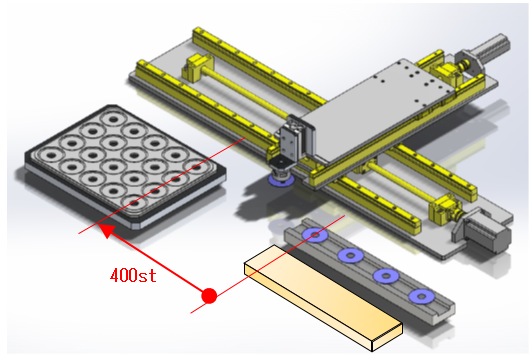
【図3】移動距離が一番短くなる動作
この時の移動距離は400stとなります。移動距離についてはタイムチャートの記事で求めていますので、そちらを参照してください。
参考:第7回「タイムチャートを書いてタクトタイムを計算してみよう」
装置全体を考えると、搬送前後にはチャック・アンチャックの動作が入ります。チャック・アンチャックについては同じ動作となりますので、実効負荷トルクを考える1サイクル動作としては、
チャッキング(下降~チャック~上昇)+ 走行(X軸)
について考えればよいです。
ここも、必ずタイムチャートを見て、対象としたモーター(軸)のサイクルを見極めてください。
チャッキングの動作は変更していないので、【図4】のタイムチャートからチャッキングには2.5秒かかっていることが分かります。加減速時間を変更していますので、走行時間を考えます。
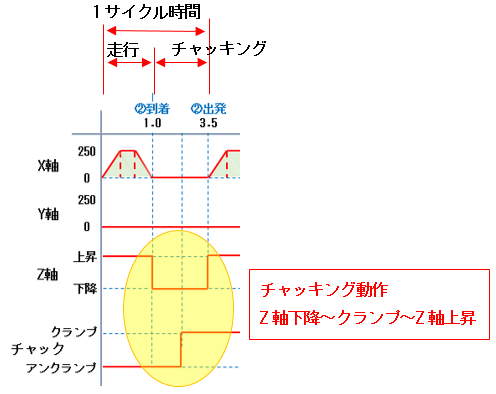
【図4】タイムチャートから動作を見極める
※このタイムチャートは第7回のものです。
加速時間、移動速度、移動距離から走行時のタイムチャートは【図5】のようになります。
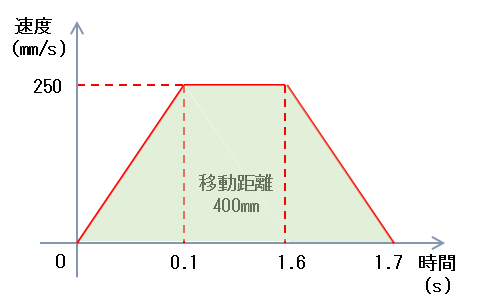
【図5】走行時のタイムチャート
以上から、X軸の1サイクル時間を求めます。
1サイクル時間=1.7+2.5=4.2sec
加速トルクは、加減速時間が0.2秒の場合の2倍になるので
加速(減速)トルク=0.087×2=0.174N・m
モーター定格トルク(0.159N・m)を超えていますので、実効負荷トルクを求める必要があるケースの2にあたります。
実効負荷トルクを求めるために必要なデータが集まりましたので計算してみます。
モーター定格トルクより十分小さいので、問題ないことが確認できました。
このように、実効負荷トルクを求める必要があるケースに当てはまる場合でも、その他の条件により、問題ないことはあります。
今回は、チャッキングの時間が長いので加速トルクは大きいですが、休んでいる時間も長いので、問題ありませんでした。ダメな時もあります。例えば、今回の条件で垂直搬送の場合は平方根内の分子第4項はゼロにはならないので実効負荷トルクは変わってきます。
求める必要がある場合は必ず計算してください。
4. モーターカタログの読み方–定格トルクと最大トルクとは
モーターの定格トルクと最大トルクについて少し触れておきます。
【図6】にサーボモーターのトルク特性図を示します。
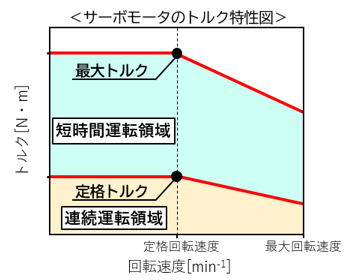
【図6】サーボモーターのトルク特性図
通常の運転では、定格回転数以下で運転します。
この範囲では定格トルク、最大トルクは一定となります。この一定となるところがインダクションモーター(三相誘導電動機)とサーボモーターの大きな違いです。
定格回転数を超えて、最大回転数まで運転は可能ですが、トルクは低下していきます。最大回転数でのトルクの値については基本的に公開されていません。
つまり、「回りますけど、あまり使わないでください。」ということです。回転数は定格回転数(回転速度)までとして設計してください。
次にトルクです。トルクは縦軸を見ていきます。定格トルクから最大トルクの間は「短時間運転領域」となっています。
「ちょっとの間ならいいですが、長時間はダメです。」ということです。
今回、加速トルクは定格トルクを超えました。
つまり、短時間運転領域を使用しています。しかし、チャッキングの時間などモーターが休む時間が長かったので、実効負荷トルクは定格トルク以下に収まりました。
基本的には加速トルクも定格トルク以下にすることが望ましいです。どうしても無理な場合のみ短時間運転領域を使用すると考えてください。
5.まとめ
以上のことから運転パターンの変更によりモーター負荷やタクトタイムに変化が発生する場合には、次のことに注意が必要です。
- モーター回転数は定格回転数以下に収まるか。(ボールねじリードなど機械的条件から決まる)
- 負荷トルクは定格トルクの80%未満となっているか。
- 加速トルクは定格トルクの100%未満となっているか。
- タイムチャートを確認し、軸(モーター)の1サイクル運転時間を確認する。
- 2と3を満たさない場合や、加速・減速の多い場合には、実効負荷トルクを求めて定格トルク以下となっていることを確認する。
実効負荷トルクの計算や、タイムチャートの読み取りと作成には非常に手間がかかります。
しかし、装置設計をする以上、ここを避けて通ることはできません。がんばってやりましょう。
次回から2回に渡ってタイミングベルトを使用した搬送装置について考えていきます。まずは、モーター負荷荷重が変わった場合を考えて、対応策を2パターン考えます。その次にベルトの弾性変形について考えてみます。
それではまた。