この記事では、ナット付き部品「板金プランジャブラケット」を使った多数個治具の事例を用いて、板金加工時間を半減する方法をご紹介します。meviy でも「ナット取付け」板金部品を手配できます。
工数半減などのアイデアが浮かんでも、市販部品では機能を満たせず思わぬ壁に当たる事があります。このような課題は市販品を応用した部品を製作し、必要な機能を満たす事で解決できます。
今回は、プランジャ位置を変更した「板金プランジャブラケット」を多数個加工治具に取り付けた事例を用いてアイデアを実現するレシピをご紹介します。
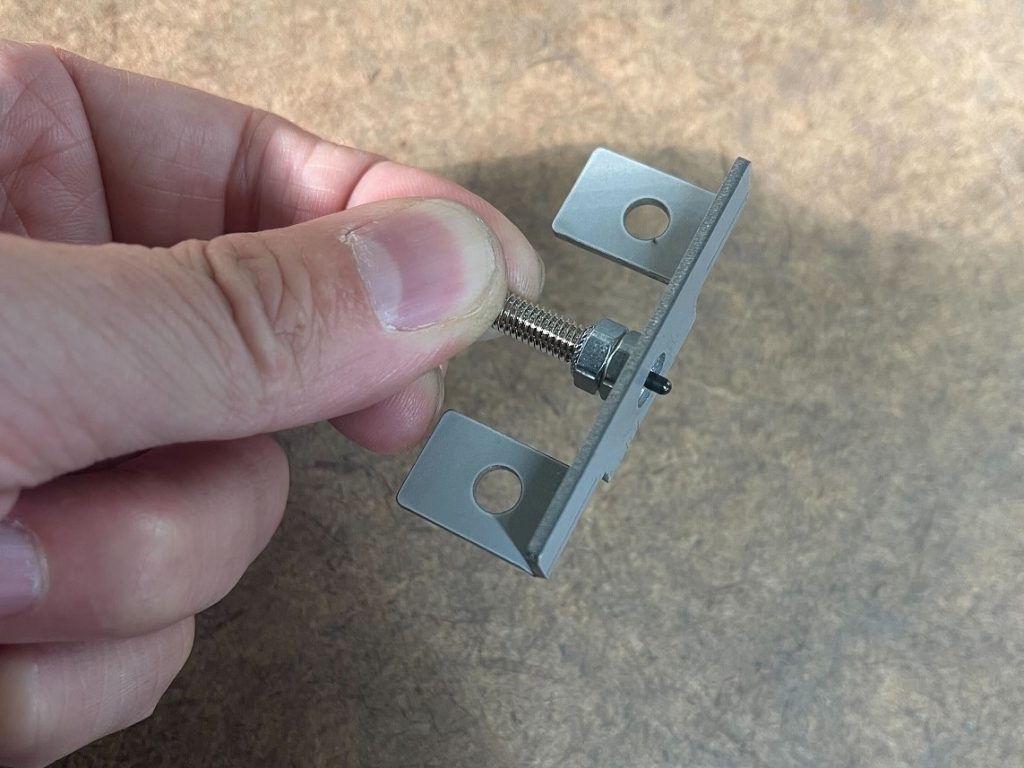
プランジャをダブルナットでブラケットと固定
目次
1.レーザー加工機の材料セット作業改善
生産設備に材料セット作業はつきものです。
弊社で保有するレーザー加工機も、当然ですが材料セット作業が必要です。加工が早く終わる製品でも、実際の加工時間よりも材料をセットする時間のほうが多くかかる事がよくあります。その場合、加工枚数の分だけ人が行うため、労力が必要になり疲れます。
そのような、付加価値を生まない非正味作業に着目し「本当に必要な作業なのか?」、「プランジャとダブルナットを使用したナット取付板金部品で材料セットできそう!」と考え、改善に向けて着手しました。
現場からの困り事の声を聴き、現状調査と外段取り化の改善、設計、改善後の評価の流れでご紹介します。
2.スケッチ材のレーザー加工の問題を解決
写真の製品を1週間に500枚加工しています。
材料はSUS304 板厚は4ミリ横700ミリ縦100ミリです。
スケッチ材の説明とメリットデメリット
板金加工で使用する材料サイズは 3′× 6′( 914×1829 mm )や 4′×8′( 1219 × 2438 mm )と言われる定尺材のほかに、製品出来上がりサイズに指定寸法して切断した物をスケッチ材と言います。
定尺材は、必ず製品外周をレーザー加工する必要がありますが、スケッチ材は外形寸法にあらかじめ切断しているため外周加工が不要です。外周加工がない為、加工費が安くできる事がスケッチ材のメリットです。
寸法精度はレーザー加工より劣るため、用途は精度要求の低い製品に限られます。
また、レーザー加工のような曲線加工には対応できず矩形などの直線の切断しか対応できない事がデメリットです。
![]() スケッチ材 |
![]() 4′×8′定尺材からの板取例 |
今回加工する製品の外形寸法精度は ±1ミリ と余裕があるので、スケッチ材を購入しレーザー加工機にセットして4か所の穴を加工します。
正味作業に集中する作業方法を考える
ある日、レーザー機オペレータから「この製品の加工量が多くてほかの仕事が入らない、加工を早く終わらせることが出来ないか」と相談を受け早速加工の様子の現状調査をしました。
時間計測の結果です。
① 材料をレーザー加工機にセット | 15秒 |
② レーザー加工 | 37秒 |
③ 材料をレーザー加工時から降ろす | 15秒 |
合計 67秒/枚 かかっていることが解りました。
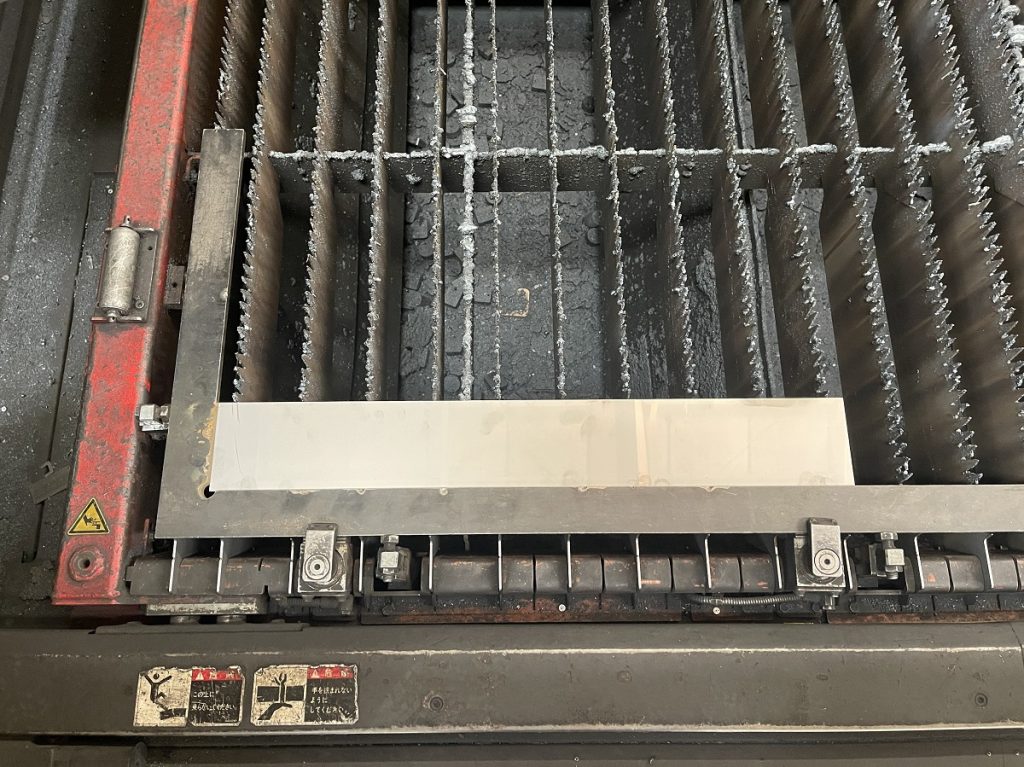
① 材料をセット(15秒)
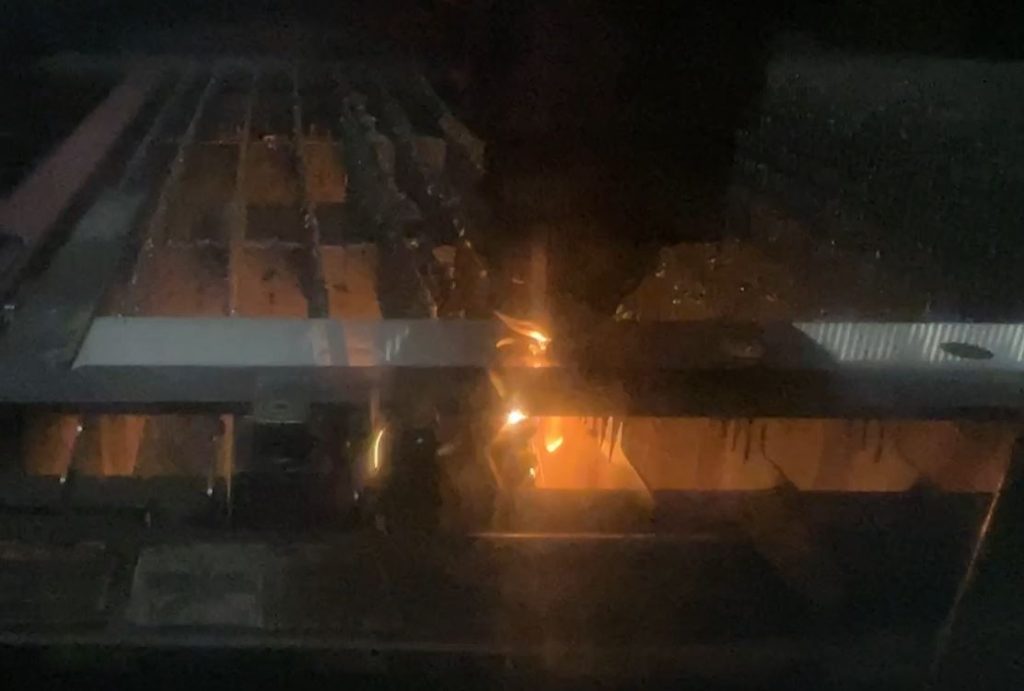
②レーザー加工(37秒)
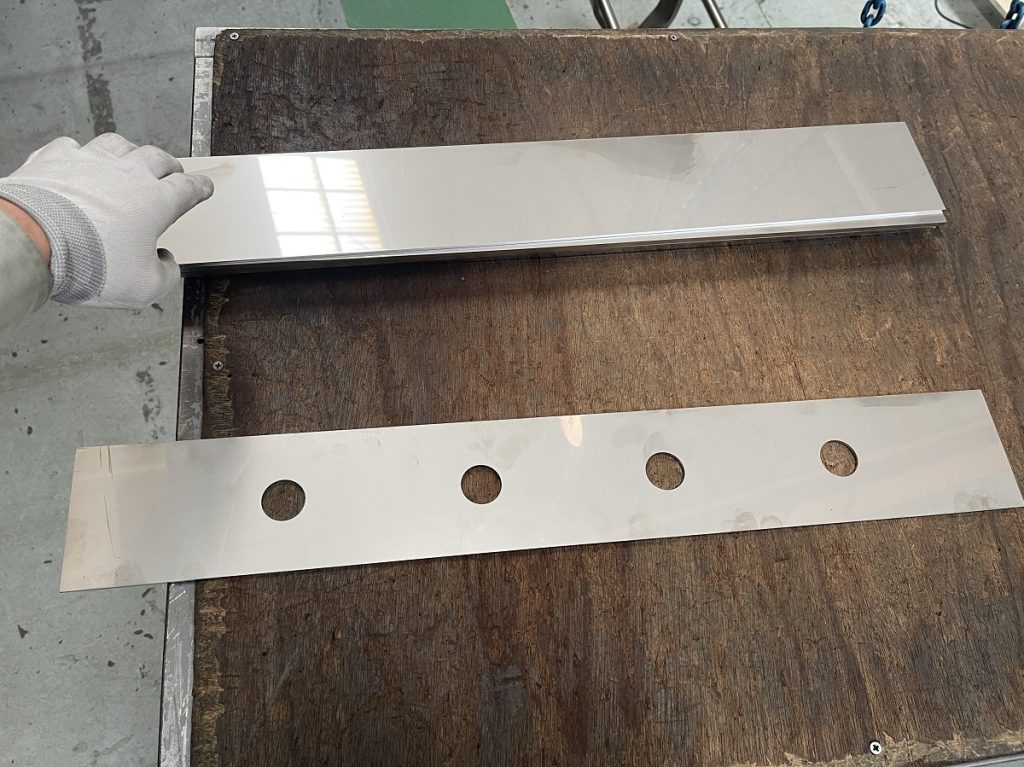
③材料を降ろす(15秒)
これを週に500枚なので、9.3時間も時間が掛かっています。
計測した時間から正味作業と非正味作業を分けます。
●正味作業とは付加価値のある作業 = ② レーザー加工(37秒) が切断している時間です。
●非正味作業とは付加価値のない作業、ここでいう ① 材料セット(15秒) と ③ 材料を降ろす(15秒)の時間です。
この非正味作業の30秒のムダを改善します。
シャトルテーブルと多数個加工治具を製作して外段取り化改善
レーザー加工機はシャトル式のテーブルA と B を2個装備しています。テーブルA を加工している間にテーブルB に次加工の材料をセットする事が可能です。
スケッチ材を5枚並べて配置できる多数個加工治具を2個製作してまとめてレーザー加工します。
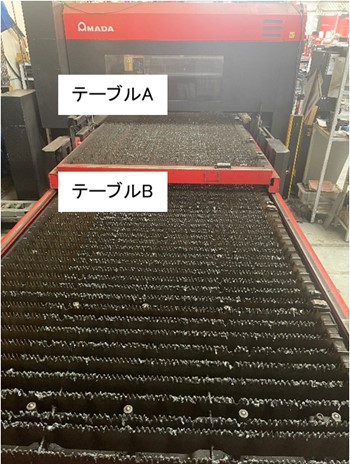
テーブルA と テーブルB
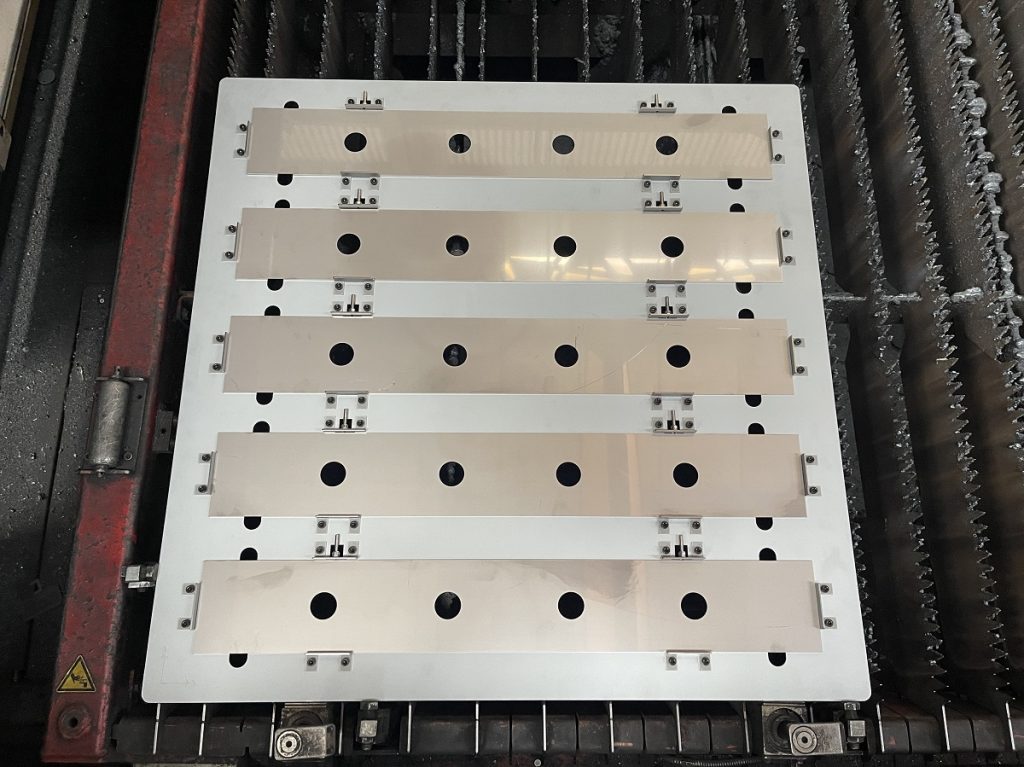
多数個加工治具
テーブルA を加工している間にテーブルB に材料をセットします。これにより材料セットを機械稼働中に行えます。この作業を「外段取り化」といいます。
テーブルA からテーブルB に交換する時間は35秒かかりますが、スケッチ材1枚ずつ加工するより早く加工できそうです。
スケッチ材の寸法精度をストロークプランジャを用いて治具にセット
スケッチ材寸法ですが精度が悪いため幅100 ミリのところ、99.58ミリ とマイナスしているケースもあれば 100.2ミリ とプラスしているケースもあります。
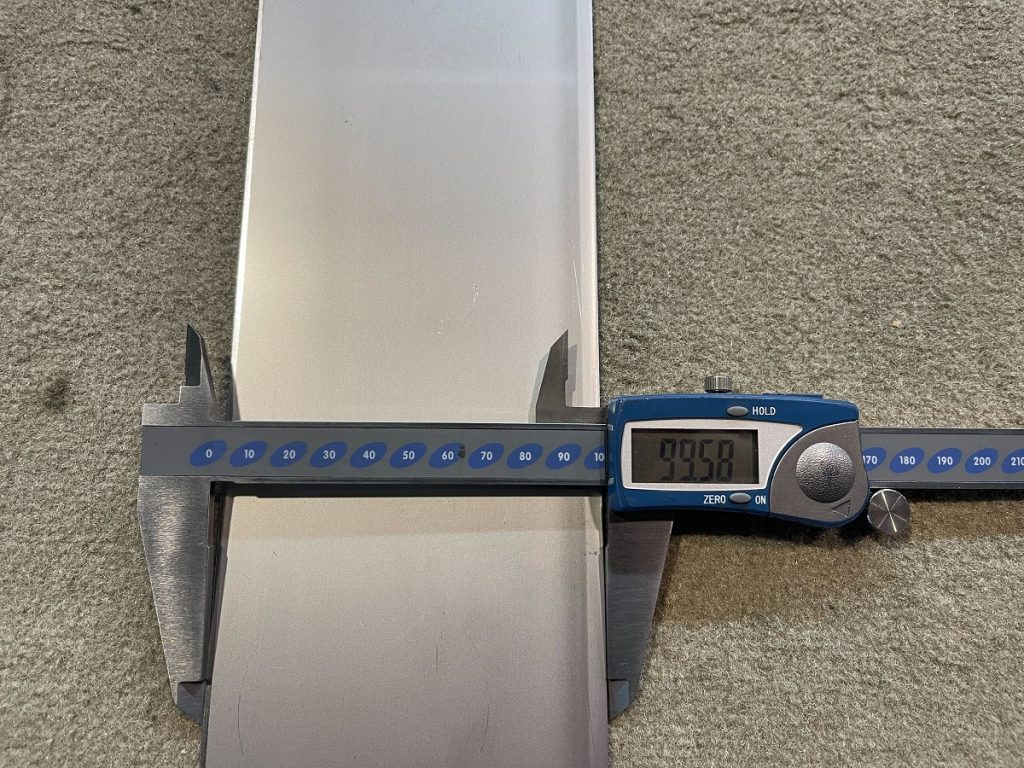
100ミリ のところ、99.58ミリ でマイナスしている
治具にセットしても隙間が発生したり、干渉してセットできない事が発生します。
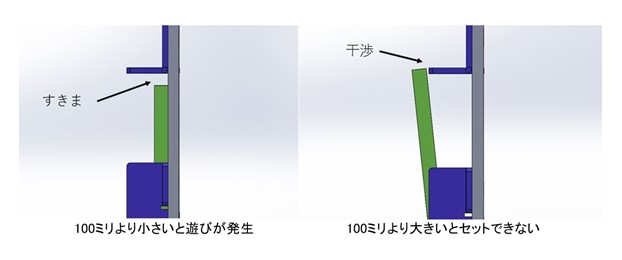
治具セット時の隙間や干渉の例
そこで、寸法誤差を考慮してセットできるストロークプランジャ PJX-N5-3を用いて位置決めを考えます。
ストロークプランジャとは、他部品の位置決め・加圧に用いる機械要素部品です。本体にばねを内蔵し荷重を与えると本体の内部に沈み込み、荷重が解けるとばねの力で元に戻る機能があります。
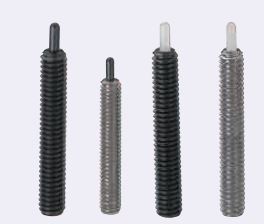
ストロークプランジャ
参考:MISUMI 技術情報「ストロークプランジャ選定のポイント(選定概要)」
しかしプランジャを治具に固定するため、市販のプランジャブラケットを使用予定でしたが材料の高さが合わず使えない事が発覚しました。プランジャ高さをあと1ミリ下げたいです。
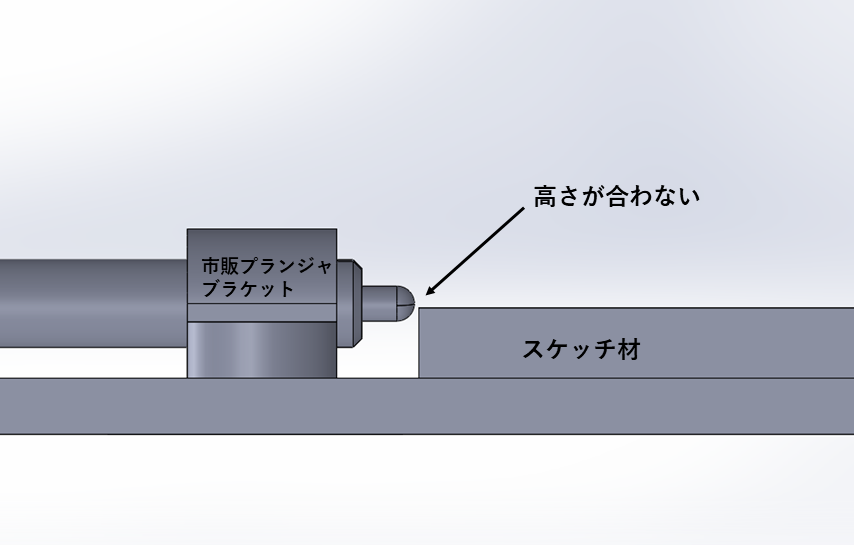
市販プランジャブラケット使用不可
板金プランジャブラケットで解決
そこで、板金プランジャブラケットを製作し、プランジャ位置を1ミリ下げます。
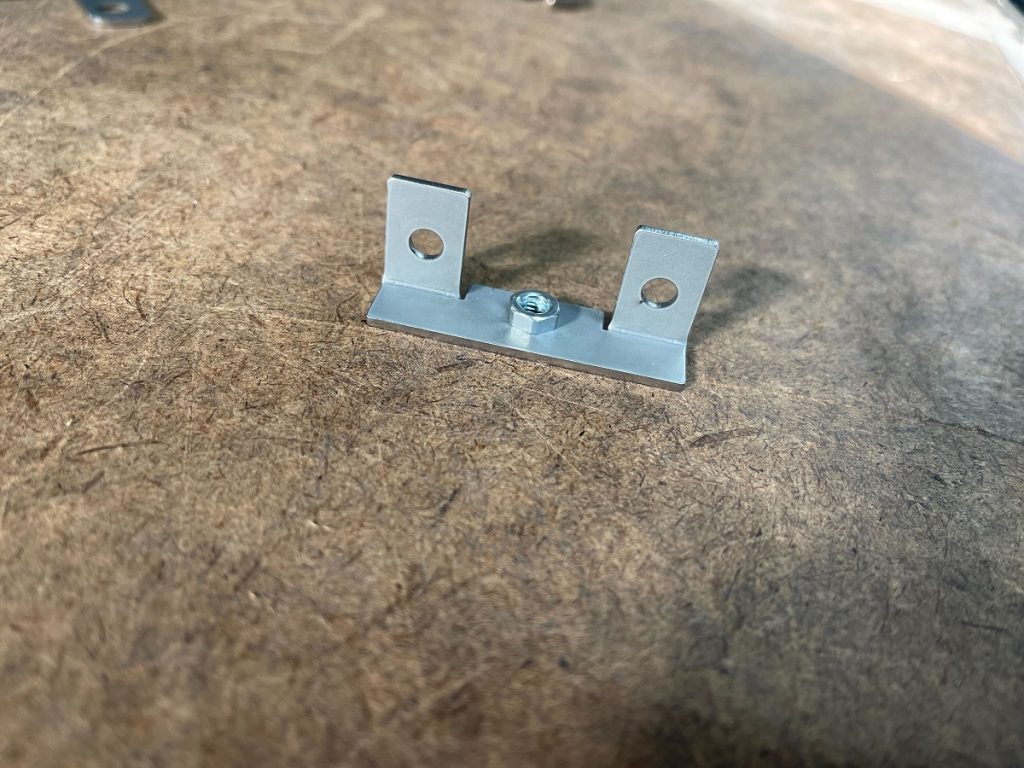
板金プランジャブラケット
ナット取付したブラケットにプランジャを取り付けたあと、動かないようにナットをもう1つ取り付けて固定します。
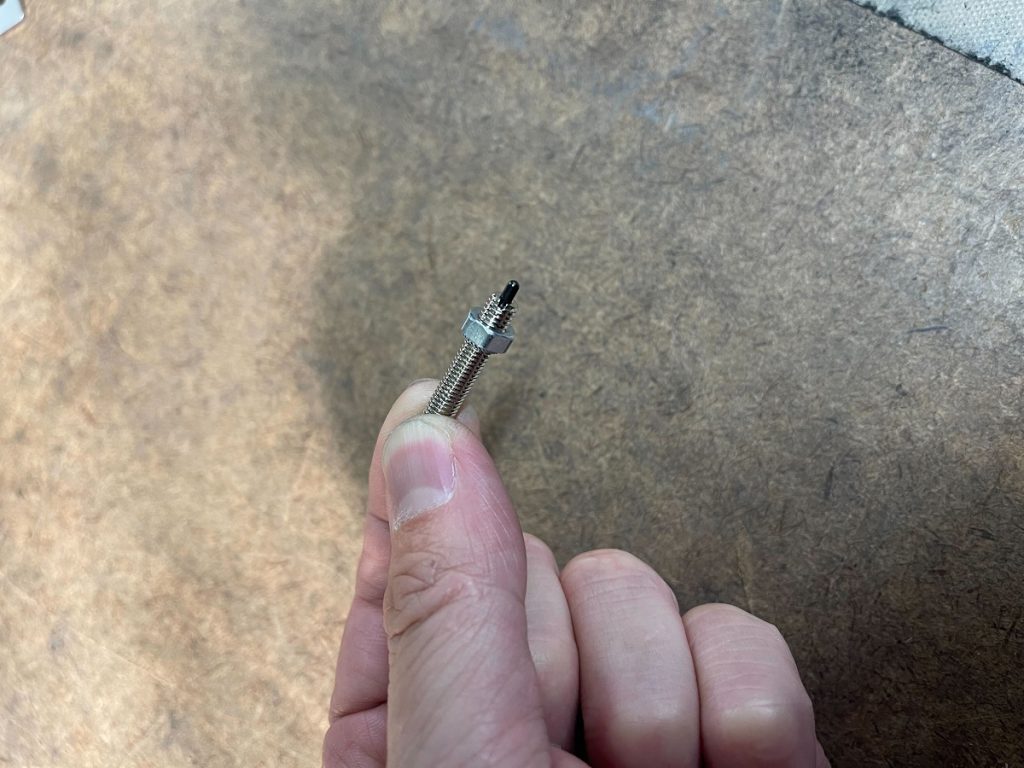
プランジャ
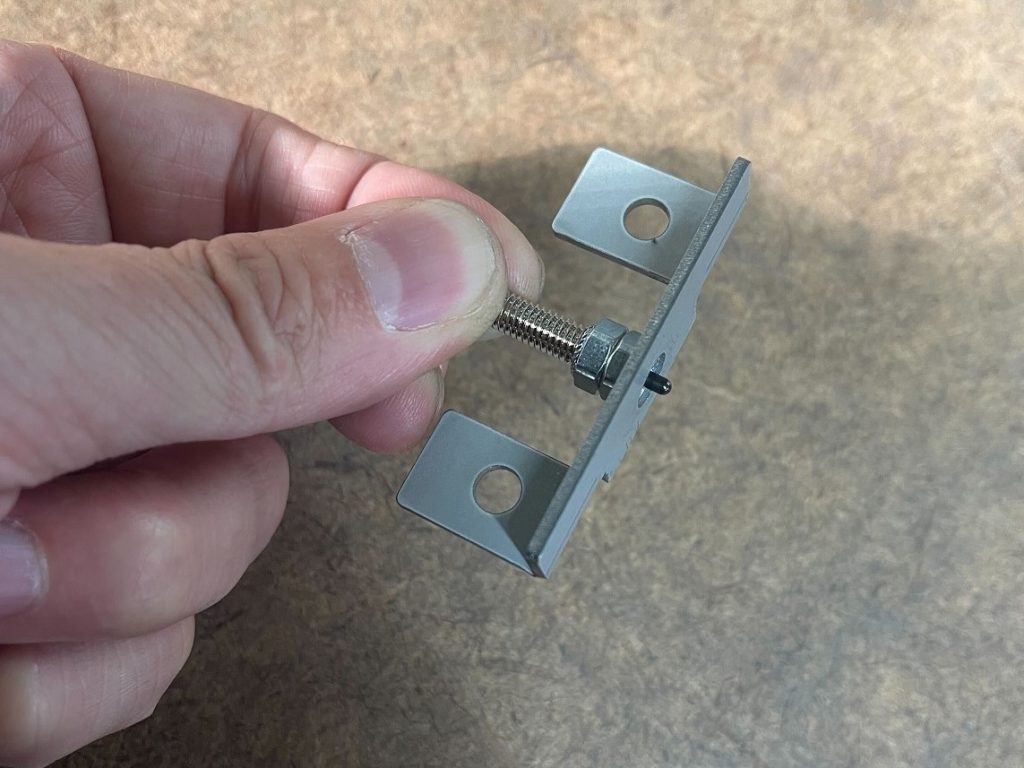
板金プランジャブラケットにプランジャをナットで固定
3.板金プランジャブラケットの設計ポイント
次に、板金部品の設計ポイントについて、加工の手順を追いながら説明します。
例として「板金プランジャブラケット」を、弊社で使用している SheetWorks ※で作成します。
※ SheetWorks は、3次元CADソフトウェア SOLIDWORKS をベース CAD とし、板金製造業向けに特化したあらゆるコマンドを搭載したアマダ社製の 3D CADソフトです。
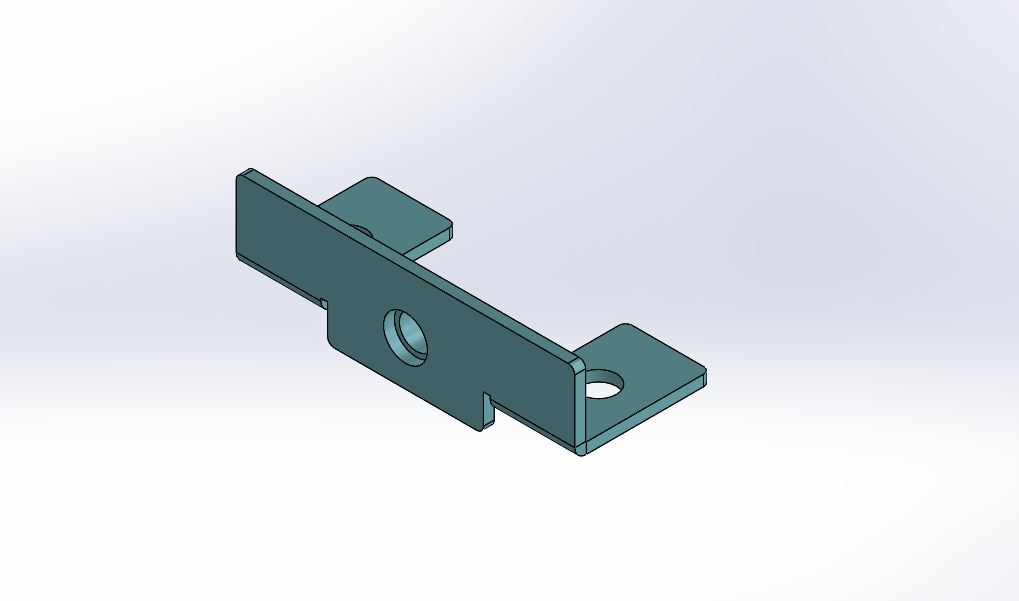
板金プランジャブラケットのイメージ
1.治具の設計
あらかじめ多数個治具を設計します。
スケッチ材が大きくても入るように板金プランジャブラケットとスケッチ材の隙間を 1ミリ 設けます。隙間があってもプランジャの機能により位置決めができます。
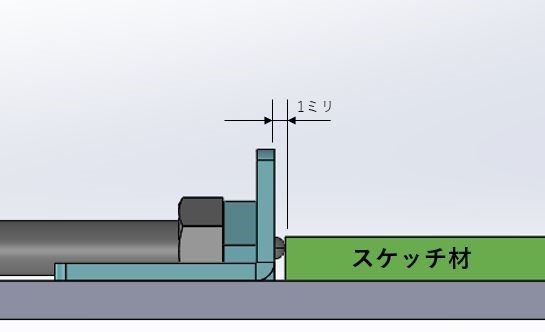
板金プランジャブラケットとスケッチ材の隙間(1ミリ)
2.外形部分の設計
●部品を開始
[新規] – [部品] – [右側面] – [スケッチ] を選択します。
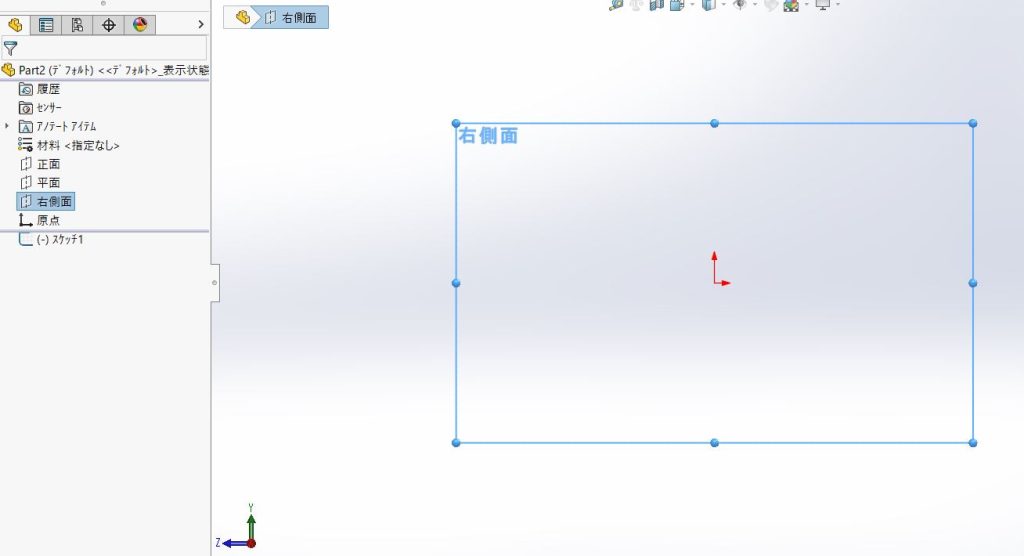
部品を開始
[直線] を選択-原点から縦に 12ミリ、原点から横に 20ミリ の直線を作成します。
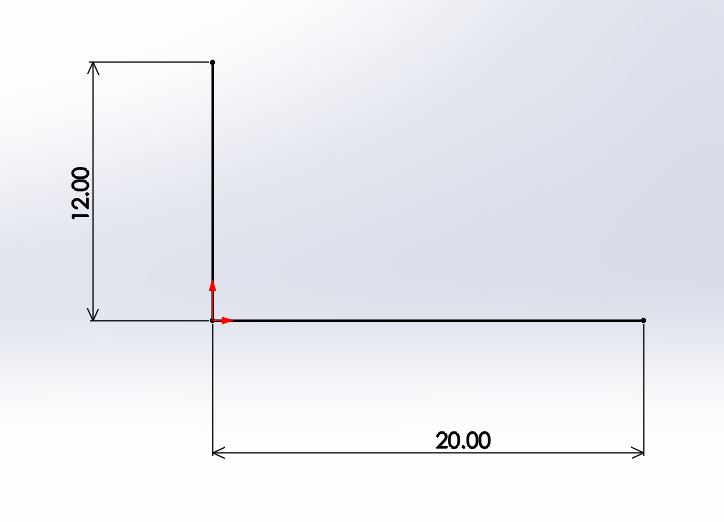
スケッチの作成
[フィーチャー] – [押し出しボス] – 方向1]、中間平面 – 深さ:50ミリ – [薄板フィーチャー] 厚み 1.6ミリ に設定します。
外径が完成しました。
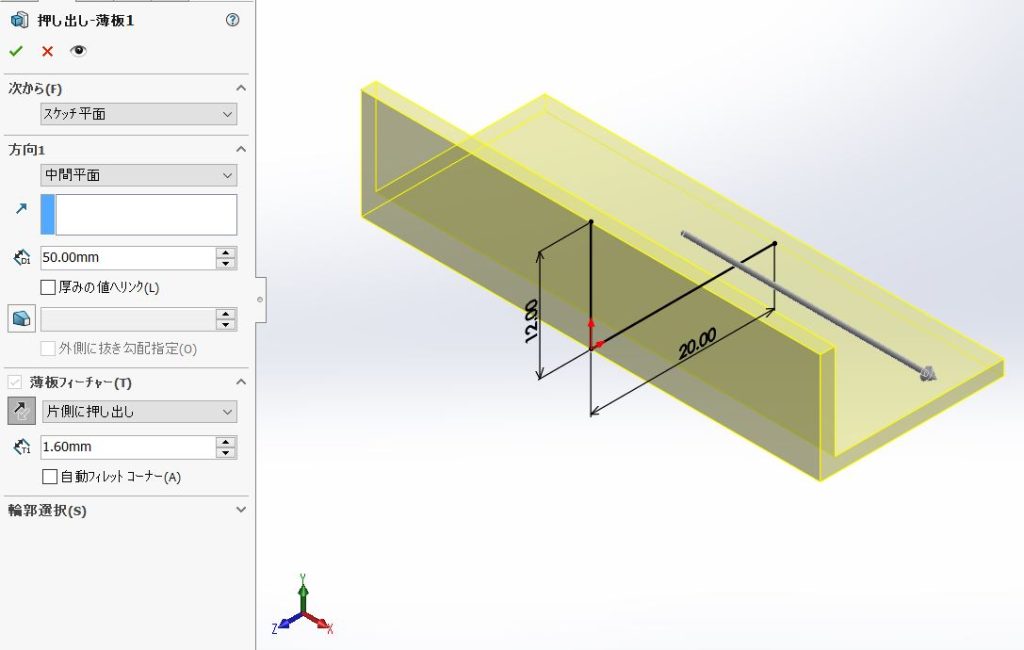
押し出しボスで外径の完成
●プランジャ逃げ部分を押し出しカット
プランジャと干渉する部分をカットします。
部品の平面に[スケッチ]を開始し、幅25ミリの矩形を作成します。
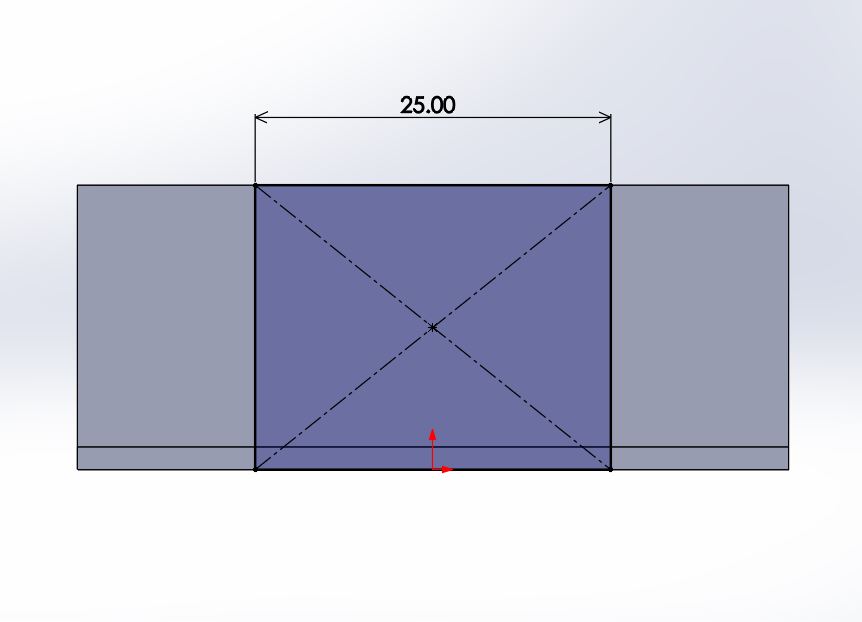
平面に幅25ミリの矩形スケッチを作成
[フィーチャー] – [押し出しカット] – [方向1] 次サーフェスまでを選択します。
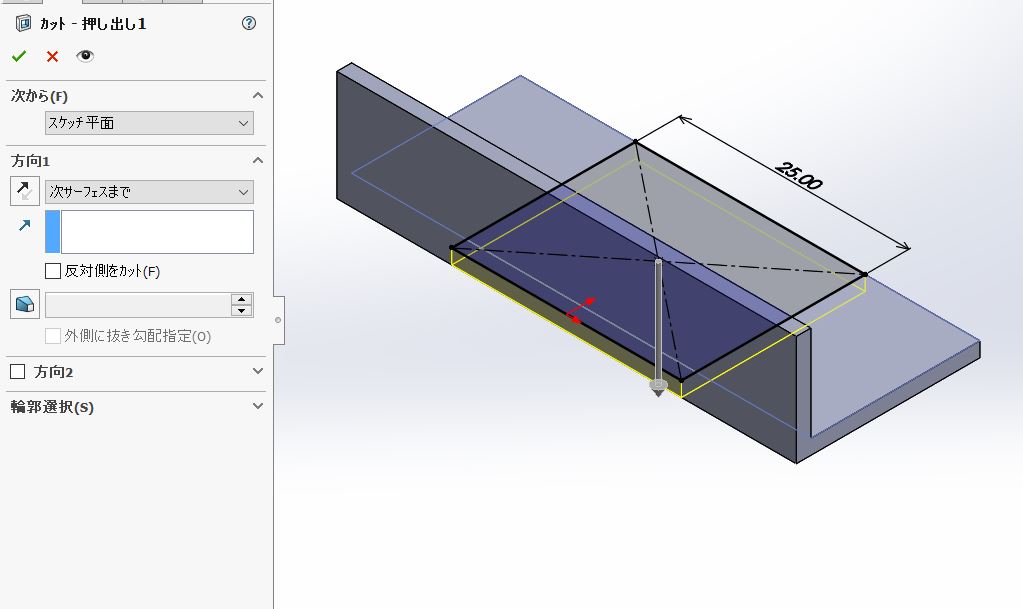
押し出しカットで逃げ部完成
●治具差込部分の作成
板金プランジャブラケットを治具に差込する部分を作成します。
パーツ正面に [スケッチ] を開始し、幅 23ミリ 高さ 3.2ミリ の矩形を作成します。
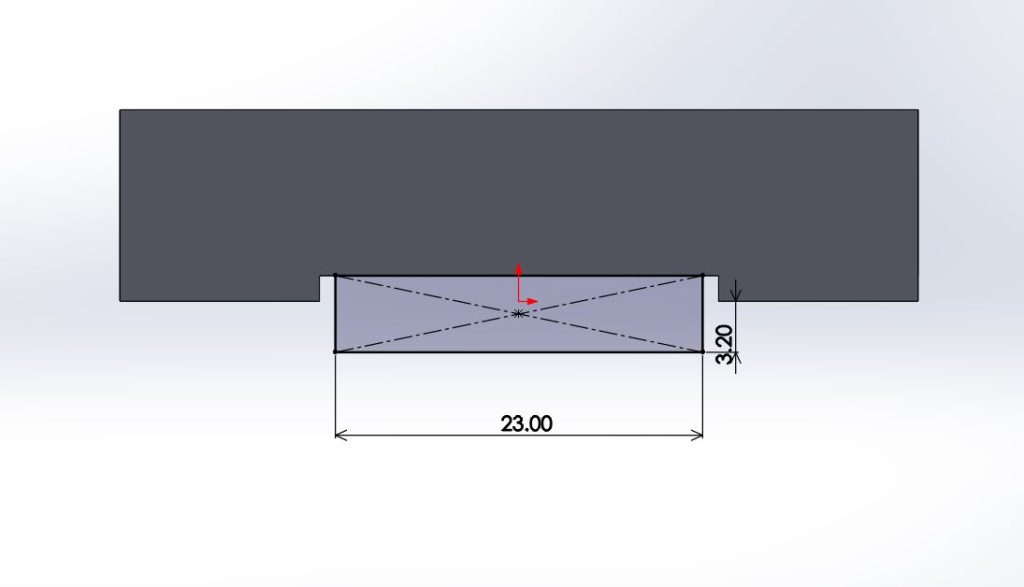
ベルトカバー部を押し出しカット
[押し出しボス] – [方向1] 端サーフェスで裏面を選択します。
治具に差込む事が可能になります。
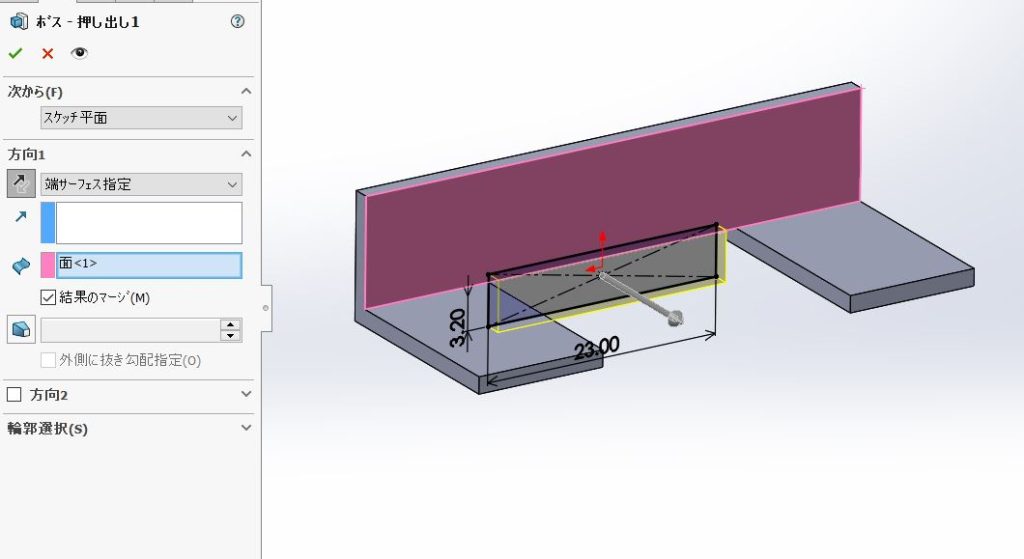
押し出しボスで差込部分完成
●ナット穴の作成
ナット穴を作成します。
穴位置はプランジャがスケッチ材を押す位置、治具に当たらない位置である事が必要です。事前に寸法を計算して治具基準面から3.25ミリの高さに設定します。
パーツ正面に [スケッチ] – [円] を開始し、M5ナット下穴の Φ6.5 を作成します。
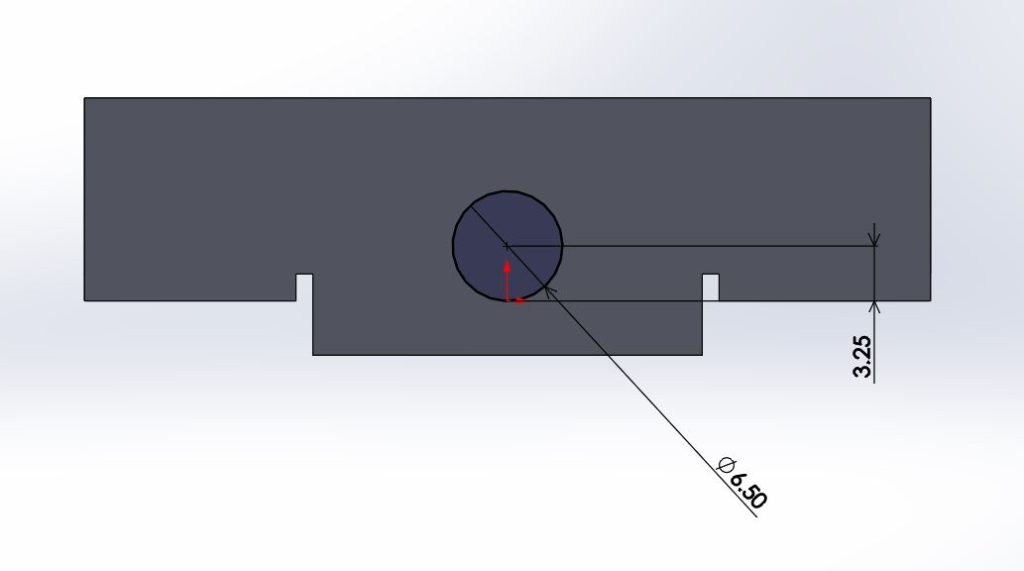
ナット下穴のスケッチ
[フィーチャー] – [押し出しカット] – [方向1] 次サーフェスまでを選択します。
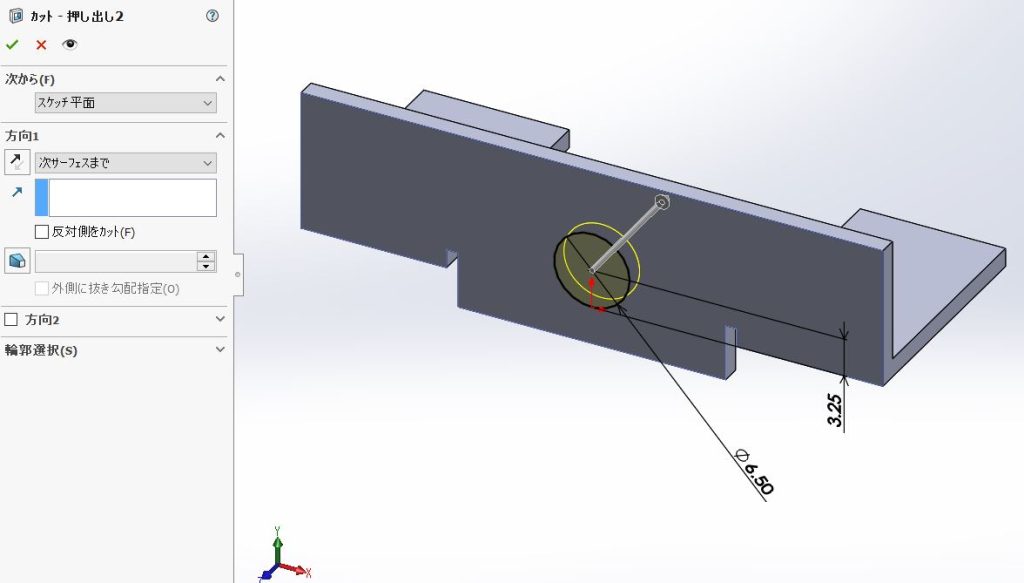
押し出しカットでナット下穴完成
●ボルト穴の作成
治具と固定するボルト穴を作成します。
パーツ平面に [スケッチ] – [円] を開始し、2 – Φ5.3 をピッチ 37ミリ 高さ 10ミリ の位置に作成します。
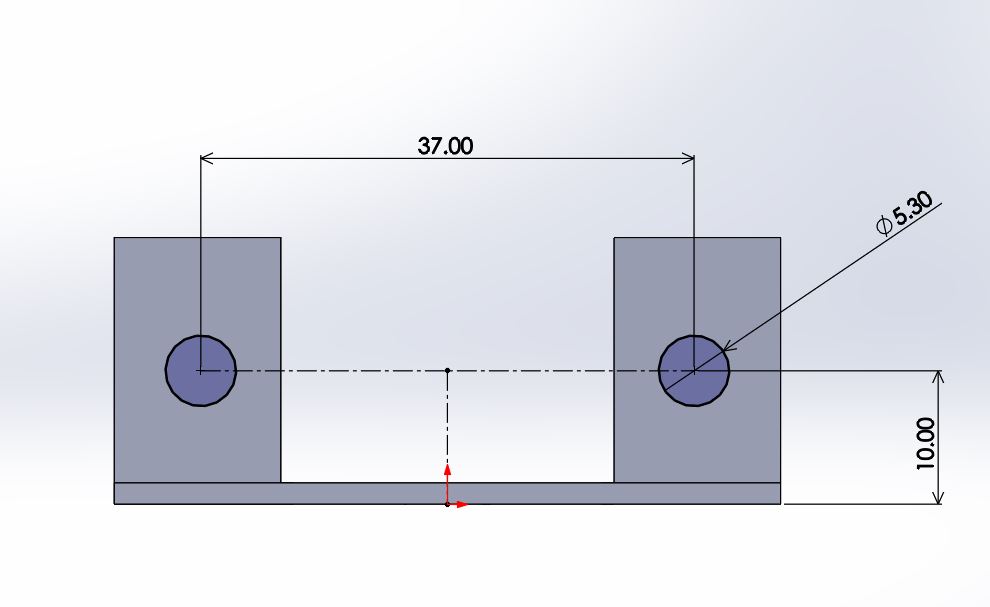
ボルト穴のスケッチ
[フィーチャー] – [押し出しカット] – [方向1] 次サーフェスまでを選択します。
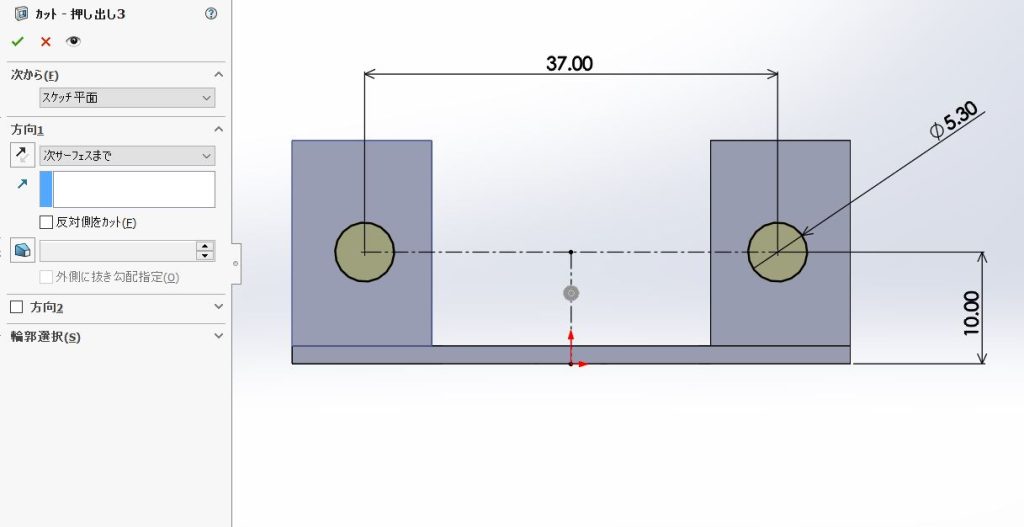
押し出しカットでボルト穴の完成
●フィレット処理
仕上げに、エッジ部はフィレット処理をします。
フィレットとは角部を取って丸める加工で、けが防止のために行います。
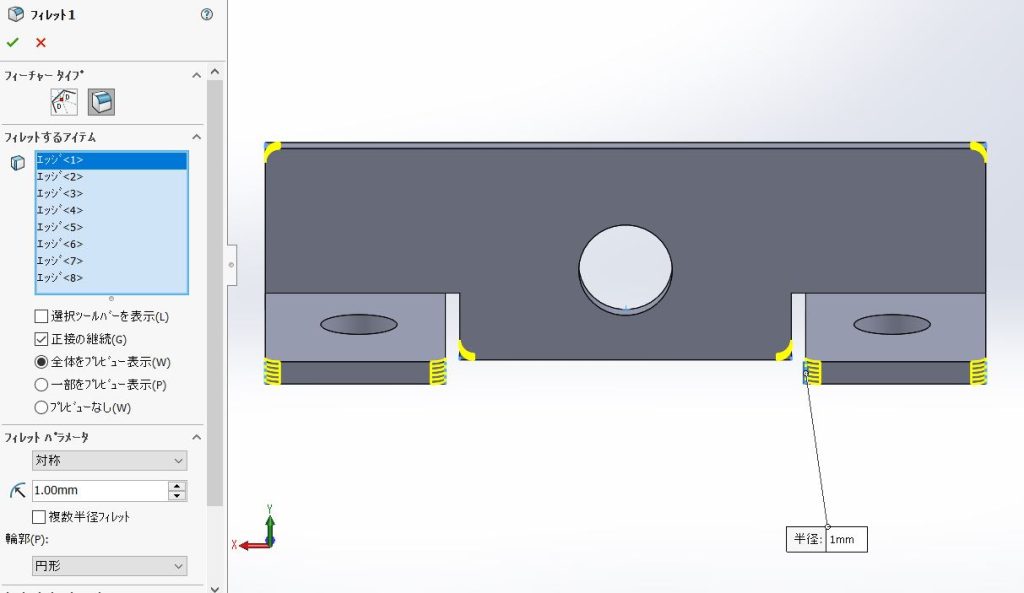
フィレット処理
●ナットの作成
ナットを作成します。
ナット穴の面に [スケッチ] – [円] [多角形]を開始し、[押し出しボス] – [方向1] ブラインド深さ 3ミリ
結果のマージのチェックをオフに設定します。
3.取り付けと機能の確認
ここで板金プランジャブラケットが多数個治具に取り付けることができ、機能するかを確認します。
取り付けは問題なくスパナを使用してプランジャの位置調整できることが確認できました。機能は市販のプランジャブラケットでは高さが合わず使用できませんでしたが、板金プランジャブラケットで固定したプランジャは材料を押してセットできる事が確認できました。
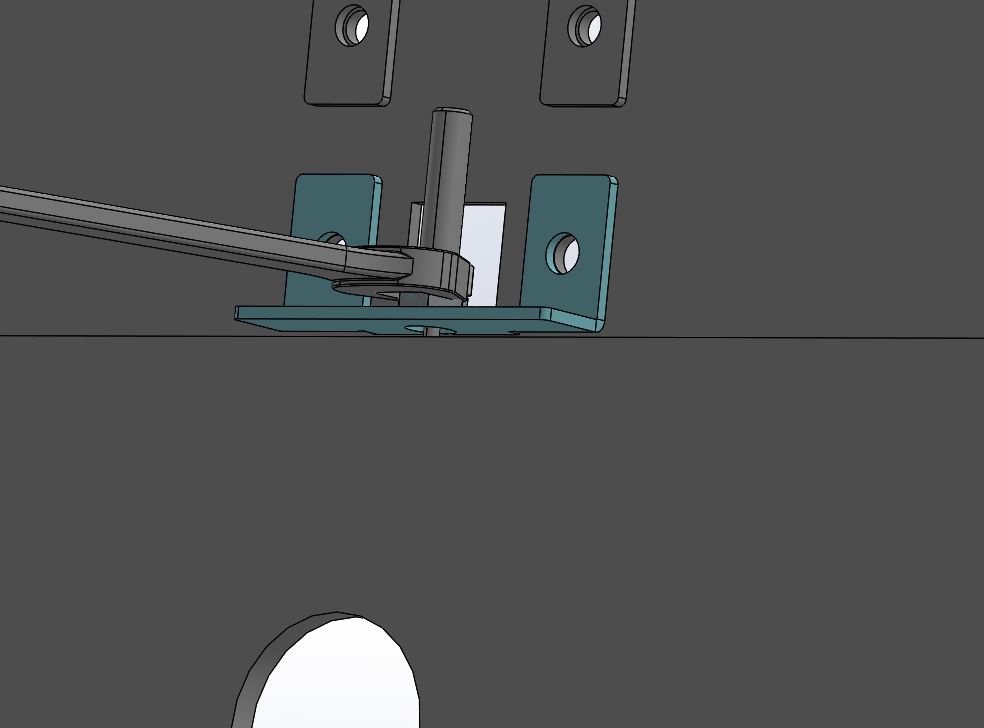
取り付け可能 スパナ使用可能
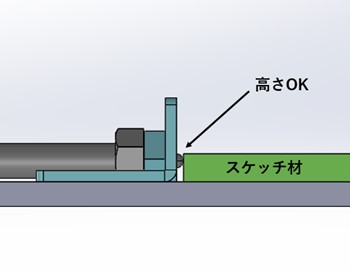
プランジャ機能OK
4.meviy 板金加工の「ナット取付け」サービスで手配
meviyにアップロードするモデルにナットは不要です。非表示にしてからアップロードをします。
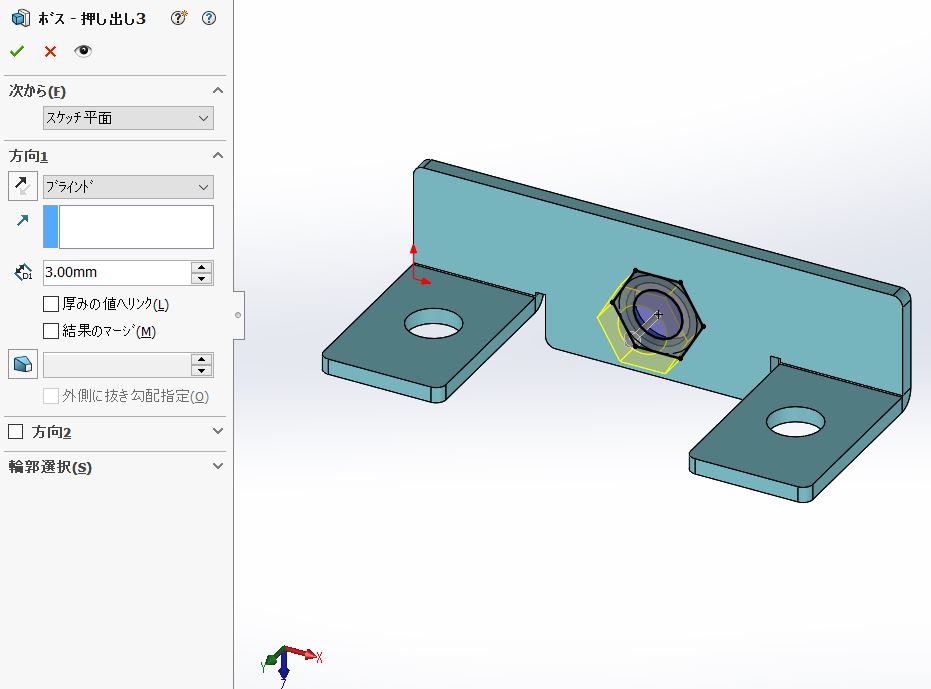
ナットを非表示にする
「穴情報指示」からナット取付の設定を追加して見積もりをします。
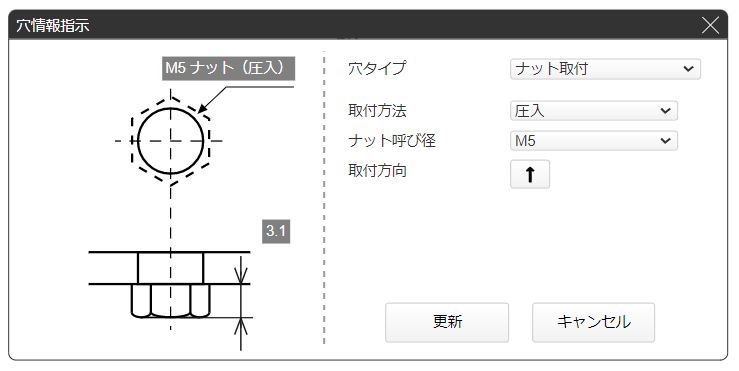
meviy 穴情報指示画面(板金加工)
価格、出荷日、型番が自動見積もりで表示されればそのまま製造が可能ということになります。
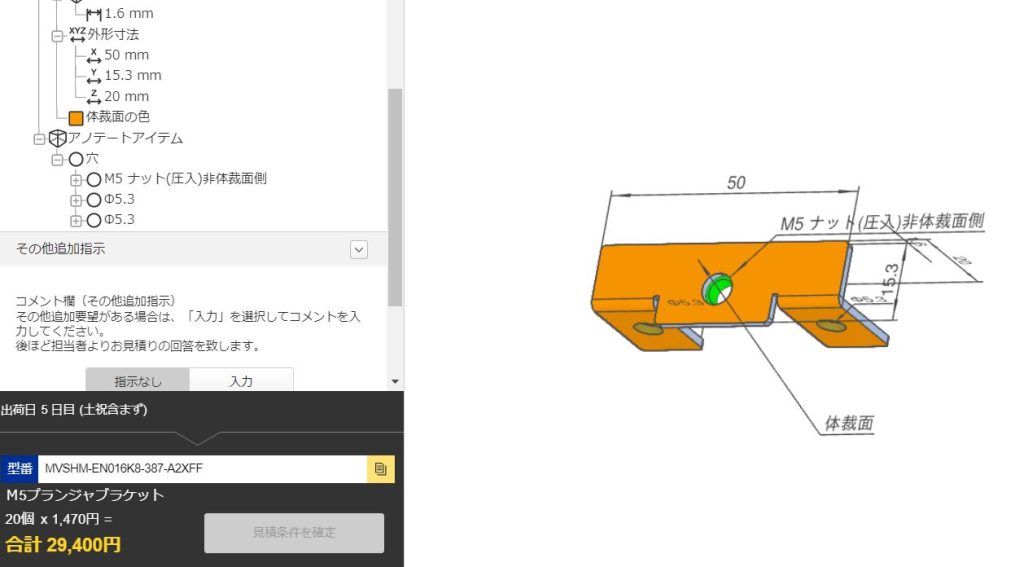
meviy 見積もり設定画面
※参考価格(2023年1月時点)
穴6.5 の穴タイプにナット取付、取付方法に圧入、ナット呼び径に M5 を選択して無事に見積もりが成功。
そのまま注文可能です。
https://meviy.misumi-ec.com/ja-jp/
4.切断、ナット取付け、曲げ加工をしてみよう!板金加工のポイント
それでは実際に切断とナット取付と曲げ加工を行い、板金加工のポイントについて説明していきます。
まずは切断です。
1.切断加工
穴と外周加工だけで成形加工はないので、単体レーザー加工機で加工します。
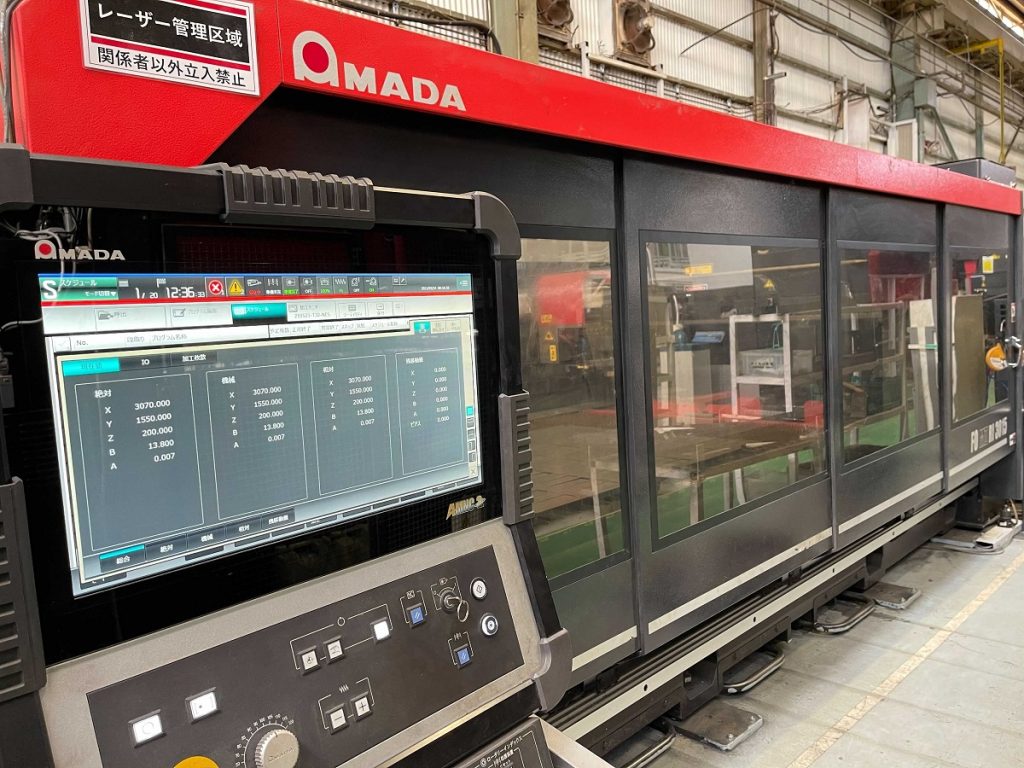
アマダ製FOMⅡRI
レーザー加工機を動かすためのプログラムを事前に CAM で作成し、レーザー加工機で読み込みます。
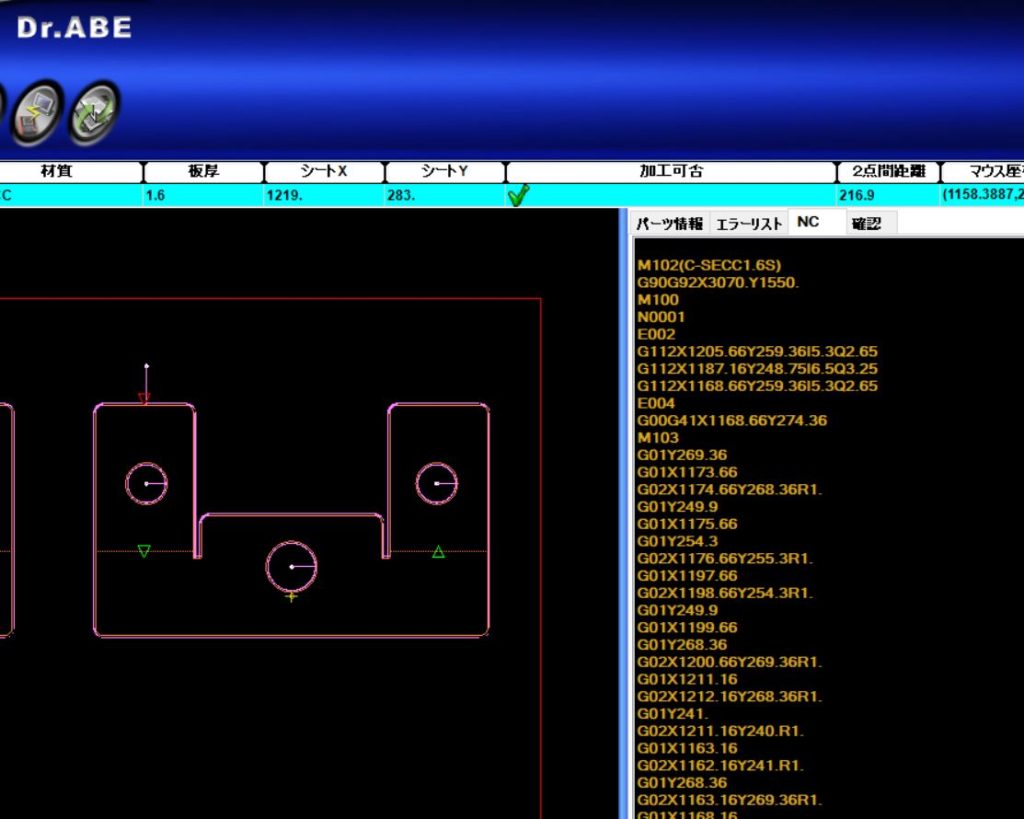
レーザーCAM画面
材料をセットして加工をスタートします。
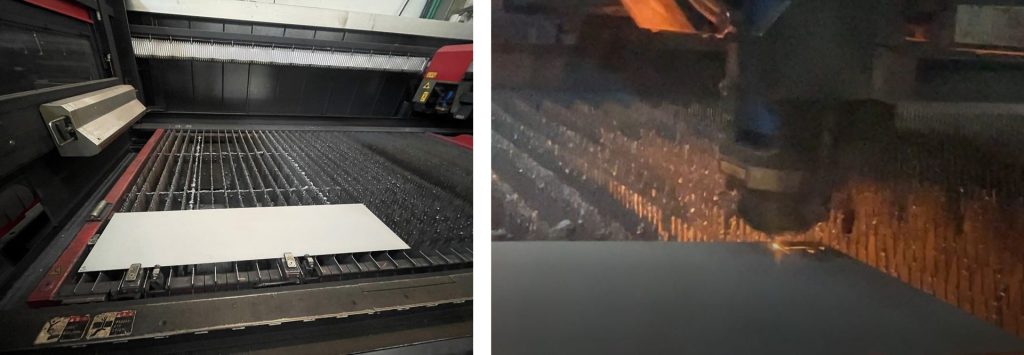
レーザー加工機に材料をセットしスタート
レーザー加工機による切断加工が完了しました。
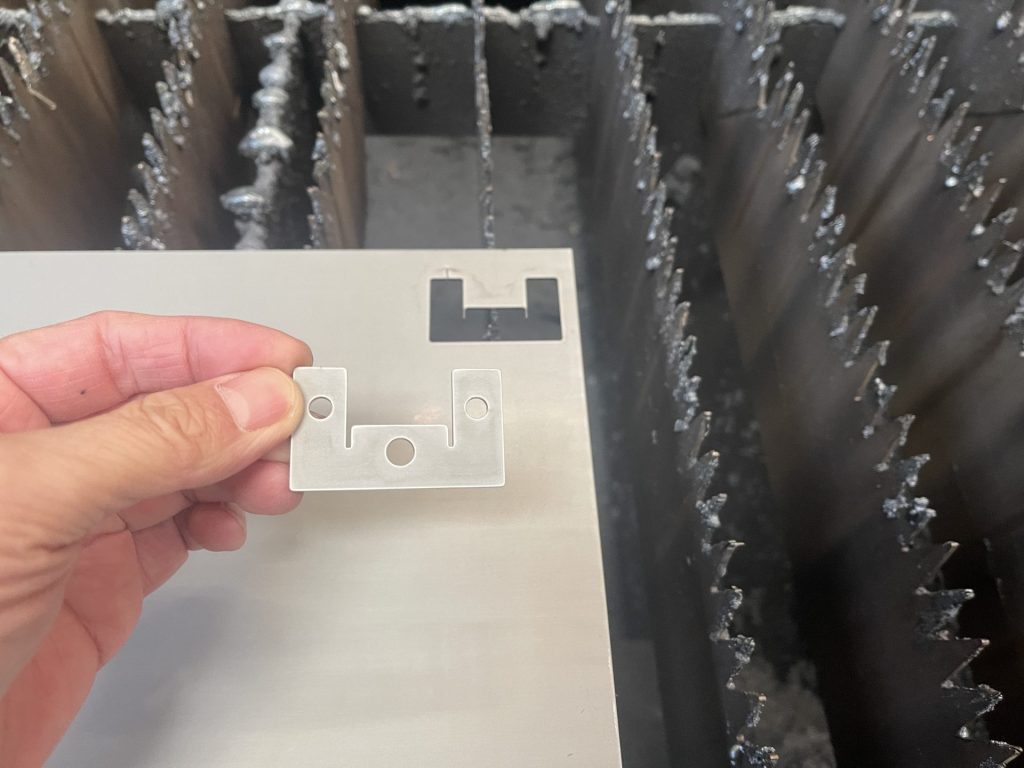
レーザー加工機による切断の完了
2. ナット取付加工(クリンチングマシン)
次はクリンチングマシンを使用したナット取付加工です。
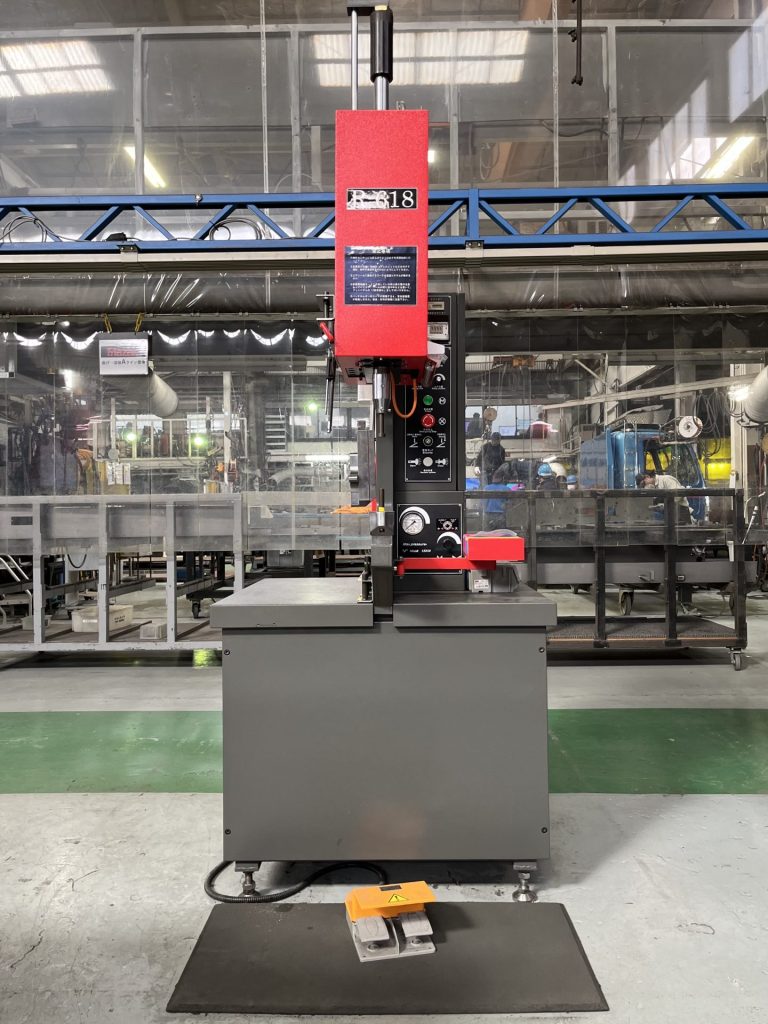
クリンチングマシン
ナットサイズに合わせたツールを選択し機械にセットします。
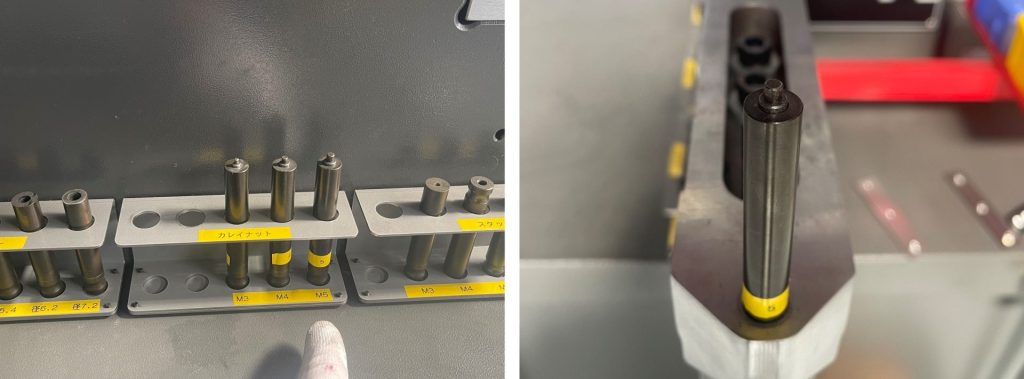
ツールを選択して機械にセット
ツールの上にワークをセット、次にナットをセットします。
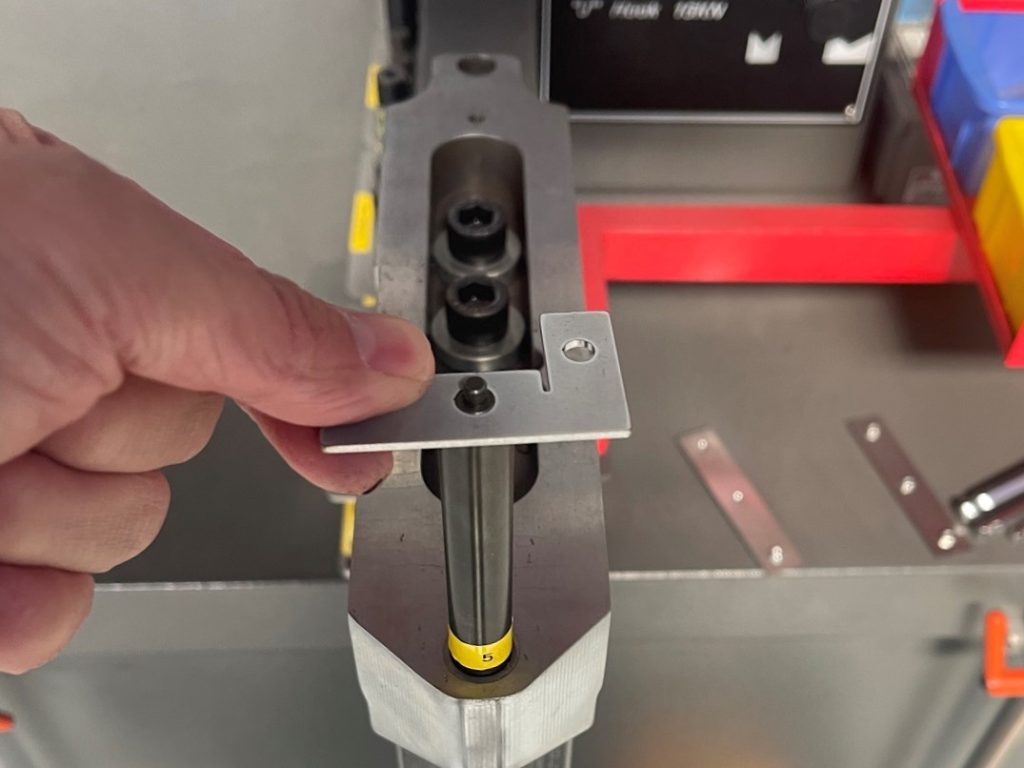
ワークをセット
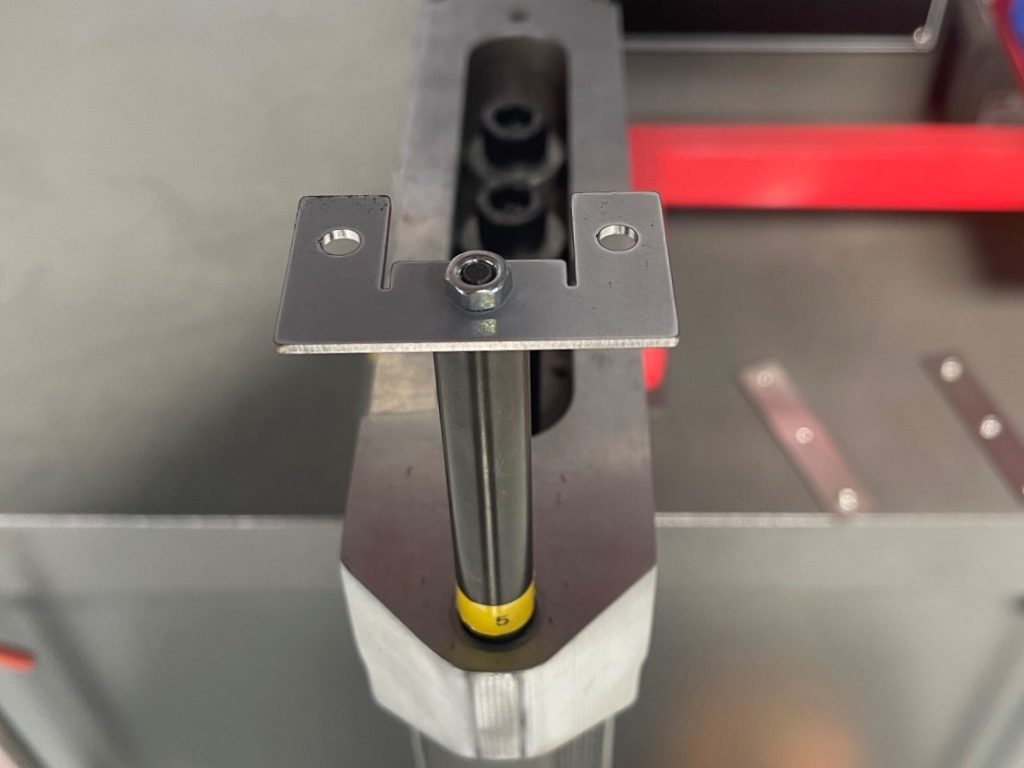
ワークの上にナットをセット
ペダルスイッチを踏むと加工がスタートします。
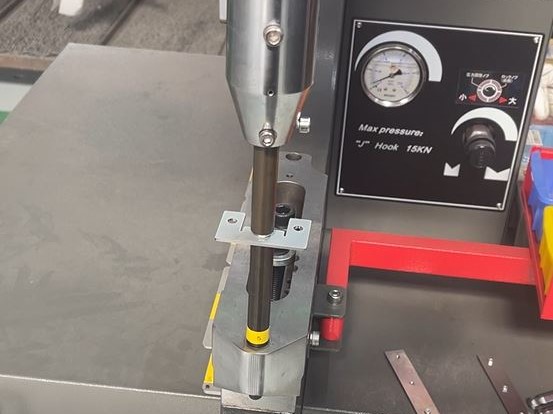
ナット取付け中
ナット取付け加工が完了しました。
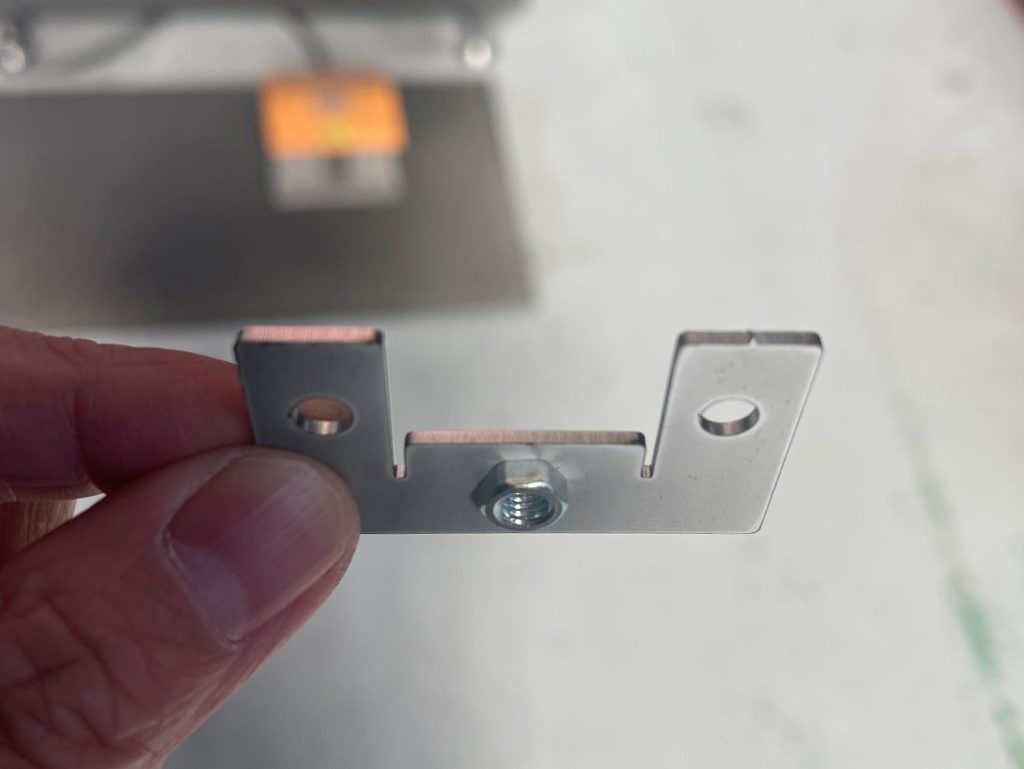
ナット取付けの完成
3. 曲げ加工(プレスブレーキ)
最後にプレスブレーキを使用した曲げ加工です。
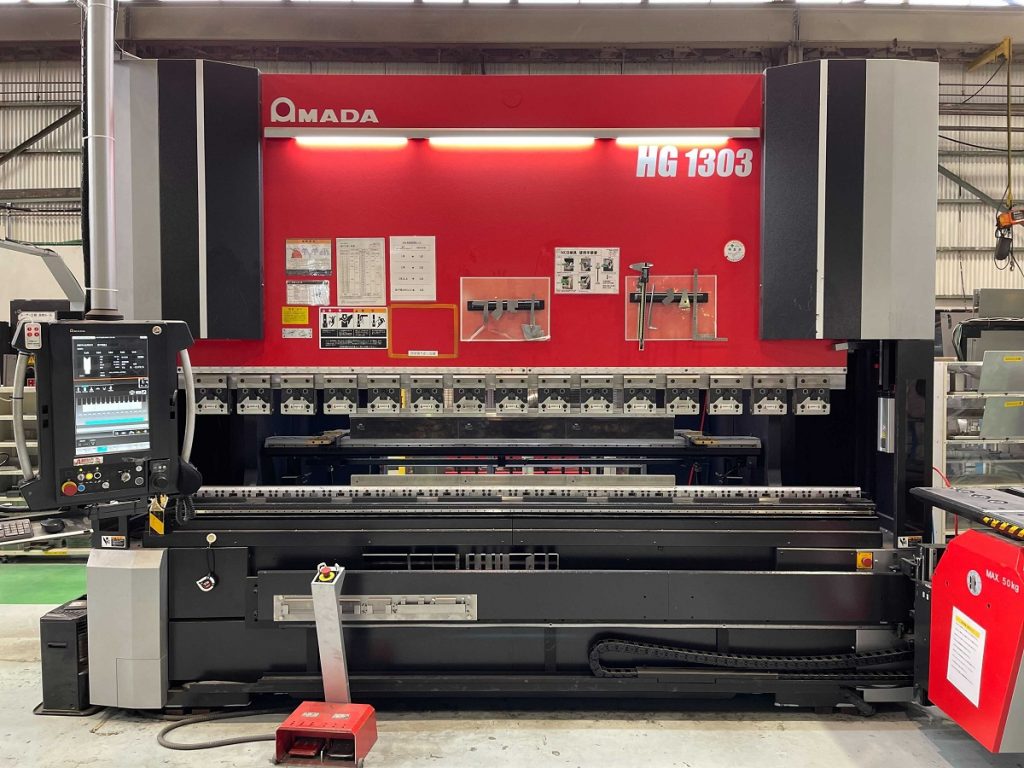
アマダ製プレスブレーキHG-1303
曲げ加工も事前にプレスブレーキを動かすためのプログラムをCAMで作成し加工機画面でプログラムを確認します。
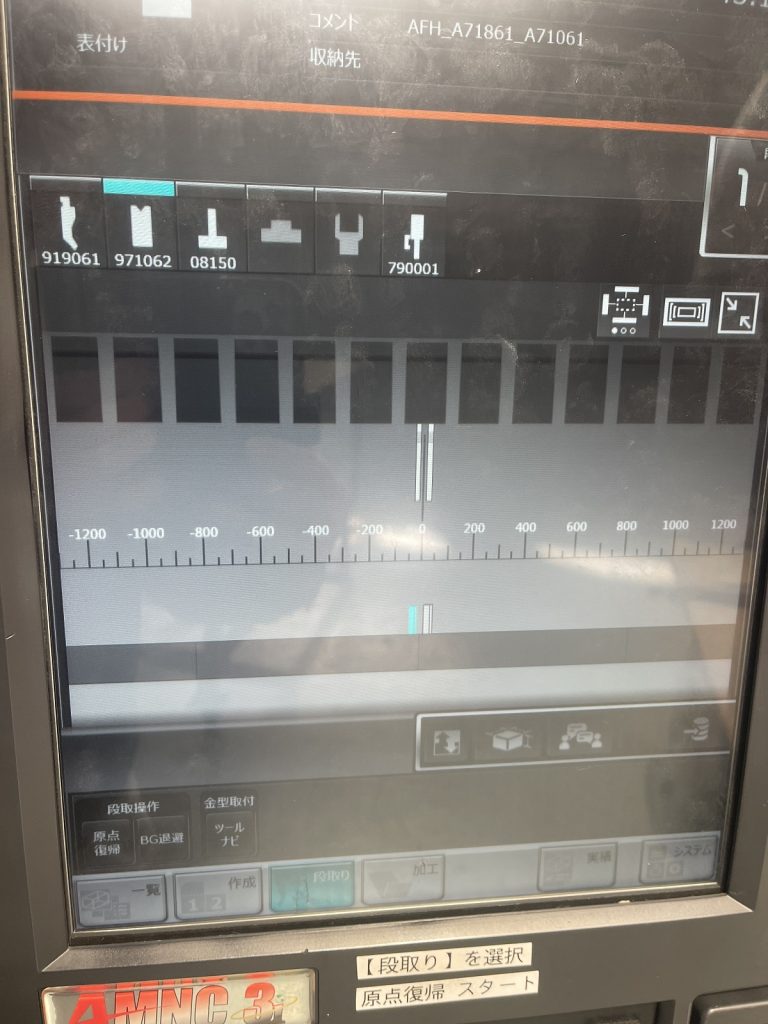
加工機画面
金型の取り付けを行います。金型種類と取り付け位置はプログラムで設定されています。
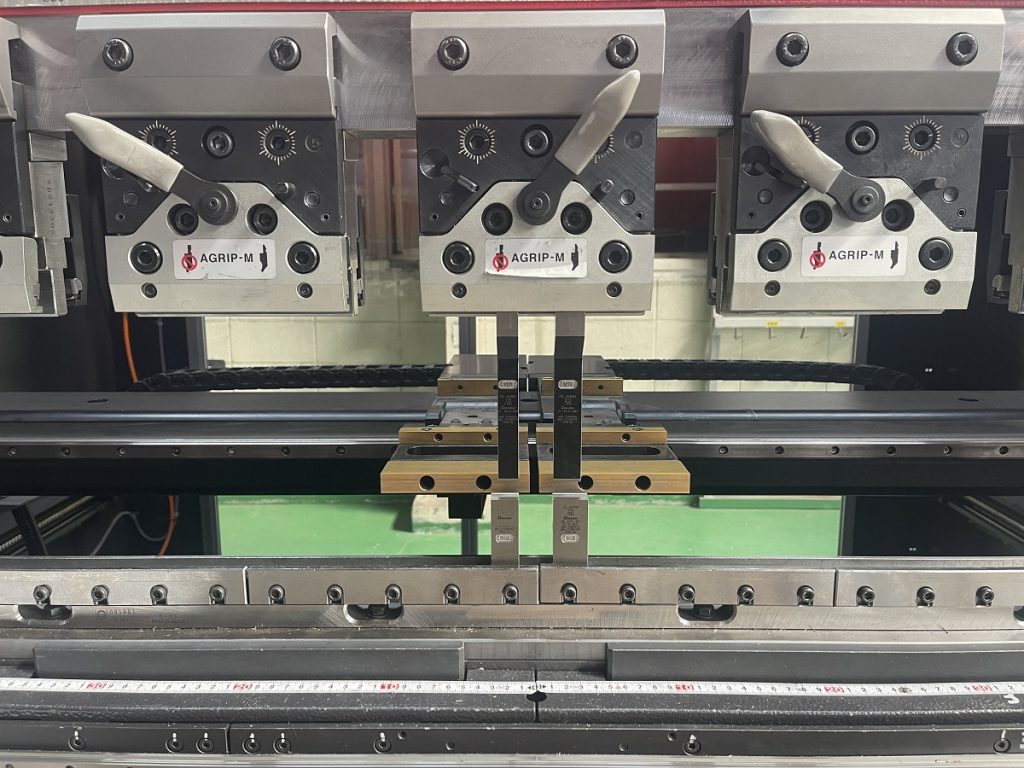
画面に従い金型を取り付け
画面を見ながら金型を取り付け、スタートボタンを押して曲げ加工を開始します。
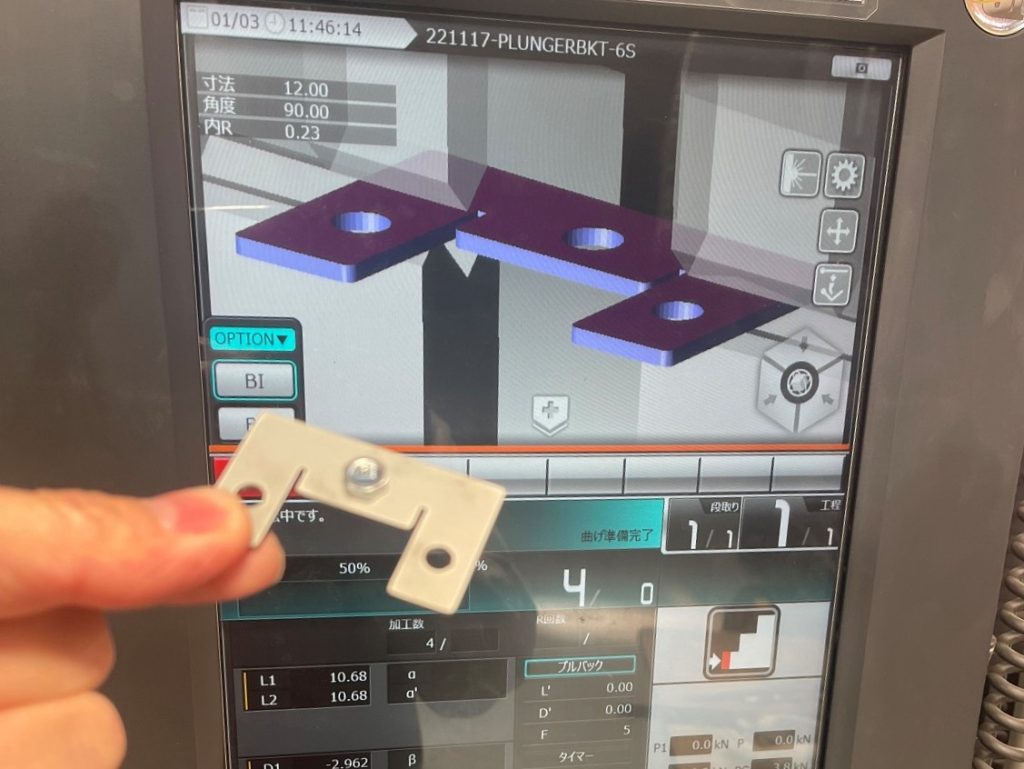
曲げ位置の確認
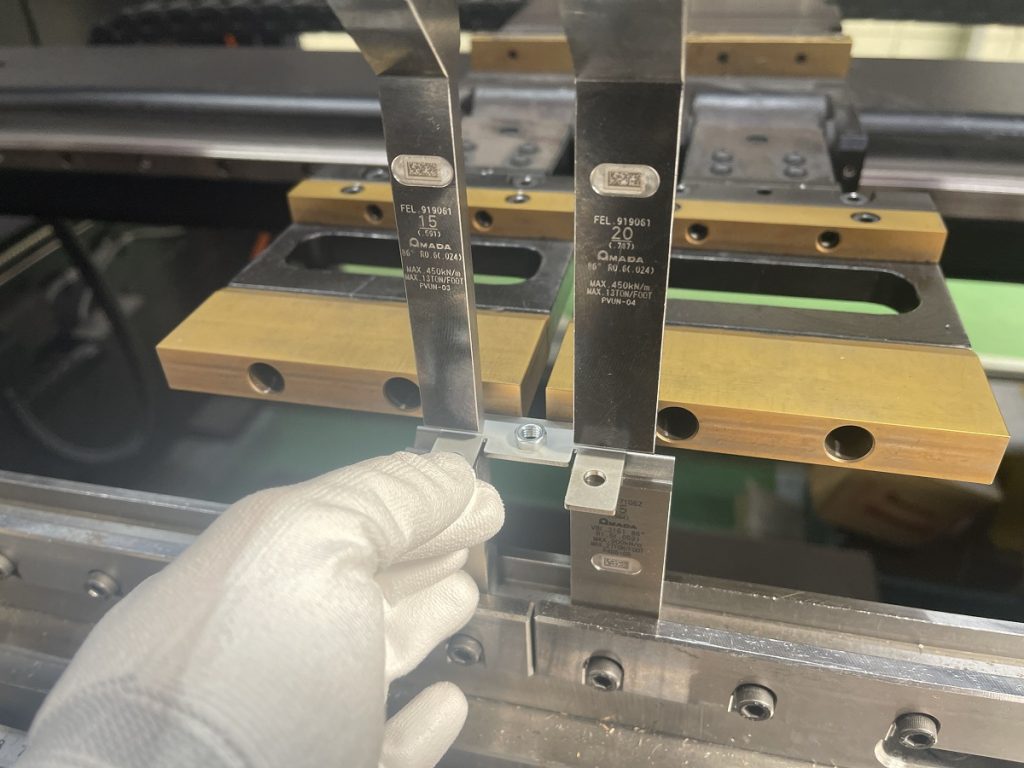
ワークをバックゲージに当て曲げる
曲げ加工が完了し、板金プランジャブラケットが完成しました。
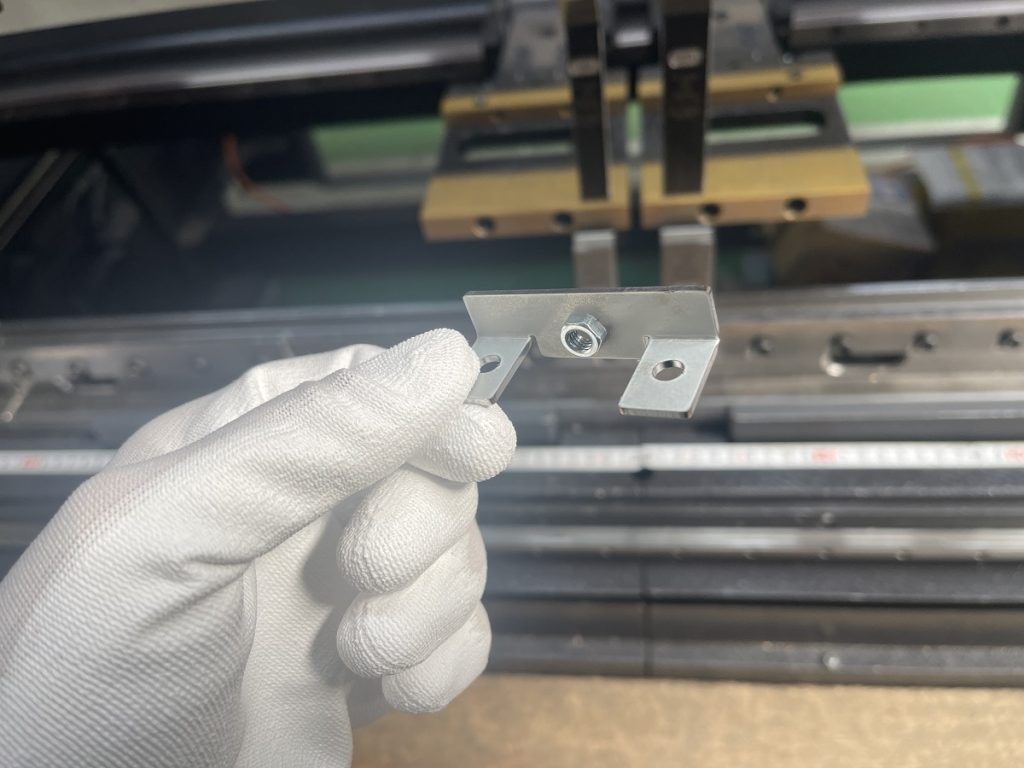
板金プランジャブラケットの完成
板金プランジャブラケットを多数個治具に取り付けます。
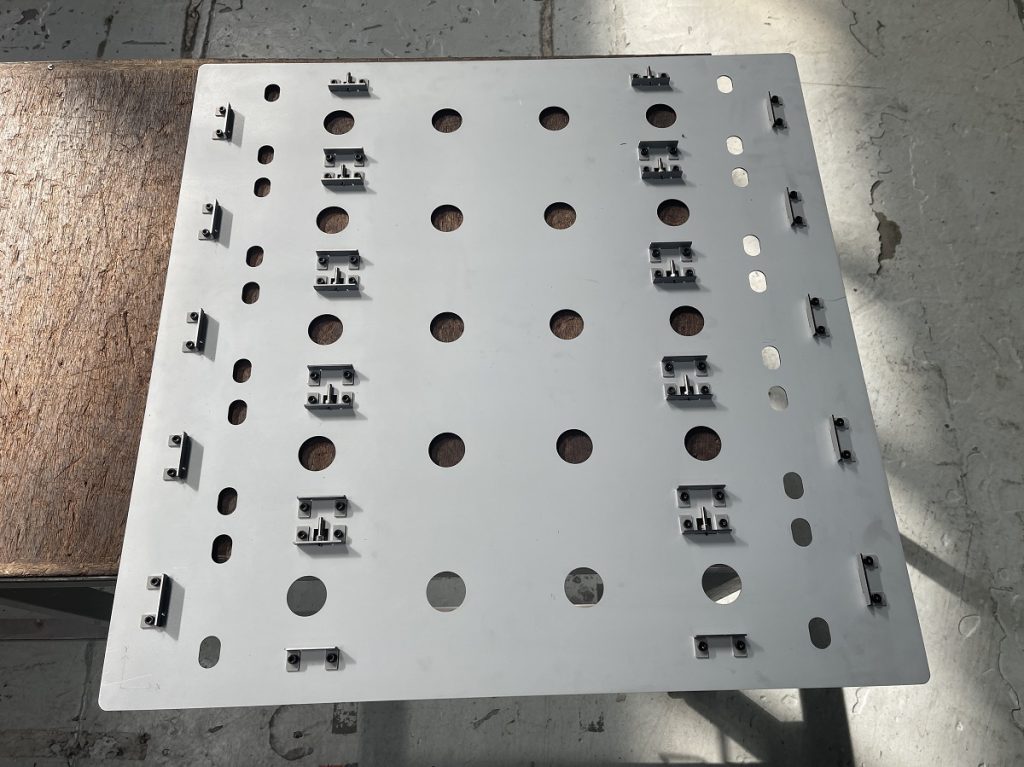
多数個治具に取り付け
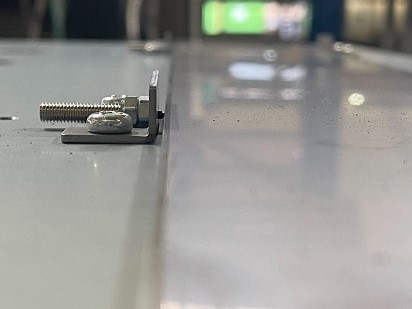
スケッチ材セット可能
スケッチ材が無事にセットできる事が確認できました。
5.改善後の評価
多数個治具をセットした状態でレーザー加工し、時間を計測します。
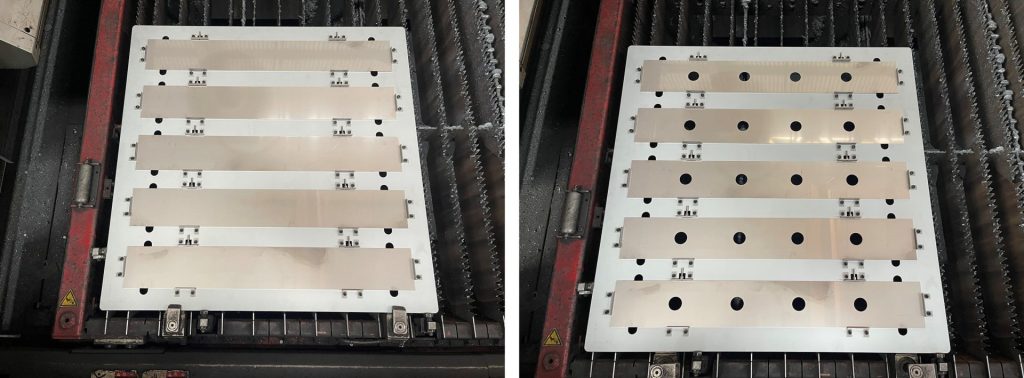
多数個治具の評価
結果、加工は130秒/回でした。テーブルAからBに交換する時間35秒を足して165秒です。
1週間の加工500枚の場合で計算すると、4.6時間です。
改善前の9.3時間から4.7時間も削減することに成功し、加工時間を半減することができました。
レーザー機オペレータも「加工が早く終わり、ほかの仕事が入るようになった」と喜んでくれました。
6.まとめ
いかがでしたか。
6つめの板金レシピ「ナット取付け部品で板金加工のムダを削減する方法」では、製造現場で課題だった時間のかかる加工を板金プランジャブラケットを使った多数個治具で工数を半減する事に成功しました。
<設計と製造のポイント> ●プランジャブラケットとスケッチ材のすきまを1ミリで設計 ●プランジャが当たるようにナット穴高さを設定 ●meviy板金加工の「ナット取付」サービスで簡単に手配可能 |
少しの工夫で広がる板金レパートリー!
次回も皆さんのアイデアにつながるような情報を発信していきますね、お楽しみに。