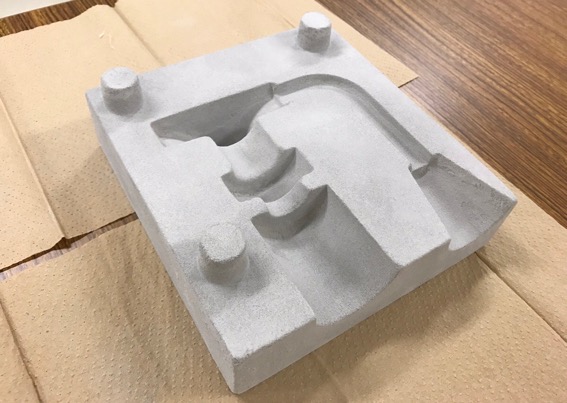
個人利用のほか、製造業の中でも導入が進みつつある3Dプリンター。こちらは福岡県福岡市の機械メーカー・渡辺鉄工さんが、実際に3Dプリンターを活用して製造した鋳型です。3Dプリンターを用いた鋳型は、溶融した金属をはじめとした高温の素材を取り扱ううえで解決しなければいけない課題が数多くありました。しかし、この鋳型では素材として耐熱材「TCaST(ティーキャスト)」を使用することで、1700℃の高温にも耐えうる耐熱性を実現しています。
当ブログでは、3Dプリンターを使った樹脂金型の製作や、自助具の製作ができるファブラボなど、さまざまな3D技術の活用現場を取材してきました。新しい技術を使った先進的な取り組みに触れるなかで、3D技術を用いたものづくりが、少しずつではありますがきちんと前進していることを実感しています。
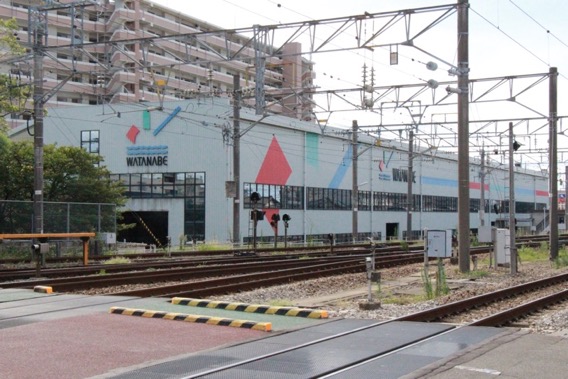
渡辺鉄工さんによる鋳型の製造も、3Dプリンターを用いたものづくりにおける革新的な取り組みの一つ。いったいどのようにして、この3Dプリンター鋳型が作られたのでしょうか。meviyスタッフの進藤が現地に向かいました。
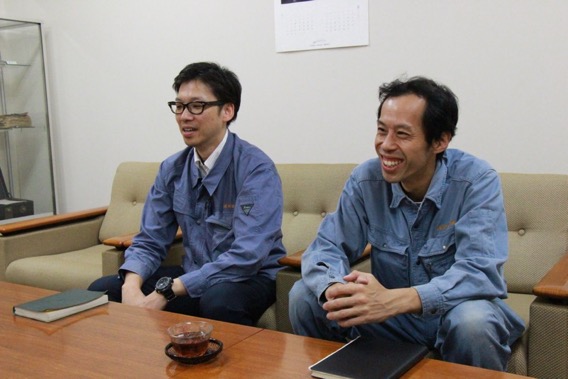
工場をご案内いただいたのは3D・IoT事業開発チームの猿渡宣弘さん(左)と製造部の河野恵太さん。まずは工場を見学させていただきました。
創業はなんと明治時代、新旧の機械が同居する工場見学
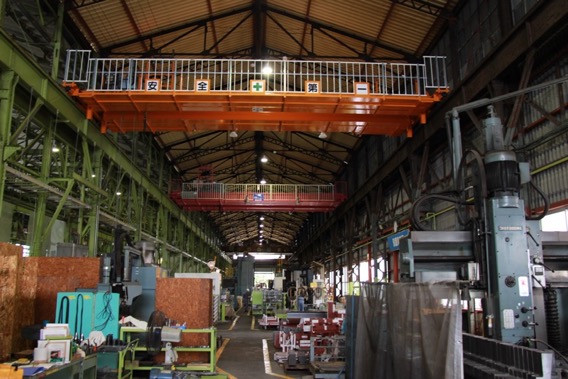
渡辺鉄工さんの創業は1886年(明治19年)、今年で132周年を迎える老舗メーカーです。主に鋼板処理装置のスリッターラインや自動車用ホイール生産設備のリムライン、防衛関連設備を製造しています。売上の半分を占めるリムラインは、なんと国内シェアの90%以上を誇るのだとか。
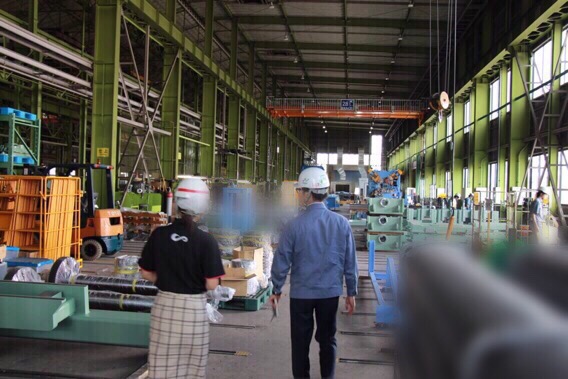
工場内には長年使い込まれた加工機が立ち並び、なんとも歴史ある佇まいを見せています。あちこちに巨大な機械や製品が置かれ、あまりのスケールにあたかも自分たちが小人になった感覚に。ここでは、溶接や機械加工、組み立て部門など各セクションに分けて作業を行っているそう。
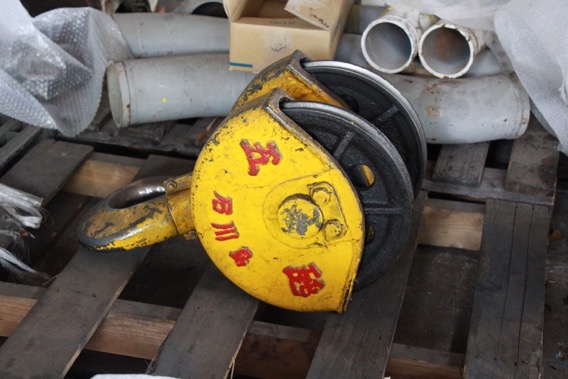
ふと目に入った部品をよく見ると、1937年(昭和12年)から約80年もの間使われていたクレーンのフック部分でした。去年の9月まで実際に使われていて、今は記念に残しているとのこと。こんなに年季のあるものが、普通に工場内に転がっているとは驚きです。ちなみに、これだけで重さなんと80キロ! 見た目に反して意外と重い……。
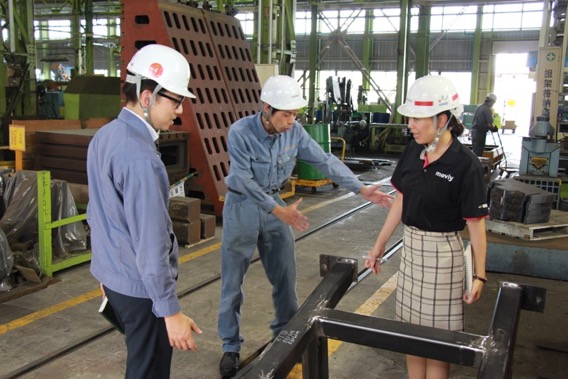
こちらは主に溶接などを行う製缶場(せいかんじょう)。機械の骨格ともいえるフレーム部分を作成する最初の工程を担うところです。高さ3メートル、横幅6メートルのサイズまで加工できるそう。
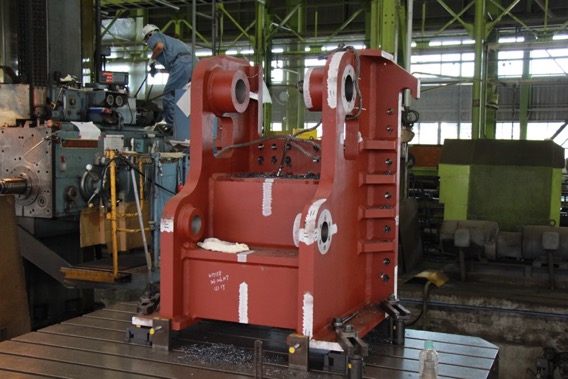
正面のレンガ色の部品を加工しているこの機械は、穴の内面をくり広げて切削していく「中ぐり盤」。作業者が上に乗り、ハンドルを使って操作します。40年以上前から稼働しているそうで、スケールの大きさには圧巻のひとこと。
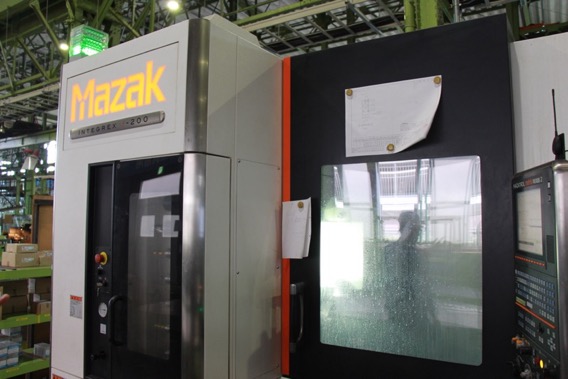
そして、その隣に設置されているのはヤマザキマザック社の複合加工機。新旧の工作機械が、工場内でいっしょに稼働しています。
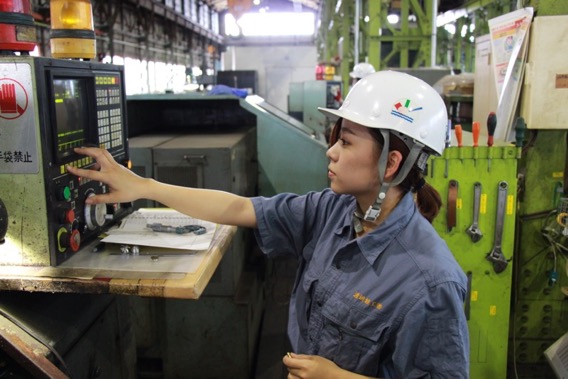
工場内には若い従業員も多く、テキパキと作業をこなしていました。プログラムを操作している松永りえさんは今年で入社3年目。丸棒の削りだしや図面作業まで、少し技術的に難しい部分も今ではスイスイ進められるそうです。
「基本的に先輩が後輩にレクチャーをして、技術をしっかりと教え込みます。また、昔のデータからどうやって構成を組むのかなどを学んだり、社員同士で技術勉強会を開いたりもしています」(猿渡さん)
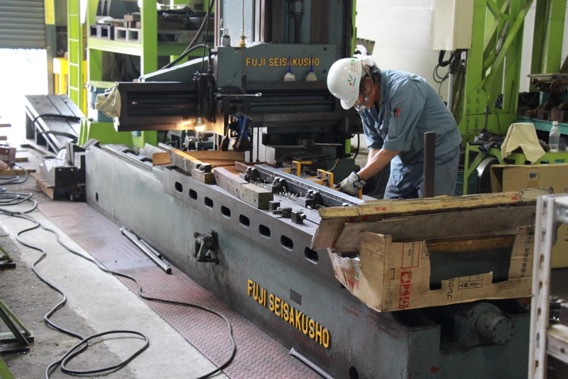
渡辺鉄工さんは防衛関係製品を始めとした特殊な製品製作を多く手がけているため、工場内にはそれ専用の、特殊な加工設備が設けられています。そのひとつがこの平削盤(油圧プレーナー)。長大な工作物の平面を切削するためのもので、機械と職人の技術によって精度の高い部品を仕上げています。
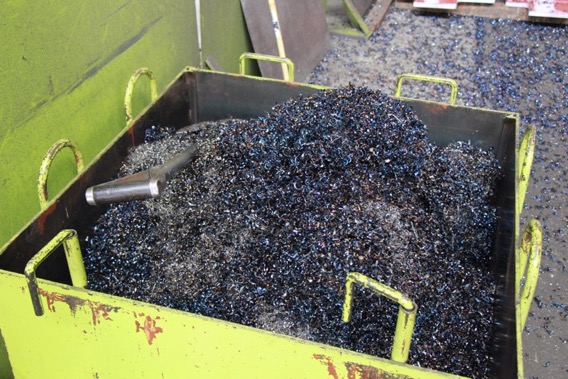
その隣には、金属を切削したときに出た削り屑。何やらキラキラしてとてもきれい……。素人には全て同じ削り屑に見えますが、職人はこの削り屑を見ただけでどの工具で切削したのかわかるそうです。
実はこの削り屑、渡辺鉄工さんも想定外のニーズが。「以前、イベントでコスプレイヤーの方とお話する機会があったのですが、削り屑を紹介したところかなり気に入っていただけたようです。工場に訪れて、削り屑を背景にして撮影したいと言われていました。普段捨ててしまうものにこんなニーズがあるなんてと驚きました」と猿渡さん。両者まったく想像しなかったであろう、異色のコラボですね。
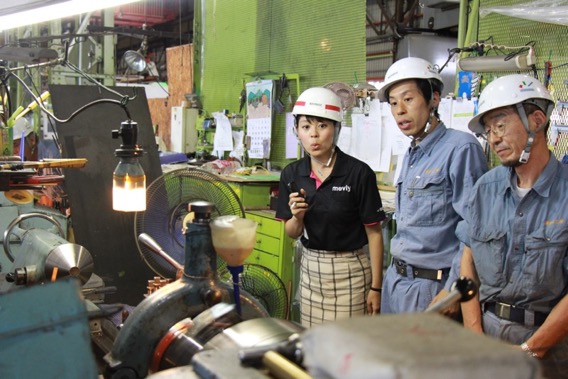
こちらは町工場などでは一般的な軸の切削機械。訪れたときは内径の切削を行っていました。作業時は切削の熱で煙がもうもうと立ち上っていて迫力満点……!
「外気温度によっても、完成品の寸法が変わってくるので、出社したときに工場内の温度を測り、常温になったときに規定の寸法になるように計算しながら削っています。図面の寸法通りにやったのでは上手くいかないことも多いので、どれくらい削るのかというのを自分たちの経験から判断するんですよ」と河野さん。さらっと答えてくれましたが、それってかなりの職人技なのでは……? やはり最終的な段取り部分は人の手が必要なのですね。
いよいよ鋳型の製造現場へ、3Dプリンター鋳型の発掘体験!
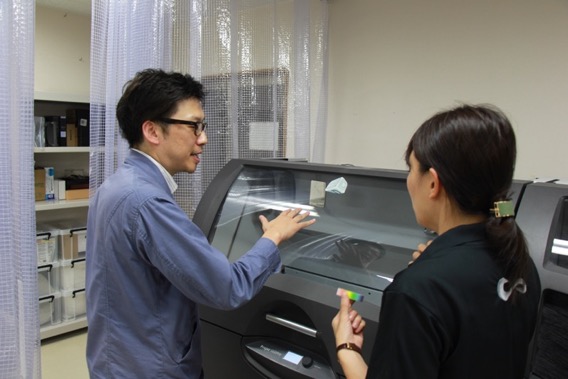
工場見学のあとは、いよいよ3Dプリンター鋳型の製造現場を見せていただきました。3D技術部門は機械部門に加えて新しく立ち上げられたもので、現在かなり力を入れて運営されているとのこと。工場2階には光造形タイプのプリンターなど、さまざまな3D機器が設置されていました。
鋳型の造形にかかる時間はおよそ6時間半とかなりスピーディ。しかし、短い取材時間では造形のスタートから完成までを見届けることができないため、今回は事前に造形いただいた鋳型を掘り出す、最後の工程を体験させていただきました。
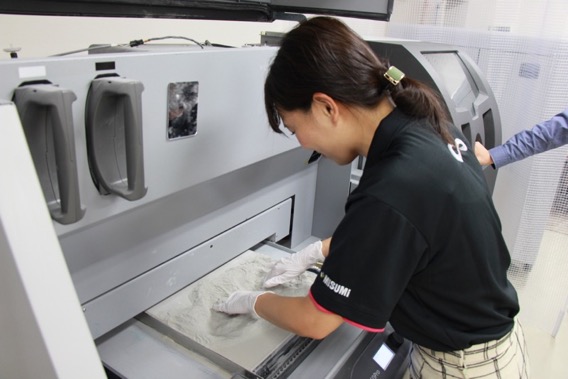
米・3Dシステムズの3Dプリンターを使用し、太平洋セメントが開発した無機粉末「TCaST」を用いて作成した鋳型を粉剤の中から取り出していきます。そもそも3Dプリンターで鋳型が作れるなんて想像もしていなかったので、今までになく新鮮な作業です。
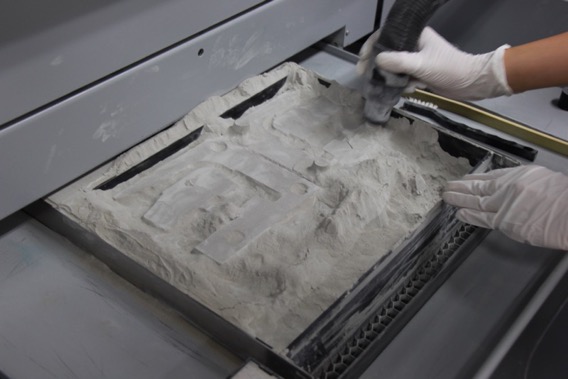
吸引ブロワーで粉剤を取り除きつつ、作業を進めます。だんだんと鋳型の輪郭が見えてきて、まるで宝探しをしているかのよう。
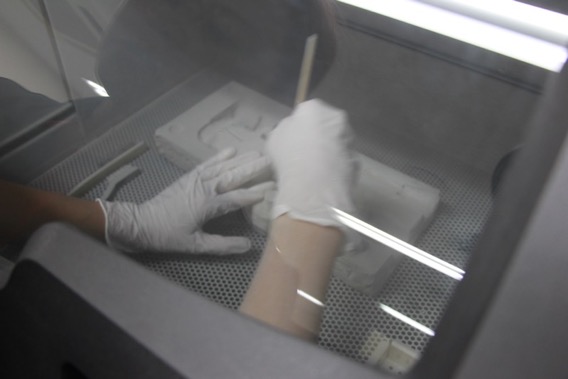
大部分の粉剤を落としたらあとはブラシで細かい粉剤を落としていきます。
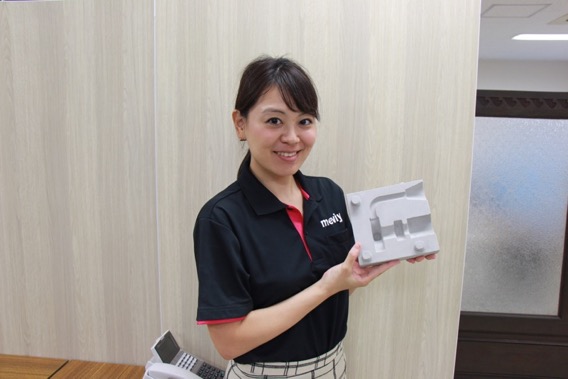
鋳型の発掘完了! 思わず顔がほころぶ進藤。
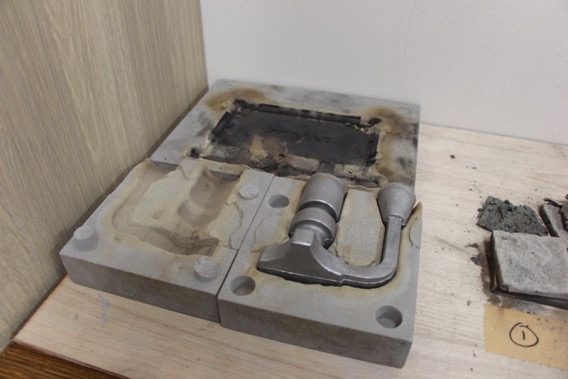
こちらが実際に溶湯を流し込んだ試作品。熱による鋳型の損傷もほぼなく、できあがった鋳物にも気泡などの欠陥もありません。表面のざらつきもなく滑らかで、すぐにでも実用化できそうなレベルでした。
従来は木型を作って鋳型を作ってと、全ての段取りを考慮すると3〜4カ月ほどかかっていた納期が、3Dプリンターを利用することでおよそ1カ月程度まで短縮できるそう。今までと比べると驚異的なスピードです。
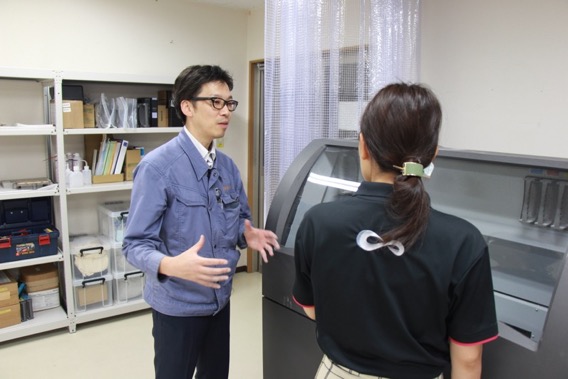
3Dプリンター鋳型のメリットについて、「通常、鋳型は製品の形となる木型を起こして、木型を転写して溶湯を流し込む砂型を作ります。しかし、そうすると木型の作成が必須ですし、砂型から鋳物を外しやすくするための抜き勾配の作成も必要になってきます。その抜き勾配があることによって、旋盤やフライス加工をするときにきれいなチャッキングができないという難点がありました。ですが3Dならば木型も必要なく、型をそのまま抜くだけなので、加工やコスト面でも大きな利点があります」と語る猿渡さん。
たしかに木型のコストもかからず、作業時間も短縮できるのはこの成形方法ならではの大きな魅力。3Dプリンター鋳型の運用がかなり現実味を帯びてきました。
3Dは、企業の良さを活かす新たなツール
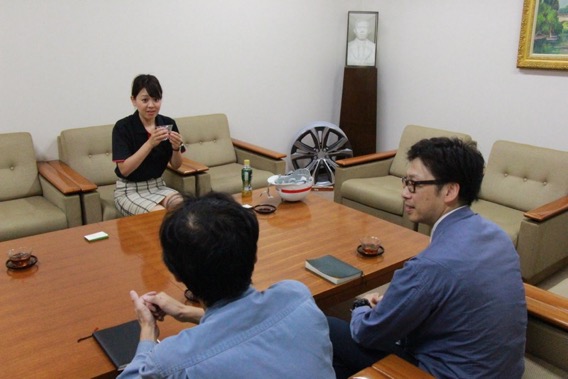
長い歴史を持ちながら、積極的に新しい技術を取り入れたものづくりをされている渡辺鉄工さん。どういった経緯で今のような取り組みを始められたのか、お話を伺いました。
進藤
今回はご案内いただきありがとうございました。歴史ある佇まいの工場の中に最新の機械がたくさんあって驚きました。そもそもですが、なぜ3Dプリンターを使って鋳型を作ろうと思われたのでしょうか。
河野さん
実は、最初から3Dプリンターで鋳型を作ろうとしていたわけではなかったんです。かといって、業務効率化を考えて導入したのでもありませんでした。
猿渡さん
とある会社さんから3D機械のメンテナンスを頼まれたことがきっかけです。そこで、やはり自分たちの手元に実機がないとやり方がわからないよね、ということで3Dプリンターを購入しました。その後、購入したものを実際に使うなかで「会社で機械組込み用の鋳物を買っているけど、実は鋳型って3Dで作れるんじゃないか」と思いついたことが、3Dプリンター鋳型ができたきっかけです。
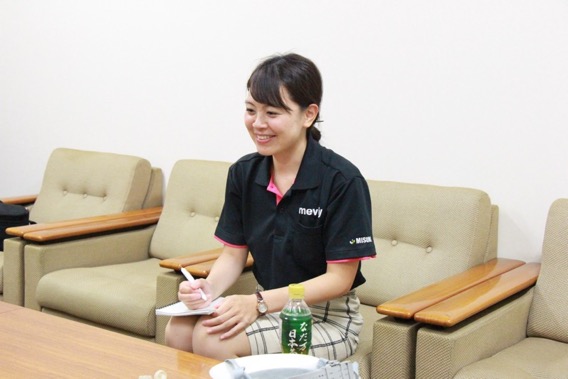
進藤
どちらも最初に目的があって動き出したわけではなかったんですね。ちょっと意外でした。ちなみに周りの鋳物屋さんの反応はいかがでしたか?
河野さん
皆さんちょっと戦々恐々としていましたね(笑)。
進藤
やはりそうですよね。今までやっていた仕事がなくなってしまうかもしれないわけですから。
河野さん
鋳物の製作は、相当なコストと時間がかかります。やっていることはすごく大変な一方で、完成した製品は労力に見合わないくらい安いんです。仕事がなくなると心配する反面、コスト面の改善や人が少ないから自動化をしたいという鋳物屋さんも多くいらっしゃいました。
猿渡さん
自動化を「仕事がなくなる」と考える人もいれば、一方で「新しい可能性だ」と考える人もいますよね。私は、今までと同じことをやっていても何も変わらないじゃないですか、と良く言うんですよ。だから、ただ鋳物を作るだけじゃなくて、新しいことをやって付加価値を付けて、コストをもっと上げてもらえるようにしたらいいじゃないか、と。
進藤
自動化で作業効率化できたら、そこで浮いた仕事量を別のところにかければ良い、という考え方ですね。
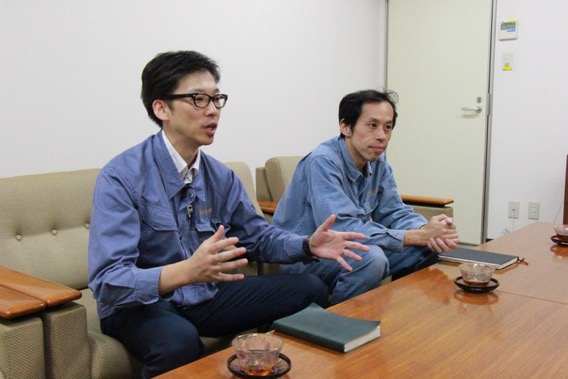
河野さん
今は3Dをやっているので、3Dに関連した新しいビジネスモデルができればいいなと思っています。3Dの設計ができたら自動でCAM出しして、加工して……と、3Dプリンターを発端として、風上から風下まで一貫して行えるような仕組みができればまた付加価値が生まれますよね。そうすると、今まではやったことがないような新しい仕事に挑戦するための環境ができます。
猿渡さん
鋳物だけでなく、新しく仕事が作れるように間口を広げて、渡辺鉄工の良さをさらに活かす新たなツールとして3Dを活用していきたいなと考えています。渡辺鉄工は歴史が長いぶん、旧態依然で変わらないところもありましたが、3Dプリンターを購入したのがきっかけで、もっと新しいことをやっていこうと、どんどん会社の体質が変わってきたのを実感しています。
進藤
新しく仕事を生み出すために3Dを活用するというのはとてもいい視点ですよね。3D自動化に向けて、現場ではどのような取り組みを行っているのでしょうか。
河野さん
うちが作る製品は防衛関係製品を除いてほとんどが一品一様で、同じものはあまり作らないんですよね。だから現場にはどんな場面でも使える汎用機を揃えています。ですが、今は人手不足でなかなか職人さんが育たないこともあり、そこは3Dデータを上手く使って、多品種少量生産の中でうまく自動化ができないか、やり方を検討しています。
猿渡さん
属人的な技術が自動機の導入で楽になる、というのが3Dデータを使った加工の良いところなのですが、逆に継承すべきところはしっかり人が受け継いでいかないといけないんですよ。基本的にプログラムを作るのもやはり手作業で、感覚的に覚えていないとそれをデータに反映できません。機械を買ったからといってポンと自動化できるわけではない、というのが難しいところです。
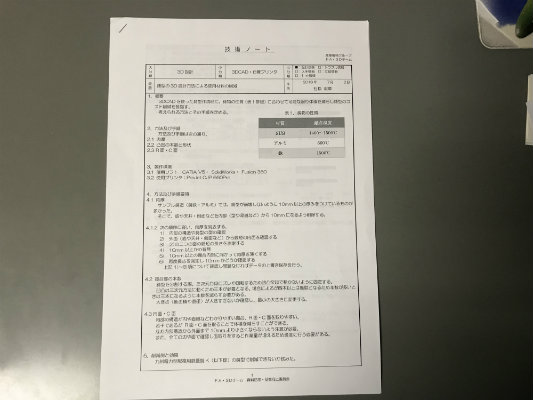
猿渡さん
教育の一環として、若手社員には「技術ノート」というのを作らせているんですよ。自分の作業中に失敗したことをノートにまとめ、それを発表する機会を作って、みんなで失敗を共有して今後は気をつけようね、という試みですね。技術以外にも、ロボットやAIがどういうものなのか、といった業界の最新動向について学ぶ社内勉強会なども積極的に行っています。
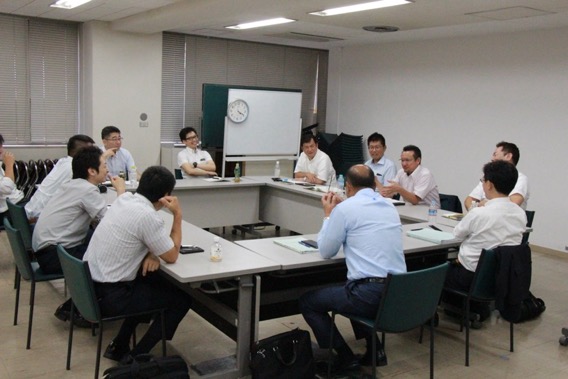
河野さん
また、会社としては社長の渡邉剛が中心となって行う新商品研究会「BLABO(ブラボ)」で、社外の方を含めた会員同士が悩みを共有したり、アイデアを交換したりといった場も設けています。地元企業が集まって横のつながりができて、お互いに高め合うようになるといったポジティブな効果が起きているようです。
進藤
3Dもそうですが、教育面や働き方などすごく多面的にアプローチされていてすばらしいですね! 最後に今後の展望についてお聞かせいただければ。
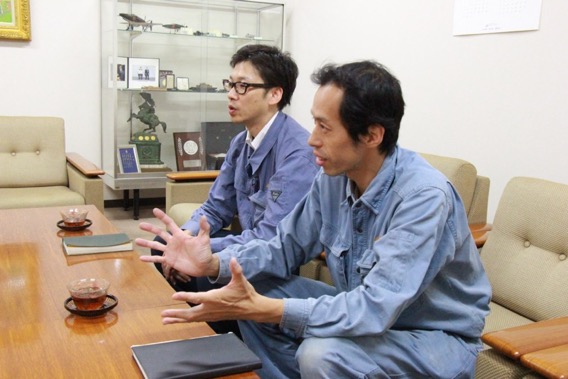
河野さん
これは若い人によく言うんですけど、この先何があるかわからない。だけど一つだけわかるのは、製造業の労働人口は間違いなく減っていくということです。ですので、そのときに私たちはどうすべきなのかと考えて動いて、その時代にあった立ち振る舞いを意識していきたいですね。
猿渡さん
3Dはすごくいい技術なんですよ。2次元はどうしても情報が少なくて頭打ちになってしまいますが、3Dは情報量が多いので様々な方面への広がりが期待できます。そういった技術はためらわず、積極的に使っていくべきなんですよ。これは業界として変わっていかないといけないところです。ものづくりは保守的では前進しない。これまでのスタイルを守り続けるのは、もう時代が許してくれないでしょう。
進藤
おっしゃる通り、新しい技術が広がっているからこそ、今とこれからを見据えた働きがすごく重要になるんですね。ミスミも、サービスが製造業界の3D化推進の一助となれるようよりいっそう頑張ろうと思います。本日はありがとうございました!
まとめ
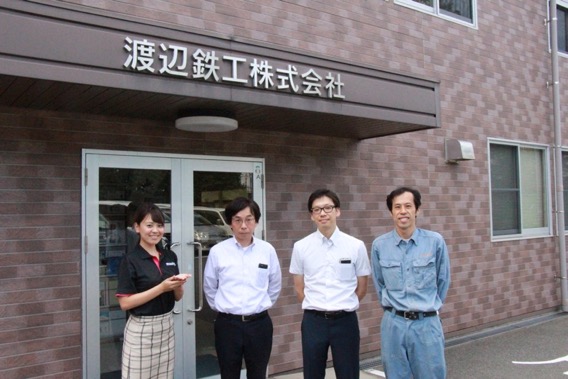
最後に常務取締役の分山康宏さんも加わり、会社の前で記念撮影。
創業132年の歴史を持ちつつ、今もなお新しい技術を積極に導入、3D領域の草分けともいえる3Dプリンター鋳型の製作といった先進的な取り組みを多数行う渡辺鉄工さん。かなりの老舗でありながらも若々しいベンチャースピリットを持ち合わせており、そのバイタリティには頭が下がります。
3Dについて含蓄のあるお話をたくさん聞けた今回の取材。3次元設計ソリューションサービス「meviy」を推し進めるミスミにとってはかなり身に沁みるトピックでした。「業界として変わっていかないといけない」という猿渡さんの言葉が強く印象に残っています。
ますますその活用範囲を広げる3D技術。これからも、meviyブログでは、ものづくりや3Dプリンターを用いた新しい試みを追いかけていきます。
(ノオト / 神田 匠)
取材協力:渡辺鉄工株式会社
●3次元設計ソリューションサービス「meviy」
▼関連記事
これまでの金型の常識を覆す!? 長野県・有限会社スワニーの「デジタルモールド」技術を体験してきた
3Dプリンターで自助具を製作! デジタルファブリケーションを作業療法に応用した「ファブラボ品川」探訪記