みなさんこんにちは!
電通総研の金型ソリューションチーム“Mold Planner”です。
私たちは金型設計製造を行われている製造業のみなさまに、30年以上にわたりCAD/CAM/CAEなどのITツールをご提供し、業務改革をお手伝いしています。
前回(第7回)は、「全体最適とは何か」というテーマで、3Dモデルをベースとした情報伝達の重要性についてお伝えさせて頂きました。
今回は、金型設計と連携することによる「工程管理」業務の効率化について事例を交えてご紹介いたします。これからお話する内容は、次の通りです。
- 「金型設計」と「工程管理」間の情報伝達に関する問題
- 工程設計の標準化
- 工程設計の効率化
- 最新トピックス
「金型設計」と「工程管理」間の情報伝達に関する問題
工程管理は金型づくりの中核であり、設計者が実現したい金型をどのように作るかの方針決め(工程設計)、各工程への指示、進捗管理を一手に請け負う業務です。
また、大日程の見積もりや工場負荷の把握(受注可否や外注依頼の判断など)といった重要な業務も担っています。
その工程管理の中でも金型製作の計画を決める「工程設計」は、非常に重要な業務です。「ムリ」な計画を立てれば、残業、休出、外注が増え原価増となり、余裕のある「ムダ」な計画を立てれば、人や機械の稼働率が下がり生産性低下となります。多くの企業では、ベテランが奮闘しながら、しのいでいるのが現状ではないでしょうか?
そのような重要な工程設計業務が抱えている問題を2つ取り上げます。
・工程設計は、豊富な知識と経験を持つベテランでなければ務まらず、属人化している。(工程設計の標準化)
・出図の遅延が多く、また工程設計に時間かかり、後工程に影響している。(工程設計の効率化)
これらの課題は、いずれも図面に起因しているため、工程管理だけでは改善することは困難であり、情報伝達手段から考え直す必要があります。これらの課題を掘り下げながら、解決するための施策について、取り組み事例を交えながらご紹介いたします。
工程設計の標準化
金型設計者は、頭の中で設計意図を考えながら、形状、公差、面粗度などを決め、加工できるかどうかも考慮しながら設計します。
しかし、金型設計のアウトプットが2D図面の場合、設計意図を2D図面に表現できるのは一部であり、大半の設計意図の情報は欠落してしまいます。工程設計者は、金型設計者の設計意図を今までの経験から想定して不足情報を補完し、加工工程を決定します。【図1】
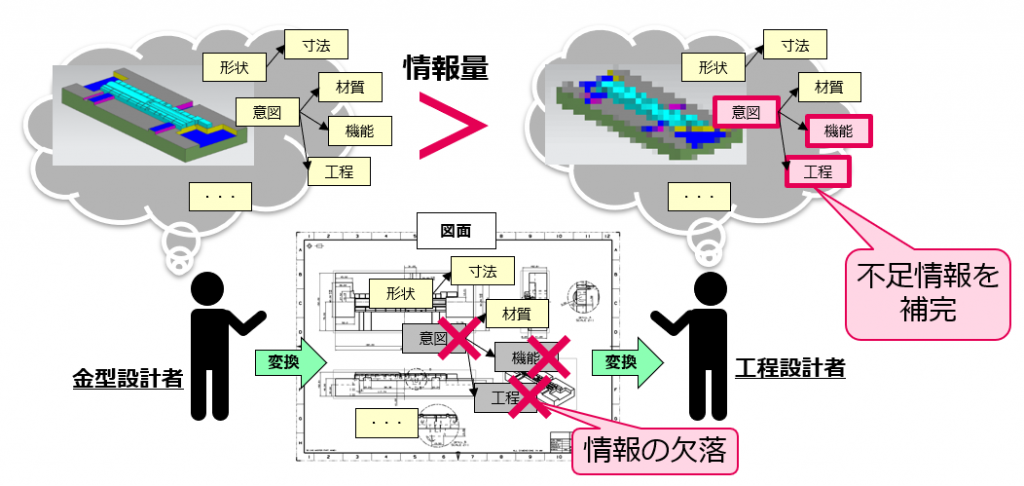
【図1】2D図面による伝達における情報の欠落
金型設計者の意図と異なった認識をすれば不具合となり手戻りが発生します。そのため工程設計は非常に重要な業務でありベテランを配置するのが一般的ですが、属人化しやすい業務とも言えます。
もし、設計意図に関する情報の欠落がなく、十分に設計意図を伝達できれば、人を限定することなく、属人化した工程設計業務を標準化することができるのではないでしょうか。
そのためには設計意図を確実に伝えられる3Dモデルベースの伝達手法が有効だと思われます。情報の送り手側は3Dモデルに様々な情報を追加することができ、受け手側はフィルタをかけて必要な情報を絞り確認できるため、金型設計者の設計意図を確実に工程設計者に伝えることができます。
また、設計意図を工程設計者に確実に伝えることができれば、それを実現するための工程が決まります。【図2】
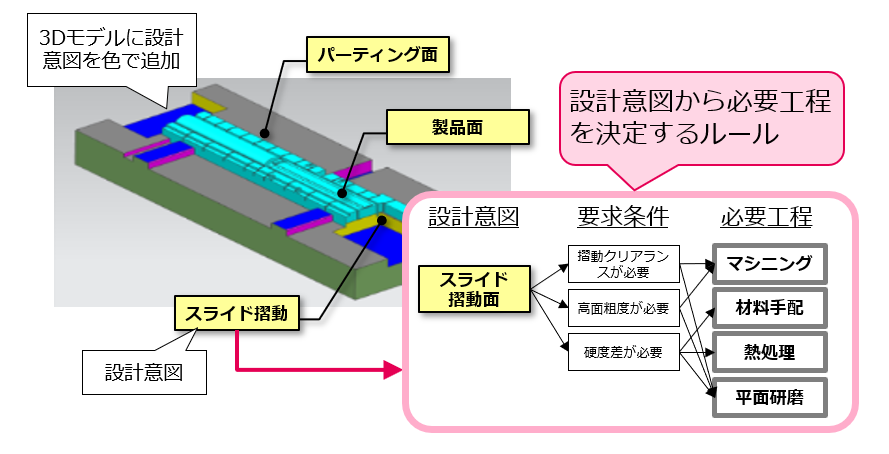
【図2】設計意図から必要工程を決定するイメージ
さらに3Dモデルから形状の制約(研磨が可能かどうかなど)を確認できれば加工工程は決定できます。このように設計意図から必要工程を決定するルールを構築することができれば、金型設計者と工程設計者の認識を合わせることができ、属人化した業務を標準化していくことが可能になります。
工程設計の効率化
工程設計業務は、金型部品ごとに図面や3Dモデルを確認し工程を決定する業務のため、部品点数が多い場合は非常に時間がかかります。
加工機が止まらないよう迅速に工程設計を進めたいところですが、以下2点の問題で後工程への指示が遅れるケースがあります。
(1)計画通りに出図されない
(2)図面の理解に時間がかかる
上記2つの問題に関して、さらに掘り下げてみます。
(1)計画通りに出図されない
金型設計が予定通りに出図できない理由は製品仕様の変更など様々ですが、設計作業を長引かせている要因に図面作成があります。3D設計しているにも関わらず、改めて2D図面に表現し直しているのは重複作業であり、間違いなく出図のタイミングを遅らせています。
情報伝達手段を図面から3Dモデルベースに変更することは、インフラ整備や各担当者の3Dモデルを扱うスキルなど幾つかのハードルはありますが、確実に出図のタイミングを前倒しすることができます。
(2) 図面の理解に時間がかかる
図面による情報伝達では、人が理解してアクションを起こす必要があり、部品点数が多ければそれだけ多くの工数が発生します。図面を理解する繰り返し作業が発生する工程設計を効率化するには、図面の情報伝達では限界があります。
前章でお伝えした通り、設計意図から工程を決める標準化は可能です。そのため、3Dモデルベースとした情報伝達であれば、3Dモデルに付与された設計意図をシステムが自動取得でき、標準化された「加工工程DB」を利用すれば、システムが工程を決定することが可能です。
以下に、3Dモデルベースの工程設計事例をご紹介いたします。【動画1】
【動画1】3Dモデルベースの工程設計
工程設計業務は工程を決める以外に工数を見積もる業務も担当しています。工数見積もりも重要な作業であり、工数を読み違えると計画が大幅に変更となり、ムリ、ムダな作業が発生するため、より精度の高い工数を見積もることが工程設計者に求められています。
工程見積もりとは異なり、工数を見積もるには加工段取りや加工範囲を考慮する必要があります。工程設計者は、図面や3Dモデルを確認しながら詳細な加工方法を頭の中で考え工数を見積もるため、非常に手間がかかります。また、加工する形状に大きく影響するため、工程決めとは異なり効率よく工数見積もりするには別のアプローチが必要となります。
工数を見積もる手法として、3Dモデルを有効活用したロジックが3つあります。
- 形状特性分析ロジック
- 形状比較ロジック
- CAM算出ロジック
「a.形状特性分析ロジック」は、加工形状の特性を読み取り、形状から求めた情報から工数(加工時間)を見積もる手法です。
例えば、3Dモデルからポケットや穴等の加工形状を自動認識し、丸穴が開いている方向の数から段取り数、素材形状と部品形状の体積差から荒取り加工時間、高精度と指定している加工面の表面積から仕上げ加工時間を求めます。これらの算出方法を標準化し、システム化することで工数見積もり作業を自動化することができます。
加工形状の認識や工数算出を高速に処理できるため、新規性の高い部品の見積もりに適しています。以下に形状特性分析ロジックを利用して工数算出した事例をご紹介します。【動画2】
【動画2】形状特性分析ロジックによる加工工数見積もり
「b.形状比較ロジック」は、過去に製作した膨大な部品情報の中から、見積もり対象の部品と形状が類似している部品を検索し、その部品の実績工数を参考にする手法です。
類似する部品形状を検索できたら、見積もり対象部品と詳細に形状比較し、具体的な形状差異を確認した上で実績工数を調整します。3Dモデルと加工時間の実績を紐づけることで、類似部品の見積もりに適した手法です。以下に形状比較ロジックを利用して工数算出した事例をご紹介します。【動画3】
【動画3】形状比較ロジックによる加工工数見積もり
「c.CAM算出ロジック」は、標準加工工程をCAMテンプレートとして作成し、CAMの削り残し機能を利用しながら簡易パスを生成し、加工時間を算出する手法です。加工シミュレーションで実際の切削長を算出することができるため、より精度の高い加工工数を見積もることができます。
ただし、CAMの演算処理が必要なため、部品の大きさ、部品点数などによっては演算時間が長くなるため運用に乗せるために工夫が必要です。これら3つのロジックの組み合わせにより、工数見積もりの作業を効率化できます。
ただし、これらのロジックは常に最新の実績情報と照らし合わせて、精度を向上させる必要があります。よって、ブラッシュアップの仕組みも併せて考える必要があります。どのロジックが最適なのかは製作する金型の種類によって異なるため、ブラッシュアップすることを前提にロジック検討が必要です。
また、3Dモデルベースの工程設計から導き出された工程、工数の情報をCSV形式等の外部ファイルとして出力し、工程管理ソフトのスケジューラ取り込むことで、工程入力ミスを未然に防止し、工程入力作業工数を大幅に削減できます。【図3】
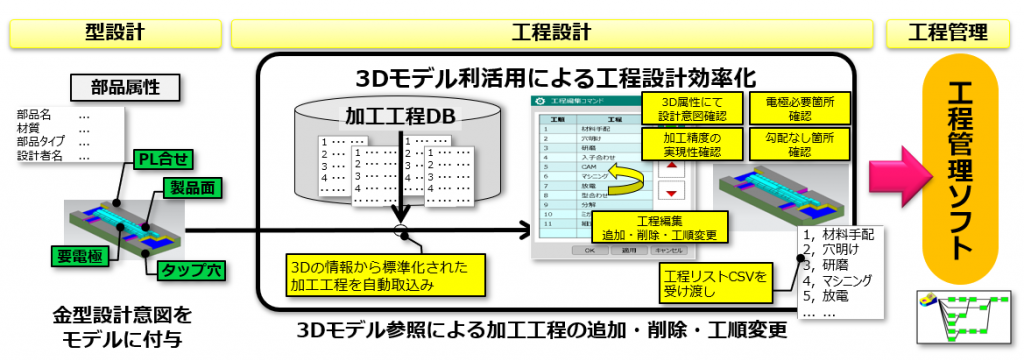
【図3】3Dモデルベースの工程設計
最新トピックス
金型設計やCAM担当者がアウトプットした3Dモデルや帳票を工程管理者や加工担当者が確認する場合、深い階層のフォルダ内に格納されたデータを引っ張り出す作業はミスを発生させる原因です。間違えたファイルを開くことにより段取りを間違えてしまうケースもよくお聞きします。
前章では、3Dモデルベースで工程設計した工程、工数の情報を外部ファイル経由で工程管理ソフトに取り込む話をさせて頂きました。その外部ファイルには、工程、工数の他、出図した3Dモデルや帳票のファイル名も一緒に記載し、工程管理ソフトに取り込むことができます。
ファイル名情報も一緒に取り込むことで、スケジューラの各タスクに3Dモデルや帳票を紐づけることができるようになり、加工担当者がスケジューラのタスクを確認しながら、即座に3Dモデルや帳票を閲覧して段取りすることができます。常に最新の情報を確認できるため、設計変更があった場合でも、混乱することなく正しい情報を素早く加工担当者が受け取ることができます。
以下に、加工担当者の方がスケジューラによりタスクを確認しながら、3Dモデルを閲覧する事例をご紹介します。【動画4】
【動画4】スケジューラに紐づく3Dモデルを閲覧
私たちは金型設計と工程管理の連携だけではなく、様々なソリューションを取り揃えています。ご興味のある方は、ぜひ、「部品製造の効率化」ホームページにお立ち寄りください。
今回は全体最適の具体的な事例として「金型設計‐工程管理」についてご紹介しました。繰り返しになりますが、工程設計は、金型の設計と製造をつなぐ重要でかつ属人化しやすい業務です。3Dモデルを有効活用しながら、業務の可視化・標準化・システム化することで全体最適の効率化を試みてはいかがでしょうか。
次回は、これも多くの企業でお困りの「金型設計-購買」の連携について事例を交えてご紹介いたします。
ぜひ、次回の記事をお楽しみに!