これまでは、主に切削加工に着目しながら、どのように部品の“カタチ”を作るのかに焦点を当ててきました。今回は、設備や装置部品等でよく使われる材料について、特徴だけでなく装置部品の製作事例を紹介しながら材料の選び方を解説します。
第12回からは、材料や、表面処理、品質保証などの、設計に関わる周辺の知識について共有していきたいと思います。
目次
1. 装置部品で良く使われる材料
設備・装置などの部品設計を任されたときに、皆さんはまずどのような材料を使おうとイメージするでしょうか?
当社でも様々な分野のお客様から、試作や少量生産の部品製作のご依頼をいただいてきましたが、分野によって良く使われる材料は様々です。
まず大切なのは、材料の特性はもちろんですが、どのような材料の形状や規格があるのかを知ることです。規格の形状をうまく利用することで、無駄のない合理的な設計も可能になると思います。
今回はまず、装置部品にどのような材料の形態や規格があるのかをご紹介し、その選び方について解説していきたいと思います。
2. 材料の一般的な形状とは
材料の選定を行う際には、まずどのような材料の形が存在するのか知ることが第一ですね。
通常、フライス系の切削加工を用いる部品ではブロック材やプレート材が利用されます。旋盤系(旋削加工)の場合は、丸材やパイプ材が良く利用されます。それ以外にもフラットバーやアングル材など、様々な形状の規格材料が存在します。
部品に求められる機能や形状を踏まえて、どのような材料を組み合わせて部品を製作するのが合理的なのかを考えながら設計する習慣をつけると良いと思います。
今まで解説してきた通り、特に切削加工では材料から除去する量が多かったり、加工する面が多かったりするほど加工工数が増大して加工賃がアップします。
まずはどのような規格の材料があって、どのように組み合わせるのが合理的なのかを考えていきましょう。
主な材料の形状は、以下のようなものがあります。
表1 一般的な材料の形状
材料 | 形状イメージ | 特徴 |
ブロック材 プレート材 |
![]() |
一定以上の厚みを持つブロック状の材料 機能部品全般に利用される 主にフライス系の切削加工に用いられる 6F材など高精度な材料も用いられる |
丸棒 | ![]() |
中身の詰まった円筒状の材料 軸形状部品に多く利用される 主に旋盤系(旋削加工)に用いられる 直径や長さは規格によって決まっている |
板材 | ![]() |
薄い板の材料 カバーや補助部品等に多く利用される 主に板金加工用に用いられる 板厚や大きさは規格によって決まっている |
フラットバー | ![]() |
帯状の材料 製缶部品の取り付け面やリブなどに多く利用される 幅や肉厚、長さは規格によって決まっている |
丸パイプ | ![]() |
丸いパイプ状の材料 支柱や軸形状部品に多く利用される 製缶加工や旋盤加工に用いられる 直径や肉厚は規格によって決まっている |
角パイプ | ![]() |
四角いパイプ状の材料 架台や躯体などの製缶部品に多く利用される 断面は正方形や長方形もあり、形状や肉厚、長さは規格によって決まっている |
アングル材 | ![]() |
L字断面状の材料 躯体などの構造部材として製缶部品に良く利用される 形状を活かしたブラケットやレール等にも利用される 肉厚や形状、長さは規格によって決まっている |
チャンネル材 | ![]() |
コの字断面状の材料 躯体などの構造部材として製缶部品に良く利用される 特に強度の必要なベース部分に多く用いられる 肉厚や形状、長さは規格によって決まっている |
H型鋼 | ![]() |
H字断面状の材料 躯体などの構造部材として製缶部品に良く利用される 特に強度の必要なベース部分に多く用いられる 肉厚や形状、長さは規格によって決まっている |
3. 装置部品の製作方法と材料の選び方
装置を設計する際には、まずその構成する部品を「購入部品」と「加工部品」とに分けますね。
基本的には、ギアやベアリングなどの機能部品や、モーターなどの電装部品などは、購入部品を購入して利用するのが一般的と思います。
また、フランジや継ぎ手、ハウジングなどの構造部品も、購入部品を活用することで、安価かつ合理的な設計が可能ですね。こういったときに、私も設計者の立場としては「MISUMI(総合Webカタログ)」のサイトを良く眺めて、まずは購入できる部品がないかを探します。
そして、購入部品では賄えない部品を、新規に設計して「加工部品」として製作していくことになると思います。
加工部品は大きく分けると次の3種類に分かれます。
- 機能部品 – リンク、シャフト、ギアなど
- 構造部品 – 躯体・架台など
- 補助部品 – カバー、ガイドなど
それぞれの部品の用途や目的によって、合理的な製作方法や材料の選定も異なってくると思います。
A 機能部品
精度や剛性が必要となる、装置の“心臓”とも言える部品ですね。このような部品はやはり、高精度な加工が可能な切削加工などの「機械加工」により製作される必要があります。
使用される材料も、「ブロック材」や「丸材」からの削り出しがメインとなりますね。もちろん、部材を無駄にしないように、溶接してから機械加工するような製作方法も良く用いられます。
B 構造部品
機能部品をあるべき場所に固定し、保持して機械全体として成立するための役割を果たします。架台や躯体、支柱などといった部品です。
全体的な剛性や強度も必要ですが、部品としても大きくなるため、「パイプ材」などを溶接等で組み立てるフレーム形状が基本となると思います。
こういった溶接でフレーム形状を作ることを「製缶加工」と呼んだりしますね。
もちろん、既成のアルミフレームをネジ止めで組み立ててフレーム構造を作ったり、板金部品をリベットだけで組み立ててフレーム構造を作ったりと、構造部品の作り方も様々な選択肢があります。
大型の構造になる程、「製缶加工」による製作が合理的となります。
機能部品を取り付けたり、お互いの製缶部品同士を連結したりするような部分は、高い取り付け精度が必要となりますので、機械加工による高精度な加工が必要となる場合があります。
また、軽量でありながら強度を上げ、剛性を保つために、しばしば「リブ」と呼ばれる補強を入れることがあります。このリブには、「フラットバー」などが用いられます。
C 補助部品
機械そのものの本来の能力・性能には影響しないけれども補助的に必要な部品ですね。カバーや補助ブラケット類、シュートやホッパーなどの部品などです。
このような強度・剛性や加工精度はあまり必要ない部品の多くは、板材を使用した「板金加工」や「溶接加工」によって製作されることが多いです。
ここからは、設備や装置で使われる部品にどのような材料や加工方法が使われているのか具体的に見てみましょう。
図3-1のような、簡単な搬送治具があったとします。
(本ブログ用に簡略化してあります)
この搬送治具は、ボールネジをモーターで駆動することで、トレーが1軸方向に移動するだけの簡単なものです。
まずは一例としてこの搬送治具に使われている部品を見ていきましょう。
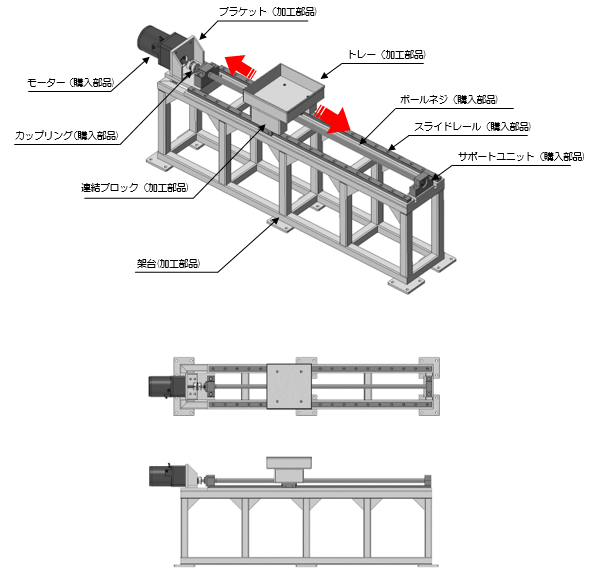
図3-1 搬送治具 外観
架台の上に、サポートユニットを介してボールネジを取り付けてあります。水平に動くためにスライドレールを両側に配して、連結ブロックでスライドレールのスライダとボールネジのスライダを連結し、トレーを取り付けます。
ボールネジの端部には、カップリングを介してモーターが取り付けられています。モーターはブラケットに取り付けられて、架台に固定されます。
購入部品は、モーター、カップリング、ボールネジ、サポートユニット、スライドレールですね。購入部品をある程度目星をつけたら、それに合うように加工部品の配置や形状を決めていくのが一般的ではないでしょうか。
ここで出てくる加工部品は、①架台、②ブラケット、③連結ブロック、④トレーの4点ですね。
それぞれの部品の作り方や材料の使い方を見ていきましょう。
3-1 架台
まずは「架台」の作り方から見ていきましょう。
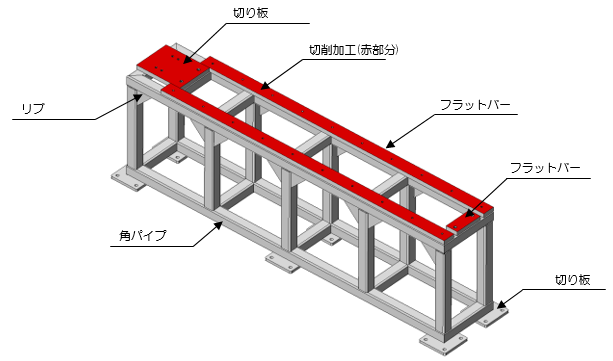
図3-2 架台 外観
この架台は角パイプをフレーム状に溶接で組み立てる想定とし、上面にフラットバーを配しています。上面には、スライドレールやブラケットなどが載ります。
これらの駆動部分は、お互いの相互関係がしっかりと精度よく配置されていないとうまく動きません。つまり、部品の取り付けに影響を及ぼす、平面度や穴位置の精度が必要になりますね。
一般的には、このようなときには、精度の必要な部分に切削加工を施します。(必要があれば下面側にも切削加工を入れる場合もあります)
このような取り付け用の面は、できるだけ範囲を狭くしておくと、切削加工による加工面が少なく済んで合理的です。フラットバーなどの規格材料を活用しながら、最小限の部材で設計することを意識すると良いと思います。
切削加工を施す範囲は、図3-2で赤色に示した部分ですね。今回はこれらが同一面になるように面削して、スライドレールやブラケットを取り付けるためのネジ穴を開ける想定としています。
上面側に配したフラットバーは、この切削加工で面を削る分も含めた選定が大切です。
例えば、仕上がりを10mmの厚みにしておけば、12mmの規格のフラットバーを利用して、2mm程度削れば良いことになります。
仕上がりを12mmとすると、鉄の場合は次の規格が16mmとなるので、4mm削らなければいけません。
どのような加工を施して、どのような素材を配置すれば合理的なのか、設計者の腕の見せ所でもあります。この辺りの材料の規格については、次回取りあげたいと思います。
下面側には、床面との取り付け用のベース板を取り付けています。ベース板もフラットバーや板材からの切り板を利用します。
また、フレームのクロスする部分にはリブを取り付けています。これによって強度・剛性が増大しますね。
このリブはフラットバーや板材を切り出して利用することが多いです。
リブを取り付けることで強度・剛性が増すのは、治具の使用時にメリットがあるだけではなく、切削加工する際にも有効です。
このような製缶部品に切削加工を施す際に、剛性が足りないと加工の負荷で切削面が振動し、きれいに仕上がらないケースがあるためです。
3-2 ブラケット
次に、モーターを固定するためのブラケットについても見ていきましょう。
このようなモーター固定用のブラケットは、モーターに応じた既成のブラケットもありますし、削り出しで製作しても良いと思います。
今回は、より部材を有効に使う例として、溶接と機械加工で製作する想定としてみました。
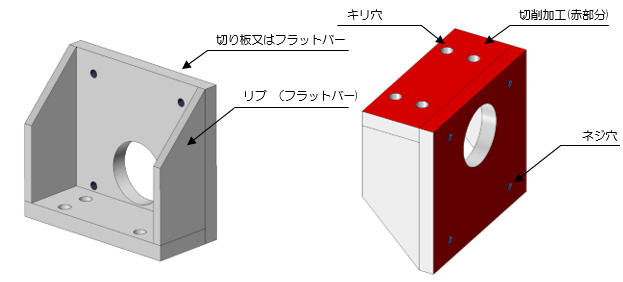
図3-3 ブラケット 外観
切り板又はフラットバーで、モーターの取り付く面と、架台に取り付く面をL字に溶接で組んで、両サイドをリブで補強しています。
リブにはフラットバーを45°に切断して部材を有効に使う想定としています。
このブラケットで重要なのは、モーターが取り付く面と、架台に取り付く面の平面度と直角度ですね。やはり溶接だけでは歪んだり、直角にはならなかったりするので、切削加工を施すことになります。
図3-3の赤色で示した部分が切削加工の範囲です。逆に、リブの側面などは精度が必要ないので、溶接したままで問題ありません。
また、モーターを取り付けるネジ穴は位置精度も必要なので、切削加工で開ける必要がありますが、架台に取り付けるためのキリ穴は必ずしも機械加工である必要はありませんね。
例えば切り板をレーザーカットで輪郭と一緒に穴まで抜いてしまっても良いかもしれません。
このように、切削加工を施す部分と、不要な部分を明確に意識しながら設計をすると良いと思います。一般的には、切削加工に比べ、レーザーカットなどの板金加工は加工賃を安く抑えられます。
3-3 連結ブロック
続いて連結ブロックについても見てみましょう。
図3-4が連結ブロックの外観です。ボールネジの駆動力を受け止めて、スライドレールに乗って姿勢を維持するために必要な部品です。
ボールネジのスライダと、スライドレールのスライダの位置関係をキープするために、加工精度が必要な部品となりますね。
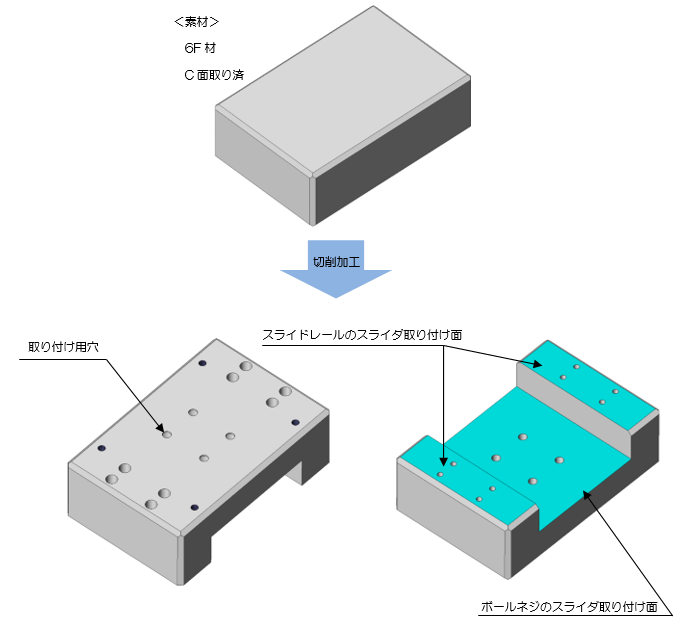
図3-4 連結ブロック 外観
特に、水色で示される面の平面度、平行度と高さ方向の精度が大切ですね。
やはりこのようなときは、ブロック材からの切削加工で製作することになると思います。
今回は素材の時点で6面が精度よく仕上げられた6F材から、中央部分の窪みを削って、穴を開けるだけの部品としてみました。
このように、動作や機構に関係する重要な部品はやはり切削加工の出番となります。
3-4 トレー
最後にトレーについても見てみましょう。
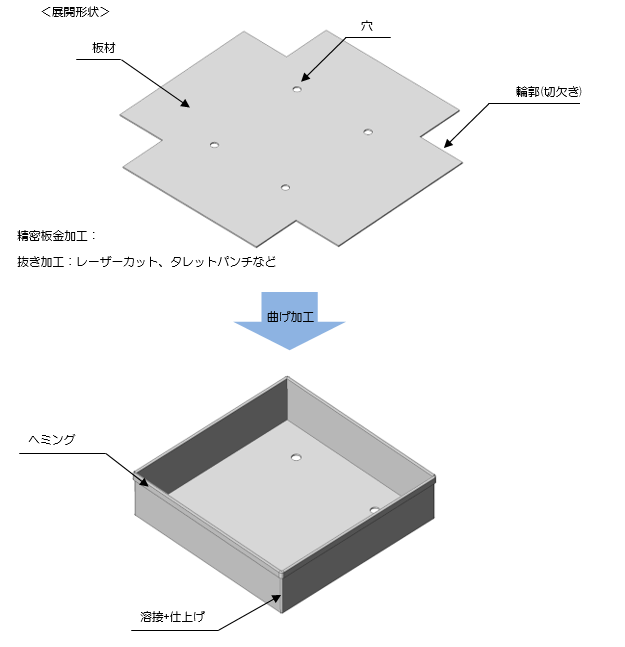
図3-5 トレー 外観
トレーは薄板を4方曲げて、角部を溶接して仕上げる想定としてみました。
このような板材の加工は、板金加工になりますね。
シャーリングと呼ばれる板材の切断機や、レーザーカット、タレットパンチと呼ばれる輪郭や穴の抜き加工用機械、ベンダーと呼ばれる曲げ加工用の機械を組み合わせることで、板材を好きな形に切って、曲げることができます。
まずは、レーザーカットやタレットパンチで図3-5のような展開形状を作ります。板金加工のうちの、「抜き加工」ですね。
大きな定尺の板から、輪郭や穴などの展開形状を抜きます。
その後、ベンダーでの曲げ加工をすると、4方壁の立った形状になります。
4角は溶接で接合して、溶接ビードをグラインダ等で仕上げると完成です。
人の触れる可能性のある部分は、切断面がそのまま残っていると、切傷する可能性があるため、縁を折り曲げて安全面にも配慮します。このような折り曲げ形状を、「ヘミング」や「アザ折り」等と呼びます。
いかがでしょうか、今回は簡単な搬送治具を例にして、そこに用いられる部品の材料の種類や加工の種類について解説していました。
設備や装置部品の加工方法としては、大きく機械加工、製缶加工、板金加工があり、それらを部品の用途や目的に応じて使い分けることが大切だと思います。
今回は具体例と共に、材料や加工の「使いどころ」を大まかにイメージできたのではないでしょうか。重要なのは、材料の規格や加工の特徴を知った上で、より合理的に組み合わせることだと思います。
できるだけ加工を少なくする、より簡単な加工で済ませる、材料の歩留まりを良くする、使う材料の規格を揃えて材料の種類を減らす等と言った観点を持ちながら、必要な機能や形状を設計していく習慣をつけていくと良いと思います。
次回は、良く利用される材料の種類ごとに、規格の形状や寸法をご紹介していきたいと思います。