これまでの連載では、設計した機械部品がどのように製作されるのかという観点を解説してきました。今回は少し目線を変えて、製作した機械部品がどのように品質保証されるのかをご紹介していきたいと思います。
目次
1.機械部品の品質保証とは
機械部品の品質保証とは、製作された部品が図面通りにできているかを保証することに他なりません。ここでは、製造現場でどのように品質が保証されていくのかを実務面からご紹介していきましょう。
品質保証とは、「自分たちの製作したものが、お客様からの要求に合致していることを証明すること」と言えます。その中で、加工現場の実務面では、製作した部品の仕様(材質や表面処理など)や寸法を確認し図面通りに出来上がっているかを、検査により確認することが主な作業内容となります。
まずは品質保証で求められる品質管理体制や、検査業務の位置づけについて簡単にご紹介していきましょう。
1.1 品質管理の体制
多くの製造現場では、ISO9001などの品質規格の要求事項に則った品質管理体制を構築しています。そのエッセンスをまとめると、おおむね下記のような品質管理体制をとっている製造現場が多いのではないでしょうか。
① 品質マニュアルなど品質管理の手法や手順・基準などを規定する文書を作成し運用・保管する
② 品質管理部門を設け、その責任者を配置する
③ 品質記録などの記録文書を作成し、運用・保管する
④ 品質管理部門の検査員を割り当て、教育し力量を評価する
⑤ 品質管理に必要な機材を用意し、適切な環境で運用・保管する
⑥ 製品実現のプロセスの中で、適切に品質の確認・管理を行う
ずいぶん堅苦しい文言が並びますが、「品質管理の基準や方法をルール化・文書化して、その通りに運用しましょう」という趣旨です。
①~④は社内体制の構築や教育・管理という面が強く、実務よりも上位の活動です。
⑤と⑥が製造現場で実際に行われている作業と考えてください。
1.2 品質管理と検査業務
品質管理部門は、製造現場によっては「品質保証部」や「検査部」という組織になります。そして、もっぱら検査業務を行う「検査員」が所属し、主に寸法測定などの測定実務を担います。基本的には、検査業務は図面通りに機械部品が製造されているかを確認する作業です。
また、製造の過程において、最終的な品質を確保するために行う検査工程も存在します。検査業務はおおむね次の3つの工程が行われます。
① 受入検査
② 工程内検査
③ 出荷前検査
① 受入検査
材料や購入品を調達した際に、自社工程に供する前にその品質を確認する検査工程です。材料や外注加工品の規格や寸法、外観に傷や打痕がないか等を確認します。後々、工程内検査や出荷前検査で問題が発覚した際に、受入検査で確認済みであるかどうかが非常に重要な意味を持ってくることがあります。そのほか、材質や熱処理などの外注工程が図面の指示通りであるかを確認するために、サプライヤーから提供される材料証明(いわゆるミルシート)や、各種証明書を取得し照合のうえ保管します。
② 工程内検査
製造工程の過程において、品質管理上必要となる寸法などを検査により確認する工程です。加工工程ごとに、検査部門で精密に検査するケースもありますし、加工機の機上でオペレータが検査するケースもあります。検査した内容は、「工程内検査表」や「工程管理表」などの品質記録文書に記録され、保管されるのが一般的です。
③ 出荷前検査
製造工程が完了後、出荷前に改めて品質管理部門で行われる最終的な検査工程です。様々な測定器具を駆使して、製品が図面の指示内容に合致しているかを検査します。
検査した結果は「検査表」などに記録され、品質記録として保管されたり、製品と一緒に顧客に提出されたりするのが一般的です。検査した結果、図面指示から逸脱する場合には、追加工等による修正や、顧客への良否判断の問い合わせなどを行います。
また、測定器具は、測定器メーカーで定期的に「校正」を行い、測定精度を保証します。測定器の「校正証明書」も品質記録として保管されます。品質記録は、ユーザー側で何か問題があった際に、製造工程で異常がなかったかを遡って確認できるような「トレーサビリティ」が重要となります。
2.品質保証に有効な検査 と検査器具
一般的に、機械部品の品質保証では、材質や表面処理などが図面指示通りであるかを確認するとともに、図面通りの寸法や幾何公差を満足しているかを検査により測定することが実務上の大きなウェイトを占めます。ここでは、実際に行われる寸法測定の検査項目と、用いられる測定器具の詳細について解説していきます。
設計をする際にも、最終的にどのような検査器具を用いて測定されるのかを想定しておくことは重要です。場合によっては、「加工はできるけど検査ができない」といったケースもあります。
2.1 外観検査
外観検査とは、目視や拡大鏡などで製品の外観表面を観察し、傷・打痕等のないことを確認する検査のことです。品質保証における検査業務では、寸法を測定することばかりに気をとられがちですが、まずは外観に問題がないことを確認することが基本となります。
もちろん、外観の傷や打痕などを確認する以外にも、バリや表面粗さの程度についても確認します。特に機械部品の場合は、バリの発生がつきものですので、どの程度まで許容されるかは事前に設計者との確認が必要です。通常は爪やシャープペンの芯などで触ったときに、引っ掛かりがあるかどうかがバリの目安となります。バリが確認された場合は、仕上げ工程に戻しバリ取りを行います。「指示なき角部は糸面取りのこと」などと図面で指示してあれば、糸面取りによりバリを除去します。設計の際にも、このような角部の処理についても指示するようにしましょう。
表面粗さは後述の表面粗さ測定器でも数値的に測定可能ですが、多くの場合は図2-1のような表面粗さ標準片を見比べて確認します。
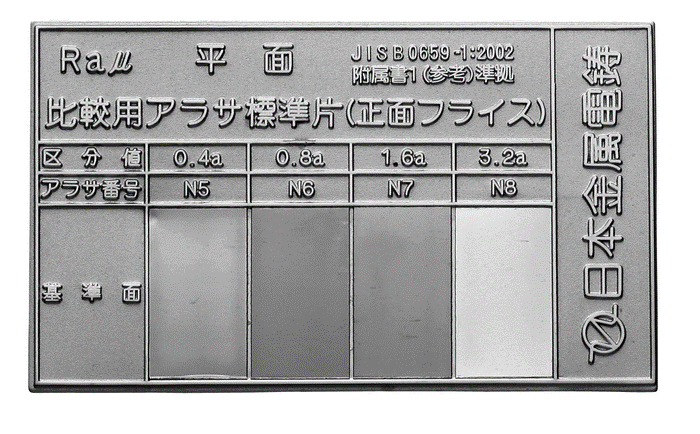
図2-1 表面粗さ 標準片
参考:MISUMI(総合Webカタログ) 表面粗さ測定器「Ra用アラサ標準片」
図面指示で表面粗さ(例えばRa3.2など)の指示があれば、このように外観検査で確認し、問題があれば表面粗さ測定器で厳密に測定するという手順が一般的だと思います。
2.2 測定器具による検査
品質保証における検査工程では主に、ノギスやマイクロメータなどの汎用的な測定器具を用いて寸法検査を行います。これらの測定器具は、取り扱い方によって読み取り寸法が変わってしまいます。下記に示すように正確な取り扱いが必要となります。
ノギス(ダイヤルノギス)
ノギスは、主に長さを測定する測定器具です。様々な部位を利用して外側寸法、内側寸法、深さなどを測定できる汎用的な測定器具と言えます。測定範囲に応じて各種大きさがありますが、広範囲になるにつれ測定誤差が大きくなります。測定範囲に応じて、できるだけ小さなノギスを選定することが重要です。
通常は下図のようなダイヤル式のノギスが用いられますが、デジタルで測定寸法が表示されるデジタルノギスも存在します。
(1)外観及び各部の名称
ノギスの外観及び各部の名称を図2-2に示します。
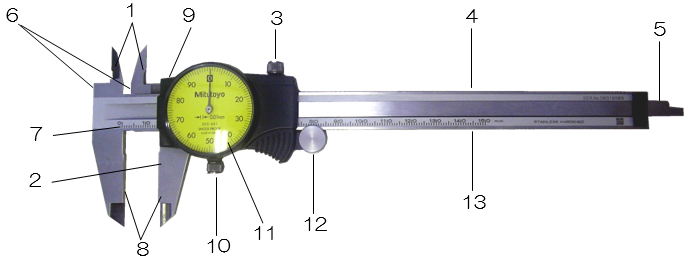
図2-2 ノギスの外観及び各部の名称
1 | 内側用ジョウ |
2 | 目盛読取り端面 |
3 | スライダクランプねじ |
4 | 本尺 |
5 | デプスバー |
6 | 段差測定面 |
7 | 本尺目盛 |
8 | 外側用ジョウ |
9 | スライダ |
10 | 外枠クランプネジ |
11 | ダイヤル目盛 |
12 | サムローラ |
13 | 基準端面 |
(2)読み取り方法
このようなダイヤル式の測定値は本尺目盛とダイヤル目盛の値を足して求めます。本尺目盛の値は、目盛読取り端面で読み取ります。図2-3に寸法の読み取り方法を示します。
例)下図の場合
A:本尺目盛の値 ・・・ 61㎜
B:ダイヤル目盛の値 ・・・ 0.87㎜
C:測定値(=A+B) ・・・ 61.87㎜
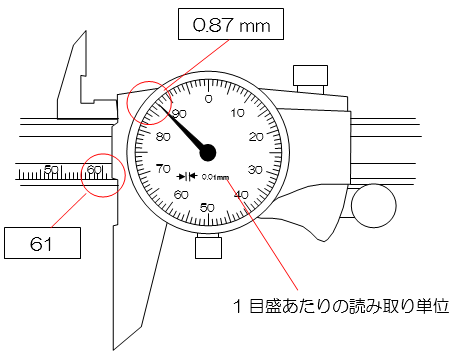
図2-3 ダイヤルノギスの読み取り方法
(3)測定の種類
ノギスの各部位を用いて、製品の様々な形状を測定することができます。
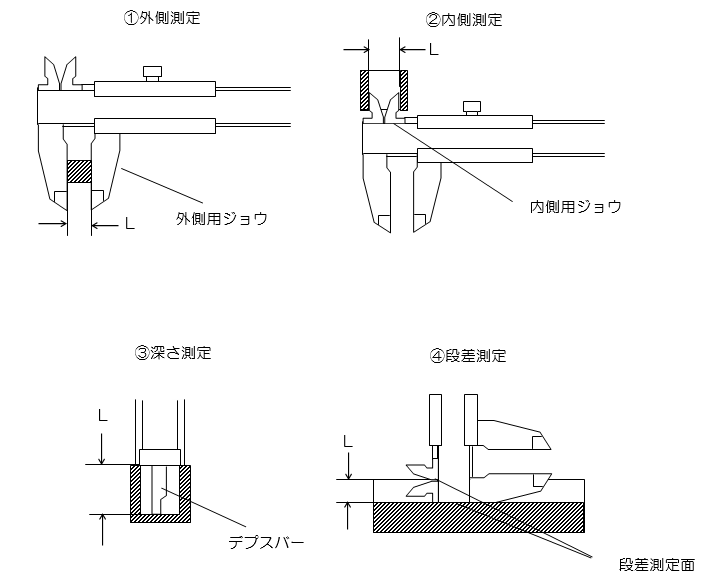
図2-4 ノギスによる測定の種類
(4)使用上の注意
①必ず測定前にブロックゲージにて精度の確認を行う
②必要以上の測定力をかけないこと
※一般的には測定圧力0.98~1.47N/m2(約100~150g)
※測定力が強すぎるとジョウが傾き、測定誤差が生じる
③測定物をできるだけ本尺に近い根元付近で挟み、測定面全体を測定物に密着させる
④内側測定の場合は内側用ジョウを測定箇所にできるだけ深く入れ、測定面全体を測定物に密着させる
(a)内側測定の場合は、測定値の最大値を求める
(b)溝幅測定の場合は、測定値の最小値を求める
⑤深さ測定の場合は、測定する面に対してノギスを直角にセットする
⑥段差測定の場合は、段差測定面を測定物に密着させる
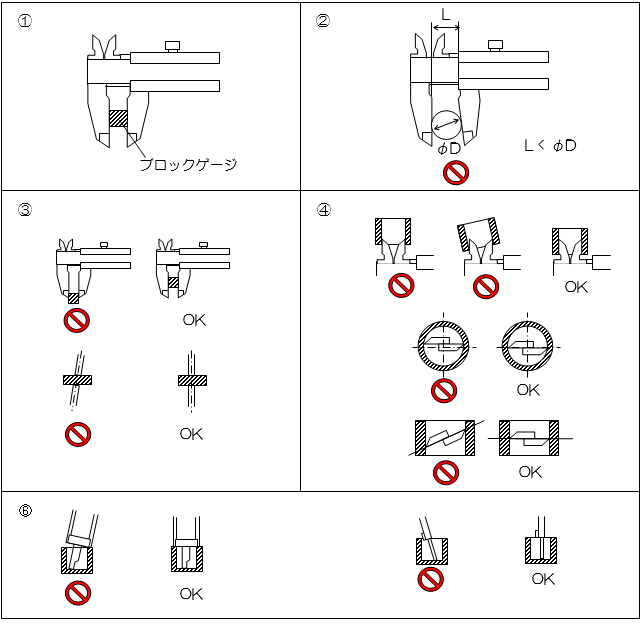
図2-5 ノギスの測定における注意点
外側マイクロメータ
外径マイクロメータは、主に外径・長さ・厚みを測定する測定器具です。ノギスよりも精確な測定精度が必要な場合に使用します。
(1)外観及び各部の名称
外径マイクロメータの外観及び各部の名称を図2-6に示します。
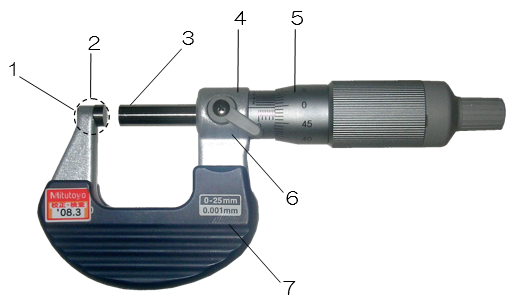
図2-6 外径マイクロメータの外観及び各部の名称
1 | アンビル(固定側) |
2 | 測定面(超硬チップ) |
3 | スピンドル |
4 | スリーブ |
5 | シンブル |
6 | クランプ |
7 | フレーム |
(2)測定方法
測定面をきれいにした後、測定物をアンビルとスピンドルに挟みシンブルを右回りに回転させます。ラチェットの音が1~3回「カチッ」と鳴ったら回転をやめ、数値を読み取ります。むやみに回しすぎないように注意します。
0.5㎜台、0.01㎜台、0.001㎜台の順に目盛を読み取り、その合計値が測定値になります。
例)下図の場合
A:0.5㎜台の目盛 ・・・ 5.0㎜
B:0.01㎜台の目盛 ・・・ 0.36㎜
C:0.001㎜台の目盛 ・・・ 0.009㎜
D:測定値(A+B+C) ・・・ 5.369㎜
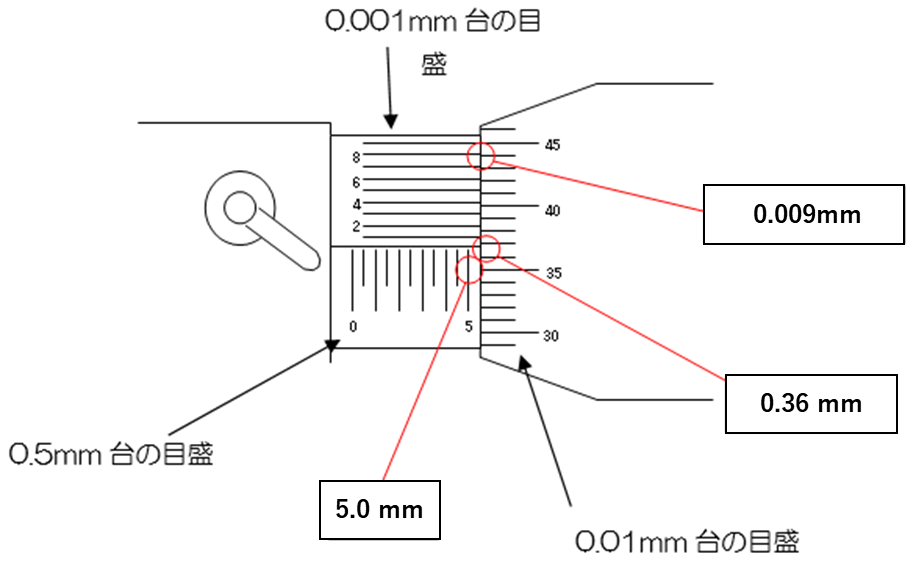
図2-7 外径マイクロメータの読み取り方
内径マイクロメータ(ホールテスト Holtest)
内径マイクロメータは穴径を測定する測定器具です。測定範囲がそれぞれ異なるので、穴径に応じた測定範囲のものを選定することが重要です。
(1)外観及び各部の名称
内径マイクロメータの外観及び各部の名称を図2-8に示します。
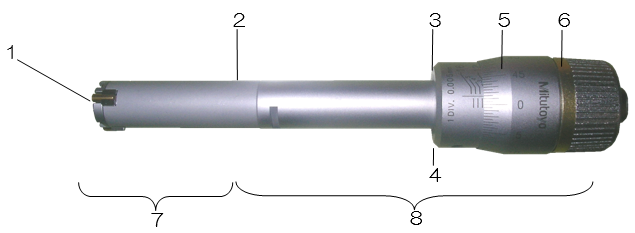
図2-8 内径マイクロメータの外観及び各部の名称
1 | 測定子 |
2 | 接続部 |
3 | 外筒 |
4 | 外筒セットねじ |
5 | シンブル |
6 | ラチェット |
7 | 測定ヘッド部 |
8 | マイクロヘッド部 |
(2)測定方法
測定面をきれいにした後、測定物をアンビルとスピンドルに挟んで、シンブルを右回りに回転させます。ラチェットの音が1~3回「カチッ」と鳴ったら回転をやめ、数値を読み取ります。0.5㎜台、0.01㎜台、0.001㎜台の順に目盛を読み取り、その合計値が測定値です。
例)下図の場合
A:0.5㎜台の目盛 ・・・ 10.0㎜
B:0.01㎜台の目盛 ・・・ 0.17㎜
C:0.001㎜台の目盛 ・・・ 0.003㎜
D:測定値(A+B+C) ・・・ 10.173㎜
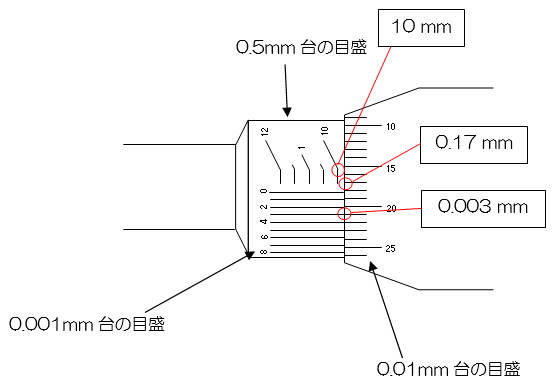
図2-9 内径マイクロメータの読み取り方
(3)使用上の注意
① 必ず測定前にリングゲージにて基点合わせ(精度の確認)をする
読取り値がゼロ点またはゲージの寸法と異なる場合は、本体をリングゲージにセットしたままの状態で外筒を微動回転させて所要の指示値に合わせる。
指示値に合わせた後は、外筒セットねじで外筒を固定する。
② 測定物に入れたままこじったり、吊り下げたりしない
③ 測定値の読み取りは、外筒の基線とシンブルな目盛面の合致点の垂直上より実施する
④ ラチェットを使用し、必ず一定の測定力で測定する
測定面を測定物に軽く接触させ、一旦静止してから、指で5~6回ラチェットを廻す程度とする。
過度の測定力は誤差要因になるため、注意する。
⑤ 測定子全面で測定する場合と、測定子の先端のみで測定する場合とで測定値が異なるため、同じ条件で測定を実施する
⑥ 基点合わせと測定とは同じ姿勢、条件で実施する
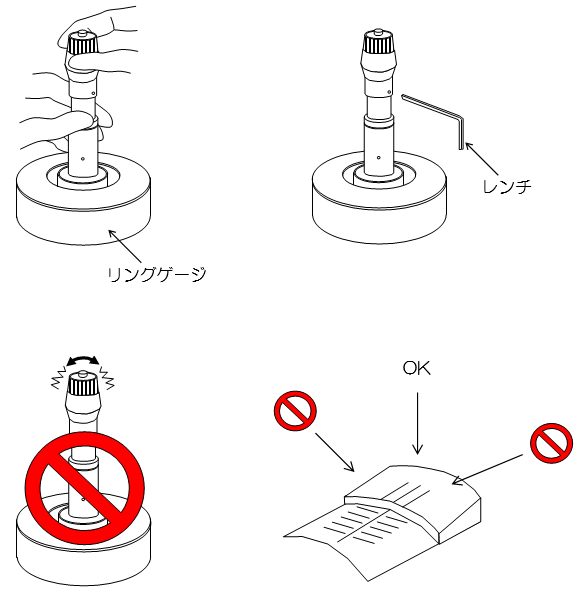
図2-10 内径マイクロメータの使用上の注意
ダイヤルシックネスゲージ
ダイヤルシックネスゲージは厚みを測定する測定器具です。ノギスでは測定できないような奥まったところにある形状や、うねりのある形状の肉厚を測定する場合などに有効です。
(1)外観及び各部の名称
ダイヤルシックネスゲージの外観及び各部の名称を図2-11に示します。
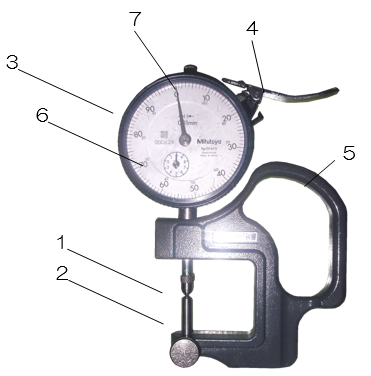
図2-11 ダイヤルシックネスゲージの外観及び各部の名称
1 | 測定子 |
2 | アンビル(固定側) |
3 | ダイヤル表示部 |
4 | ノブ |
5 | 取手部 |
6 | 1㎜単位ダイヤル |
7 | 0.01㎜単位ダイヤル |
(2)測定方法
測定物を挟みこんだ後、力を抜いてダイヤルシックネスゲージを軽く傾け、最も針の読みが小さくなったときの数値を読み取ります。
例)下図の場合
A:1㎜台の目盛 ・・・ 6.0㎜
B:0.01㎜台の目盛 ・・・ 0.93㎜
C:測定値(A+B) ・・・ 6.93㎜
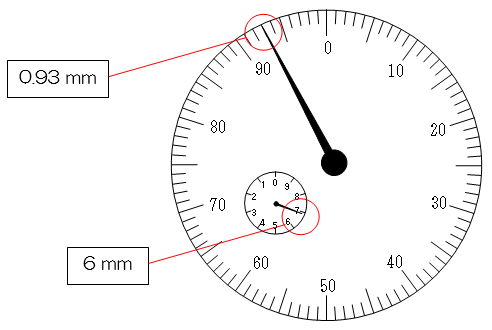
図2-12 ダイヤルシックネスゲージの読み取り方
デプスゲージ
デプスゲージは深さを測定する測定器具です。
(1)外観及び各部の名称
デプスゲージの外観及び各部の名称を図2-13に示します。
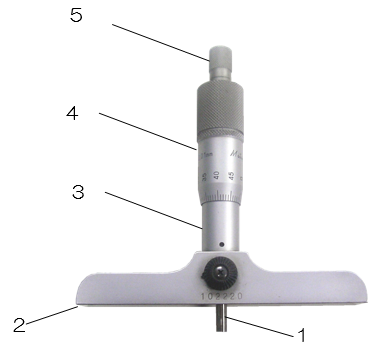
図2-13 デプスゲージの外観及び各部の名称
1 | 測定子 |
2 | 測定面 |
3 | スリーブ |
4 | シンブル |
5 | ラチェットストップ |
(2)測定方法
①測定物の段差をまたぐように測定面を当て、デプスゲージを設置する
②ラチェットストップを回転させ、測定子を測定物の底面に接触させる
③ラチェットの音が1~3回「カチッ」と鳴ったら回転をやめ、数値を読み取る
数値の読み取り方は、外側マイクロメータと同様
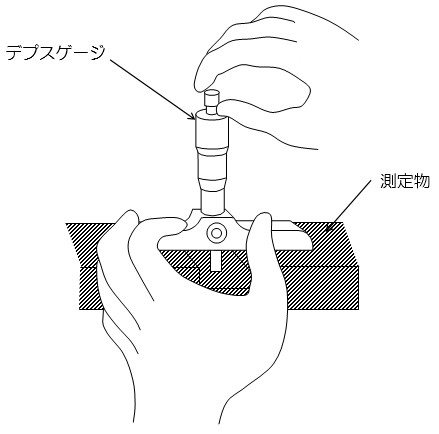
図2-14 デプスゲージの読み取り方
ハイトゲージ
ハイトゲージは製品の高さや段差を測定する測定器具です。製品を定盤に置き、相対的な高さを精度よくスピーディに測定することができます。
(1)外観及び各部の名称
ハイトゲージの外観及び各部の名称を図2-15に示します。
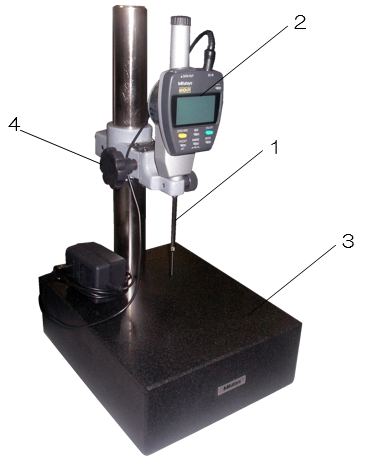
図2-15 ハイトゲージの外観及び各部の名称
1 | 測定子 |
2 | デジタル表示部 |
3 | テーブル |
4 | 高さ調整用ノブ |
(2)測定方法
①測定子がテーブルに当たるように高さを調整する
②電源プラグをAC100Vコンセントに差し込み、インジケータの電源を入れる(ON/OFFボタン)
③測定物をテーブルに設置する
④ZERO/ABSボタンを押し、ゼロ基準をとる
⑤測定子を持ち上げ、測定箇所を測定子の直下に移動する
⑥測定子を測定箇所まで下ろし、表示部の数値を読み取る
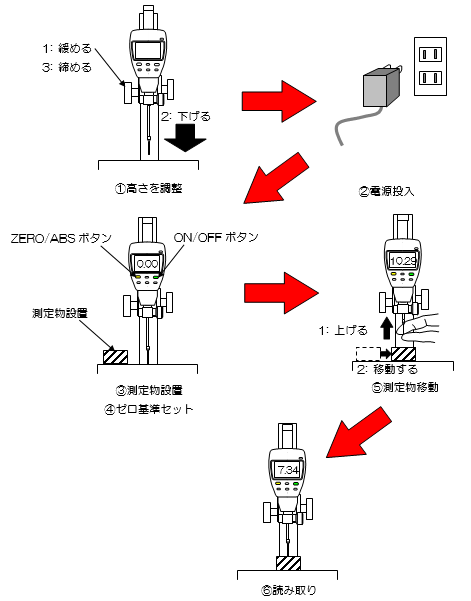
図2-16 ハイトゲージの測定方法
ピンゲージおよび栓ゲージ
ピンゲージおよび栓ゲージは、穴径を測定する測定器具です。精密に製作された円筒状のゲージで、実際に穴形状に入れて、スムーズに入るかどうかで内径の精度を確認します。
(1)外観及び各部の名称
ピンゲージ、栓ゲージの外観を図2-17に示します。
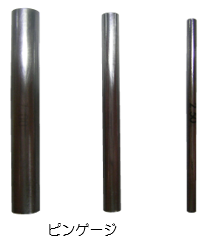
図2-17 ピンゲージと栓ゲージの外観
(2)測定方法
測定する穴部にピンゲージを差し込み、差し込むことができる最大の径が測定値となります。無理に入れようとすると穴やピンゲージを傷つける可能性があるので注意が必要です。
ねじゲージ
ねじゲージはねじ穴が規格に合っていることを確認するための測定器具です。ねじゲージには、測定すべきねじの等級と同じゲージの等級が決められています。通り側と止まり側がついていて、通り側でねじが入り、止まり側では規定以上入らないことを確認します。
(1)外観及び各部の名称
ネジゲージの外観及び各部の名称を図2-18に示します。
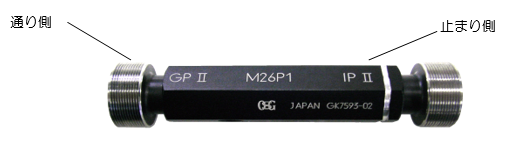
図2-18 ねじゲージの外観
(2)測定方法
ねじ穴にねじゲージをねじ込み、下記を確認します。
①通り側のねじが無理なく通り抜けること
②止まり側のねじが2回転以上ねじ込まれないこと(JIS規格)
止まり側のねじが2回転をこえてねじ込まれないこと(ISO規格)
①②の条件を満たすことができれば、ねじゲージによる等級検査に合格したと判定します。
【JIS等級】
通り側 | 止まり側 | 精度 |
GP(検査・工作 共用) 1級~3級 |
WP(工作用) 1級~3級 |
精密 |
IP(検査用) 1級~3級 |
【ISO等級】
通り側 | 止まり側 | 等級 | 精度 |
GP | NP | 4H | 精密 ↑ ↓ 粗い |
5H | |||
6H | |||
7H |
Rゲージ、Cゲージ
RゲージはR面部、CゲージはC面部が交差内であるか確認するための測定器具です。
(1)外観
RゲージおよびCゲージの外観を図2-19に示します。
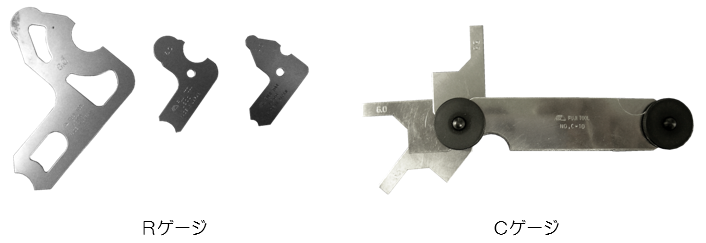
図2-19 RゲージとCゲージの外観及び各部の名称
(2)測定方法
測定する端部にゲージを当てます。端部形状とゲージ形状が最もしっくりとはまりあうゲージサイズが測定値です。場合によっては光源に透かして見て、最も光の漏れが少ないサイズを確認します。
2.3 三次元測定機
品質保証の検査工程において、2.2の汎用的な測定器具だけでは十分に測定ができないケースもあります。複雑な形状の寸法や、幾何公差などを測定する場合などです。このようなときには、三次元測定機が活用されます。
三次元測定機は、マシニングセンタなどのフライス系工作機械と同様に、X軸、Y軸、Z軸に駆動する機構を備えた測定器具です。工作機械と異なるのは、ワークを削るための回転工具の代わりに、測定するためのプローブを備えていることです。このプローブの先端を製品に接触させることで、接触したポイントの三次元座標を認識し、記録します。
様々なポイントの座標情報を測定することで、平面や直径などを割り出し、さらには形状同士の位置関係などを算出することが可能となります。このため、汎用の測定器具では測定できない幾何公差なども測定可能となります。
ただし、三次元測定機自体が非常に高価で、測定にも専門の技能が必要になります。また、測定精度を保つために、一定の空調(おおむね20±1℃など)の効いた空間で使用することが必要で、振動が少なく剛性の高い地面に設置する必要があります。
三次元測定機の構成
図2-20に三次元測定機の外観を示します。
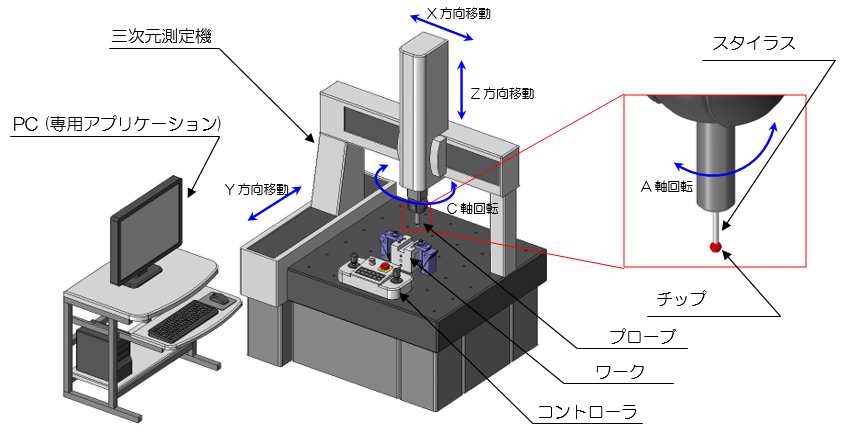
図2-20 三次元測定機の外観
三次元測定機は、X、Y、Zの3軸の移動機構を持った測定器具です。仕様により、A軸、C軸の回転が可能なものもあります。先端のチップをワークに触れると、その中心位置の3次元座標値を読み取ります。チップはルビーなど真円度が高く、硬い材質が使われます。チップの大きさやスタイラスの長さはバリエーションがあり、測定する形状や向きなどによって使い分けます。
基本的にはコントローラによりマニュアル的に操作しますが、専用アプリケーションでNCプログラムを作成し、プログラム通りの自動測定も可能です。
専用アプリケーションでは、3次元座標値を記録するだけでなく、読み取った座標値から、寸法や幾何公差などを計算し表示、記録することが可能です。
三次元測定機で測れる要素
三次元測定機では、チップの触れた座標値から最小二乗法などにより、次のような要素として算出します。
これらの要素情報を専用サプリケーションで記録し、要素同士の幾何的関係などを算出します。例えば、ある円筒と別の円筒の中心軸の線データから「同軸度」を算出したり、点同士の座標値から「位置度」を算出したりすることが可能です。
三次元測定機で測定可能な要素
要素 | イメージ | 必要な 接触点数 |
算出される情報 |
点 | ![]() |
1点 | 点データ (点のX,Y,Z座標値) |
線 | ![]() |
2点以上 | 線データ (線のベクトル方向および線上の任意の点) |
平面 | ![]() |
3点以上 | 平面データ 法線データ |
円 | ![]() |
3点以上 | 直径・半径 真円度 中心点位置 |
楕円 | ![]() |
5点以上 | 楕円データ 長辺・短辺長さ 中心点位置 |
球 | ![]() |
5点以上 | 直径・半径 中心点位置 |
円筒 | ![]() |
6点以上 | 軸の線データ 直径・半径 円筒度 |
円錐 | ![]() |
6点以上 | 軸の線データ 直径・半径 |
三次元測定機の測定手順
三次元測定機による測定には、所定の手順が必要となります。ここでは、実際の操作手順をご紹介します。
手順1:起動及びキャリブレーション
三次元測定機は、起動後に使用するスタイラスのキャリブレーションを行います。チップの直径や、スタイラスの姿勢ごとの補正値を割り出すことになります。
具体的には下図のような、真球度の高い「マスターボール」を使用します。マスターボールの球形状部分を「球」の要素として測定します。これにより、チップの半径を割り出すことができ、測定の際にはこの半径分だけ補正してチップ中心位置の座標系を読み取ることができるようになります。
基本的にはこのスタイラスが真下を向いた姿勢が「基準姿勢」となります。
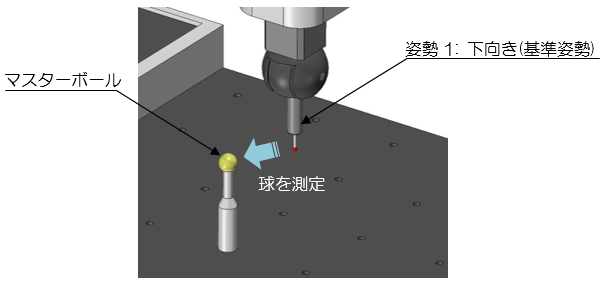
図2-21 キャリブレーション(基準姿勢)
三次元測定機の多くの機種で、スタイラスの姿勢(A軸角度、B軸角度)を変更することができます。スタイラスの姿勢を変えることで、基準姿勢では測定できない横穴などにもアクセスできるようになり、幾何公差の測定が可能となったり、段取り替えの手間が省けたりします。
姿勢を変えた状態で、再度キャリブレーションを行うことで、基準姿勢との相対的な位置関係を割り出すことができ、測定途中で姿勢を変えても基準を変えずに測定を続けることが可能となります。
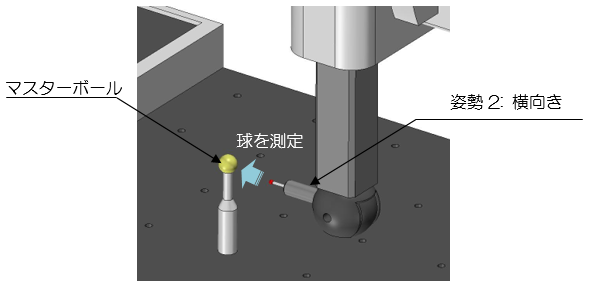
図2-22 キャリブレーション(横向き)
手順2:ワークの固定、座標系の定義
キャリブレーションが済んだら、ワークを三次元測定機のテーブルに固定します。
通常の三次元測定では、切削加工のような強い力がかかりませんので、クランプ工具などで動かないように軽く固定する程度が一般的です。重いワークは固定が不要な場合もあります。
次に、ワークの座標系を定義します。
三次元測定機自体の持っている機械座標系(X軸、Y軸、Z軸)と、ワークの座標系は異なりますので、ワークを基準とした座標系を改めて設定することが必要となります。
通常は図面に定義されているデータムを優先してワーク座標系を設定しますが、特に図面の指定がない場合は、オペレータの判断で任意に座標系を定義します。通常の直交座標系では、座標系の定義として「原点」と「X軸、Y軸、Z軸のうち2軸」が必要となります。
一般的には、基準となる平面、原点、1軸の方向を順に測定していき、座標系を構築していく方法がとられます。(もちろん、オペレータやワーク形状などによってバリエーションがあります)
実際に座標系の測定をしてみましょう。
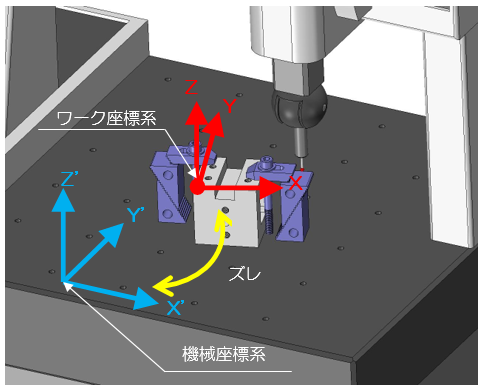
図2-23 ワーク座標系と機械座標系
例えば図2-23のようにワークが固定されていたとします。
当然三次元測定機の機械座標系(青)とワーク座標系(赤)にはズレがあります。切削加工の場合は、加工前の段取り作業において、ワークを微調整して機械座標系に一致させて固定するという手法となります。
参考記事:切削加工を疑似体験してみよう!(前編)
一方で三次元測定機の場合は、測定する座標系をワーク座標系に置き換えるという考え方になります。ここでは、図2-23の通り「ワーク上面の画面から見て左下の角が原点」という設定で座標系の測定を進めていきましょう。
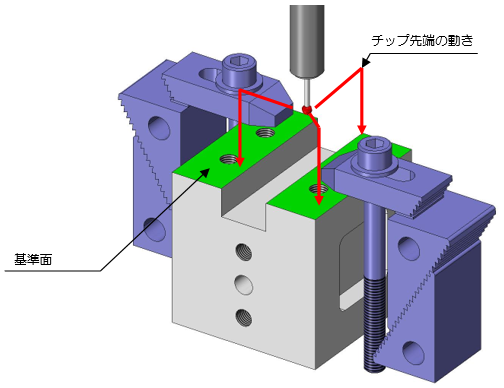
図2-24 座標系の設定 基準面
まず、図2-24の緑色の部分が基準面(Z基準)となりますので、この面にチップを触れさせ「平面」を測定します。測定するポイント数は多いほど測定精度が増しますが、多すぎても測定時間がかかってしまいますので、現実的なポイント数が選ばれます。
平面は3点以上触れることで測定可能ですが、通常は10~20点程度のポイントを取得します。取得した平面を、専用アプリケーション上で「基準面」として定義します。
これで、新しくワーク座標系の基準となる平面のデータを取得し定義することができました。
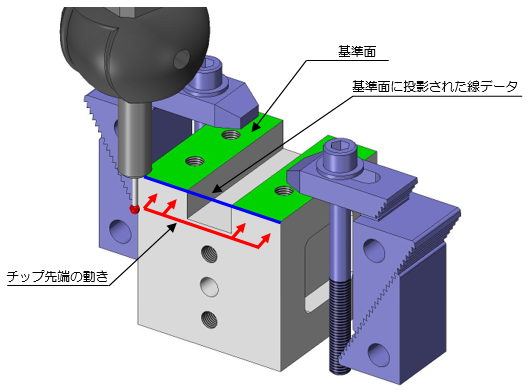
図2-25 座標系の設定 X軸
次に、ワーク座標系のX軸を定義していきます。
このような場合、ワークの側面にチップ先端を当てていきます。線を定義するためには2点以上のポイントが必要ですが、現実的には5~10点ほどとることが多いと思います。
取得したポイントの座標系を専用アプリケーション中で先ほどの「基準面」に投影し、それを線データ(青)とします。得られた線データを「X軸」に定義します。
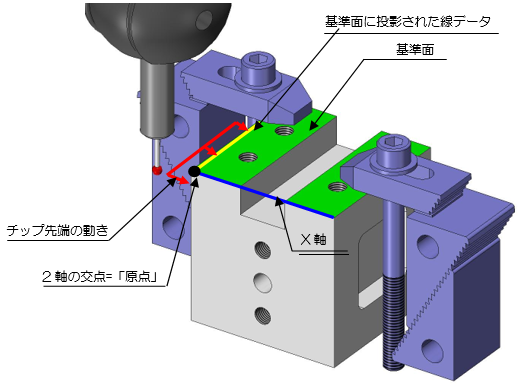
図2-26 座標系の設定 原点
続いて、X軸と同様に画面から見て左奥側の側面にチップ先端を当てていきます。
取得したポイントの座標系を専用アプリケーション上の「基準面」に投影することで基準面上の線データ(黄色)を得ることができます。
そして先ほどのX軸(青)とこの線とが交差するポイントの座標値(黒点)を割り出します。この黒い点がワーク座標系の原点となりますので、「原点」として設定し、座標系の構築が完了します。
以上のように、「基準面」、「基準軸」、「原点」を順に測定しながら設定していくことで、ワーク座標系を構築することが「座標系の定義」となります。
ここまでで、測定前の準備が完了です。
手順3:測定
座標系の設定が完了したら、図面指示に基づいて各形状の測定を行います。
ここでは例題として、図2-27に示されるような「基準面」に対する水色の面の「直角度」と、水色の平面に対するオレンジ色の穴の「直角度」を測定する手順を見てみましょう。
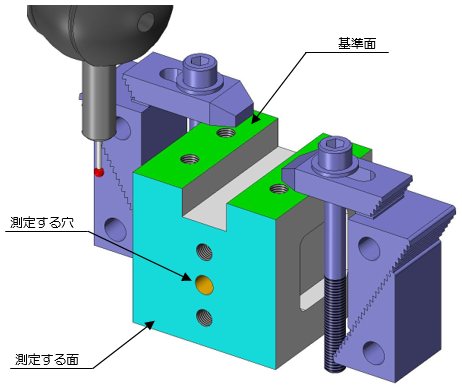
図2-27 直角度の測定要素
スタイラスを傾け(事前にキャリブレーションしておきます)、図2-28のようにチップ先端を側面に触れさせて「平面」を測定します。
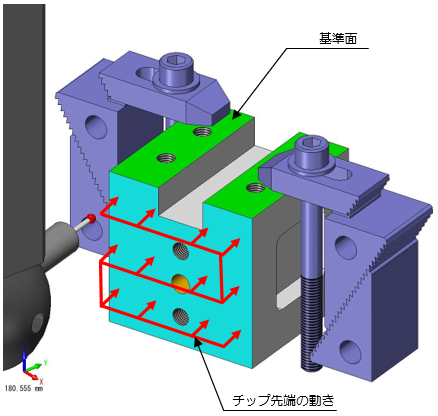
図2-28 平面の測定
これで専用アプリケーション上に記録されている「基準面」と今回取得した「平面」との直角度を算出することができます。アプリケーション上でデータ同士を照合し、「直角度」を演算させます。
続いて穴の測定に移ります。
直角度を算出するためには、穴を「円筒」として測定し、中心軸の線データが必要となります。スタイラスを穴に入れ、ある深さで穴の内径に数点触れて各ポイントの座標値を取得した後、さらに置く前入れて内径のポイントの座標系を取得します。繊細な操作が必要な測定作業です。
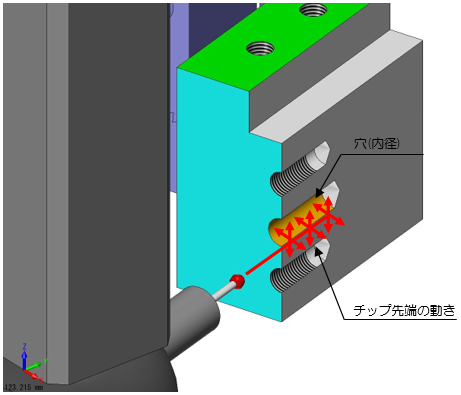
図2-29 穴の測定(断面)
円筒形状もできるだけ多くのポイントを取得することで、測定精度が向上します。特に軸方向の情報が必要な場合は、奥行方向に3か所ほどは測定ポイントを設けた方が良いです。
取得した「円筒」のデータに中心軸の線データが含まれますので、先ほどの「平面」と「円筒」との直角度を算出することが可能となります。専用アプリケーション上で、直角度を演算させます。
また、円筒と平面の交線は、平面上の「円」となります。この円を算出すると、円の中心点の情報も得ることができ、例えば基準点からの「位置度」の算出に利用することができるようになります。
このように、三次元測定機による測定では、測定データを蓄積しながら、要素ごとの三次元的な幾何公差や寸法値を割り出していくことが可能で、検査工程においては非常に強力なツールです。
2.4 検査項目と検査器具のまとめ
検査工程は、図面に指示された要求事項を、合理的な方法で測定し要求値に合致しているのを確認する作業となります。
上述した三次元測定機は万能な測定器具ではありますが、特定の寸法を測定する際にはマイクロメータなどの汎用的な測定器具の方が、測定精度が高い場合が多いです。測定項目によって測定器具の使い分けをすることが重要です。
以下に検査項目ごとによく用いられる測定器具をまとめますので、参考にしてみてください。
検査工具と検査器具まとめ
◎:主として使用する器材
○:補助的に使用する器材
参考文献:株式会社ミツトヨ 取扱説明書等
3.まとめ
今回は、機械部品の品質保証について解説しました。自分の設計した機械部品が、実際にどのように製作され、その品質を保証されるのかを事前に知っておけば、何か不具合が出たときの対処や確認の方法もイメージしやすくなると思います。
今回ご紹介した以外にも、要求によっては溶接部の漏れを「リークディテクタ」などで検査したり、表面硬さを「硬さ試験機」で測定したりすることなども検査工程度行われます。あまり一般的でない測定項目は、製造現場で対応していないケースもありますので、事前にどのような項目であれば対応可能であるか確認しておくと良いでしょう。
また、測定作業も製造工程の1つですので、当然製作コストに含まれます。同じ部品を1ロット100個作ったとして、全数、全項目検査するのと、抜き取りで3個公差部だけ検査するのとでは、検査工数も大きく違ってきますね。三次元測定機の活用によって、比較的幾何公差を測定しやすくなってきましたが、三次元測定機を設備している加工現場はまだ多くはありません。
さらに、幾何公差を必要以上に入れてしまうと、測定だけで大きな工数が発生してしまうことになりかねませんのでご注意ください。
品質保証の程度についても、設計者としての意見を持っておくことは大変重要と思います。部品の製造工程だけでなく、品質保証や検査工程についても理解したうえで、より合理的な設計に役立てていただければ幸いです。