寸法は記入もするし省略もする。
そんなことも忘れてしまったのか設計者ども
皆さんは寸法を記入する際に、何を一番重要視するでしょうか?
上司も含めて多くの設計者は寸法漏れを気にしているはずです。しかし、寸法を記入する際に記号や配列など注意すべきポイントが多々あります。また、あえて寸法を記入しないというテクニックも存在するのです。
図面の本質を考えるうえで、今回は寸法補助記号や寸法記入法の種類について復習しましょう。
meviy 2D|PDF図面アップロードで簡単操作
かんたん見積もりはこちらから >
目次
1)寸法の目的を再確認
寸法を記入する際に、最初に考えなければいけないものが基準です!
基準には次の3つがあります。
●取り付け基準(位置決め基準も含む)
●加工基準(端面など加工する際に最初に機械加工しておきたい面や穴など)
●機能基準(軸や軸受け挿入穴、スライド面など)
ある製品に組み付けるカバーの事例で基準の考え方を確認してみましょう。
上段左側にカバーの3次元モデル、上段右側に2次元の組図(断面図)を示しており、形状と組みつけ状態からある程度、設計機能が読み取れると思います。下段には部品図の基準となる部位を赤線で示しています(図4-1)。
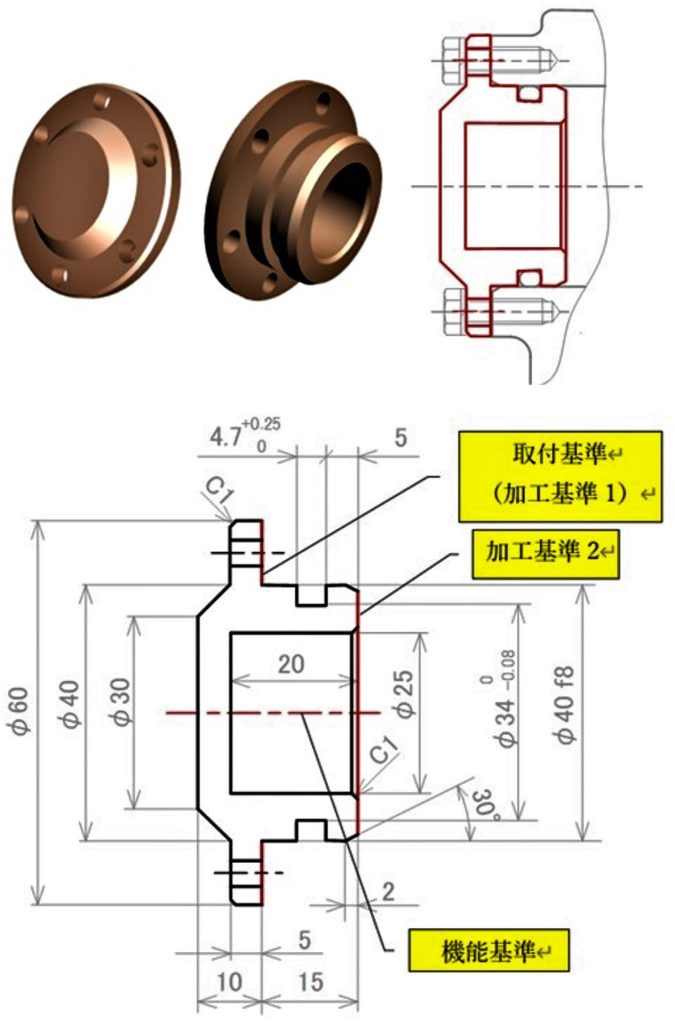
図4-1 カバーの形状と取り付け状態、3つの基準
|
これらの基準を明確にしてから寸法を記入し始めると、設計意図を伝えやすく、かつ関連する寸法群を整列して記入することができます。
しかし、世の中で流通している図面には”基準”を意識せずに寸法記入した図面も少なくありません。基準を意識せずに寸法を記入すると次のような悪さが生じて組立できない、あるいは機能が出ないという不具合につながります。
●重要寸法なのに直接寸法線で関連付けしていないため、ばらつきが大きくなる。
●加工を意識した寸法記入ができないため、加工ミスや寸法漏れの原因になる。
2)寸法に関係する用語の定義
普段、なんとなく使っている用語も間違って認識している可能性もあります。
間違った認識で用語を使わないようにJIS Z 8114 : 1999にある寸法に関係する用語の定義を改めて確認してみましょう。(表4-1)。
*ただし、寸法の公差に関するものは次回解説するため省いています。
表4-1 寸法に関係する用語の定義
用語 | 定義 |
寸法線 | 対象物の寸法を記入するために、その長さ又は角度を測定する方向に並行に引く線 |
寸法補助線 | 寸法線を記入するために図形から引き出す線 |
引出線 | 記述・記号などを示すために引き出す線 |
直列寸法記入法 | 個々の部分の寸法を、それぞれ次から次に記入する方法 |
並列寸法記入法 | 基準となる部分からの個々の部分の寸法を、寸法線を並べて記入する方法 |
累進寸法記入法 | 基準となる部分からの個々の部分の寸法を、共通の寸法線を用いて記入する方法 |
座標寸法記入法 | 個々の点の位置を表す寸法を、座標によって記入する方法 |
寸法補助記号 | 寸法数値に付加して、その寸法の意味を明確にするために用いる記号 |
基準 | 対象物の形・組立部品の位置などを決めるもとになる点、線又は面 |
起点記号 | 累進寸法記入法及び座標寸法記入法における寸法0の点を表す記号 |
寸法 | 決められた方向での、対象部分の長さ、距離、位置、角度、大きさを表す量<参考> 寸法には、長さ寸法、大きさ寸法、位置寸法、角度寸法などがある |
サイズ | 決められた単位・方法で表した大きさ寸法 |
長さ寸法 | 長さを表す寸法(単位はmmが標準であり、図に単位は記入しない) |
角度寸法 | 角度を表す寸法(単位は°(度)が標準であり、図に単位を記入する) |
位置寸法 | 形体の位置を表す寸法(端面と穴、穴と穴の距離など) |
機能寸法 | 機能上必須の形体の部分、すきまなどの寸法(重要な寸法) |
呼び寸法 | 対象物の大きさ、機能を代表する寸法(軸受けの内径など) |
仕上がり寸法 | 製作図で意図した加工を終わった状態の対象物がもつべき寸法 |
基準寸法 | 寸法の許容限界の基本となる寸法(ノミナルと呼ぶ企業もある) |
実寸法 | 仕上がった対象物の実際の寸法 |
参考寸法 | 図面の要求事項でなく、参考のために示す寸法(カッコを付けた寸法で表す) |
テーパ | 投影図又は断面図における相交わる2直線間の相対的な広がりの度合い (角度あるいは比率で表す) |
こう配 | 投影図又は断面図における直線の、ある基準線に対する傾きの度合い (角度あるいは比率で表す) |
※( )内は、筆者による補足
3)まず基本!寸法の表し方
ここでは、寸法線に関する用語や最新の寸法補助記号の情報に加えて、寸法の配列の種類を復習します。
①寸法記入原則
寸法は、次項のようなJISが定める「寸法記入の一般原則」に従います。
|
寸法は主に、次の要素から成り立ちます。
●横方向
●縦方向
●任意方向
●直径
●半径
●球
対象物に寸法を記入する場合は、寸法補助線を用いて寸法線と対象物を結び、寸法線の上に寸法数値を記入します(図4-2)。
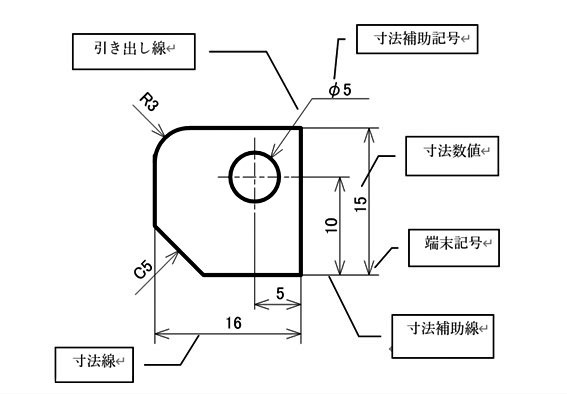
図4-2 寸法記入要素の名称
②寸法補助記号
2022年時点のJISで規定されている寸法補助記号の種類を確認しましょう。2010年や2019年に追加された新しい記号は設計や製造の現場での認知度が低く、採用している企業とそうでない企業の差があります(表4-2)。
表4-2 寸法補助記号
項目 | 記号 | 呼び方 |
直径 | φ | まる・ファイ |
半径 | R | あーる |
コントロール半径 | CR | しーあーる |
球の直径 | Sφ | えすまる |
球の半径 | SR | えすあーる |
正方形の辺 | □ | かく |
円弧の長さ | ⌒ | えんこ |
板の厚さ | t | てぃー |
45°面取り | C | しー |
穴深さ | ![]() |
あなふかさ |
ざぐり・深ざぐり | ![]() |
ざぐり |
皿ざぐり | ![]() |
さらざぐり |
円すい | ![]() |
えんすい |
読者の皆さんの中でも、新しく追加された記号を初めて知ったという人も多いのではないでしょうか?
新しい記号の採用云々の差は、その企業で製図標準が誰も見ることのない形骸化した標準ではなく、実際に“生きた運用”されているかどうかで決まり、製図標準がない企業では個人個人の設計者の知識で図面を描くため、図面として統一感が無くなっている場合が散見されます。
③寸法の配列
実際の製図では、複合する形状の関連を見極めながら多数の寸法線を記入しなければいけません。寸法の配列方法によって、寸法の公差ばらつきや累積度合い、見やすさなども考慮して選択していくことになります。
複合する形状に寸法記入する際の記入法には、次の4種類があります。
a)直列寸法記入法
個々の寸法を直線上に連ねて記入する方法。切削加工品やプレス加工品にかかわらず、すべての部品に適用することができます(図4-3)。
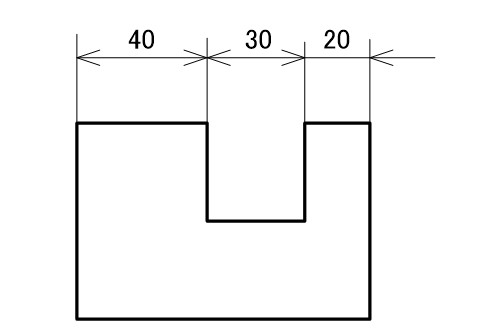
図4-3 直列寸法記入法
b)並列寸法記入法
個々の寸法を個別に並べて記入する方法。切削加工品やプレス加工品にかかわらず、すべての部品に適用することができます(図4-4)。
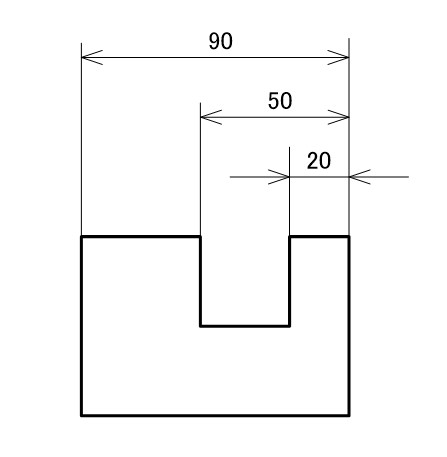
図4-4 並列寸法記入法
c)累進寸法記入法
基準となる部分(起点記号〇で示す)からの寸法数値を共通の寸法線上に記入する方法。並列寸法記入法を省スペースに改善したもので、並列寸法記入法と意味は同じです。切削加工品やプレス加工品にかかわらず、すべての部品に適用することができます(図4-5)。
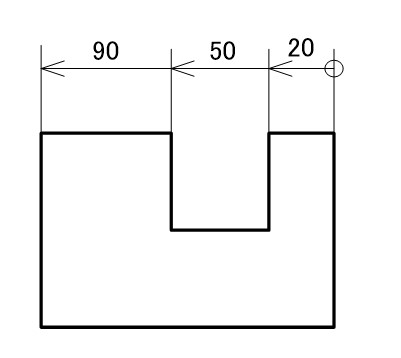
図4-5 累進寸法記入法
d)座標寸法記入法
個々の点の位置を表す寸法を、座標によって同一図面中に記入する方法。多数の穴やねじなどの寸法補助線が重なり見難くなる場合、X-Yの座標原点を決め、同じ図面の中に表を用いて座標位置と穴径の寸法をセットにして記入したものです。大きな板金部品に多数の穴が開いた部品に用いられることが多いでしょう(図4-6)。
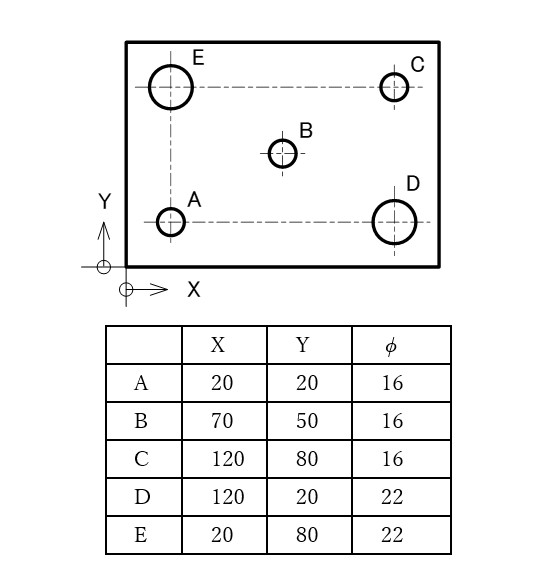
図4-6 累進寸法記入法
4)「暗黙の了解」の下で省略される寸法
寸法は漏れなく記入するものと考えている人も多いですが、製図の世界では図が煩雑になることを防ぐ目的で暗黙的に寸法を省略することがあります。
最も代表的な寸法の省略を紹介しましょう。
皆さんも無意識にやっていると思いますが、直方体の対向する面の平行(0°)や隣り合う面の直角(90°)を角度寸法として記入しないのは、暗黙的に省略することが決まっているからです。
それ以外にも寸法を省略する事例を見てみましょう。
次の2つの図において、端面からの穴位置が上下左右共に記入されていないため、位置がわかりません。これは、左右対称あるいは上下対称の部品に使われる記入法で、一般的な呼び方として「センター振り分け(あるいは中心振り分け)」という寸法指示になります(図4-7)。
ただし、JISにはセンター振り分けという用語の説明はなく、センター振り分けを使用している図例が散見されることと、国家試験である「技能検定(機械・プラント製図)」の模範解答でもセンター振り分け寸法が記載されているため、設計意図を伝えるのに有効なテクニックのため使うことをお勧めします。
まず投影図を見る限り、穴の位置は左右対称、あるいは上下対象となる中央にレイアウトされているように見えます。対称がどうかの判断は中央に縦向きと横向きで記入されている“対称中心線(図中で赤色で示す)”から判別することができます。
このように穴の位置の寸法が省略されている場合、暗黙の了解の下、左右等分あるいは上下等分という解釈をします。
例えば左側の図で穴の位置は次のように考えます。
・穴は、左右方向で中央となる端面から寸法30mmの位置にある
・穴は、上下方向の中央にある端面から寸法15mmの位置にある
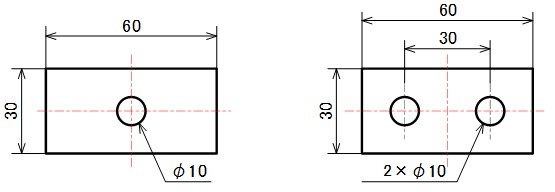
図4-7 センター振り分け寸法
なぜセンター振り分けにするのかというと、設計意図と加工プロセスとの矛盾を無くすためです(図4-8)
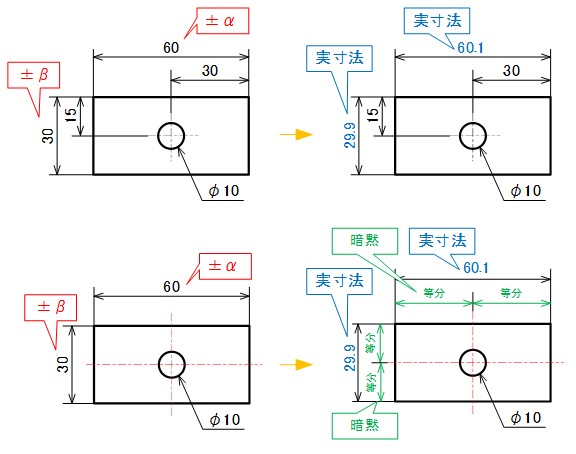
図4-8 端面からの寸法記入とセンター振り分け寸法の考え方の違い
まずは上段の図を見てください。
穴位置が横幅の中央値「30」と縦幅の中央値「15」で示されており、特に矛盾は感じません。
しかし、加工のことを考えると、一般的に穴加工前に外形形状を仕上げることが一般的です。その時、外形は寸法数値ジャストで加工されるわけではなく、「±α」や「±β」のばらつきをもって加工されます。実寸法である外形サイズがばらついている状態で、図面指示通り穴位置を端面から「30」や「15」で狙って加工する時点で穴位置は中心狙いではなくなってしまい、設計意図からずれた解釈となってしまうのです。
下段に示すセンター振り分け寸法の場合、端面からの寸法指示がないため、ばらついた実寸法に合わせて中央位置を狙って加工するというプロセスを促すことができるのです。
図4-8に示したセンター振り分け寸法に対して、初めて聞いたし、上司によっては「寸法漏れだ!」と怒る人もいるから、この寸法表記はおかしいと考える人もいるでしょう。しかし、部品形状を円筒軸に置き換えると、日常的にセンター振り分け寸法を使っているのがわかります(図4-9)。

図4-9 円筒形状とセンター振り分け寸法
図例は円筒軸に穴が開いた形状ですが、段付き軸や溝付軸でも同じです。
左側の図を見てください。中央に穴が開いていますが穴位置を示す位置の寸法が記入されていません。これは投影図から暗黙的に中心に穴をあけるものと解釈するからです。
したがって、外径が加工ばらつきによって変動しても、加工者はそれに合わせて中心を狙って加工します。
同様に、ピッチ円(図中で赤色で示す)上に配置する穴の位置を示す角度が指示されず見た目で等分であれば、暗黙的に均等配置、つまり等配(とうはい)という解釈をし、この考え方はISOの原文*にも明記されていることを確認しています(図4-10)。
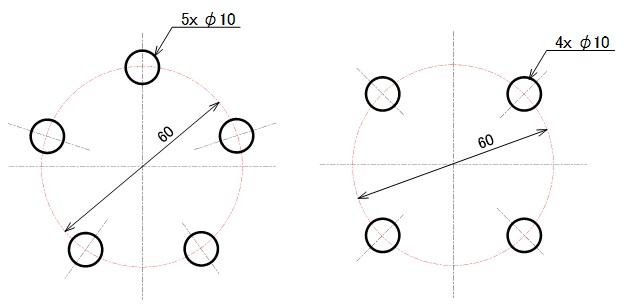
図4-10 ピッチ円上の均等配置
したがって、次のように考えます。
・左側の図のそれぞれの穴位置の相対角度は360°/5=72°で、一番上の穴が直交座標の縦軸上にある
・右側の図のそれぞれの穴位置の相対角度は360°/4=90°で、直交座標に対してセンター振り分け角度寸法として斜め方向は45°にある
5)まとめ
今回は、2022年時点でJISに規定されている寸法補助記号や寸法配列の種類を解説しました。また、寸法には暗黙的な考えの下、設計意図を忠実に実現するために記入を省く手法もあることにも触れました。
寸法補助記号の正しい使い方について、今回は詳しく解説しませんでしたが、JISの定めるルールと設計現場で記入しているルールに若干の乖離が見られます。筆者自身は、JISのルール通りになっていなくても第三者が誤解しなければよいと考えています。これらについては2クール目以降の実用図面を使った事例で詳しく解説したいと思います。
次回は、普通許容差に比べて高い精度を要求する場合のサイズ公差の記入法の注意点や世界共通記号として使用される公差クラス記号の意味について解説します。
meviy 2D|PDF図面アップロードで簡単操作
かんたん見積もりはこちらから >