設備部品の設計を行う場合、その部品の機能を決める際には「硬さ」や「耐衝撃性」なども重要な要素となります。他の部品との摺動面や、衝撃を受け止める箇所があるなど、一定以上の硬さや耐衝撃性などが必要とされる部品もあります。
これらの性質を求めようとした場合、材料そのものの特性だけでは不十分なケースがあります。このような場合に、熱処理によって硬さや耐衝撃性を向上させて対応することも一つの解決策となりますね。所望の性質を得られるよう、適切な材質や熱処理を選定していく必要がありますが、熱処理の種類や特徴も多岐にわたり、大変わかりにくいのも事実と思います。
熱処理は材質や目的によってさまざまな種類が存在しますし、特別な目的以外であまり用いられることがないため馴染みのない設計者さんも多いと思います。
今回は設備部品でよく用いられる熱処理の基本や使い分けのポイントをわかりやすくまとめましたので、ぜひ参考にしてみてください。熱処理をうまく使いこなすことで、きっと設計の幅も広がると思います。
この記事では「焼入れ」「焼き戻し」「焼きならし」「焼きなまし」や、「高周波焼入れ」「浸炭処理」「窒化処理」など、設備部品でよく用いられる熱処理の種類や特徴について解説していきます。
目次
1.よく用いられる熱処理
熱処理とは部品を加熱し、冷却することで、部品全体や表面の組織に変化を生じさせる処理です。特に炭素の含まれる鋼鉄は、熱処理によって硬さ・耐食性・耐摩耗性・耐衝撃性などが変化します。
熱処理の方法は、部品全体を処理する「全体熱処理」と、主に表面のみを処理する「表面熱処理」に分けられます。全体熱処理は「焼入れ/焼もどし」、「焼なまし」、「焼ならし」などに分けられ、表面熱処理は「高周波焼入れ」、「浸炭処理」、「窒化処理」などがあります。
熱処理は加熱の温度と、冷却の温度や速度でその効果が異なります。基本的には、焼入れのように加熱後に急激に冷やすと、硬く脆くなります。一方で、ゆっくり冷やすことで、組織を整えるのが、焼きもどしや焼なまし、焼ならしの目的となります。
冷やし方は、水冷、油冷、空冷、炉冷などがあり、その熱処理の目的に応じて使い分けられます。
部品の目的とする機能や性能に対して、どのような材質と熱処理を組み合わせるのが適切か、以降の内容を参考にしてみてください。
全体熱処理の基本

図1-1 全体熱処理のイメージ
炭素の含まれた鋼鉄は、その炭素の含有量によってオーステナイト(γ鉄)化する温度が異なります。炭素含有量(質量%)で、0.8%を境にその傾向が異なります。ちょうど0.8%の含有量となる鋼鉄を共析鋼と言います。0.8%未満の鋼鉄は亜共析鋼、0.8%よりも多い鋼鉄は過共析鋼と呼ばれます。
図1-2は炭素-鉄合金の平衡状態図と呼ばれます。
横軸が炭素の含有量、縦軸が金属の温度です。
炭素の含有量に応じて、温度ごとの金属内部がどのような組織になっているかを表したものになります。
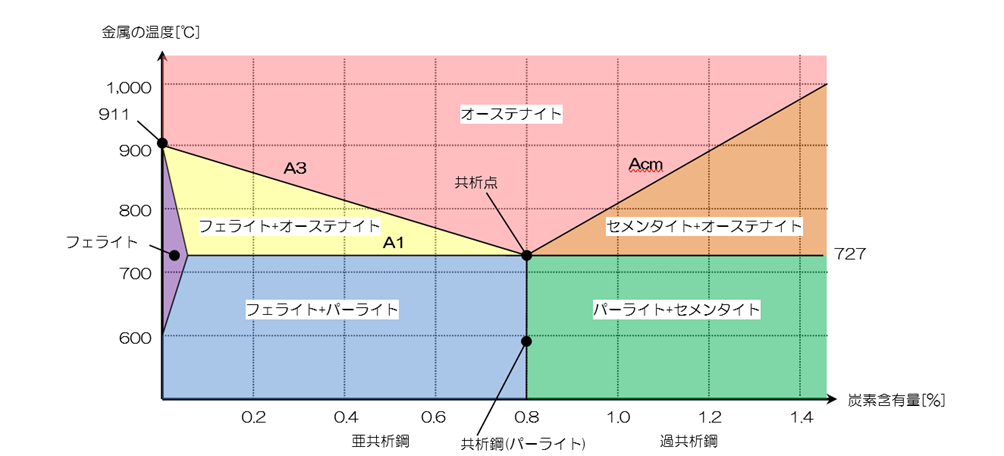
図1-2 炭素-鉄合金 平衡状態図(簡略モデル)
A1は727℃で、組織のオーステナイト化が始まる温度(変態温度)です。
完全にオーステナイト組織に変化する温度が亜共析鋼の場合はA3、過共析鋼の場合はAcmのラインとなります。亜共析鋼ではA1とA3の間はフェライトとオーステナイトが混在し、過共析鋼ではAcmとA1の間はセメンタイトとオーステナイトが混在している状態ということになります。
フェライト(α鉄)は炭素をほとんど含有しない組織です。セメンタイトは鉄炭化物(FeC3)の組成を持つ非常に硬い組織です。
パーライトは、フェライトとセメンタイトが層状に重なり合った組織です。
焼入れをする際には、亜共析鋼はA3以上の温度、過共析鋼はA1以上の温度として安定化させます。その後急冷し、前述のマルテンサイト組織を得ることになります。概ね各ラインの30~50℃程度上の温度とするのが一般的なようです。
マルテンサイトは図1-2には出てこず、オーステナイトを急冷することによって得ることのできる組織です。
焼入れ/焼もどしに適した材質は炭素を含んだS45Cなどの炭素鋼や、SKD、SKHなどの特殊鋼です。ステンレスでは、SUS420J2も焼入れ/焼もどしにより硬さを向上させることができます。また、析出硬化系ステンレス(SUS630が代表的)は炭素含有量が低く焼入れ/焼もどしにより硬さを高めることは困難ですが、析出硬化処理により強度を高めることが可能です。
固溶化熱処理は、ステンレスを加熱し急冷する処理で、加工応力の除去やCr炭化物の固溶を目的に行われます。
析出硬化処理とは、固溶化熱処理の後に析出硬化熱処理(時効硬化熱処理)を行い、金属間化合物の微細な析出物粒子を分散させて強度を高める処理です。
「オーステンパ(JIS記号ではHQA)」、「マルテンパ(同HQM)」、「マルクエンチ(同HQM)」、「サブゼロ処理(同HSZ)」など通常の焼入れ/焼もどし以外の特殊な熱処理も存在します。通常の焼入れ/焼もどしよりも、靭性や耐衝撃性に優れた性質が得られる、変形が少なくて済むなど特殊な効果が得られます。通常の熱処理以外の方法を模索したい場合などには、これらの手法を検討しても良いと思います。
参考までによく利用される熱処理による物性値を表1-1にまとめます。
表1-1 鋼鉄の熱処理に関する物性値
材質 | 炭素含有量 [%] |
熱処理状態 | 条件 | 引張強さ [MPa] |
伸び [%] |
衝撃値 [J/cm2] |
硬さ | ||
機械構造用炭素鋼 | S45C | 0.42-0.48 | 焼ならし | 820-870空冷 | ≧570 | ≧20 | – | 167-229 HBW |
|
焼なまし | 約810炉冷 | – | – | – | 137-170 HBW |
||||
焼入れ/焼もどし | 820-870水冷/550-650急冷 | ≧690 | ≧17 | ≧78 | 201-269 HBW |
||||
S50C | 0.47-0.53 | 焼ならし | 810-860空冷 | ≧610 | ≧18 | – | 179-235 HBW |
||
焼なまし | 約800炉冷 | – | – | – | 143-187 HBW |
||||
焼入れ/焼もどし | 810-860水冷/550-650急冷 | ≧740 | ≧15 | ≧69 | 212-277 HBW |
||||
クロムモリブデン鋼 | SCM435 | 0.33-0.38 | 焼入れ/焼もどし | 830-880油冷/530-630急冷 | ≧930 | ≧15 | ≧78 | 269-331 HBW |
|
炭素工具鋼 | SK3 | 1.00-1.10 | 焼なまし | 750-780徐冷 | – | – | – | ≦212 HBW |
|
焼入れ/焼もどし | 780水冷/180空冷 | – | – | – | ≧61 HRC |
||||
合金工具鋼 | SKD11 | 1.40-1.60 | 焼なまし | 830-88徐冷 | – | – | – | ≦255 HBW |
|
焼入れ/焼もどし | 1030空冷/180空冷 | – | – | – | ≧58 HRC |
||||
ステンレス | SUS304 | ≦0.08 | 固溶化熱処理 | 1010-1150急冷 | ≧520 | ≧40 | – | ≦187 HBW |
|
SUS420J2 | 0.26-0.40 | 焼なまし | 約75急冷 または800-900徐冷 | ≧540 | ≧18 | – | ≦235 HBW |
||
焼入れ/焼もどし | 980-1040急冷/150-400空冷 | ≧540 | – | – | ≧40 HRC |
||||
SUS630 | ≦0.07 | 固溶化熱処理 | 1020-1060急冷 | – | – | – | ≦38 HRC |
||
析出硬化処理 | H900 | 470-490空冷 | ≧1310 | – | – | ≧40 HRC |
|||
H1150 | 610-630空冷 | ≧930 | – | – | ≧28 HRC |
ニツコー熔材工業株式会社 総合ガイドカタログより抜粋
2.焼入れ/焼もどし
2-1 焼入れ/焼もどしとは
炭素の含まれる鋼鉄は、ある温度(800℃くらい)以上まで加熱すると「オーステナイト」という組織になります。全体をオーステナイト化して安定させた後、急冷して「マルテンサイト」という硬い組織に変化させるのが「焼入れ」です。焼入れ(Quenching)はJISの記号でHQと表記されます。
焼入れを行うと硬くなりますが、その反面脆くなってしまい、そのまま部品として使用するには不向きです。そこで再度焼入れ時よりも低い温度に加熱し、ゆっくりと冷却することで粘り(靭性)を高める処理が「焼もどし」です。焼もどし(Tempering)はJIS記号でHTです。
焼もどしによる再加熱の温度は高いほど硬さが減少し、粘りが増します。高温で再加熱して、硬さよりも粘りを増す手法を「高温焼もどし」と言います。一方低温で再加熱して、粘りよりも硬さを優先する手法が「低温焼もどし」です。
通常は、焼入れと焼もどしがセットで行われます(HQ/HT)。
2-2 焼入れ/焼もどしの特徴
焼入れというと「加熱すること」と、とらえられがちですが、加熱した後に「急冷すること」でマルテンサイト組織に変化させることというのが本来の意味になります。
また、焼入れ後に高温焼もどしを行い、硬さや強度、靭性などを調整する熱処理を「調質」と呼びます。特にS50Cなどの炭素鋼やSCM440などは、機械加工ができる程度にあらかじめ調質された「調質材」が多く利用されています。各種材料メーカーより「プリハードン鋼」(NAK55, DH2F, STAVAXなど)としても販売されています。調質材の硬さはHRC30~40程度と、切削加工が可能な範囲に調整されて用いられることが多いようです。
2-3 焼入れ/焼もどしの方法
焼入れは、加熱と冷却によって行われます。
加熱は、部品を熱処理用の加熱炉に入れ加熱し、組織がオーステナイトに変わる温度にまで高めます。通常、亜共析鋼ではA3の温度、過共析鋼ではA1(727℃)よりも30~50℃程度高い温度にします。
この焼入れ温度が高すぎても低すぎても十分な焼入れとはなりませんので、温度の調節が非常に重要になります。過共析鋼の場合は、Acmの温度以上にすれば完全にオーステナイト化しますが、この温度まで上げてしまうとうまく焼入れできないため、A1温度プラス30~50℃程度となります。この温度はセメンタイトも含まれる組織になりますが、焼入れ温度を保持することでセメンタイトをオーステナイト組織に固溶させることで、十分な焼入れ性を獲得します。
「固溶」は、ある金属の結晶構造の中に他の金属の組織が入り込んでも、元の組織の状態を保って混ざり合った状態のことです。十分にオーステナイト化あるいは固溶化するまで焼入れ温度を保持した後に、冷却を行います。冷却には、水冷、油冷、空冷、水溶液、塩浴冷却などの種類があります。
水冷は水を用いた冷却方法で、冷却速度が高く、コストが安い冷却方法です。ただし、水冷だけだと冷却しすぎてしまい、変形が発生して不具合がでる可能性が高くなります。
油冷は油を用いた冷却方法で、水冷よりもゆっくりと均一な冷却ができます。
苛性ソーダなどを水に溶かした水溶液による冷却は、水の冷却性能をさらに高め、濃度に応じて冷却速度を変えることができるという利点があります。
塩浴(ソルトバス)は、塩類を数百度程度に加熱して液体化したものです。均一な冷却ができ、焼割れなどが起きにくい特徴がありますが、コスト面で割高となります。
空冷は大気中で冷却する方法で、冷却速度が非常に遅い方法です。通常は焼きなましに利用される冷却方法です。
熱処理の種類や材質に応じて、これらの冷却方法から最も適した方法が選ばれ、あるいは組み合わされて使用されることになります。ゆっくりと冷却すると、組織が元に戻っていくだけですが、急速に冷却するとパーライトやフェライトに変化する時間が足りず、「マルテンサイト」に変化するマルテンサイト変態が起こります。この急冷によりマルテンサイトへと変化させることが「焼入れ」です。
焼入れはこの冷却スピードが非常に重要となります。スピードが足りないと、マルテンサイト以外の相が混入してしまい、十分な焼入れ特性が得られないためです。ただし、マルテンサイトへの変態が始まる温度を過ぎても急速な冷却を行ってしまうと、「焼き割れ」や「変形」が大きくなりすぎてしまう可能性が高まります。この変態温度を過ぎたら空冷などにより、冷却速度を緩める二段冷却が用いられることが多いようです。
マルテンサイトそのものは硬く、靭性が低下して脆い組織なので、焼入れをしただけでは実用に供することができません。そこで、再度加熱冷却を行い、靭性を取り戻すのが焼もどしです。
焼もどしは、A1温度よりも低い温度に加熱し、ゆっくりと冷却を行います。焼入れ時よりも硬さは減ります。
3.焼なまし(焼鈍)
加熱した後に徐々に冷却すると、組織が均一化され軟らかくなり、内部応力が除去されて切削性が向上します。このような熱処理を「焼なまし」(または、焼鈍:しょうどん)と言います。焼なまし(Annealing)は、JIS記号でHAです。アニール処理とも呼ばれます。
完全焼なまし(JIS記号でHAF)、軟化焼なまし(同HASF)、応力除去焼なまし(同HAR)、拡散焼なまし(同HAH)、球状化焼なまし(同HAS)などがあります。目的に応じて加熱時の温度も異なります。炭素鋼などだけではなく、ステンレスやアルミ合金などにも用いられます。
焼なましは「やわらかくする」というイメージです。
また、焼なまし(アニール処理)は、熱を加えることによって部品の残留応力を除去し加工性を向上させます。薄物の切削加工品などは、適切なタイミングで焼きなまし処理をすると、完成時の精度が向上することがあります。
加工前の材料の状態で熱処理する場合と、余肉をつけた荒加工状態で熱処理する場合が考えられます。特にSUS304などは加工応力による変形も大きいため、焼なましを活用することで平面度などの精度向上が見込めます。
加工現場と積極的に情報交換して、焼なましの是非やタイミングについて議論してみてください。
4.焼ならし(焼準)
鋼鉄は、鋳造や鍛造、圧延など力を受けた状態で製造されます。熱処理によって、組織を均一化・微細化して機械的性質を確保する手法が「焼きならし」(または、焼準:しょうじゅん)です。焼ならし(Normarizing)は、JIS記号でHNRです。
焼ならしは「組織を整える」というイメージです。
5.高周波焼入れ
この章から表面熱処理でよく利用される「高周波焼入れ」、「浸炭処理」、「窒化処理」について解説していきます。
高周波焼入れは、交流電源による誘導加熱によって、表面部分だけ800℃以上に加熱する方法です。主にシャフト形状やギア形状部品の硬さ向や耐疲労性の向上を目的に用いられます。高周波焼入れはJIS記号でHQI(Induction Hardening)で表されます。電熱用のコイルを部品に近接させて、コイルに高周波誘導電流を通すことで、抵抗熱により部品表面が急速に加熱される原理を利用します。その後、低温での焼もどしにより、靭性を回復させます。
高周波焼入れは表面のみ焼入れが行われますので、表面は硬くなり耐摩耗性などが向上しつつ、内部には靭性を備えた状態が残ります。部分的にしか熱が加わらないため、変形や寸法変化も少なくて済みます。
シャフト形状などは、熱処理後に曲がり等の変形が生じる場合がありますので、プレス機等での歪取りが行われます。表面のみ焼入れされることで、表面に圧縮残留応力が発生し、耐疲労性が向上します。また、高周波焼入れによる表面の硬さは、通常の焼入れ/焼もどしよりもやや硬くなります。
高周波焼入れは加熱時間が短時間で済むため環境にやさしい熱処理と言われています。全体焼入れと異なり、焼入れする部位や焼入れの深さを指定できるという特徴もあります。表面焼入れの一種ですが、表面焼入れには他に、「炎焼入れ(JIS記号でHQF)」、「電子ビーム焼入れ」、「レーザー焼入れ」もあります。
6.浸炭処理
鋼鉄を焼入れするためには、炭素が必要となります。炭素鋼などの炭素含有量の多い鋼鉄は焼入れが可能ですが、低炭素鋼など炭素含有量の少ない鋼鉄は焼入れができません。このような場合に、表面の炭素分を高めて焼入れを行う手法が浸炭(しんたん)処理です。浸炭処理はJIS記号ではHC(Carburizing)で表されます。
低炭素鋼は粘りがあり、高炭素鋼に比べると安価で加工性に優れていますが、硬さが劣ります。浸炭処理は表面だけ硬さを高めることができますので、低炭素鋼の良い部分を生かし、劣る部分を強化する優れた手法と言えます。
浸炭処理では「浸炭剤」を部品と一緒に加熱して、部品表面に炭素を拡散させ浸透させます。浸炭剤の種類に応じて、固体浸炭(炭)、液体浸炭(シアン化塩)、ガス浸炭(炭化水素系ガス)の手法があります。
浸炭処理は、高温で長時間加熱するため、部品の中心部の組織が変質します。このため、浸炭処理後には、焼入れ/焼もどし処理を行います。主に低炭素鋼に用いられますので、表面は硬く耐摩耗性に優れた性質を持ちながら、内部は柔軟な構造を保つことができます。S15Cなどの低炭素鋼や、SCM415などの炭素含有量の少ないものがよく用いられます。
浸炭処理により得られる硬い層(硬化層)には、全体硬化層深さと有効硬化層深さの2種類の深さ規定があります。有効硬化層深さは、「焼入れのまま、または200℃を超えない温度で焼もどしを行った時の表面から550HVとなる深さまでの距離」(JIS G 0559より)です。
全体硬化層深さは、素材そのものの硬さまでの距離となります。
有効深さは指定が可能ですが、熱処理業者によっては決まった範囲しか対応していないところも多く、有効深さ0.3~1.5mm程度で処理されることが多いようです。
7.窒化処理
窒化処理は、部品の表面を窒素の化合物として硬さを高める手法です。ガス窒化、塩浴窒化、ガス軟窒化、イオン窒化などがあります。オーステナイト化温度以下の温度域で、アンモニアや窒素を含んだ雰囲気中に暴露することで、表面近傍に窒素を浸透させて硬化させる処理です。
窒化処理は処理温度を上げる必要がないため、処理後の熱処理が不要となり、変形等が生じにくいという特徴があります。窒化処理はJIS記号ではHNT(Nitriding)で表されます。
1000HV程度まで硬くなる窒化処理と、600HB程度の軟窒化処理に分かれます。硬くして主に耐摩耗性を向上させる目的の場合は窒化処理、耐疲労性を改善させたい場合は軟窒化が選択されます。
処理温度が低いため、調質鋼などでも、内部の硬さを保持したまま表面の硬さを向上させることができる点も特徴と言えます。また、SUS304やSUS316などのオーステナイト系ステンレスにも利用される処理として知られています。処理温度に応じて、窒化層の厚さと硬さが変化し、窒化層の厚さは概ね0.1~0.5mm程度となります。
8.まとめ ‐ 熱処理を考慮した設計のポイント
今回は設備部品でよく使われる熱処理について解説しました。熱処理によって、部品の表面を硬くしたり、耐摩耗性や耐衝撃性を向上させたりすることができる大変有効な手段だということをご理解いただけたと思います。特に、材質の硬さが変化するということが大きなポイントですね。
一方で、熱処理を用いる際には、設計上気をつけなければいけない注意点もあります。
熱処理全般に言えることは、熱を加えることで変形や寸法変化が生じるということです。精度の必要な箇所は、あらかじめ余肉をつけておき、熱処理後に仕上げ加工を行って精度の良い形状に整えるという工程が必要になります。
熱処理で硬くなった部品は、エンドミルでの切削加工が困難になる可能性もあります。HRC60を超えると切削加工による仕上げが難しくなってきますので、余肉の程度や箇所、仕上げ方法について事前に確認が必要です。
平面や円筒形状の内外径であれば研削加工での仕上げが比較的容易です。段差のある形状では、研削用の砥石の側面が当たらないように、研削加工用のニガシ形状(逃げ溝など)が必要となります。
複雑な形状で通常の切削加工での仕上げが難しい場合は、プロファイル研削盤やジグ研削盤での仕上げ加工となりますので加工コストも割高となります。もちろん、仕上げの箇所が少ない方がコストを低減できますので、最小限の仕上げ加工で済むような設計を心がけてください。
変形を生じさせたくない場合は、窒化処理を選択することも一案と思います。また、表面の硬さが必要な場合は、熱処理だけでなく前回ご紹介した「硬質クロムメッキ」や「ニッケルメッキ」等も選択肢になると思います。
今回ご紹介した熱処理をうまく使いこなして、合理的な設計に役立てていただければ幸いです。