みなさんこんにちは!
電通総研の金型ソリューションチーム“Mold Planner”です。
私たちは金型設計製造を行われている製造業のみなさまに、30年以上に渡りCAD/CAM/CAEなどのITツールをご提供し、業務改革をお手伝いしています。
前回(第3回)の「金型設計者が活用するCAEのすゝめ」では、設計根拠を導き出すため、試行錯誤するツールとして金型設計者がCAEを活用する事例をご紹介しました。
今回は、金型設計として試行錯誤の必要がない単純な「作業」を徹底的に効率化している事例を、CADの最新機能を交えながらご紹介します。
これからお話する内容は、次の通りです。
- 金型設計業務を分析すると…
- 金型設計者はどのような「作業」に時間を費やしているのか?
- 金型設計作業の効率化事例
- 最新トピックス
金型設計業務を分析すると…
私たちは、数多くの企業に対して金型設計業務の効率化支援をしています。
その際に金型設計業務を分析した上で効率化施策を決定しますが、一般的な幾つかの企業の分析結果を集計すると以下の図のようになります。
業務は以下の5つに分類できます。
- 作業 ・・・手を動かす業務
- 思考・検討 ・・・頭を使う業務
- チェック ・・・設計した結果を検証する業務
- 修正 ・・・チェックの指摘を反映する業務
- 打合せ ・・・他部門との調整や相談する業務

【図1】金型設計業務内訳
このグラフを見ると、多くの金型設計者は「作業」に時間を費やしていることが分かります。
今回は、業務工数比率が高い「作業」に着目し、効率化を実現した取り組み事例をご紹介していきます。
金型設計者はどのような「作業」に時間を費やしているのか?
リードタイム短縮、作業工数削減を目的とした効率化活動は、ほとんどの企業で進められていますが、それでも未だに6割以上の「作業」が残っているのが現状です。
私たちの経験では自社で効率化活動された企業でも、この「作業」を徹底的に効率化することで、業務全体の工数を30%程度削減出来るケースがほとんどです。
この「作業」を徹底的に効率化する際に、以下の2点に注目して分析を行います。
①作業の抽出
②作業の分類
まず、「① 作業の抽出」についてです。
エジェクタピン設計を例にして、「作業の抽出」の分析内容についてご説明します。
エジェクタピン設計を分析する場合、「エジェクタピンのレイアウト検討」と「エジェクタピンの詳細設計」の様に、大まかな工程に分解してしまうと、各工程の中に「思考」と「作業」が混在し、どのように効率化すべきかが見えてきません。
そこで、以下のように、更に分解してみます。
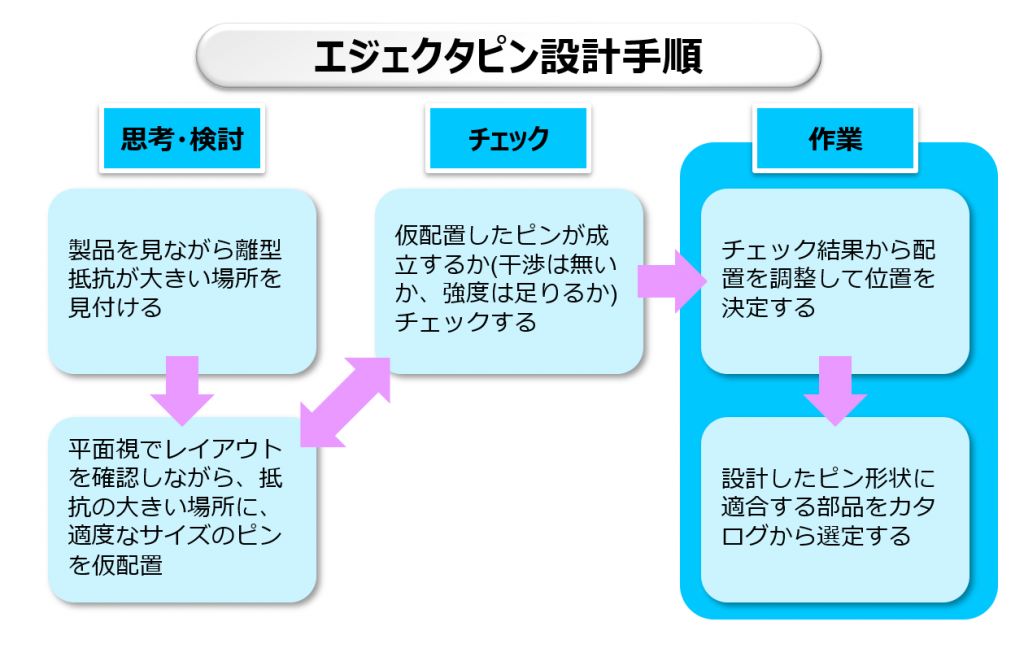
【図2】エジェクタピン設計分析
この様に詳細な工程に分解することで一連の流れが実は5つの工程に分解でき、今まで見えていなかった単純な「作業」が抽出され、初めて効率化することができます。
こうして作業の抽出ができたら、「② 作業の分類」に移ります。
金型設計作業の多くはCADを操作する「モデリング」ですが、大きく2つに分類されます。
一つは、単純で何度も同じ操作をする「繰り返しモデリング」であり、もう一つは毎回異なり複雑な操作となる「特殊モデリング」です。
「繰り返しモデリング」は、標準化した「部品」や「操作手順」をライブラリ登録して、誰でも再利用できるようにすることで大幅に作業効率を改善できます。
また、標準化を進めることで設計者によってバラついていたCAD操作も統一化でき、他の設計者が作成したモデルでも容易に修正することが出来るようになります。
「特殊モデリング」は、操作手順を標準化することが困難ですが、最近のCAD機能の進化により飛躍的に作業効率を改善できる様になってきています。
以上の2つの視点で「作業」効率化の取り組み事例をご紹介します。
金型設計作業の効率化事例
まずは、「繰り返しモデリング」を効率化する事例を幾つかご紹介します。
標準部品のライブラリ登録と選択配置
まずは、インストールすれば簡単に環境を構築できる「Mold EX-Press」を利用し、3次元の金型設計をスタートすることをお勧めします。
【動画1】ミスミ金型用標準部品3D CADライブラリ「Mold EX-Press」
私たちが推奨するミスミ金型用標準部品3D CADライブラリ「Mold EX-Press」の詳細は、リンク先ホームページに掲載されています。ご興味のある方は、ぜひ、お立ち寄りください。
3D部品ライブラリ環境構築の次に効率化を進めたい工程としては、エジェクタピンのようにタイプや寸法違いの部品を数多く配置しなければいけないケースです。
一つ一つの部品に対し、カタログを確認しながら、何度も部品選定と配置を繰り返す操作は非効率です。
このような部品は専用機能により、部品の選定と配置を自動化することで、効率化している事例があります。【動画2】
前章でお話させて頂いたように、エジェクタピンは幾つかの工程に分解して設計を進めます。
構想設計段階では製品モデルを参照し、「思考・検討」しながらエジェクタの径と位置のみをレイアウトします。
詳細設計に入り、構想設計でレイアウトされた円筒ソリッドの径と高さに合致する市販部品をライブラリから検索し、部品選定、部品配置も自動で行います。
この機能によりエジェクタピン設計を大幅に効率化できます。
【動画2】規格部品の自動選定・自動配置
また、各個別部品の選定、配置が効率化できたとしても、全ての部品を積み木のように積み上げていく操作には時間がかかります。
そのため、ある程度一緒に検討する部品群を一つのユニットとしてライブラリ登録し、再利用することで、更に効率的な設計を実現されている事例があります。【動画3】
ユニットとしては、「モールドベース」「スライド」「傾斜」「ホットランナ」等を分けて登録されるケースが一般的ですが、製品仕様が大きく変化しないような金型であれば、金型構造モデル一式をユニット化して登録するケースもあります。
登録方法としては、ユニットの各部品寸法を決定するための設計標準をEXCELに組み込み、3Dモデルとリンクさせます。これによりEXCEL上でユニット仕様を入力することで各部品の寸法が決定し、3Dモデルが連動して形状更新できます。設計標準とモデルを切り分けることにより、設計根拠が明確となり、設計標準のメンテナンス性も向上させることができます。
【動画3】ユニット一括配置
私たちが推奨する金型設計支援パッケージ「Mold Planner」の詳細は、リンク先ホームページに掲載しています。ご興味のある方は、ぜひ、お立ち寄りください。
操作手順の再利用
次に、形状部位を繰り返しモデリングするため「操作手順」をライブラリとして登録し、再利用することで効率化している事例をご紹介します。
パーティング面にガス抜きの溝を掘る場合、パーティングラインに沿って一定距離オフセットした位置に溝形状をモデリングする操作は多いかと思います。
一連の操作手順は常に同じですが、製品によってパーティングラインが異なるため、事前に形状を作成しておくことは困難です。
そのような場合、形状ではなく「操作手順」を登録して再利用することで効率化できます。【動画4】
操作手順のライブラリ登録は、プログラミングすることなく金型設計者自身が作成したモデリング履歴をもとに簡単に登録できます。
「ゲート」「ランナー」「油溝」なども同様に操作手順をライブラリ化し、作業効率を大幅改善できたという事例もあります。
【動画4】操作手順の再利用
次に、「特殊モデリング」を効率化する事例を幾つかご紹介します。
難しい形状をモデリングする場合、高度なCADスキルや作業工数が必要となりますが、最近のCAD機能は非常に高度化し、容易にモデリングできるケースも増えています。
一般的に煩雑なモデリングとして取り上げられるものとしては「入れ子モデルへの金型要件盛り込み」や「冷却配管設計」があります。
以下では、この煩雑なモデリングを短時間で作り込んでいる事例をご紹介します。
入れ子モデルへの金型要件盛り込み
金型要件は、キャビティ・コアに分割した後に盛り込むケースも多くあります。
入れ子に分割されたソリッドに対して金型要件を盛り込む場合、複雑にからみ合った製品設計モデルの履歴を変更するより、今ある形状を直接変更する「ダイレクトモデリング」の手法を活用した方が有効です。
ダイレクトモデリングの勾配機能は、履歴がなくとも、対象フェースに隣接するR面を自動認識し、勾配付けに対してR面を追従させることが可能です。【動画5】
【動画5】履歴なしモデルへの勾配付与
また、金型設計では、成形性や加工性などの製造工程上の都合により、製品設計仕様に問題がない程度でR面の値を変更する場合があります。
今回は、ダイレクトモデリング手法で、形状の深い部分に工具の突き出しが届くように徐変Rに変更する事例をご紹介します。【動画6】
【動画6】履歴なしモデルへのR面変更
冷却配管設計
その他、煩雑なモデリングとしてよくお聞きする「冷却配管設計」は、ある点と点を結ぶ経路(ルーティング)を簡単に設定、編集できるモデリング手法が必要です。
金型内部の冷却配管には直線的の径路、型外のホース配管にはスプライン径路を設定します。
部品に干渉しないように限られた3D空間を縫って経路を定義するモデリングは、非常に手間がかかります。
また、部品の追加や配置済部品の位置変更に対応するため、冷却の経路は修正しやすくなければなりません。
配管モデリングに特化したルーティング機能を利用し、型内の直線的な冷却配管を設計している事例を紹介します。【動画7】
【動画7】型内水管設計
以下は、型外のホース配管の設計です。ライブラリから冷却部品一式を呼び出し、ホースを冷却プラグにつなぎ、部品表でホース長さが自動で反映されるまでの事例をご紹介します。【動画8】
【動画8】型外ホース配管設計
私たちが推奨するCADパッケージ「NX」の詳細は、リンク先ホームページに掲載しています。ご興味のある方は、ぜひ、お立ち寄りください。
最新トピックス
日本の製造業は長い間、図面を利用してモノづくりをしてきました。最近は「図面レス」をあるべき姿としている企業もありますが、それでも「完全な」図面レスにより金型製造できているメーカーは限定的です。
CAD開発元も図面作成を効率化する為、図面表題欄に部品名や材質や個数などを自動記入する機能、外形や穴に自動で寸法を入れる機能など様々な機能を開発してきました。
そんな図面作成の中でも、設計者の悩みの一つに設計変更に伴う図面の改定履歴の記入、更新があります。
「いつ、どんな変更をしたのか」「変わったのはどこか」「以前の寸法からどれだけ変わったのか」など、さかのぼって確認する場面は多々あります。
その図面更新を自動で認識し、変更箇所に訂正番号を自動で振る事例を最新トピックスとしてご紹介します。【動画9】
【動画9】図面訂正番号自動追加
私たちが推奨するCADパッケージ「NX」の詳細は、リンク先ホームページに掲載しています。ご興味のある方は、ぜひ、お立ち寄りください。
以上ご紹介してきた様に、CAD機能は日々進化を続けています。皆様も最新のCAD機能を有効活用することで3次元金型設計を効率化しましょう。
今回は金型設計の「作業」を徹底的に効率化する事例を新機能も交えてご紹介してきました。
次回は、NCプログラム作成作業について金型設計と同様に3Dモデルを活用して徹底的に効率化する事例をご紹介いたします。
ぜひ、次回の記事をお楽しみに!