接合を指示する製図の知識(スライドプレートの例)
前回はフライス盤で加工する板物の図面を使って、その図面の悪さと改善点をビフォー・アフター形式で解説しました。
今回は、フライス盤と旋盤で加工する部品を互いに接合した部品図に着目して解説します。部品同士の接合には様々な手法や手段があります。その表現方法を知りましょう。
meviy 2D|PDF図面アップロードで簡単操作
かんたん見積もりはこちらから >
目次
1)機械的接合の種類
一般的な図面は、1枚の図面の中に1つの部品を示した一品一葉図(いっぴんいちようず)として作成しますが、その他に1枚の図面の中に複数の部品を示した多品一様図(たひんいちようず)もあります。
多品一葉図は、製品やユニットの組立図として表現される場合と複数の部品が接合されて構成される部品の場合があります。今回は複数部品が接合されて構成される部品の図面を取り上げます。
部品同士を機械的に接合する手段には次の種類があります(表3-1)。
表3-1 機械的接合の種類
接合名称 | 特徴 | 備考 |
---|---|---|
溶融接合 | 材料を溶かして接合し、一般的に溶接と呼ぶ | アーク溶接や抵抗溶接など |
液相接合 | 材料を溶かさずに融点の低い合金(ロウやはんだ)を隙間に流し込み接合する | ロウ付け、はんだ付けなど |
固相接合 | 材料の接触面に高速回転する丸棒状のツールを押し付け、摩擦熱で接合する | 摩擦攪拌接合(FSW:Friction Stir Welding)と呼ばれる |
接着 | 接着剤や両面テープなどで接合する | |
ねじ固定 | ボルトやナットで締め付けて接合する | |
圧入 | 部品間の締め代の圧力を利用して接合する | |
カシメ | 2つの材料に穴を開け挿入物を変形させて接合する | リベットやバーリングカシメなど |
表3-1の接合の種類のうち複数部品が結合された状態で納品される部品の場合、溶接や圧入による接合が一般的です。
溶接の種類
溶接は、次のように分類できます(表3-2)。
表3-2 溶接の種類
融接アーク溶接手アーク 溶接被覆アーク溶接 |
|||||
---|---|---|---|---|---|
ティグ(TIG)溶接 | |||||
半自動 アーク 溶接 |
ソリッド ワイヤー |
炭酸ガスアーク溶接 | |||
ミグ(MIG)溶接 | |||||
マグ(MAG)溶接 | |||||
フラックス入り ワイヤー |
炭酸ガス(CO2)溶接 | ||||
セルフシールドアーク溶接 | |||||
自動溶接 | サブマージアーク溶接 | ||||
ガス溶接 | |||||
テルミット溶接 | |||||
電子ビーム溶接 | |||||
レーザー溶接 | |||||
圧接抵抗溶接スポット溶接 |
隅肉(すみにく)溶接とは
溶接の種類の中でも、丸物や板物の接合に多用されるのがミグ(MIG)溶接やマグ(MAG)溶接による隅肉溶接です。
隅肉溶接は、直交する2つの材料の接合の隅部にビードと呼ばれる溶融金属の盛りあがりを付けて接合する手法です。そのため溶接部のビードが邪魔にならないように周辺の部品の配置を検討します(図3-1)。
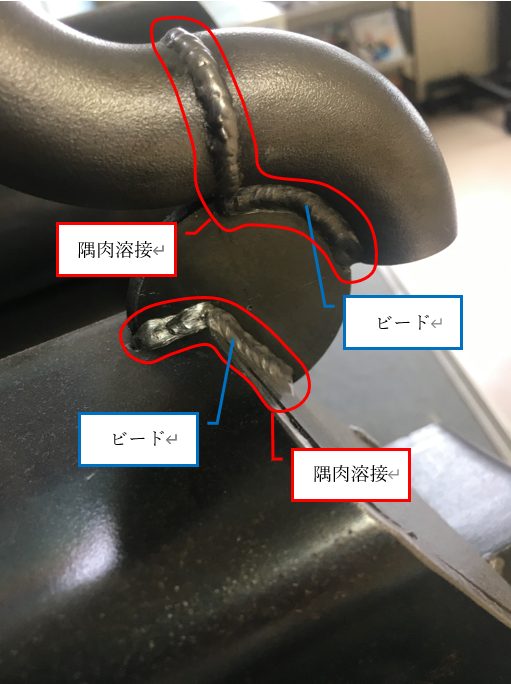
図3-1 隅肉溶接とビード
圧入(あつにゅう)とは
圧入は“しまりばめ”とも呼ばれます。丸穴に軸を挿入する構造が一般的です。穴の直径よりも軸の直径がわずかに大きく、互いの部品が干渉する状態でプレス機などを使って大きな圧力をかけて挿入し接合します。止まり穴に軸を圧入する場合もありますが、加工や圧入作業の容易さから貫通穴に軸を挿入することが一般的です。
例えば圧入部(1)の裏面のように面一まで軸を挿入したり、圧入部(2)のように治具を使って軸をわずかに飛び出させたりすることもできます(図3-2)。
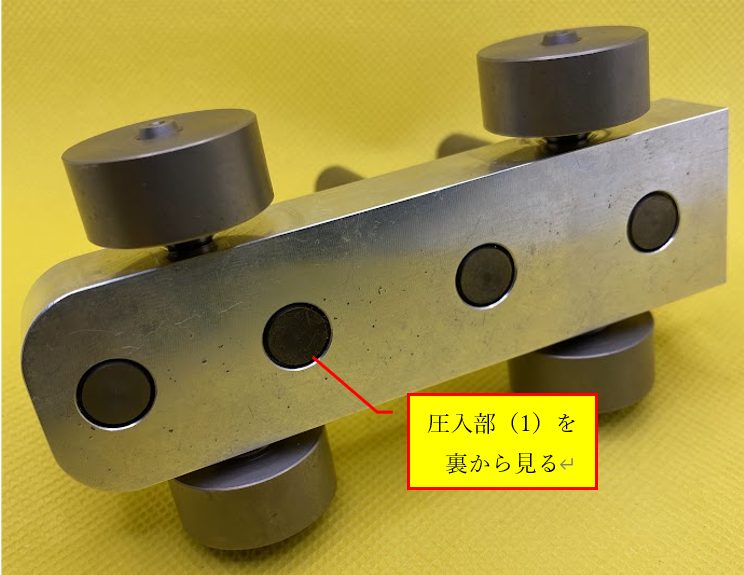
図3-2 圧入の状態の例
隅肉溶接にしろ、圧入にしろ、図面にどうやって接合するのかを明記せずに部品手配している図面が散見されます。発注側と最終受注側の間に何社も経由して手配されていると加工者が設計者に直接問い合わせることが難しくなり、加工者の想像で部品が接合され納品されることになります。
想定外の接合手段で仕上げられた部品の場合、組立時に他部品と干渉したり耐久性がなく将来的に破損したりするリスクもあります。
接合手段を第三者に伝える図面の指示方法を知りましょう。
2)参考とする図面のビフォー・アフター(スライドプレートの例)
本来であれば、組立図からその部品の機能(基準となる取付面や関連する寸法など)を見極めて、投影図や寸法などを記入しなければなりませんが、今回のシリーズで使用する部品図は組立図のない単品図しか所有していません。そのため筆者の経験からその機能を想像ながら解説します。ご了承ください。
今回事例として取り上げる図面は、厚めの平板にピンが立っている「スライドプレート」という名称の部品になります(図3-3)。
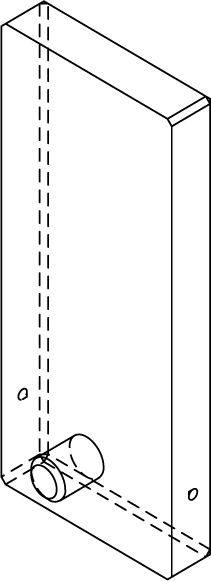
図3-3 スライドプレートの3Dモデル
スライドプレートのビフォー図面
それでは現状のスライドプレートの図面の悪さを、事実として列記していきます。
なお、解説の前提条件として下図における左側の図を正面図、右側の図を右側面図と呼びます(図3-2)。
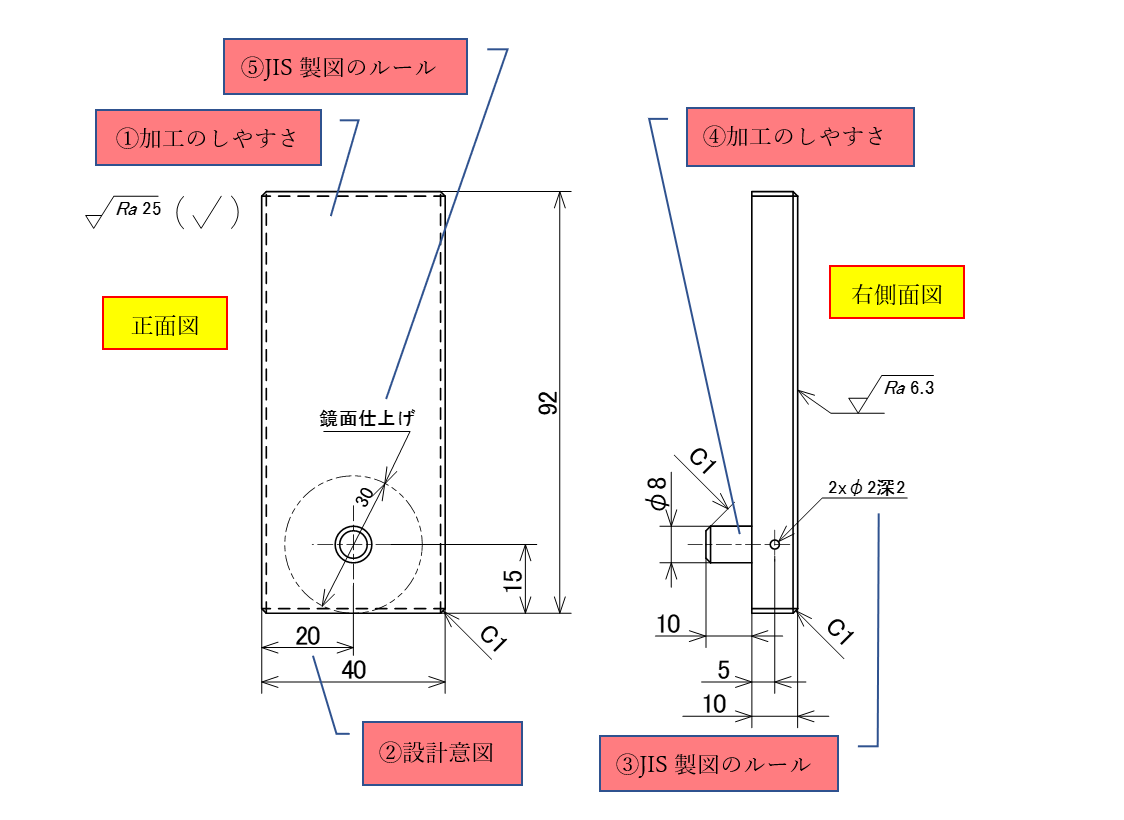
図3-2 スライドプレートのビフォー図面
① 投影図の向き(加工のしやすさ)
正面図において部品が縦向きに配置されています。この向きのままで最も広い面が横向きになりフライス盤で加工する際の取付姿勢として不適切であることがわかります。
② 対称位置の寸法(設計意図)
現状の正面図の寸法記入では、幅寸法40にばらつきが生じても、それとは無関係に左側から寸法20を狙うような指示になっています。設計意図として穴位置は左右の面に対して対称位置(中央)にあるべきと考えますので、現状の寸法指示は設計意図通りにはなっていません。
③ 旧JISの記入法(JIS製図のルール)
穴深さを指示する場合「深」という表記は旧JISのルールです。現在はJIS製図標準に従った記号で表現しなければいけません。加えて、裏面に存在する穴の個数まで合わせて指示することはできません。
④ 接合手段が不明(加工のしやすさ)
平板にピンが立っていますが、ピンの接合方法が明示されていません。板から削り出すのか?ピンを溶接するのか?ピンを圧入するのか?あるいはピンをねじ固定してよいのかもわからないため、加工者泣かせの図面となっています。
⑤ 表現方法の誤り(JIS製図のルール)
範囲を示す細い二点鎖線を使って示されており、JIS製図のルール上間違いになります。さらに「鏡面仕上げ」と注記が書かれていますがどのような加工で、どの程度の粗さが必要か?情報がないため、検査のしようがありません。
スライドプレートのアフター図面
次に改善した図面例を確認しましょう。
なお、解説の前提条件として下図における右下の図を正面図、右上の図を平面図、左下の図を左側面図と呼びます(図3-3)。
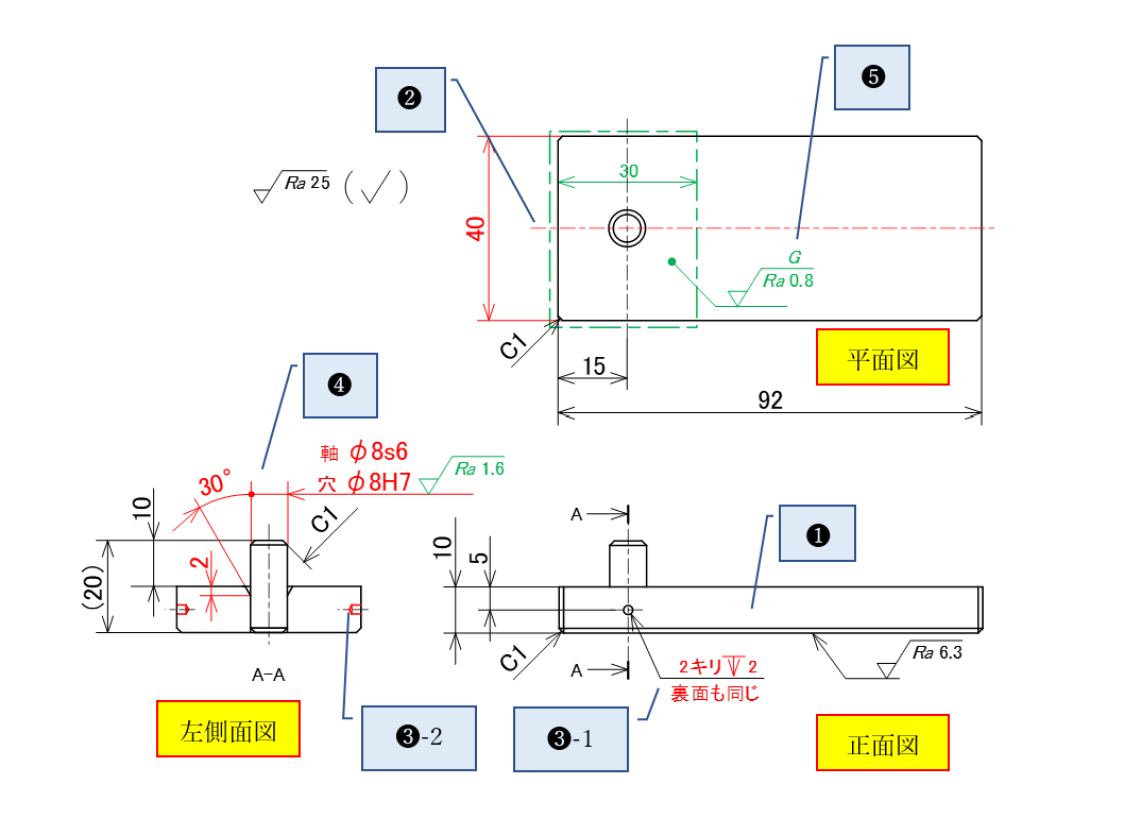
図3-3 スライドプレートのアフター図面
❶投影図の向き
フライス盤加工しやすい向きとして、切削面積の広い面を上下に向けるよう修正しました。
❷センター振り分け寸法
平面図に対称中心線(赤く示した一点鎖線)を記入し、全幅寸法40のみとしました。ピンの上下方向位置の寸法がありませんが、対称中心線によって暗黙的に中央であることを指します。これをセンター振り分け寸法と呼びます。
❸個数表記と穴深さ記号
「2xφ2深2」の寸法表記ですが、JIS製図のルール上、穴やねじなどの個数は同じ投影図に見えるものしか数えることができません。したがって裏面にあるφ2の数まで表現できないので「裏面も同じ」という注記で補足しました。
穴深さに関して、旧JISでは「深」や「x」で表していましたが、2010年に改正された“穴深さ記号( )”を使って指示します。
φ2の止まり穴は「φ2」のままの表記でも構いません。しかし、穴の奥にドリル刃先の円すい穴形状が残っても構わないことを明示するために「キリ」という言葉を使うと加工者は安心してドリル加工できます。
このとき、左側面の断面図ではφ2の穴が見えていますので、先端の円すい形状を描き忘れないよう注意しましょう。標準ドリルの刃先角度はJISによって118°と規定されています。
CADで形状を描く際には118°(あるいは120°でも可)にしてください。円すい穴形状はドリルによる成り行きの形状ですので、図面に角度寸法の指示は記入しません(図3-4)。
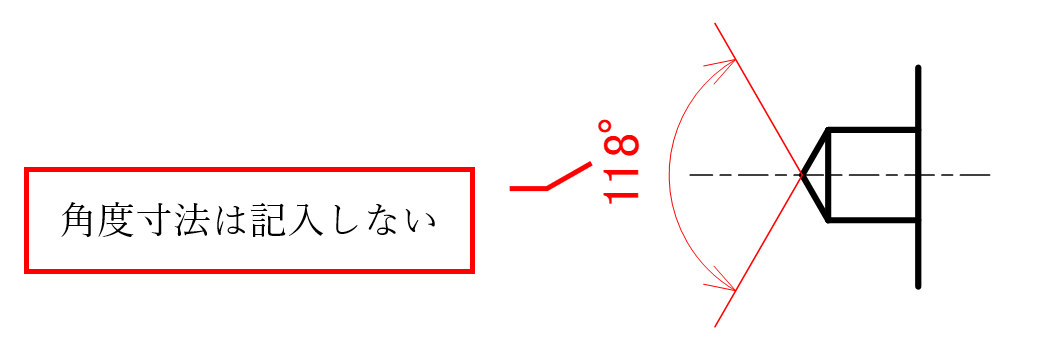
図3-4 ドリル刃先が残す円錐穴形状の拡大図
❹接合手段の明示とそれに伴う寸法の追加
ビフォー図面ではピンの接合手段が明記されていませんでした。丸物と板物の接合方法は溶接や圧入が考えられます。溶接に比べると圧入の方がコスト的に安価になることが多いため、圧入する場合の軸や穴の詳細形状と寸法の公差を示すには断面図が最適です。
組み合わせ図面の場合、平板の穴径とピンのそれぞれの直径は一つの寸法線に2段に重ねて記入することができます。このとき、どちらの寸法を示しているのかを「穴」や「軸」など読み手が誤解しないように補足することを忘れてはいけません。
軸のサイズ公差はプラス側になる「s6」として穴よりも大きくなるようにしています。
また、ピンの先端は元図ではC1面取りであったため、ピン側に挿入性を向上させる30°のテーパー面取りはせず、平板側に30°のテーパー面取りを指示しました。
平板に貫通穴を加工し、そこに長さ寸法20のピンを下面まで押しこめばよいため、特別な治具や調整も不要です。
他の接合手段として圧入を選択せず、溶接で接合する場合も考えてみましょう。
隅肉溶接を指示する場合
溶接で接合する際は、穴とピンのはめあいは“すきまばめ”でよいため、軸のサイズ公差をマイナス側になる「h7」として手で挿入できるようにしています。
隅肉溶接を明示するために、溶接部分から引き出した線に隅肉溶接の記号(直角三角形の記号)を付与します。
しかし、隅肉溶接は平板とピンの直交部にビードの盛り上がりが生じるため、ピンに挿入する相手部品との干渉が懸念され現実的ではありません(図3-5)。
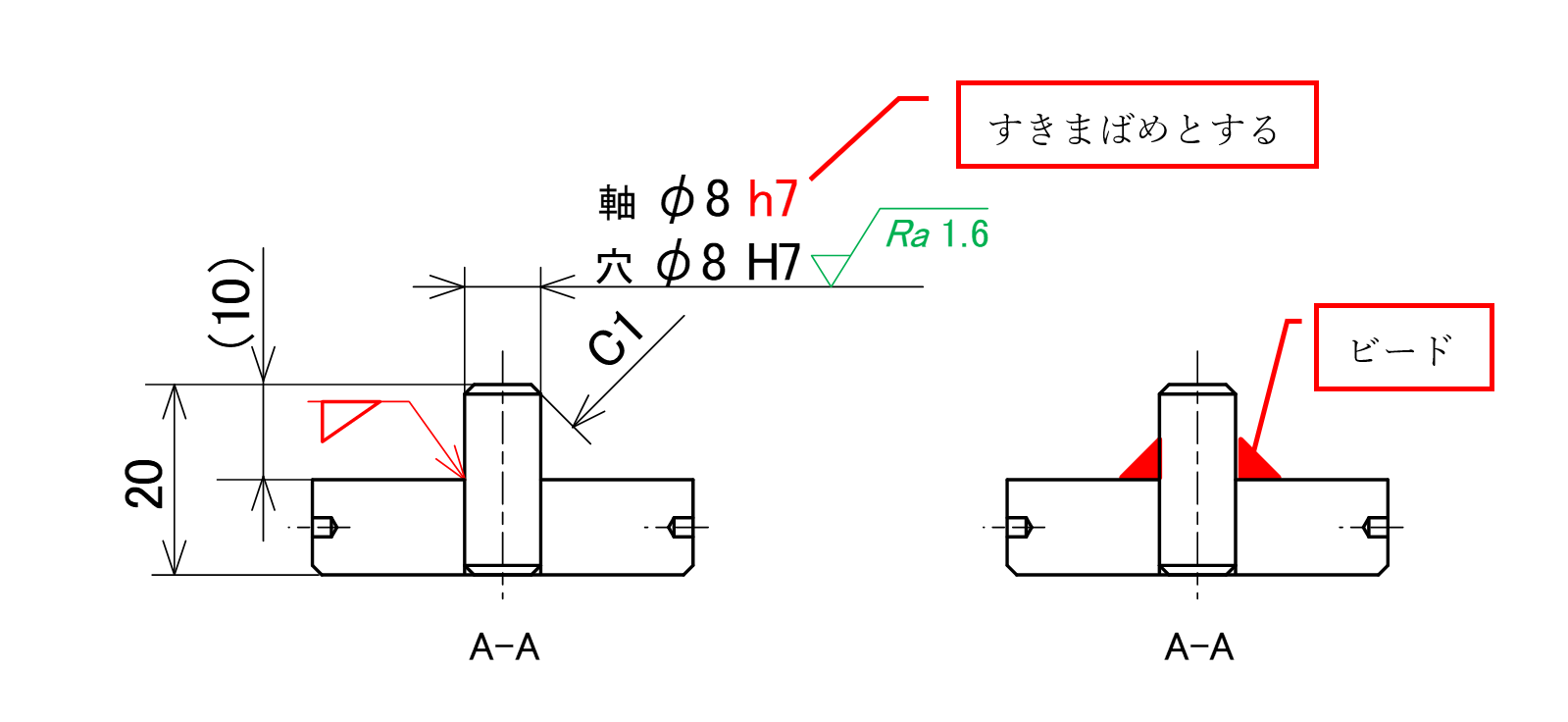
図3-5 隅肉溶接で接合する場合
プラグ溶接を指示する場合
ピンが突出している側に溶接のビードを残すことができないとなると、平板の裏面から溶接するしか手段がありません。この時、図3-4「ドリル刃先が残す円錐穴形状の拡大図
」のように、ピンが平板の裏面いっぱいまで存在すると溶加材が入る隙間がなくなり接合できません。
そこで、溶加材が入るスペースを作るために、例えば2mm程度ピンを短くして平板の裏面から穴をふさぐような形で溶接を行います。これを“プラグ溶接”といい、プラグ溶接記号( )を付与します。
プラグ溶接記号の下にある横線は平ら仕上げを意味し、記号Gはグラインダーで加工することを意味します。したがって溶加材が面からはみ出た部分を「ディスクサンダーなどを使って平らにしなさい」という意味になります(図3-6)。
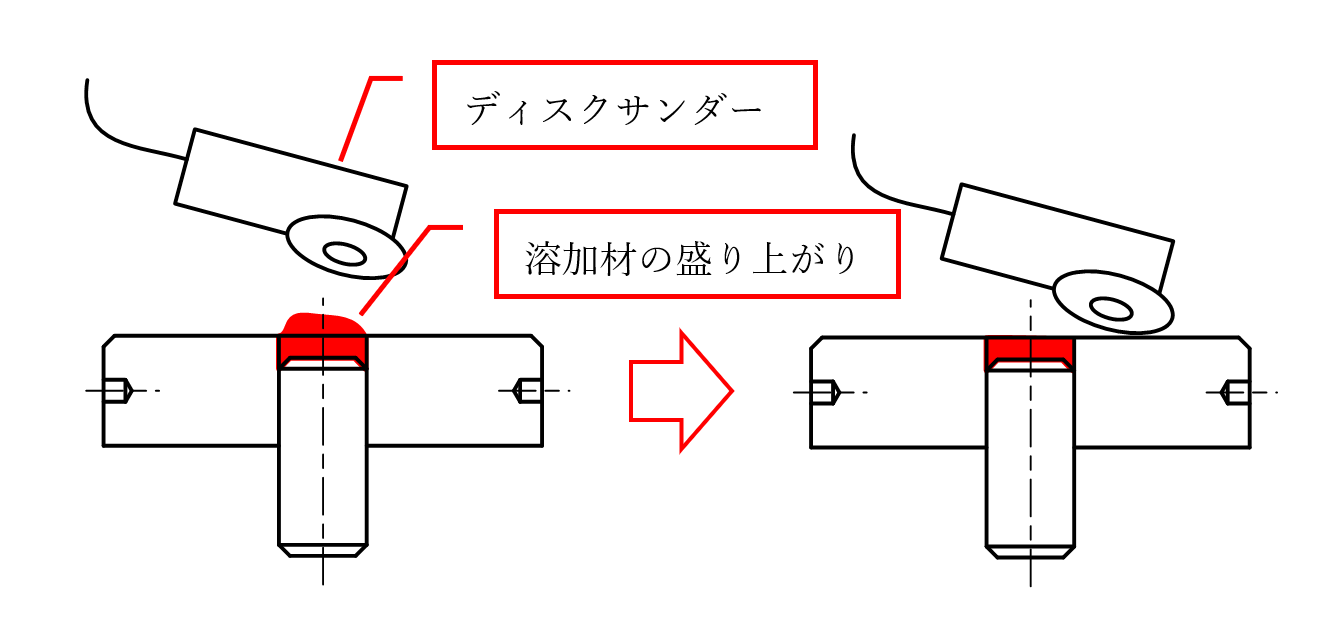
図3-6 グラインダー仕上げのイメージ
ここで、a)の構造を見てみると、ピンがすきまばめのため自由に動いてしまって位置決めができません。そのため治具などを別に準備しなければならず手間がかかります。
逆に、b)のようにピンに段差を設けると位置決めはピン単独でできますが、ピンの段差加工する分、部品単価がわずかに高くなります。どちらがトータルコストとして安くなるかは製造側と協議するとよいでしょう(図3-7)。
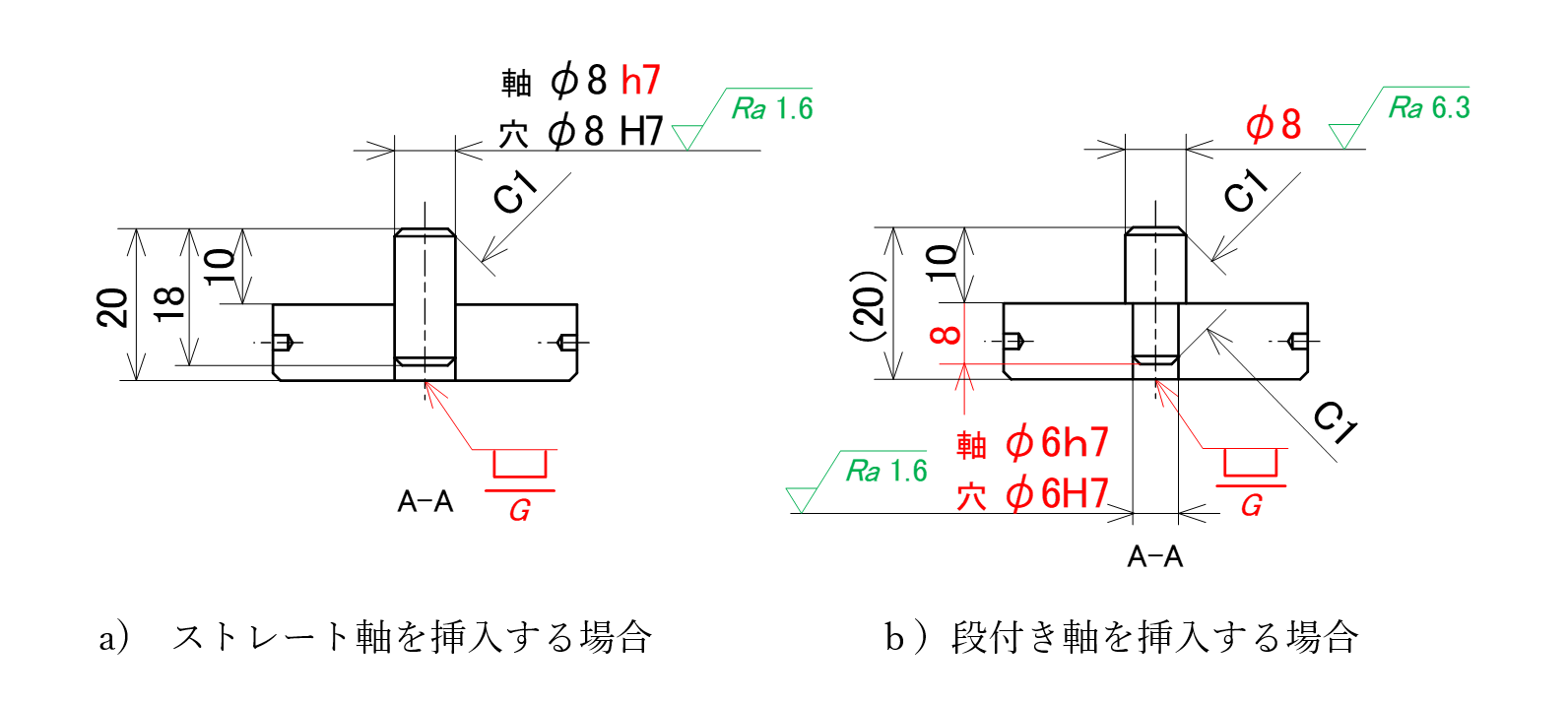
図3-7 プラグ溶接で接合する場合
❺仕上げ方法と粗さの記号
元の図面では、ピンの周辺で部品が回転接触すると思われる直径30の円形部分だけ、鏡面仕上げが指示されていました。鏡面仕上げといってもどの程度の粗さまで仕上げるのか、加工者には判断できませんし検査もできません。例えば、平面研削盤で表面を磨く程度でよければ、表面粗さ記号「Ra0.8」として指示したうえで研削盤を使う記号Gを記入します。
平面研削盤の構造と原理を示し、前後左右に併進動作するテーブルに磁力によってワークを固定します。その上から回転する砥石がワークを数μm~数十μm削りながら表面を磨きます(図3-8)。
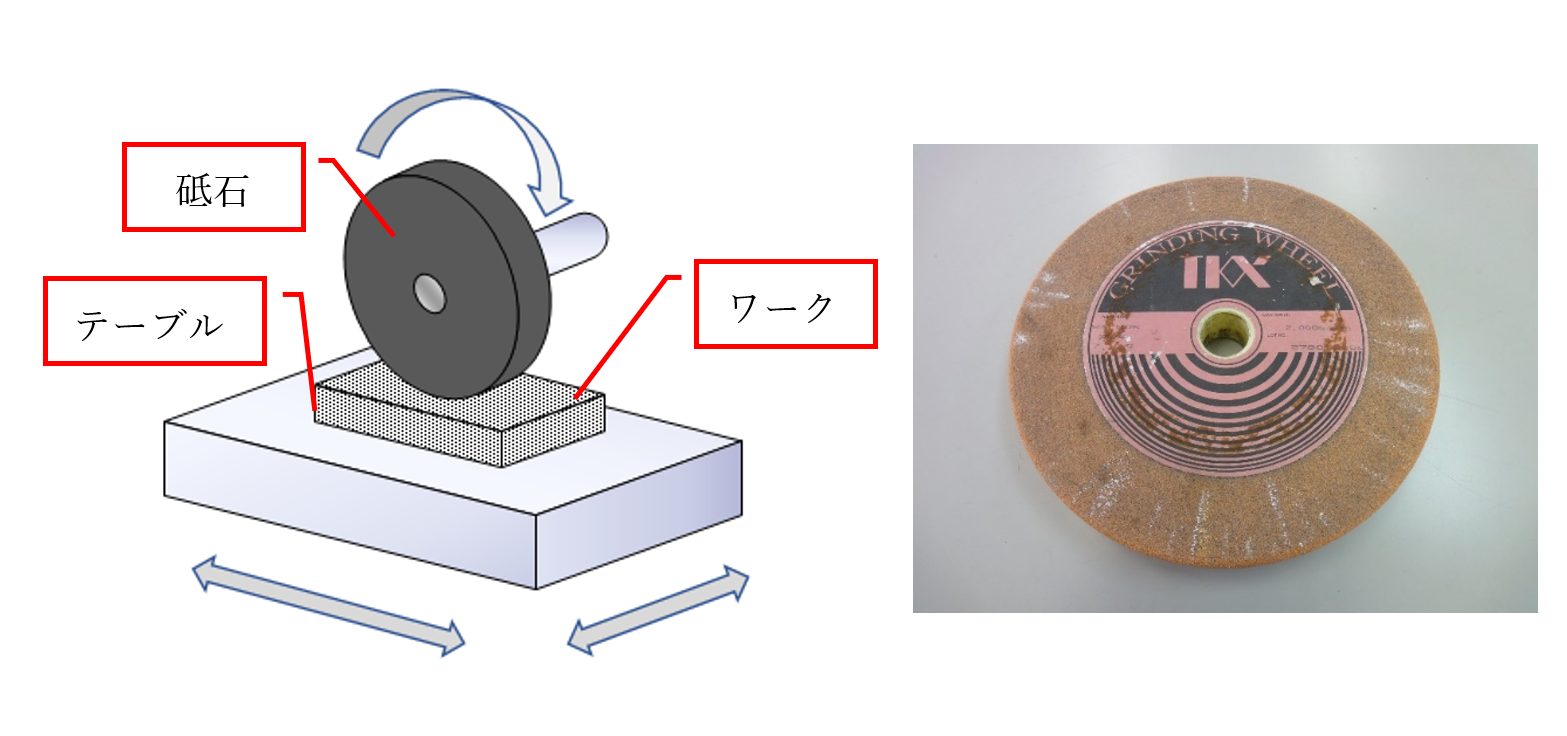
図3-8 平面研削盤の構造と砥石
研削などの領域を指定する場合は太い一点鎖線を用います。
機能上は直径30の円形部分のみ研削加工してあれば問題ないのですが、研削盤は円盤状の砥石が平面を前後左右の動作によって研削するため円の領域で研削することができません。
この場合、関係のない面まで仕上げられてしまいますが、矩形領域で指示すれば加工方法に合致した指示にすることができます。この時、ピンが取り付けられていると邪魔になりますので、ピンの取付前の状態で研削します(図3-9)。
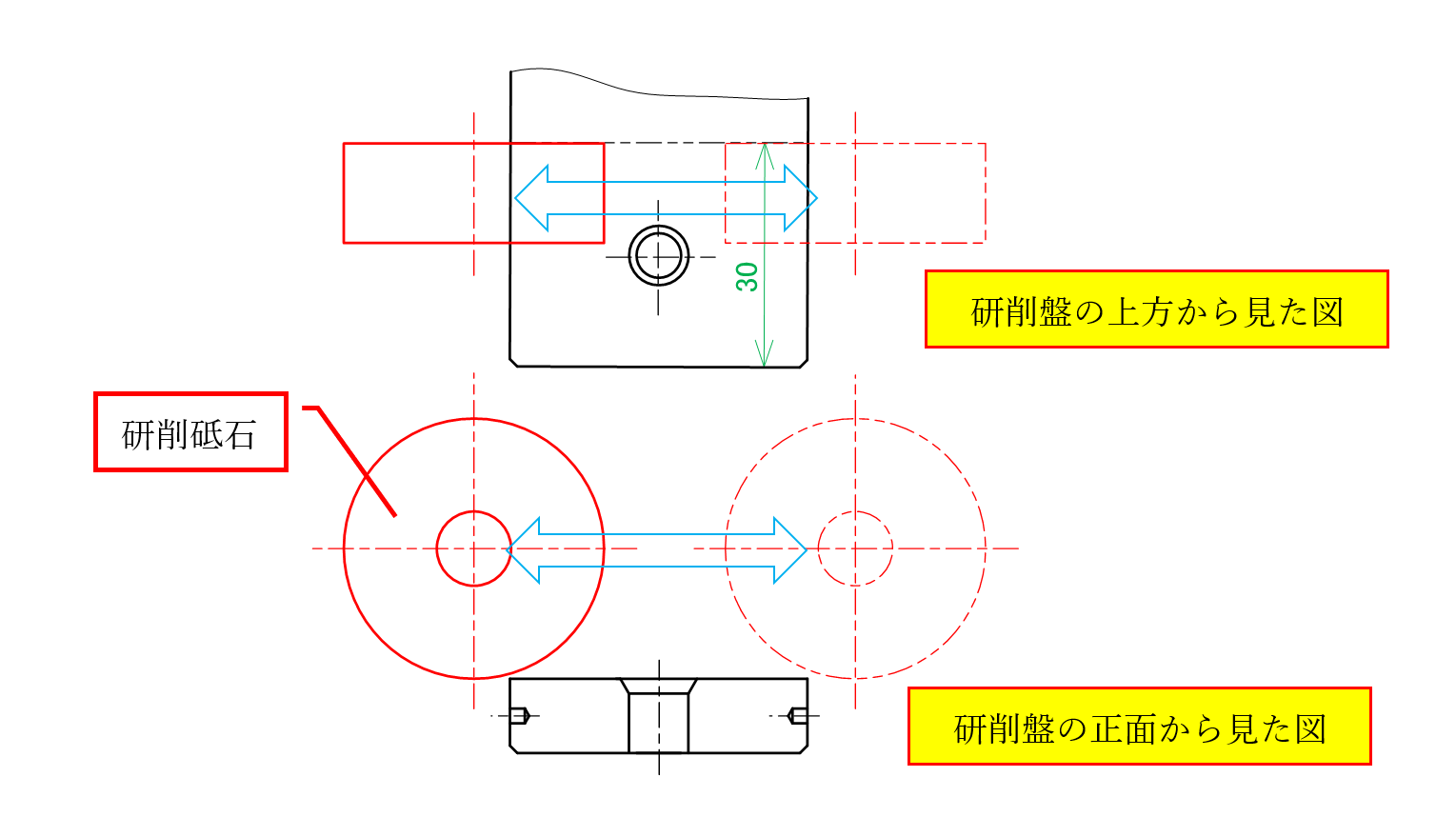
図3-9 平面研削盤で指定された領域の加工状態
【平面研削盤】円盤状の砥石が往復運動するよ!(凹み部は研削できひんねん)
3)まとめ
今回は、板物と丸物を接合して1つの部品として製作する図面の悪さと改善点を紹介しました。
最終形状のみの投影図を描いて、接合する手段を明記しない図面が散見されます。
そのような図面を描いた設計者に確認すると「加工の知識がない自分が指定するより、加工者にお任せした方が安心できるから」と回答が返ってきます。
しかし、加工者にお任せのままでは、加工担当者が変わった場合や発注先企業が変わった時に違う手段で部品が製作されることで、ピンが外れる、ピンが折れるなどの不具合が生じるリスクが増えます。
部品の不具合に伴う製品のクレームは、最終的に設計者が責任を負わなければいけません。 製品の機能を知らない加工者に丸投げで部品を製作することは許されません。 接合手段やそれを図面に指示できる製図の知識を得るようにしましょう。 |
製品の機能を知らない加工者に丸投げで部品を製作してはいけません。
図面不備による部品の不具合に伴う製品のクレームは、最終的に設計者が責任を負うことになります。
次回は、特殊加工する部品を製図する際に、その悪さと改善点のポイントをビフォー・アフター形式で解説します。