板金の製図ビフォー・アフター!レーザー加工の例
前回は板物と丸物の接合部品の図面を使って、その図面の悪さと改善点をビフォー・アフター形式で解説しました。
今回は、フライス盤を使って加工できる板物ですが、フライス盤より加工効率の良いレーザー加工を指定する部品図に着目して解説します。フライス盤の工程とレーザー加工の工程の違いを知りましょう。
meviy 2D|PDF図面アップロードで簡単操作
かんたん見積もりはこちらから >
目次
1)レーザー加工の特徴
レーザー加工機(レーザーカッターとも呼ぶ)は、レーザー光を照射し材料の表面温度を上昇・蒸発させて加工する工作機械です。鉄鋼板であれば厚み0.1~12mm程度まで切断可能です(図4-1)。
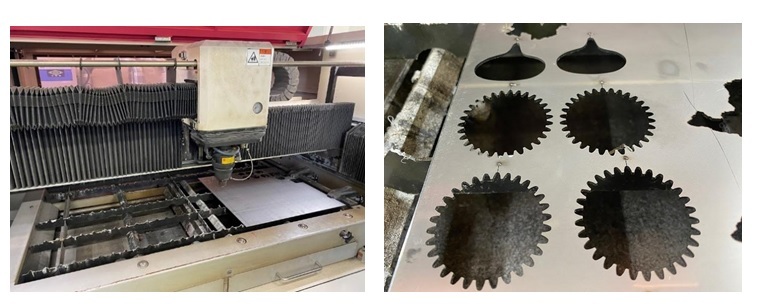
図4-1 レーザー加工機
レーザー加工は一筆書きの要領で自由な形状の切断や穴あけ以外に肉盛りや文字などのマーキングができます。
フライス盤による切削加工やワイヤーカットによる放電加工と比べて加工速度が早いことがメリットですが、切断面が粗くなってしまうデメリットがあります(図4-2)。
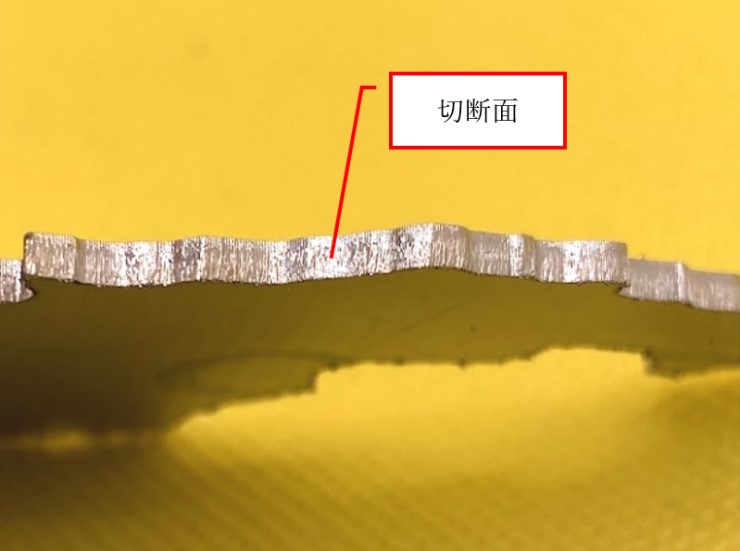
図4-2 レーザー加工した部品例と切断面
レーザー加工でマーキングと穴あけ、外周切断の様子を確認しましょう。
動画が始まって28秒までがマーキング工程、34秒までが穴あけ、その後が外周切断になります。
動画から、レーザーの出力に応じてマーキングと切断が分けられ、自由形状を切断できる便利な加工法であることが判ったと思います。
2)参考とする図面のビフォー・アフター(プレートの例)
本来であれば、組立図からその部品の機能(基準となる取付面や関連する寸法など)を見極めて、投影図や寸法などを記入しなければいけませんが、今回のシリーズで使用する部品図は組立図のない単品図しか所有していません。そのため筆者の経験からその機能を想像ながら解説します。ご了承ください。
今回事例として取り上げる図面は、厚み5mmで若干複雑な形状をした外形を持つ板物の「プレート」という名称の部品です(図4-3)。
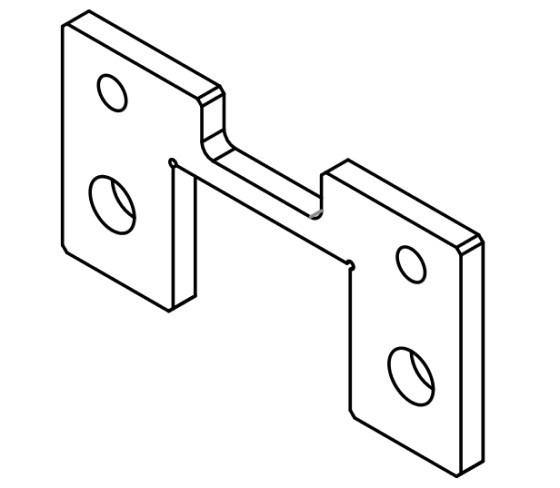
図4-3 プレートの3Dモデル
プレートのビフォー図面
それでは現状のプレートの図面の悪さを、事実として列記していきます。
なお、解説の前提条件として、下図における下側の図を正面図、上側の図を平面図と呼びます(図4-4)。
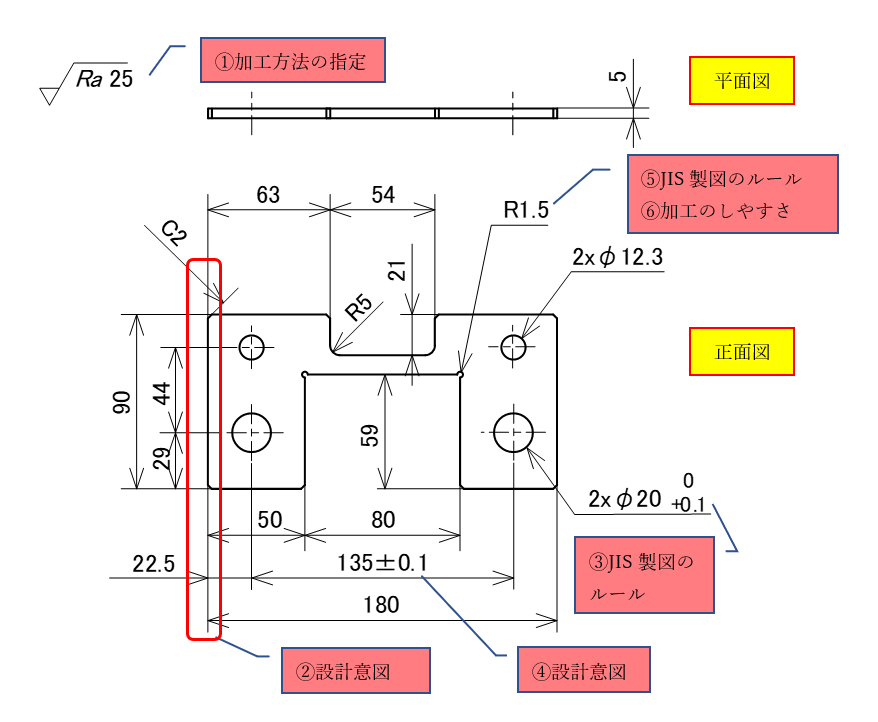
図4-4 プレートのビフォー図面
①粗さ記号の意味(加工方法の指定)
代表記号で示された粗さ記号の形が三角形状(下図のb)参照)をしていることから、全面の切削加工を要求する指示になっています。しかし5mm厚の板を購入すれば板厚部分は切削加工しなくて済みます。粗さの基本記号の違いを示します(図4-5)。
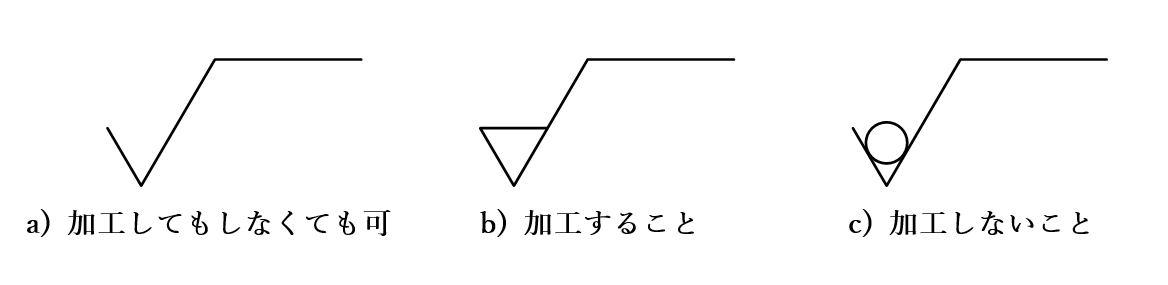
図4-5 粗さの基本記号の違い
②端面を基準とした寸法配列(設計意図)
正面図の左端面を基準に寸法線が配列されています。製図上、この寸法配列自体は問題ないのですが寸法から逆算すると、この部品は左右対称形状をしており裏向きで組むことも可能となります。
表裏で取り付けができると基準面が左右に移動してしまい、設計者としてどういった設計思想なのか説明ができなくなります。
③サイズ公差の記入法(JIS製図のルール)
穴のサイズ公差が2段に記入されていますが、プラスの公差が下側にあります。単なる記入ミスなのか、マイナス公差として記入するつもりがCADの入力操作を誤ってプラス表記になってしまったのか判断できません。
④公差の適用形体(設計意図)
穴位置の寸法(135)に公差が付いています。しかし、この公差は「2つのφ20穴のピッチだけに適用するのか?」その上にある「2つのφ12.3穴のピッチにも適用するのか?」が判断できません。穴の直径に公差が付与されていることから考えると2つのφ20穴のピッチだけに公差を適用するように思えます。
しかし、検査時に2つのφ12.3穴のピッチまで検査されて公差外れであった場合、機能的に問題がないのに不良品と判断されるリスクがあります。
⑤円弧の寸法表記(JIS製図のルール)
円弧部の寸法表記が「R1.5」となっています。JIS製図では特別な理由がない限り180°を超える円弧は直径指示すると決められています。また加工上も直径3mmのドリルを使うことが想像できます。
⑥逃がし穴の設定(加工のしやすさ)
フライス盤でエンドミルを使って角穴加工する場合、隅部にはエンドミルの半径分の丸みが付くためエッジ形状に加工することができません。相手部品を挿入するために隅部に丸みがあってはいけない場合、隅部の丸みを回避するため、四隅に逃がし穴を設けるのが一般的です(図4-6)。
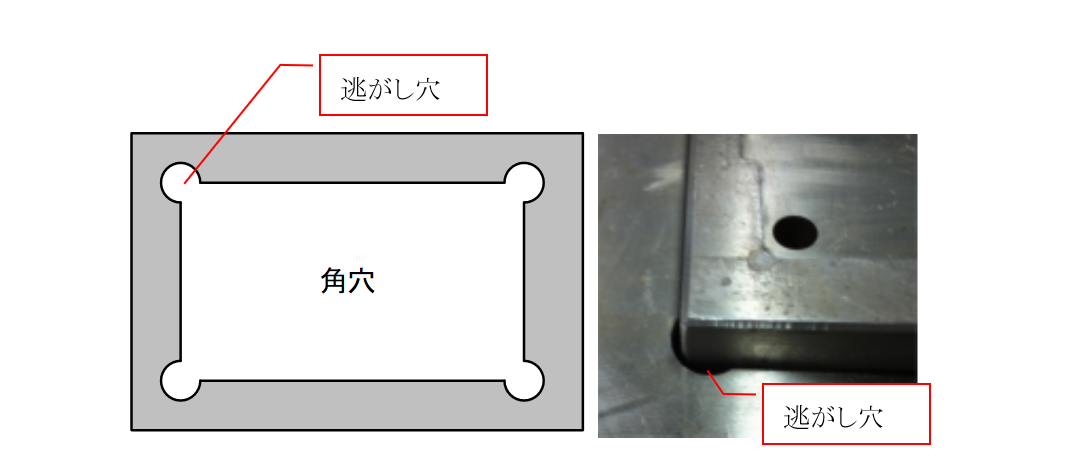
図4-6 四隅の逃がし穴
ビフォー図面では、切り欠き隅部の逃がし穴の直径が3mmと小さく、隅部に丸みを残さないように加工するには角穴の外周を直径3mm以下のエンドミルで切削しなければいけません。
これでは、刃物径が小さすぎて加工時間が増え、コスト高になります(図4-7)。
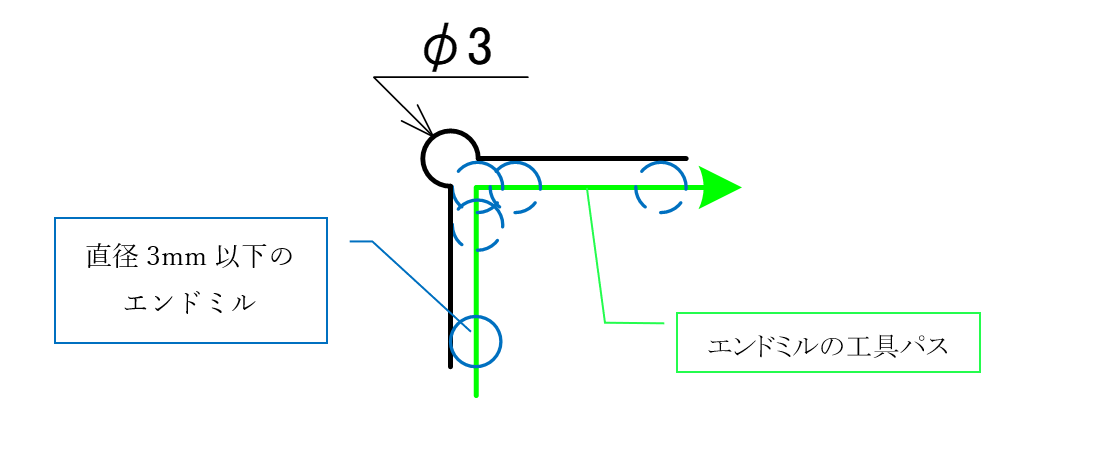
図4-7 丸みが付かないためのエンドミルの直径と工具パス
プレートのアフター図面
次に改善した図面例を確認しましょう。
なお、解説の前提条件として下図における下側の図を正面図、上側の図を平面図と呼びます(図4-8)。
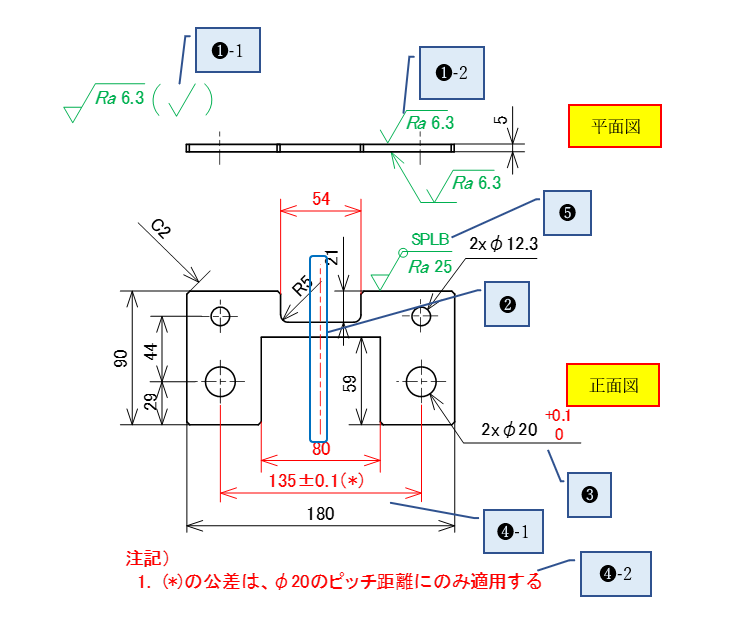
図4-8 プレートのアフター図面
❶加工方法の冗長性
- 代表記号として粗さ記号を付与することで粗さ記号のない面はRa6.3とするよう指示しています。後ろに続くかっこの中の記号は“他の種類の粗さがある”ことを示しています。
- 平面図に▽記号の上側が開放された記号が2か所あります。指示された面は「加工しても加工しなくてもよい」という意味を持ち、購入した板のままでもよいし切削加工してもよいことを示し、加工の冗長性を表しています。
❷設計意図を表す寸法配列
左右対称形状であるため表裏が変わっても組み付けができます。
そこで中心基準になるよう対称中心線(図中の青枠)を記入したうえでセンター振り分け寸法(図中の赤色寸法)で指示しなおしました。
❸正しい公差の表記
図示サイズ(基準寸法のこと)に対して非対称の公差を指示する場合、正の許容差を上側に負の許容差を下側に2段に分けて記入します。
❹公差適用部の明示
- 位置の公差を適用する部位がわかるよう注記に誘導する記号を付けました。
- 注記として、位置の公差を適用する部位を明記しました。
❺粗さ記号を使った加工方法の指示
粗さ記号の角部に全周記号「〇」印をつけることで外周はその粗さを適用することを意味します。加えて、粗さ記号の上に加工方法の記号を記入することもできます。
加工方法の記号「SPLB」の「SP」はSpecial Processing(特殊加工)を意味します。「LB」はLaser Beam Machining(レーザー加工)を意味します。レーザー加工することで角穴の隅部はR0.2程度の丸みしかつかないため、ビフォー図面にあった逃がし穴の形状が不要になります。
レーザー加工の欠点として、穴の直径や穴ピッチなどに厳しい寸法精度を要求することができないため、穴に関してはレーザー加工を指定せず、代表記号の表面粗さ「Ra6.3」を適用し、フライス盤加工などレーザー加工以外の加工機を選択できるようにしています。
JISで規定する加工方法の記号には次のようなものがあります(表4-1)。
表4-1 加工方法の記号(JIS B 0122 機械加工からの抜粋)
加工方法 | 記号 | 参考 |
---|---|---|
旋削 | L | Lathe Turning |
穴あけ | D | Drilling |
リーマ仕上げ | DR | Drilling Reaming |
フライス削り | M | Milling |
ブローチ削り | BR | Broaching |
研削 | G | Grinding |
ラッピング | GL | Grinding Lapping |
放電加工 | SPED | Special Processing Electric Discharge Machining |
電子ビーム加工 | SPEB | Special Processing Electron Beam Machining |
ただし、特に加工方法を指定したいという設計意図がある場合を除いて、これらの記号を粗さ記号に付与することはありません。
3)まとめ
今回のような5mmという板厚はブロックから切削加工もできるし、厚板素材をレーザー加工することもできます。様々な加工の手段を知れば選択肢が広がりコストを考慮した図面を描くことができます。表面粗さ記号を利用して、加工方法を指定したり、逆に加工の自由度をあげたりするテクニックも知りました。
加工の基本に忠実な図面を描いたつもりでも、逆にそれが足かせになって加工が面倒になりコスト高になることもあります。しかし、加工の素人である設計者の独断で加工方法を指示することも避けなければいけません。 |
出図前に加工部門と打ち合わせを行い、最適な加工方法を図面に反映する手段を知ることができました。
次回は、薄板のプレス部品を製図する際に、その悪さと改善点のポイントをビフォー・アフター形式で解説します。