板金形状設計の腕の見せ所
板金部品というと、薄くて変形しやすいというイメージがあります。確かに切削部品に比べると厚みの差から圧倒的に変形しやすいのですが、形状の特徴をうまく利用すれば少しでもその変形のしやすさを克服することができます。
meviy 2D|PDF図面アップロードで簡単操作
かんたん見積もりはこちらから >
目次
1.板金部品が受ける荷重の向きの考え方
板金部品の剛性(変形のしにくさ)は、荷重方向に対する断面係数Zの値が大きくなるようにすることがポイントです(表2-1)。
表2-1に示した断面係数Zの式から、次のことがわかります(図2-1)。
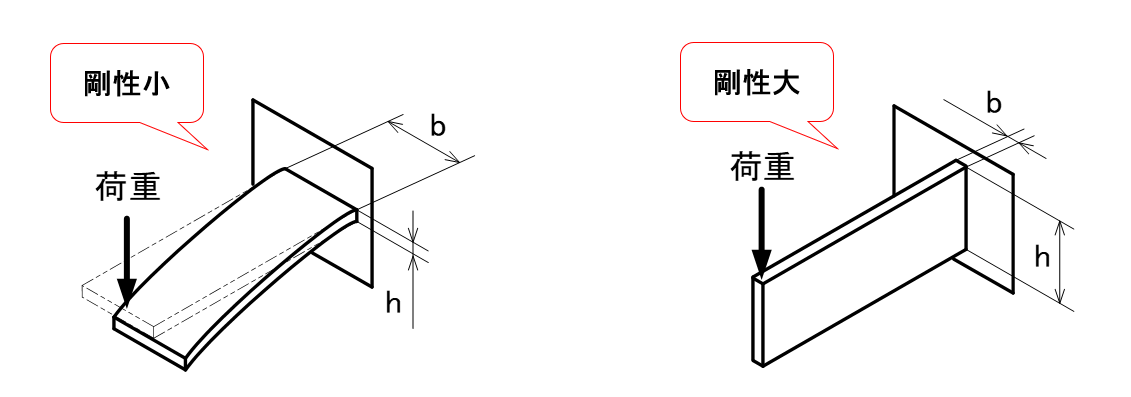
図2-1 同じ形状の板材が受ける荷重の方向と剛性
- 横寸法 bと、縦寸法 hが分子にあるので、どちらの値も大きいほど断面係数Zが大きくなる。
- 縦寸法hは2乗で効くので、縦寸法 hを大きくするほど断面係数Zを効果的に大きくできる。
したがって、薄板であっても縦寸法hが大きくなる向きで荷重を受けるように配置すれば剛性を上げることができます。
2.板金の寸法精度の考え方
板金は「打抜き加工」と「曲げ加工」に大別できます。
寸法数値に公差指示がない場合に適用するものを普通寸法公差(普通許容差、一般公差、普通公差とも呼ぶ)といい、JISに数値が規定されています。
打抜き加工と曲げ加工の普通寸法公差を比較してみましょう(表2-2、表2-3)。
表2-2 金属プレス部品の打抜きの普通寸法公差(JIS B 0408)
寸法の区分 | 公差等級 | ||
A級 | B級 | C級 | |
6以下 | ±0.05 | ±0.1 | ±0.3 |
6を超え30以下 | ±0.1 | ±0.2 | ±0.5 |
30を超え120以下 | ±0.15 | ±0.3 | ±0.8 |
120を超え400以下 | ±0.2 | ±0.5 | ±1.2 |
400を超え1000以下 | ±0.3 | ±0.8 | ±2 |
1000を超え2000以下 | ±0.5 | ±1.2 | ±3 |
備考:A級、B級及びC級は、それぞれJIS B 0405の公差等級f、m及びcに相当する
表2-3 金属プレス部品の曲げおよび絞りの普通寸法公差(JIS B 0408)
寸法の区分 | 公差等級 | ||
A級 | B級 | C級 | |
6以下 | ±0.1 | ±0.3 | ±0.5 |
6を超え30以下 | ±0.2 | ±0.5 | ±1 |
30を超え120以下 | ±0.3 | ±0.8 | ±1.5 |
120を超え400以下 | ±0.5 | ±1.2 | ±2.5 |
400を超え1000以下 | ±0.8 | ±2 | ±4 |
1000を超え2000以下 | ±1.2 | ±3 | ±6 |
備考:A級、B級及びC級は、それぞれJIS B 0405の公差等級f、m及びcに相当する
「打抜きの普通寸法公差」と「曲げおよび絞りの普通寸法公差」で寸法の区分ごとの数値を比べると、曲げや絞りの数値が大きく、打抜きよりも曲げの方が、加工精度を上げることが難しいことがわかります。
公差等級のA級、B級、C級の選択は、企業や事業所ごとに決められています。
例えば、公差等級B級を適用する事業所の場合、寸法「100」の普通寸法公差は表2-2「30を超え120以下の公差等級B級」と表2-3「30を超え120以下の公差等級B級」で黄色くマーキングした許容差が適用されます。
それぞれの許容差を図に描き表すと赤字のようになり、打抜きと曲げの精度に違いがあることが判ります(図2-2)。
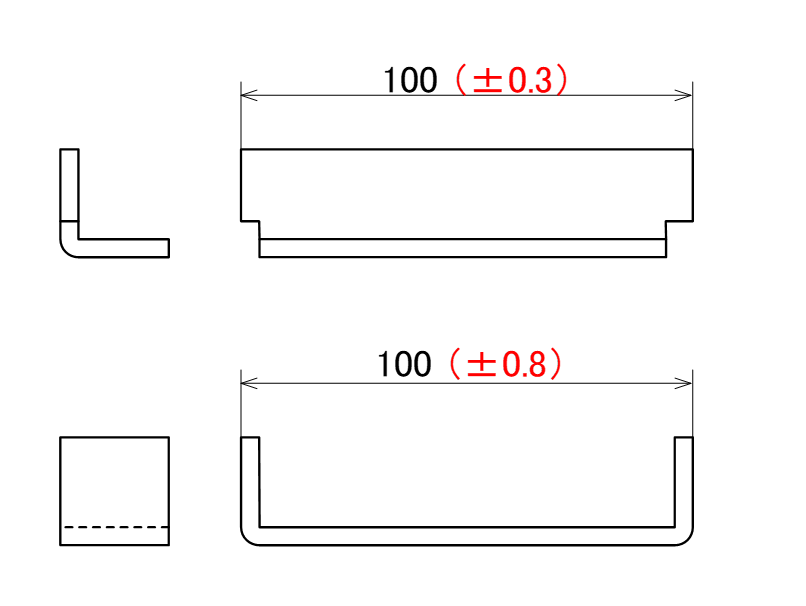
図2-2 打抜きと曲げの普通寸法公差の差
3.板金の形状設計の考え方
板金設計におけるポイントは薄い板を曲げて断面係数を有効に利用できるかが設計者の腕の見せ所です。少しでも強度を上げたいからと厚めの平板を使用するよりも、薄板を曲げて剛性を上げれば軽量化にもつながります(図2-3)。
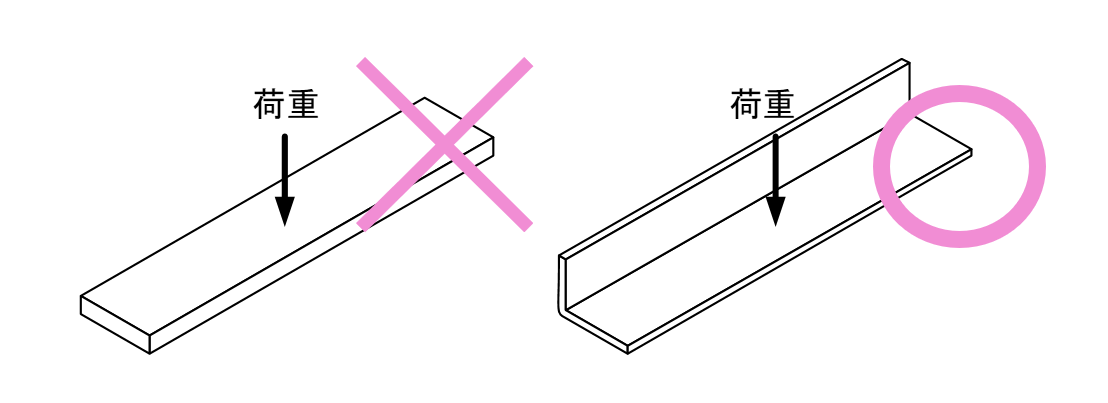
図2-3 平板とL字曲げの板の差
取付けねじによって固定されるブラケットがあり、矢印方向に荷重を受ける場合を考えてみましょう。
① 荷重を受ける面が平板形状の場合
平板形状の面に荷重をかけると、断面係数の値が小さいことから平板の面全体がたわんで変形しそうというのがわかると思います(図2-4)。
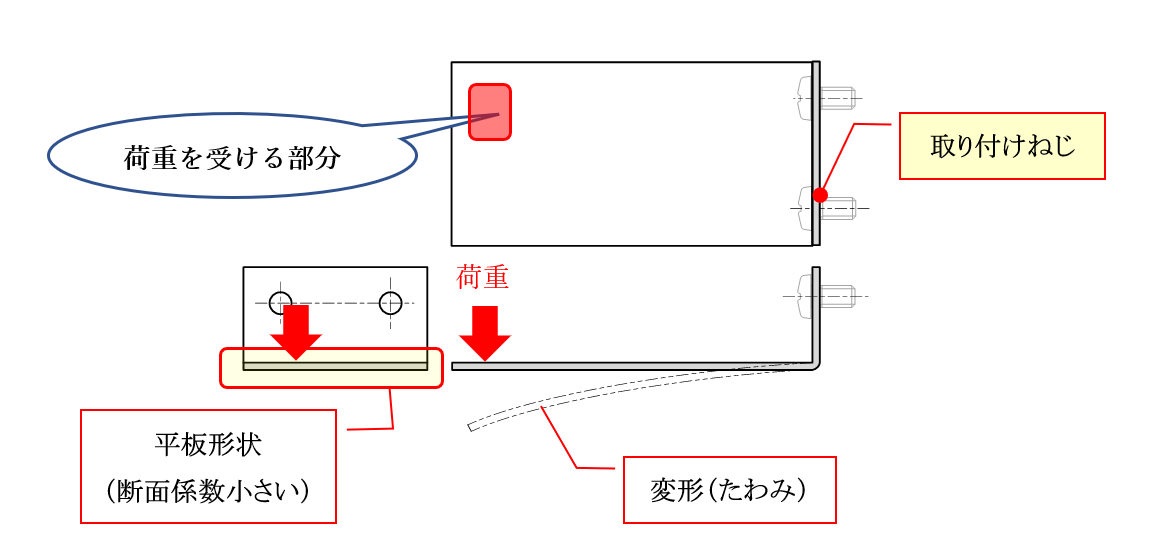
図2-4 ブラケットの基本形状と荷重による変形
② 荷重を受ける面を曲げ形状にした場合
図2-4の形状に対して断面係数を大きくするため、荷重を受ける部分に近い側の端部に曲げを追加しました。曲げの追加によって荷重を受ける面全体のたわみはなくなりますが、取付けねじ下部にあるL曲げの根元に荷重による応力が集中し、L曲げの根元から変形してしまいます(図2-5)。
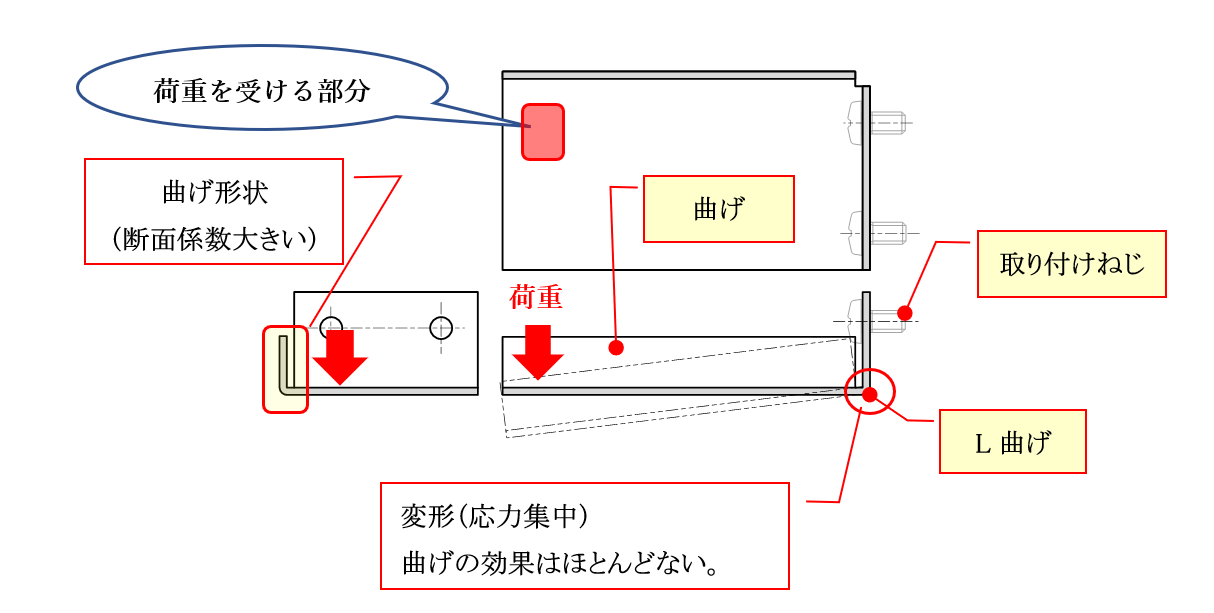
図2-5 曲げ面の追加と応力集中による変形
③ 荷重を受ける面の曲げ形状をねじ固定部につなげた場合
図2-5の曲げ面の高さを増やしつつ、さらに横曲げを追加してねじの固定部とつなげました。荷重は断面係数の大きい面を通してねじ固定部で受けることができ、L曲げ根元の応力集中が緩和され剛性アップが期待できます(図2-6)。
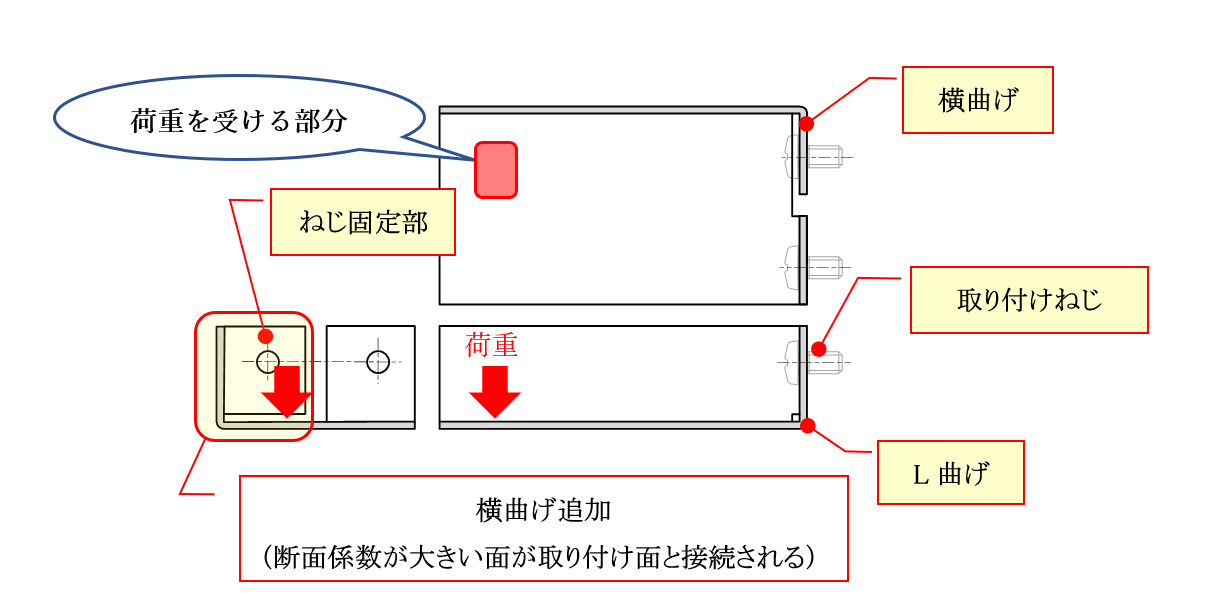
図2-6 断面係数を意識して剛性アップした形状例
その他の類似形状で、断面係数をあげつつ、荷重を固定面側に逃がす構造例を紹介します(図2-7)。
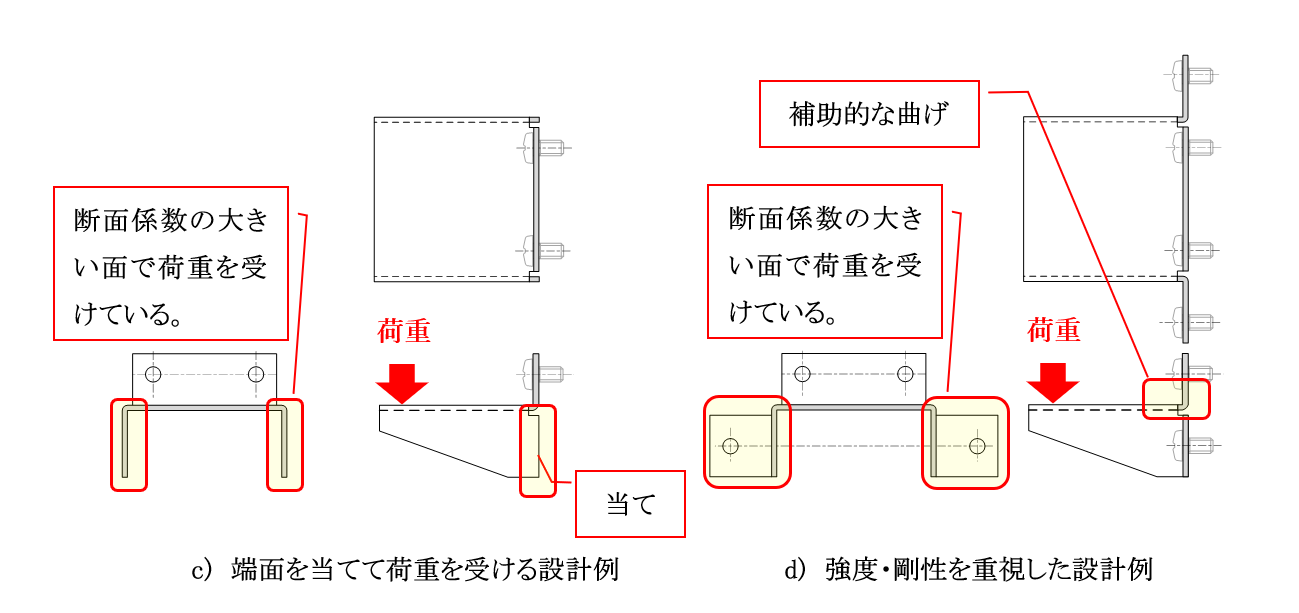
図2-7 荷重に対して剛性を考えた形状設計例
4.展開形状の確認
板金部品を設計する際は、曲がった状態で周辺の部品との取り合いを考えながら機能を満足する形状を設計します。その形状が確定した後に、念のため展開形状を確認する場合があります。
板金展開のイメージを示します(図2-8)。
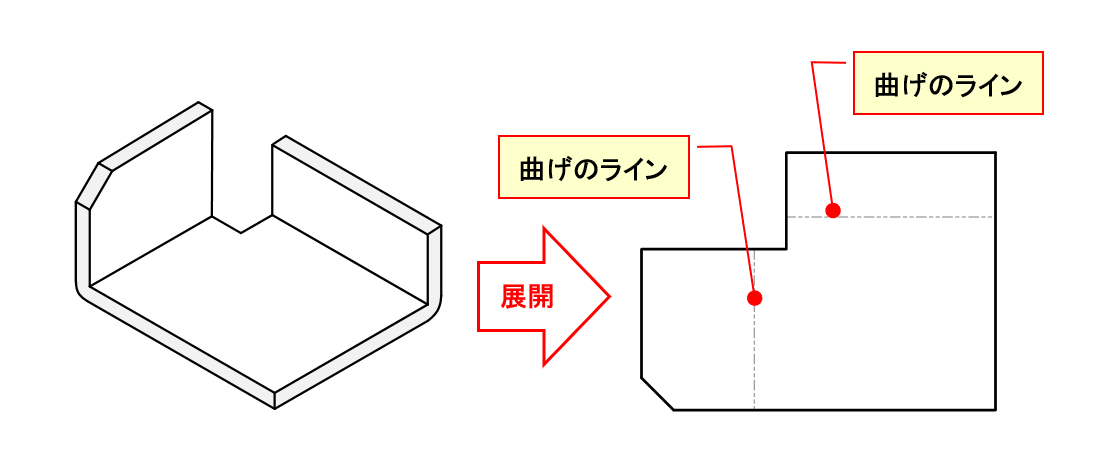
図2-8 板金展開形状のイメージ
①溝ができた際の溝幅寸法の考慮
例えば、曲げ部が互いに交差するような形状では、展開した際に溝ができる場合があります(図2-9)。
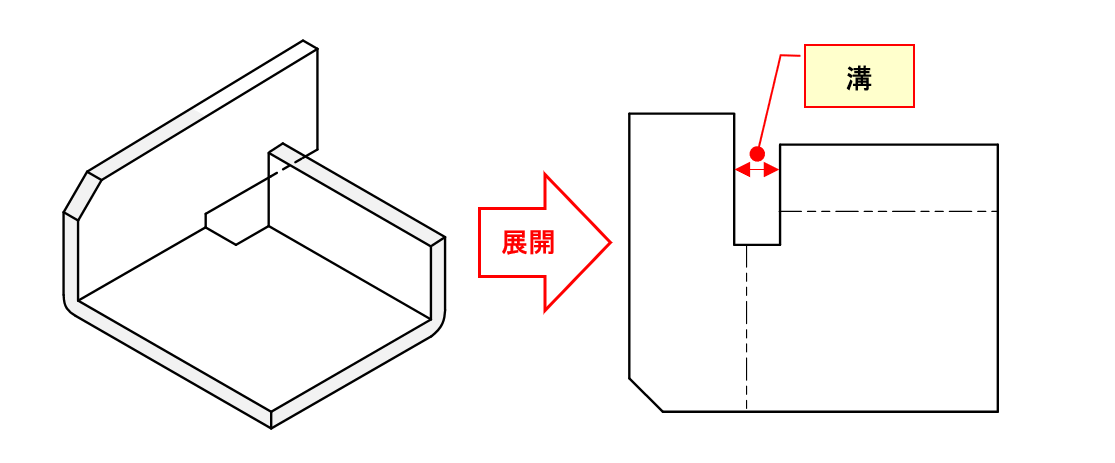
図2-9 曲げが交差する板金部品の展開形状の例
レーザー加工する場合、この溝は0mm以上の任意の数値であれば加工することができます。
しかし工場が所有する標準パンチで打抜く際には、溝幅を標準パンチの幅に合うように設計します。なぜなら標準パンチ1回の抜き(ワンパンチと呼ぶ)で済み、加工時間短縮によるコストダウンが期待できるからです。
②展開時に素材同士が干渉するかどうかの確認
曲げ回数を増して曲げの交差が多くなるほど、展開したときに素材同士が干渉して、ブランクが成り立たないという状況が発生します。板金製の受け皿の例で確認しましょう(図2-10)。
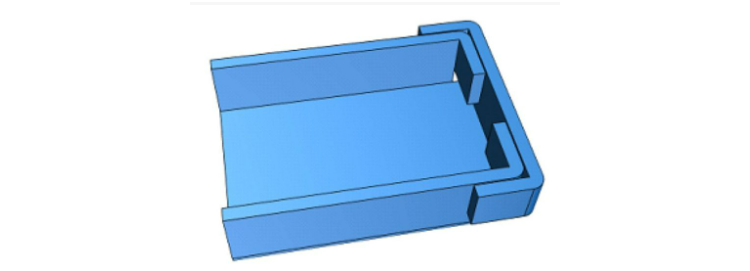
板金受け皿の3Dモデル図
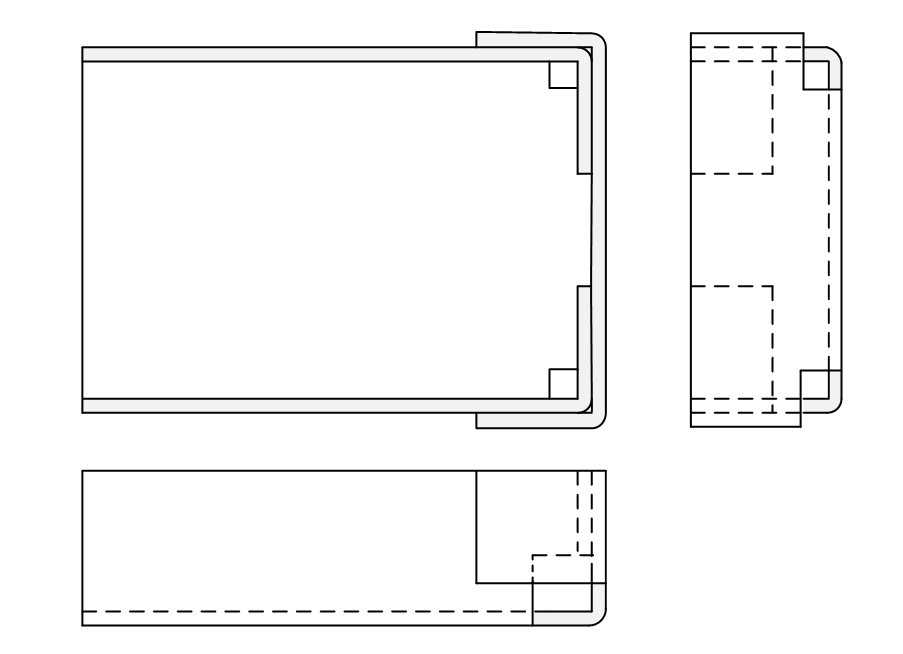
板金製受け皿の2次元図面
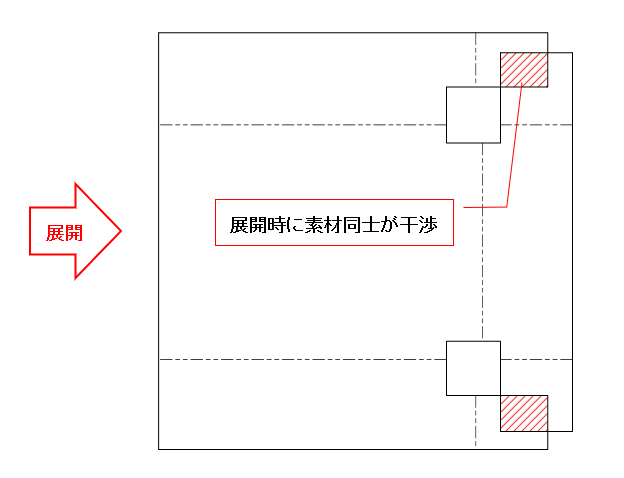
板金製受け皿の展開図
図2-10 展開時に素材同士が干渉する例
このように、展開形状の確認は、パンチで打抜く回数を減らすことや展開形状の干渉問題の両方を確認することが要求されます。
5.打抜きによるダレ面とカエリ面の注意
板金部品は素材をシャーやパンチで打抜く工程になり、その切断面には“ダレ”と“カエリ(バリとも呼ぶ)”が生じます。パンチの抜き方向によって、ダレ面とカエリ面が決まります。特に手が触れる可能性のあるカエリ面では、切り傷などの怪我のリスクが生じます。
また、配線が接触する可能性のあるカエリ面では配線の被覆破れによるショートのリスクが生じます。
リスクのある部分がカエリ面にならないように図面で指示しなければいけません(図2-11)。
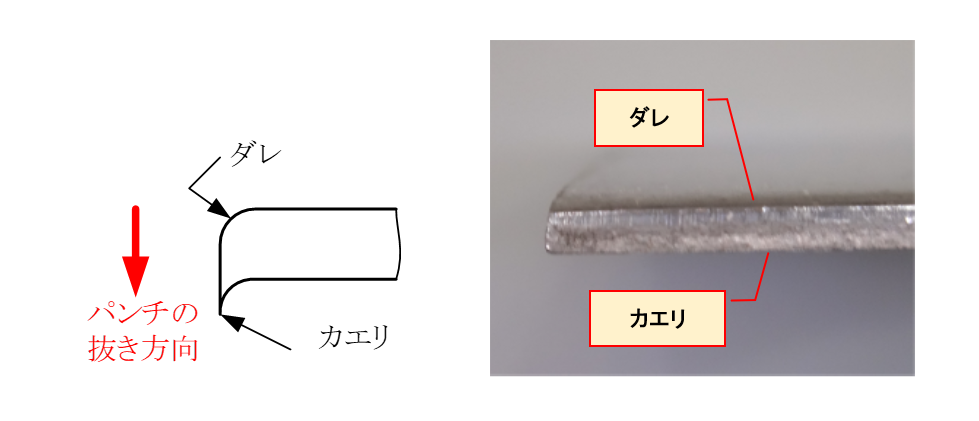
図2-11 ダレとカエリ
パンチで板金を打抜くイメージを動画で確認しましょう。
【パンチング】丸穴を打ち抜くよ!
JIS製図のルールにダレ面やカエリ面を指示する記号は存在しません。抜き方向を「ダレ面」や「カエリ面」など注記によって明示するか、カエリがあってはいけない部分を指定して「糸面取りのこと(C0.1~0.3)」のように注記として指示します(図2-12)。
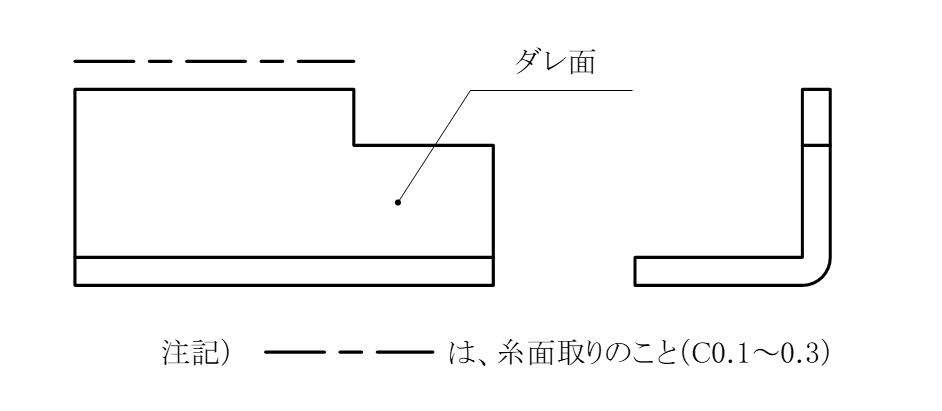
図2-12 図面指示例
~コーヒーブレイク~ 製品を使用する業界にもよりますが、通常操作の流れの中で偶発的に女性のストッキングが板金の端面に引っかかって破れたり、爪のマニキュアが板金のエッジに当たって剥がれたりするとクレームにつながることがあります。 板金部品は切削部品以上に安全性に関する仮説検証を徹底しなければいけません。 |
6.まとめ
板金は切削部品に比べて剛性や寸法精度で劣りますが、板金を使う目的は部品のコストダウンです。
板金設計は、CADで形状を作るだけでなく次の事項に注意しながら設計しなければいけない繊細なものであり、逆にそれが板金設計の醍醐味でもあります。
・その部品に掛かる荷重の方向を把握し断面係数を大きくするように工夫する ・荷重による応力集中がかかる場所を把握し、応力緩和の手段を考慮する ・展開形状を確認し、標準パンチのサイズの考慮や素材同士の干渉を確認する ・手や配線が接触する可能性を推測し、該当部のエッジをなくし、ダレ面・カエリ面を図面に明記する |
次回は、板金に他の部品を接合する技術と図面指示について解説します。
meviy 2D|PDF図面アップロードで簡単操作
かんたん見積もりはこちらから >