生産設備や装置の設計者さん向けに、“タメになる”部品設計の秘訣について、製造現場目線で情報を共有させていただくシリーズの第7回です。
今回は、現在の切削加工技術の中で、最新とも言える「5軸加工」についてご紹介していきます。機械部品の設計や製造をしている人であれば、1度は耳にしたことがあるのではないでしょうか。
5軸加工とは、5軸加工に対応したマシニングセンタによる切削加工を意味します。このようなマシニングセンタは、通称「5軸加工機」とか「5軸マシニングセンタ」とも呼ばれます。
通常のマシニングセンタはX、Y、Zの3軸にしか動きませんので、「3軸加工機」とも呼ばれます。それに対し5軸加工は、3軸加工機だと手間取る段取り替えを省略して工程短縮ができたり、3軸加工機にはできない加工ができたり、といったメリットがあります。
目次
1. 3軸加工機と5軸加工機の違い
それでは、3軸加工機と5軸加工機はどこがどのように違うのでしょうか。まずは、構造的な所から見ていきましょう。
図1-1が3軸加工機と5軸加工機の内部エリアの外観です。3軸加工機は、今までもご紹介してきたように、ワークを固定するテーブルと主軸から構成されます。
テーブルに対して、主軸が左右方向(X軸)、前後方向(Y軸)、上下方向(Z軸)の3軸方向に動くことができます。主軸にエンドミルが取り付けられ、回転しながら3軸方向に自由に動いてワークを削っていくわけです。これにより、3次元加工も含めた様々な形状を実現できることは既にご説明した通りです。
・ 3次元加工については、第4回 3次元加工の世界へようこそ!をご参照ください。
5軸加工機は、X、Y、Zの3軸に回転の2軸を加えた機構になります。
図1-1は典型的なクレードル型の5軸加工機の構成です。テーブルをX軸回りの回転(A軸)と、Z軸回りの回転(C軸)の2軸回転方向に自由に傾斜させることができます。A軸を回転する機構が、ゆりかごのように動くことから、ゆりかご=クレードルと呼ばれています。
他にも1軸回転の機能を主軸側に付けたり、主軸に2軸回転を付加したりする(いわゆる5面加工機)のようなケースもあります。
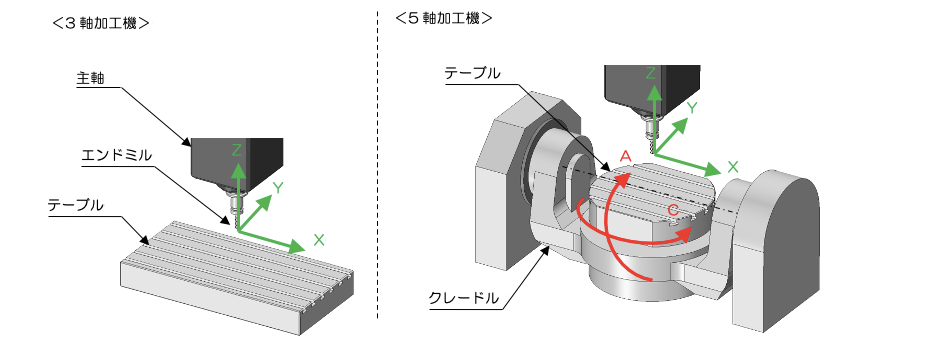
図1-1 3軸加工機と5軸加工機の外観比較
5軸加工機は、このような機構を備えていることで、実際にどのような動きができるのでしょうか?具体的な動作を見てみましょう。図1-2をご覧ください。
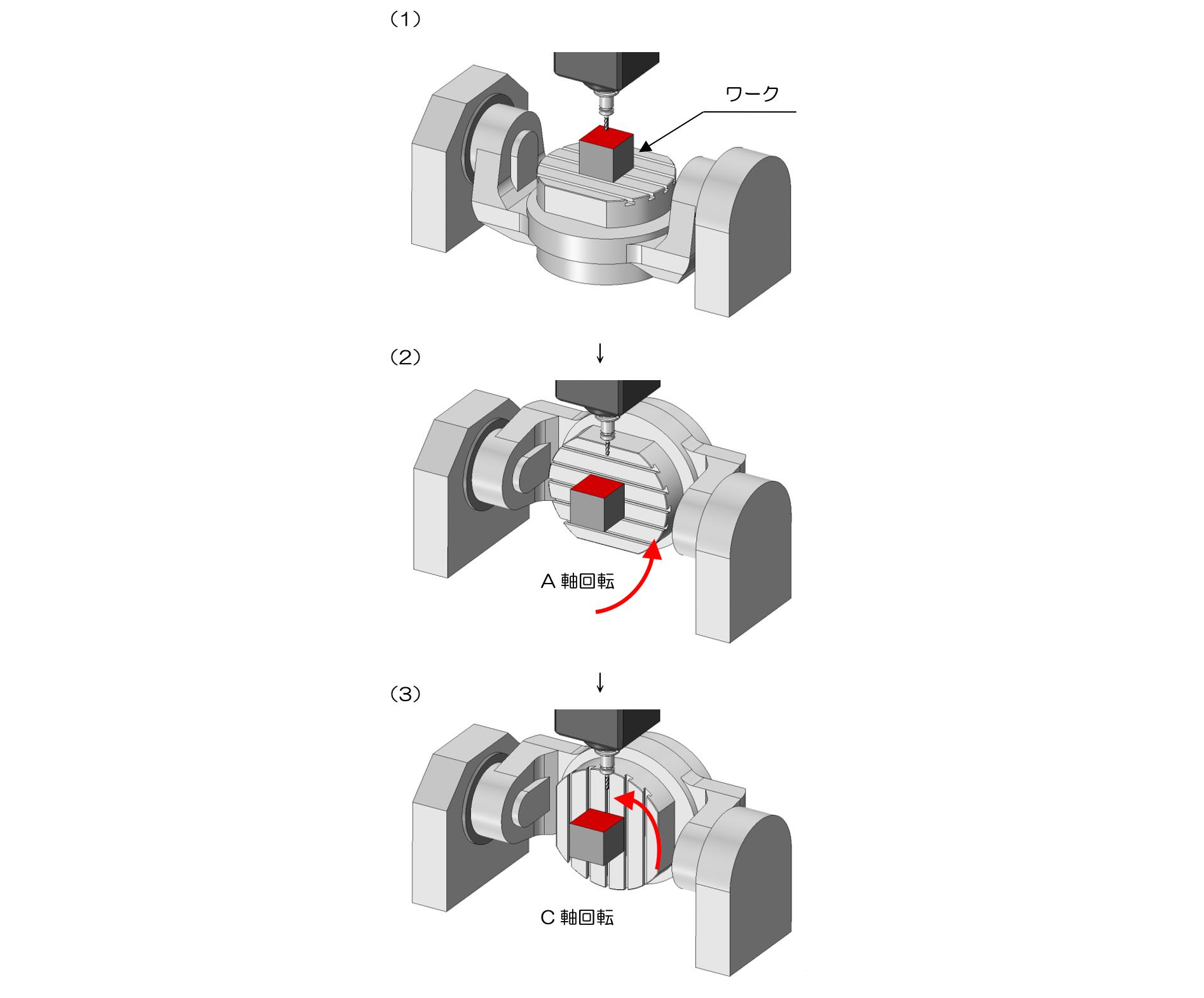
図1-2 5軸加工機の動作イメージ
まず(1)のように、テーブルにそのままワークを載せて加工すると、上面側が主軸と正対しますね。ちょうど赤く塗られた面が削れる範囲です。
そして、そのままA軸を90度傾けると(2)の状態となります。(1)の状態だと削れなかった面が、主軸と正対して削れるようになりますね。
さらに、C軸を90度傾けると(3)の状態となり、次の面を加工できます。そして、そのままC軸を回転させ続ければ、次々と他の面を加工することができるわけです。
つまり、一度ワークを取り付けさえすれば、そのまま底面以外の全ての面の加工をすることができるのです。これにより、段取り替えを省略し、工程短縮による加工時間短縮と加工精度の向上が期待できます。
もちろん、5軸加工機で回転できるのは図1-2のような90度刻みだけではありません。A軸もC軸も自由な角度に設定できますし、A軸・C軸個別に回転させることが可能です。さらにA軸、C軸とX、Y、Zの5各軸全てを、ダイナミックに同時に動かすことができるのです。
通常の5軸加工機の使い方は、A軸やC軸をある角度に傾けて加工→次の角度に傾けて加工という感じで、主軸を動かしているときは回転軸を止めておきます。このような加工の仕方を、「固定5軸加工」「割り出し5軸加工」などと呼びます。
これに対して、回転軸も含めて全ての軸を同時に動かす加工方法を「同時5軸加工」と呼んでいます。いわゆるインペラなどは、同時5軸加工でないと加工できない形状です。
また、5軸加工機の中には、C軸が高速で回転し、まるで旋盤のように旋削加工ができる機能を備えた機種もあります。
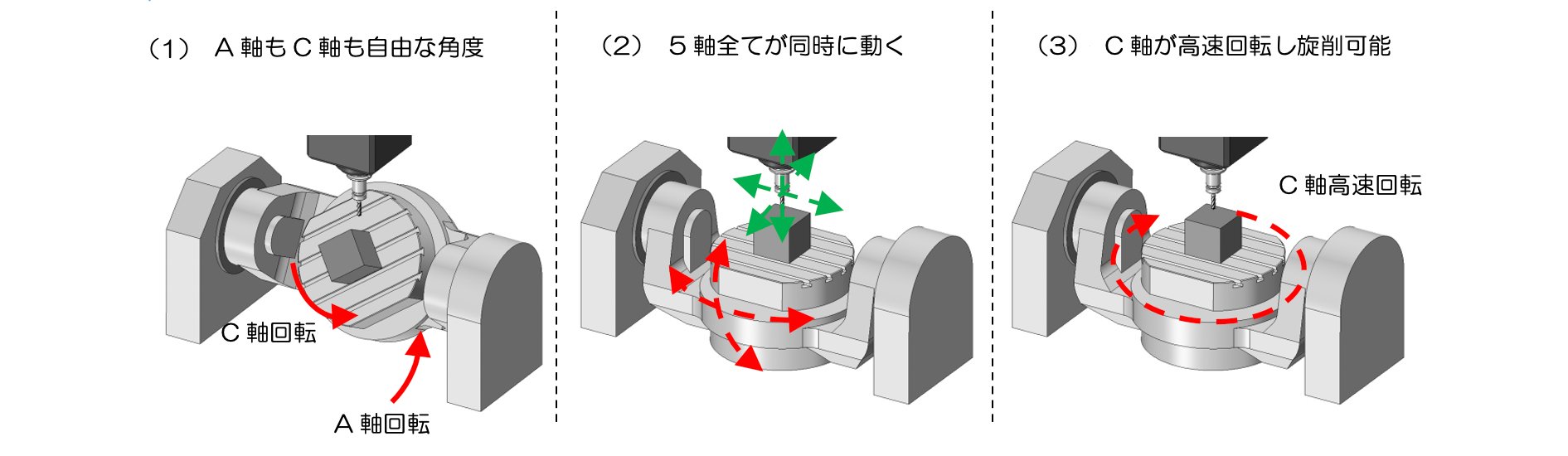
図1-3 5軸加工機の特徴
2. 5軸加工の効果を実感してみよう!
さて、せっかくですので5軸加工の威力を感じていただくために、サンプルの部品を例にとって、5軸加工の疑似体験をしてみましょう。そうです。あの“ブロック”にもう一度登場してもらうとしましょう!
久しぶりの登場となりますが、図2-1、2-2のようなブロックを5軸加工で製作したらどうなるか、一緒に体験してみましょう。
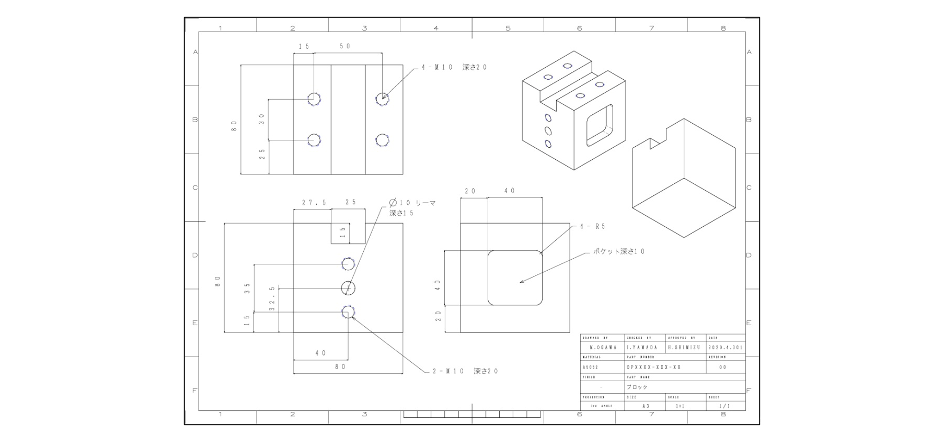
図2-1 ブロック図面
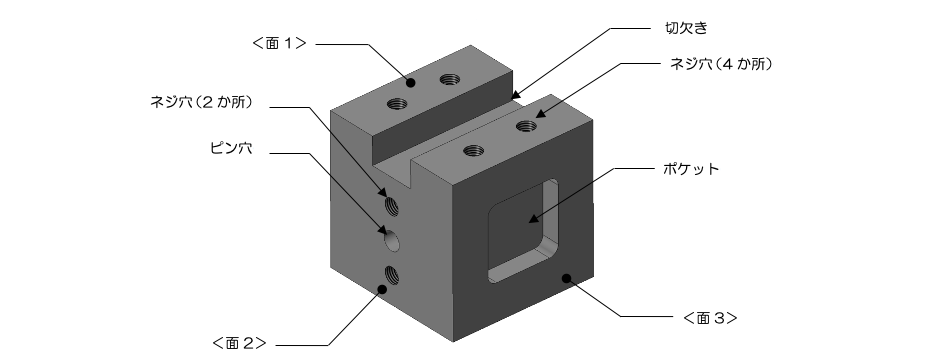
図2-2 ブロック概要
本ブログの第2回と第3回で、3軸加工機でこのブロックを加工する工程をご紹介しました。
第2回 切削加工を疑似体験してみよう!(前編)
第3回 切削加工を疑似体験してみよう!(後編)
3面の加工をするために、1つの面の加工が終わると次の面にひっくり返して、段取り替えして加工して、またひっくり返してと、とても大変な加工であったことを思い出していただけましたでしょうか。何せ、やむを得ず記事を2回に分けたくらい大変なことなのです。
3軸加工機での加工を簡単に表現すればこの通りです。
- 面1の加工段取り
- 面1の加工(切欠き、ネジ穴)
- 面2の加工段取り
- 面2の加工(ネジ穴、ピン穴)
- 面3の加工段取り
- 面3の加工(ポケット)
それぞれの面の、加工の前に必ず段取り作業が発生します。この段取り作業には、ワークの並行出しや、原点設定など、職人技の必要な慎重な作業が含まれます。段取り作業が増えるほど、加工時間も増えますし、作業の誤差によって寸法精度が悪化します。
一方で、5軸加工機での加工はどうでしょうか?図2-1をご覧ください。
まずは、5軸加工機のテーブルにマシンバイスを取り付けます。5軸加工機の場合は、このように嵩上げするようなバイスでワークを固定することが多いですね。理由は、C軸を傾けたときにテーブルと主軸が干渉しないためです。
マシンバイスの平行出しや原点出しを行い、ワークを固定します。そしてワークの原点を設定し、刃物を取り付けて加工データを作成します。ここまでで段取り作業は完了です。
そして加工に入ります。面1を加工したらA軸をグルっと回して面2の加工、そしてC軸をグルっと回して面3の加工で完了です。この間、一度もワークを取り外して段取り替えをする必要がありません。一貫して加工を継続できるわけですね。
工程を表現すると、次の通りです。
- 加工段取り
- 面1の加工
- A軸回転→面2の加工
- C軸回転→面3の加工
このように、5軸加工機による加工では、加工段取りを省略することが可能なのです。
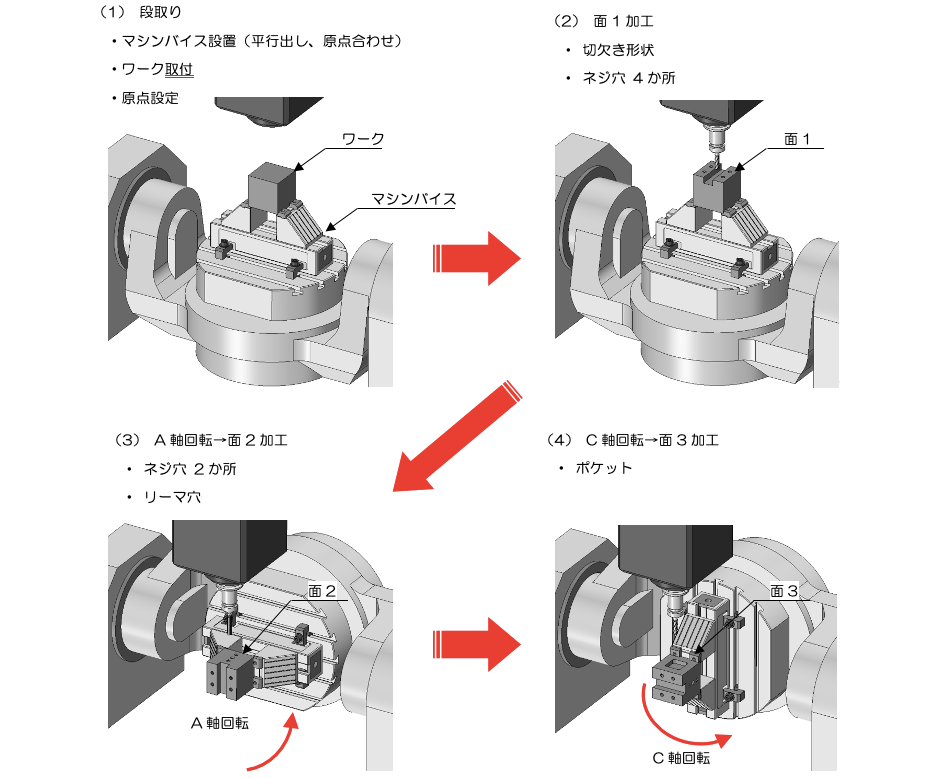
図2-3 ブロックの5軸加工
3. 5軸加工のメリットとは?
5軸加工の威力は、段取り替えを省略できることだけではありません、細かく傾きを制御できますので、様々な角度からワークにアクセスできるというメリットがあります。
いくつか5軸加工のメリットとされることをご紹介していきましょう。
3-1 5軸加工で多面加工の工数とコストを削減
5軸加工の利点は、6面体を単に段取りを省略しながら加工できることだけではありません。色々な角度から加工しないとできないような複雑な形状を加工できることは、非常に大きな威力を発揮します。3軸加工では傾きごとに専用の治具を製作する必要があるなど、膨大な手間がかかり現実的ではありません。
5軸加工では自在に角度や向きを制御できますので、専用治具なども不要です。これにより、初期製品の製作工数とコストを大幅に削減できる可能性があります。
例えば3-1のようなブロックの加工を考えてみましょう。傾斜した面に対して、面直に開けられたポケット形状があります。
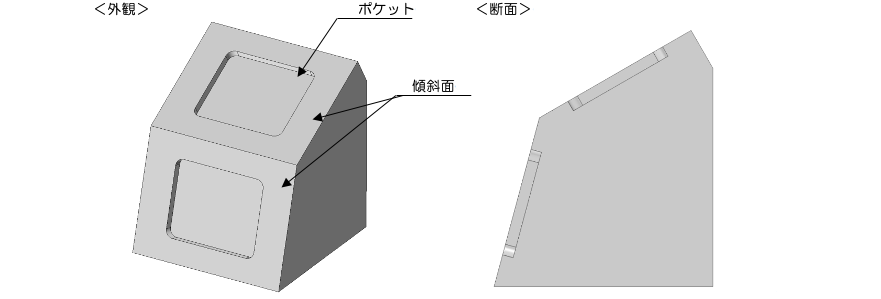
図3-1 傾斜ブロック
通常の3軸加工機でこのような傾斜面を加工するには、傾斜面を主軸に対して正対させる必要がありますので、工夫が必要となります。1つは傾斜機能付きバイスなどの道具を活用する方法、もう1つは専用治具を作る方法が考えられます。
傾斜機能付きバイスは、例えば図3-2のようなものを使います。3軸加工機上で、このようなバイスでワークを固定して、加工したい角度に調整するわけですね。手間もかかりますし、アナログ的な作業となりますので加工精度も悪化します。
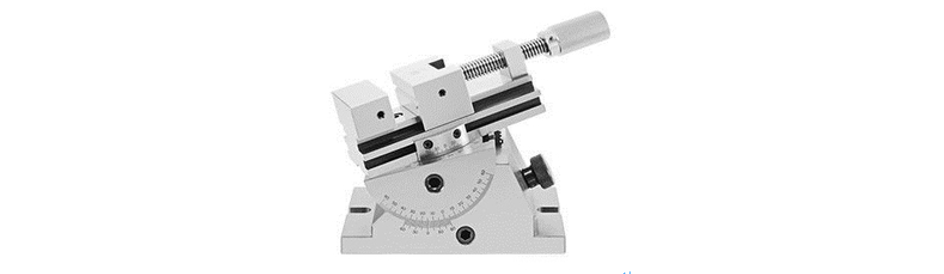
図3-2 傾斜機能付きバイスの例
(TDP120:ミスミ参考サイト)
専用治具は、例えば図3-3のようなモノですね。
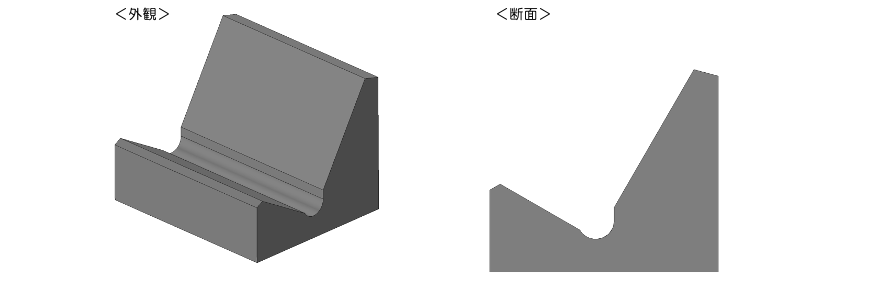
図3-3 傾斜ブロック用治具のイメージ
このような治具を製作してワークの下に挟むことで、3軸加工機でもワークの傾きを変えて固定することができます。例えば図3-4のように固定するイメージですね。これで何とか3軸加工機で傾斜面のポケットを加工することができます。当然、この場合はもう1つの傾斜面のポケットにも、個別の専用治具が必要になります。
かなりの手間と労力がかかることがご想像いただけるのではないでしょうか。
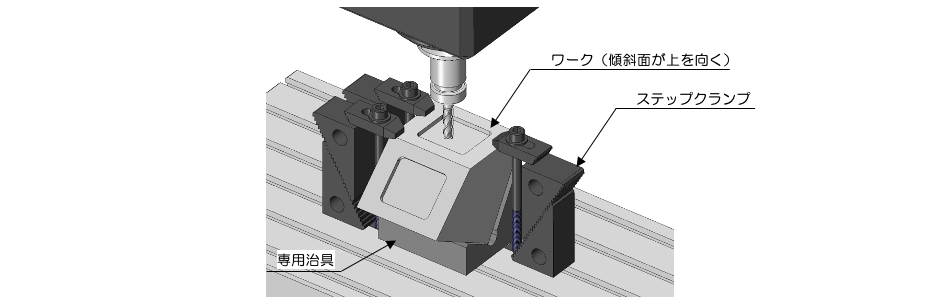
図3-4 傾斜ブロックによる加工イメージ
5軸加工機であれば、このような手間は必要ありませんね。テーブルにワークを固定して、A軸とC軸を機械上で回転させれば、即座に加工が可能となります。
3-2 5軸加工は刃物を斜めから当てられる
5軸加工では、あまりクローズアップされませんが、ワークを傾けた状態で刃物を当てることにより得られるメリットがあります。ひとつは、状況によって、刃物の突き出し量を短くできる可能性があることです。もうひとつは、ボールエンドミルの先端以外でもワークを削れることです。
突き出し量は、刃物の先端からホルダ端面までの距離ですね。刃物の直径(D)と突き出し量(L)との関係でL/D≦5とすべき、という説明を以前させていただきました。突き出し量が長すぎると刃物の振れが大きくなり、加工精度が悪化したり切削後の表面がガサガサとむしれたような汚い仕上がりになったりします。
例えば、図3-5のような部品(L型ブロック)を加工する場合を考えてみましょう。
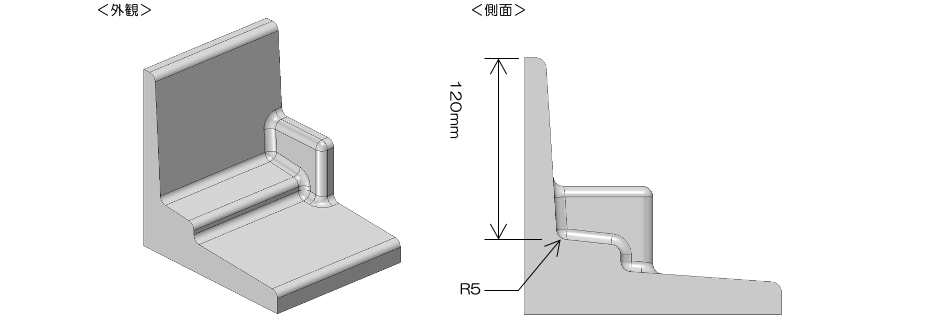
図3-5 L型ブロック
このL型ブロックは、内側までの深さが120mmありますが、その隅アールはR5です。これを3軸加工機で加工しようとすると、図3-6(1)のような状況になりますね。
隅アールがR5なので、使用するエンドミルはΦ10のボールエンドミルです。そして、立壁とホルダが干渉しないようにボールエンドミルの突き出し量を長くしなければいけません。最低でも120mmは突き出し量が必要になりますね。
この場合、突き出し量(L)120mm ÷ 刃物直径(D)10mm = 12.0となります。本来L/D≦5とすべきところに対して、突き出し量が大きすぎるということですね。このまま削ってしまうと、全体的にガサガサとした表面になったり、場合によっては加工中に刃物が折損してワークを損傷させたりしてしまうかもしれません。
5軸加工機で加工する場合は、ワークを都合の良い角度に傾けることができますので、図3-6(2)のようにホルダが干渉する心配なく、突き出し量を小さくすることができます。
これにより、3軸加工では加工できない形状を作り出すことができます。あるいは、突き出し量を小さくすることで、表面をきれいに仕上げることができるようになります。
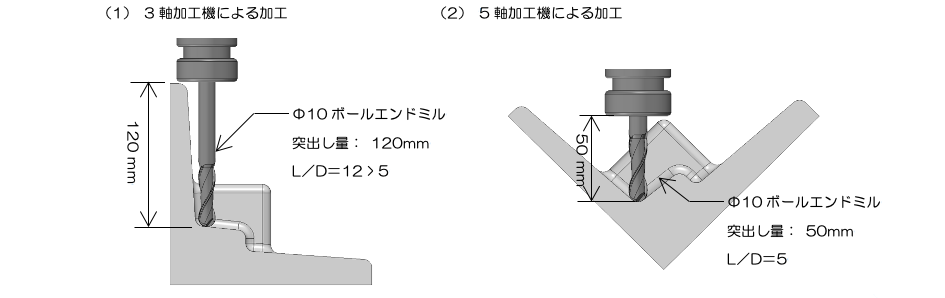
図3-6 L型ブロックの加工方法比較
また、ボールエンドミルの先端は回転速度がゼロです。つまり、回転中心付近は本来は切削する力がほとんどないのです。それを無理やりワークに押し付けて削っていくわけですね。5軸加工によってワークを傾けてエンドミルを当てると、この回転速度ゼロの部分をワークに当てずに済みます。
つまり、切削力のある部分でワークを削れるため、表面をきれいに仕上げることができるというメリットもあるのです。
4. 同時5軸加工って何ができるの?
5軸加工機の真骨頂は、X、Y、Zの3軸とA、Cの回転2軸を同期させて、同時に制御しながら動かせる「同時5軸加工」ができることです。
そもそも加工機やCAMが同時5軸加工に対応していなければいけませんし、加工データの作成も非常に難易度が高い加工です。テーブルも主軸もダイナミックに動きますので、少しでも設定に見逃しがあると主軸とテーブルとの衝突がすぐに起こってしまいます。
固定5軸加工にはない、高度なノウハウが必要になります。同時5軸加工までを使いこなしている加工業者は、日本でもごく限られていると思います。同時5軸加工に興味がある方は、是非インターネットなどで動画などをご覧になってください。
同時5軸加工の1番のメリットは、「インペラ」に代表されるような、アンダーカットだらけの複雑形状を削り出せることでしょう。図4-1のような部品が典型例ですね。
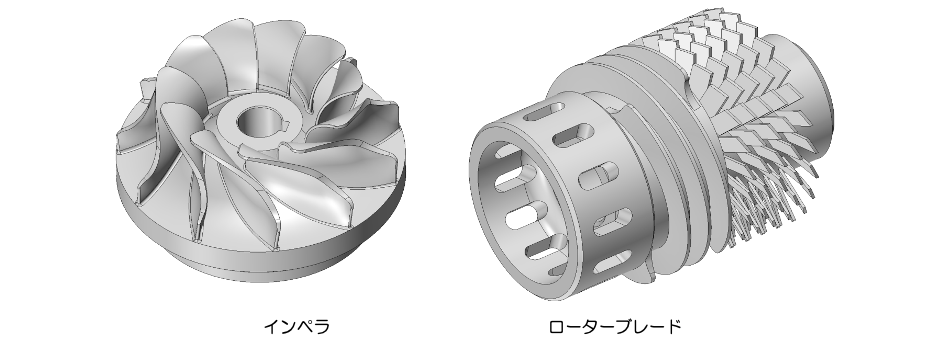
図4-1 5軸加工の部品例
固定5軸加工では、ある傾斜でテーブルを止めて加工し、また次の傾斜でテーブルを止めて加工……といちいちテーブルの傾斜を固定する必要があります。インペラのような複雑な形状も、何度も傾斜を変えながら加工できなくはないのですが、とんでもない労力が必要になるのは想像がつくのではないでしょうか。
それに対して、同時5軸加工ではテーブルを主軸の動きに同期させながら、連続的に傾斜させて加工ができます。エンドミルが入る隙間さえあれば、ワークをうまく避けながらテーブルを止めることなく一続きの加工ができるのです。
このような複雑形状の加工で同時5軸加工が本領を発揮するということを是非覚えておいてください!
5. 5軸加工の注意点
さて、何でも加工できる万能な5軸加工ですが、その機構から注意が必要な点がいくつかあります。
5-1 粗加工・重切削に向いていない
ご覧いただいた通り、5軸加工機には通常の3軸加工機と比べると、2軸回転するための機構が追加されています。つまり機械の構造が複雑になり、一般的には3軸加工機よりも剛性が低いと言われます。
特に5軸加工機を使用するような複雑形状の部品、例えば航空機部品などは、軽量化のために薄肉構造になっていることも多いですね。材料の90%以上は削りカスになってしまうような部品も多いと思います。
切削加工の基本は、ボリュームを削る粗加工と表面を精度よく仕上げる仕上げ加工です。粗加工では、できるだけ大きな刃物で大きな切込み量でゴリゴリ削ります。このような加工は切削時の抵抗も大きく、「重切削」とも呼ばれます。
しかし、5軸加工機は構造的に“華奢”なので重切削に向きません。例えば、抵抗の大きなステンレスなどを5軸加工機で重切削しようとすると、加工機自体がグワングワンと振動してワークにも悪影響を与えかねません。
必然的に、小さい刃物で抵抗が少なくなるような、やさしい加工を心掛けなければいけないわけです。粗加工では精度を気にせず早く済ませたいのに、加工機の振動を気にしてゆっくり加工することになってしまうわけですね。
つまり、粗加工は3軸加工機で重切削を行い、5軸加工機に移し替えて仕上げ加工や5軸加工でなければ加工できない部分を削る、という使い分けが重要となるケースが多いのです。
加工現場がきちんと3軸加工機と5軸加工機を使い分けられれば良いのですが、5軸加工機しかないような現場だと、本来向いていない重切削を5軸加工機で行わざるを得ない、などという事態になりかねません。
5-2 必ずしも加工精度が高いわけではない
先ほど、5軸加工機では段取り替えが省略できるので、加工精度を向上させやすいという説明をしました。ただし、5軸加工機での加工がそもそも高い精度かというと、そうとも言えない要素もあります。5軸加工機ではテーブルが回転するため、最初の段取りの際に誤差が増幅されてしまうケースがあります。
例えば、図5-1のように同軸のザグリが重要なブロックを加工するとしましょう。貫通穴の両端に、ザグリ加工が入ります。この部品の機能上、このザグリ加工の同軸度が重要だとしましょう。
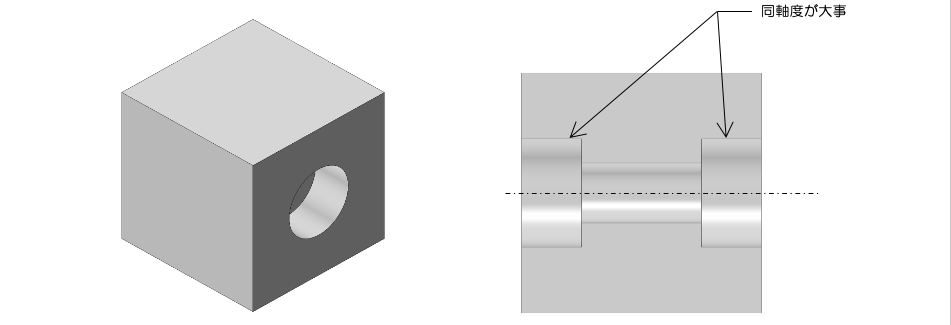
図5-1 同軸穴ブロック
5軸加工機で、ザグリ穴部分を図5-2のように加工したとしましょう。ここで(1)のようにワークを固定する際に、テーブルの回転中心とワークの加工原点がずれていたとします。ずれの量はDとしておきましょう。
片側のザグリ穴を加工した後に、テーブルをC軸周りに180度回転させて逆側のザグリを加工しようとすると、ズレ量が2倍(つまり2D)の位置に加工してしまうことになります。これに気付かずに加工を進めてしまうと、同軸度が重要なはずなのに大きく同軸度がずれた加工をしてしまいますね。
このように、テーブルを回転することで誤差が増幅する可能性については、常に気を付けていなければいけないわけです。
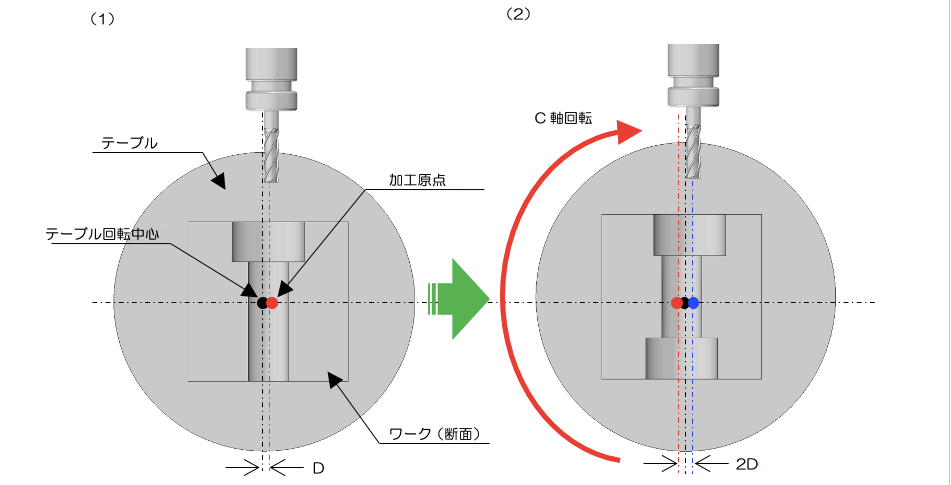
図5-2 加工のズレのイメージ
5-3 ワークサイズが制限される
5軸加工機は、3軸加工機と比べると2軸付加された分だけ構造が複雑です。同じサイズの加工機では、どうしても5軸加工機の方がテーブルの大きさが圧迫されがちですね。
つまり、5軸加工で扱えるワークの大きさは、3軸加工機と比べると制限されてしまいます。機械の大きさからすると、意外と小さいモノしか扱えない印象を受けるのではないでしょうか。大きなワークまで対応できる加工機を持っている加工業者も限られますね。
このように、5軸加工機ではワークサイズが制限されがちだということを覚えておきましょう。
5-4 加工単価が高い
5軸加工機は、3軸加工機と比べると購入費用が高いのは事実です。さらに5軸加工に対応したNCデータを作成するためのアプリケーション(CAM)も、新しく導入するとか、5軸加工用にカスタムする必要があります。
その分、加工単価も割高になるということを覚えておいた方が良いと思います。
5-5 1面は別工程での加工が必要
お気づきいただけたと思いますが、5軸加工は6面全てを加工できるわけではありませんね。固定する際の底面になる面は加工できません。したがって、基本的には5軸加工に入る前に、底面を別工程で加工する必要があるわけです。
5軸加工機にワークをどのように固定するか、工夫が必要なケースも少なくありません。今回ご紹介したマシンバイス以外にも、専用治具が必要なケースなどもあります。
固定の精度によって加工精度も大きく変動しますので、5軸加工に載せる前の下準備が大切となります。
6. 5軸加工のメリットとデメリット
今回は現在における切削加工の最新技術である5軸加工についてご紹介しました。5軸加工についてのメリットとデメリットをまとめてみましょう。
<メリット>
- 段取り回数を省略でき、工程短縮によるコストダウン、加工精度向上が見込まれる
- 刃物の突き出し量を短くしたり、回転中心以外で削れるため表面をきれいに仕上げたりすることができる
- 刃物の突き出し量を短くすることでしかできない形状を実現できる
- インペラなど同時5軸加工でしか削れない製品を実現できる
<デメリット>
- 構造上、重切削に向いていない(場合により3軸加工機との併用が必要)
- 加工機の大きさに対して、取り扱えるワークサイズが小さい
- 必ずしも加工精度が良いわけではない
- 加工賃は割高となる
- 必ず1面は加工できない部分があるため別工程での加工が必要
5軸加工を意識した設計も良いと思いますが、是非これらのメリットとデメリットを考えたうえで設計に反映していただけると良いと思います。
5軸加工機は1台で全ての工程を効率的にできる万能加工機でも、3軸加工機の完全上位互換機でもありません。5軸加工機特有の課題もあることをご理解いただき、適切な距離感で上手にご利用いただければと思います。