生産設備や装置の設計者さん向けに、“タメになる”部品設計の秘訣について、製造現場目線で情報を共有させていただくシリーズの第4回です。
第3回では、切削加工につきものの「隅アール」についてご説明しました。
「回転する刃物で削った場合にどうなるか」を考えて、隅アールを設計に盛り込む事が大切だという事をご理解いただけたと思います。
目次
1.3次元加工とは?
今回は、切削加工を使って実現できる形状のうち、「3次元形状」についてご紹介したいと思います。
機械部品のカタチは基本的には、「形状」と「穴」から成り立っています。
形状は、平面や円筒面等の数学的な「幾何形状」と、計算式では表せないような「自由曲面形状」に分かれます。
あるいは、「平面的」な形状と、高さ方向に変化する「立体的」な形状という分け方もできます。
穴も、「キリ穴」、「リーマ穴(公差穴)」、「ネジ穴」、「ザグリ穴」など機能によって分けられますね。
機械部品において、穴は色々な機能を持つ重要な要素です。
形状で最もシンプルなのは、サイコロのような6面体ではないでしょうか。
比較的板厚の薄いプレート形状や、肉厚のブロック形状をイメージしてください。
これに穴を開けたり、肉抜きや切欠き加工をしたりといった加工が、最も切削加工で簡単に実現できる部品です。
例えば図1-1のようなベースプレートやブロックなどの形状が典型的ですね。
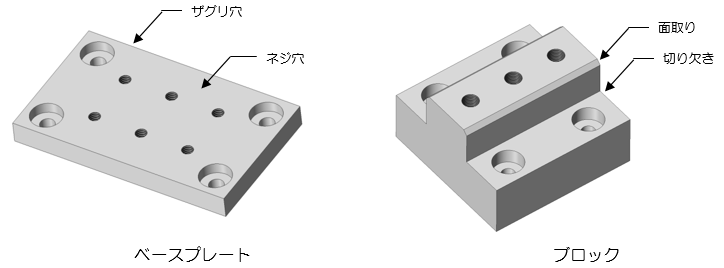
図1-1 機械部品の典型例
切削加工では、このような幾何形状だけではなく、ウネウネと曲がりくねった曲面形状や傾斜面などの立体的な形状も実現する事ができます。
このような立体的な曲面形状を「3次元形状」と呼んでいます。
そして、この3次元形状を切削加工により実現するのが「3次元加工」です。
一方で、プレート状の形状など、上から見て上下面が同じ形状のものは「2次元形状」と呼んでいます。
3次元形状でイメージしやすいのは、図1-2や図1-3のような凹凸を持った形状でしょうか。
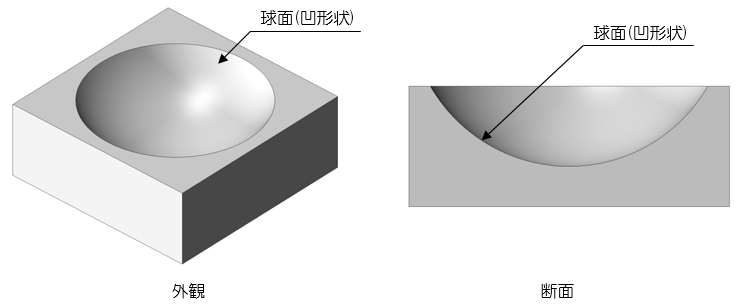
図1-2 3次元形状の例 球面の掘り込み
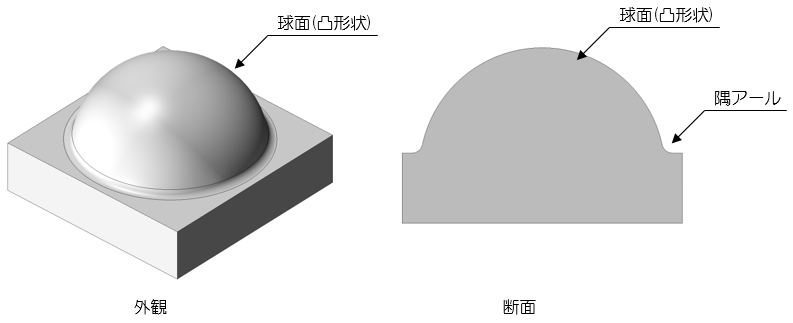
図1-3 3次元形状の例 球面の削り出し
図1-2は球面(凹形状)を彫り込んだ形状で、
図1-3は球面(凸形状)を削り出した形状です。
「削り出す」というのは、切削加工の独特な表現ですね。
不要な部分を“削って”、必要な部分を材料の中から掘り“出す”事で形状を実現するわけですね。
図1-2と1-3のどちらも、高さ方向に対して立体的な形状をしていますので3次元形状と言えます。
また、図1-3の凸形状の付け根部分に、隅アールが付いている点にもご注意ください。
前回説明した「隅アール」がこのようなところにも必要になります。
このような3次元形状は「フラットエンドミル」ではなく、先端が半球状の「ボールエンドミル」で加工します。
このため、「工具が回転する」事によるアール形状がどうしても残ってしまうのです。
つまり、図1-4のように、隅が曲面と平面でピン角になる形状は切削加工では表現できません。
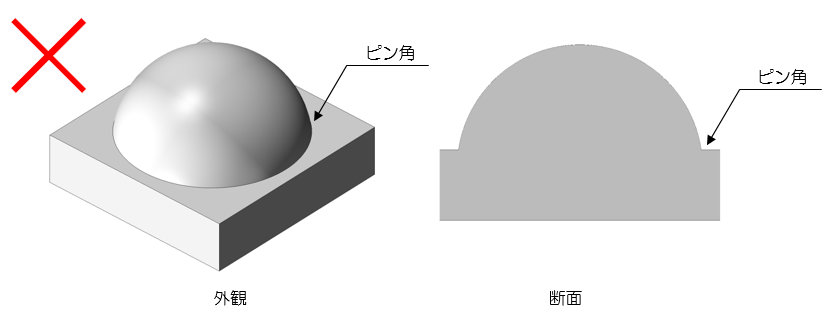
図1-4 削り出し形状NG例
もし、どうしても付け根部分まで3次元形状が必要であれば、図1-5のようにニガシ形状をつけることを考えてください。
ニガシ形状は、稜線に沿って半円状の窪みをつけるのが一般的です。
もちろん、この時にはアールの大きさと刃物の突き出し量との制限「L/D≦5」を意識してください。
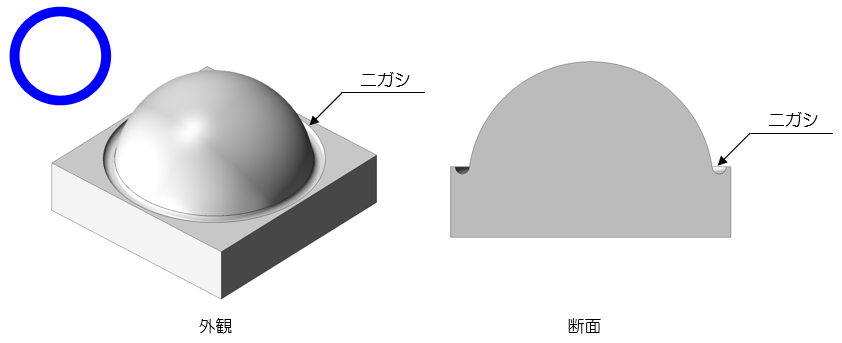
図1-5 ニガシ形状の例1
図1-6のように曲面自体を削ってしまうニガシ形状もOKです。
このようにすればニガシ部分は面と面が直交するため、円筒形状の「フラットエンドミル」で削れます。
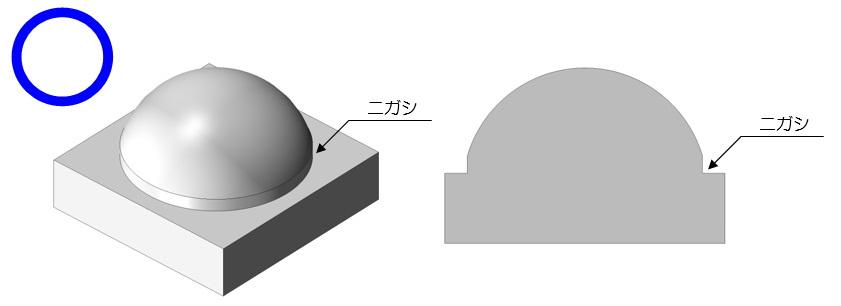
図1-6 ニガシ形状の例2
2.3次元加工はどのような形状に使われるのか?
3次元形状や3次元加工について、もう少し具体的な用途や形状をご紹介しましょう。
曲面などでも自由に表現できる3次元形状は、外観上必要な形状だったり、肉抜きなどの軽量化のために利用されたりします。
製作サイドからすると、曲面形状は加工に時間もかかり、効率的な形状ではありません。
外観や機能上の理由が無ければ、多用は控えるべき要素と言えます。
自動車やバイクなどの試作品などでは、削り出しによる3次元形状の加工は日常的に行われています。
実用上で最も多用されているのが、航空機やレース用の部品でしょうか。
必要な強度や剛性を確保しながら、極限まで軽量化を図る航空機やレース用部品に3次元形状が用いられることが多いようです。
図2-1のような航空機部品などが典型的ですね。
幾何形状と曲面形状がミックスされたような形です。
肉抜きのために形状を薄くしながら、両サイドにリブ形状を残して強度と剛性を確保しています。
更に図2-2のインペラのように全体が3次元的な曲面形状だけでできている部品などもあります。
その他にも、製品の構成部品のうち、強度と外観上の理由から3次元形状を採用する部品は多いようです。
量産品になるとロストワックスなどの鋳造で製作するケースも多いですが、小ロット生産では切削加工の削り出しで外観部品を製作するという選択肢も取られます。
3次元加工を活用した部品の例としては、成型部品の受け治具なども典型的です。
例えば、自動車に多用されるようなプラスチック製の部品は、非常に複雑な3次元形状をしています。
検査や組立用の治具部品としてこれらの3次元形状を反転させた「受け部品」を作るという事にも切削加工は利用されています。
例えば図2-3のような曲面ばかりで構成された成型部品をイメージしてみましょう。
もちろん、このような形状自体を切削加工で製作する事も可能です。
成型部品は基準となる平面や基準点となるポイントが無い場合も多いと思います。
検査や、組立、試験、追加工などの必要がある場合に、この部品を正しい姿勢で固定できるような受け治具が必要になるケースが多いようです。
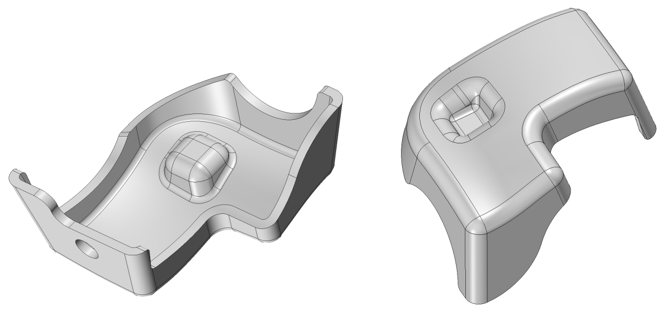
図2-3 成型部品の形状例
このような場合などにも、3次元形状の切削加工は威力を発揮します。
3D CADで受け形状の3Dモデリングさえできれば、成型部品をすっぽりと嵌め込むことのできる治具を製作できるのです。
試しに、受け形状を3Dモデリングしてみたものを図2-4に示します。

図2-4 受け治具の例
もちろんこの受け治具は、元の部品形状を反転させた面を持ちますので、3次元形状となります。
3D CADによる3次元設計と、切削加工による3次元加工は非常に相性の良い組み合わせです。
3D CADで3次元モデルデータを作成し、それを3D CAMに読み込んで、加工データを作り、マシニングセンタ等で加工する、という流れが一般的ですね。
実際にCAD上ではめ合わせてみたものが図2-5です。
断面を見ると、すっぽりと成型部品が嵌り込んでいることがわかると思います。
(実際にはスムーズに嵌るように、多少隙間ができるように設計します)
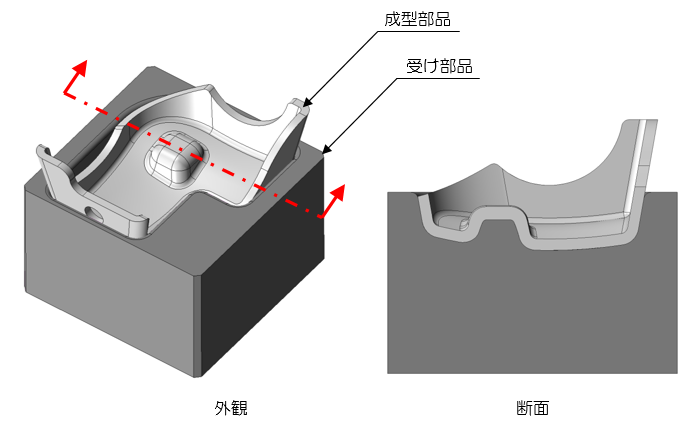
図2-5 受け治具へのはめ込み状態
3次元加工の可能性を色々と感じていただけたのではないでしょうか。
3.3次元加工の仕組みとは?
通常の機械部品は、平面で構成されている事がほとんどだと思います。
これらの平面形状は、基本的には「フラットエンドミル」と呼ばれる刃物で加工されます。
あるいは、広い面を仕上げる際には「フェースミル」(又はフルバック)と呼ばれる刃物を使うケースも多いです。
これらの刃物は、底面や側面を使って刃物が接する面積をまとめて削ることができますので、切削加工でも比較的スピーディな加工です。
一方で、今回ご紹介したような3次元形状を削る刃物は「ボールエンドミル」と呼ばれる先端が半球状の刃物です。
図3-1にスクエアエンドミルとボールエンドミルの形状の違いを示します。
このボールエンドミルを使って、曲面形状の平面に沿いながら削ることで、様々な3次元形状を削り出す事が可能となります。
ただし、「隅アール」が付く事や、L/D≦5の考え方は、他のエンドミルと同様です。
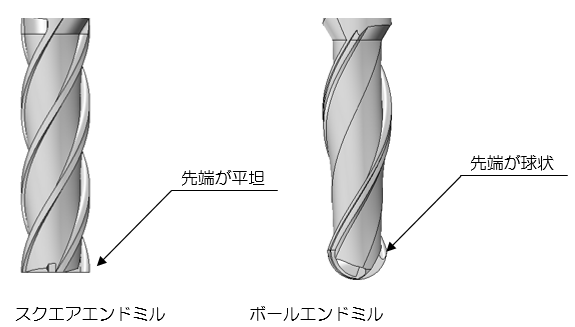
図3-1 エンドミルの形状
それでは、実際に3次元加工はどのように行われるのでしょうか。
基本的に切削加工は、大きく「粗加工」と「仕上げ加工」に分かれます。
太くがっちりとした刃物でスピーディかつ大まかに加工するのが粗加工、細い刃物で面に沿って精細に表面を仕上げていくのが仕上げ加工です。
まず粗加工を行って、最後に仕上げ加工という流れですね。
図1-1の形状を加工する場合を見てみましょう。
粗加工
まず、ブロック状のワークから、フラットエンドミルなど比較的径の大きなエンドミルで、不要な部分を削り、おおよその形を削り出します。
粗加工は、どちらかというと精細さよりも、ボリューム(体積)を除去する事が目的です。
加工時間は、除去する体積によって変動します。
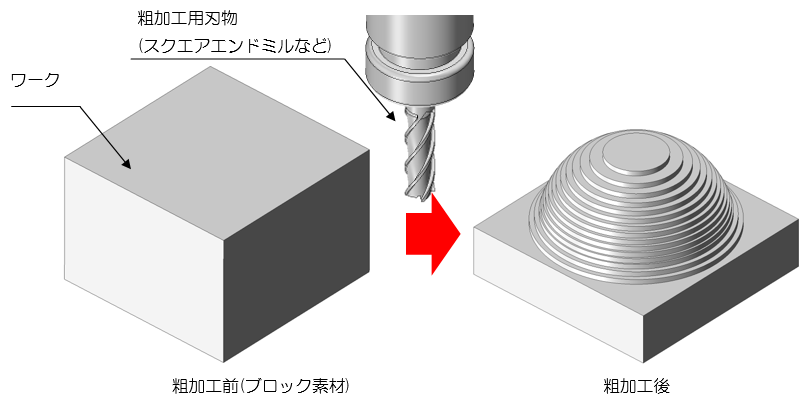
図3-2 粗加工の様子
粗加工後の状態は、図3-3のように粗い階段状の表面になります。
段の大きさは、材質や、大きさなどによって変わりますが、数mm程度のイメージです。
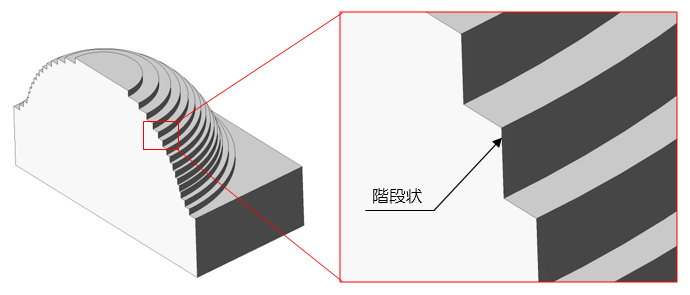
図3-3 粗加工後の状態
仕上げ加工
次に、刃物をボールエンドミルに交換して、仕上げ加工を行います。
仕上げ加工は、粗加工よりも細かい刻み幅(ピッチ)で、表面をなぞるように削ります。
粗加工がボリュームを除去する目的だったのに対して、仕上げ加工は表面を繊細に精度良く仕上げていく事が目的です。
加工時間は、仕上げる面の表面積と、仕上がりの表面粗さ(細かさ)によって変動します。
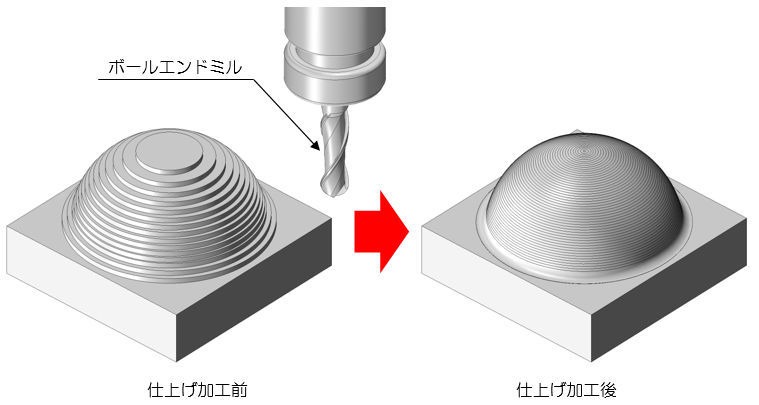
図3-4 仕上げ加工の様子
図3-5が仕上げ加工後の状態です。
先端が円弧状のエンドミルを細かい間隔で削って滑らかにはなっていますが、よく見ると筋目のようなもの(微細な凹凸)が残ります。
このように、一見綺麗な曲面に見えても、厳密には多少の凹凸が残るのが3次元加工の特徴となります。
この凹凸を無くしてツルツルな面にしたい場合は、追加で研磨加工(バフ研磨など)を施す必要があります。
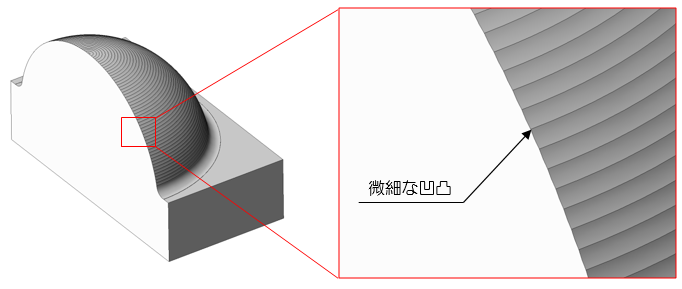
図3-5 仕上げ加工後の状態
4.3次元加工と表面粗さの関係を理解しよう!
以上、ご紹介した通り、3次元加工では厳密には、微細な段差が残ります。
この段差の大きさは、ボールエンドミルの直径と、仕上げる際の削り幅(ピッチ)によって決まります。
つまり、表面粗さと切削加工の条件には、関係があるわけです。
図4-1をご覧ください。
半径RのボールエンドミルをピッチPで削った時に、凹凸の一番高いところと低いところの差をカスプハイト(理論加工面粗さ)と呼びます。
計算式としては、下記の近似式が良く使われるようです。
h = P2 / ( 8 x R )
つまり、加工面粗さは使用するエンドミルの半径が大きく、ピッチが小さいほど小さくなります。
エンドミルの半径は大きければ大きいほど良いのですが、現実的には最小の隅Rの設定により制限されます。
その部品の中で最も小さな隅アールの事を「最小R」などとも呼びます。
エンドミルの大きさ(最小R)が決まって、目標とする面粗さが指定されれば、加工するためのピッチを計算することができます。
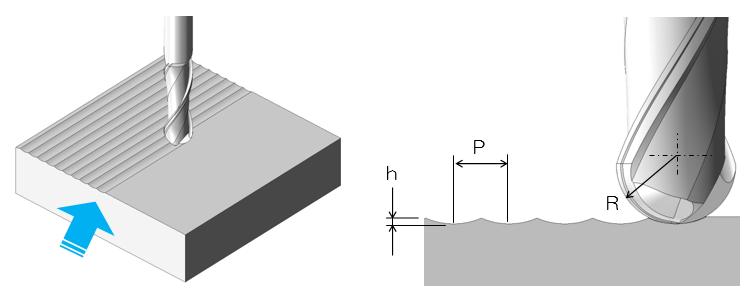
図4-1 カスプハイト
カスプハイト(h)は、理論上の加工面粗さですが、いわゆる最大高さの表面粗さ(Ry)に相当します。
表面粗さの単位はマイクロメートル[μm]となります。
表面粗さについての詳細は、下記のサイトをご参照ください。
ミスミCナビ: https://cp.misumi.jp/tech/tech10.html
部品設計上で用いられる表面粗さ指示は、算術平均粗さ(Ra)が一般的ですね。
あるいは、▽▽等の仕上げ記号で指示される設計者さんも多いと思います。
概ね、Ra=Ry/4(新JIS:Ra=Rz/4)という関係があります。
最小のRが4で、Ra3.2(▽▽相当)の粗さ指示の面を加工する場合には、大まかには次のような加工条件となります。
P = √(8Rh)
P = √(8 x 4 x 3.2 x 4/1000)
P = 0.64mm
つまり、この場合は0.6mm程度のピッチで、表面全てを削れば指示された表面粗さが達成できるという事になります。
そして、仕上げ加工のピッチが分かれば、表面積全てを削った場合の総距離が計算できますので、刃物を動かす速さ(送り速度)から、加工時間が計算できるようになります。
このように、3次元加工の場合は、ワークの表面積と最小R、面粗さの指示によって、加工時間が影響を受ける、という事を是非覚えておいてください。
不用意にRa1.6等の指示を入れてしまうと、非常に細かいピッチで加工しなければならず、加工時間が膨大となります。
つまり、面粗さの指示がそのまま加工賃に影響を与えるわけですね。
加工時間=加工賃となりますので、低コストで済ませたければ、次のような点に留意すると良いでしょう。
- 最小Rをなるべく大きくする
- 必要でなければ面粗さの指示はなるべく粗くする(Ra1.6よりも、Ra3.2やRa6.5など)
- 不要な部分は曲面ではなく平面とする
まとめ
いかがでしょうか、今回は切削加工の醍醐味ともいうべき、3次元加工について取り上げてみました。
一般的な平面と穴だけの2次元的な機械部品だけでなく、立体的な3次元の曲面形状も実現できる事で、設計時の発想の幅も広がるのではないでしょうか。
隅アールやカスプハイト等の関係を押さえておけば、適切な3次元形状部品を設計できると思います。
今回取り上げた内容は、3次元加工の基本部分になりますが、これだけ押さえていただければ加工屋さんにも十分に理解してもらえる設計ができるのではないでしょうか。
ポイントさえ押さえておけば、あらゆる形状を実現できる事が切削加工の強みと言えますね。
次回は、何でもできる切削加工でも、苦手な事やできない事と、その解決策についてご紹介したいと思います。