みなさんこんにちは!
電通総研の金型ソリューションチーム“Mold Planner”です。
私たちは金型設計製造を行われている製造業のみなさまに、30年以上にわたりCAD/CAM/CAEなどのITツールをご提供し、業務改革をお手伝いしています。
これまでのブログでは「金型設計製造の効率化」という観点で話をしてきました。
今回は、切削刃具の摩耗による加工精度の悪化や、量産時の金型劣化に起因する成形不良を『未然に防ぐ』という視点で書かせて頂きます。
多くの金型製造・量産成形に従事される皆様は、このような問題をどのように対処されているのでしょうか。
一つは、問題が起きてから原因を調べて対処をする方法、一方、問題が起きなくても定期的に(加工時間やショット数など)工具や部品を交換する方法のいずれかではないでしょうか。
最近では、問題が発生するタイミングを予測し、未然に対処するAIの技術が大きく進化しています。AIを活用しながら、機器の健康管理をすることで業務上の適切な意思決定を行う技術のことを「PHM」と言います。
そこで、今回は「切削加工・射出成形におけるPHM」についてご紹介します。
これからお話する内容は、次の通りです。
- PHMとは
- 切削加工におけるPHM
- 射出成形におけるPHM
- PHMの進め方
PHMとは
PHM(Prognostics and Health Management)とは、直訳すると「予後と健康管理」ですが、産業界で使われる「PHM」とは「故障予知と寿命予測」と訳され、下記の内容を示します。
- 機器の不具合の予兆をとらえ、原因を特定する。
- 機器の劣化をモデル化し、寿命を予測する。
- 機器の健康状態を把握し、適切な意思決定をする。
この技術は航空機や宇宙産業など、これまで「絶対に失敗できない分野」に積極的に適用され、技術開発が進んできました。最近では自動車業界、電機・精密業界、さらには工作機械や金型の業界まで浸透し始めています。
PHMは、ここ数年で大きく進化し、注目され始めてきましたが、2つの理由があります。
一つが「計測技術の向上」です。
機器を管理する上では、健康状態を適切に把握するために様々な計測機器が必要です。一口に計測機器といっても、寸法計測から各種センサまで多岐にわたります。
最近では、センサの扱いが容易となり、超高性能な画像センサなどの新たな計測機器も出てきています。
もう一つは「AIの進化」です。
センサから取得した大量の情報から「健康な状態か」「故障・異常な兆候が出はじめている状態か」を判断する技術が向上しました。健康・異常の情報を数多く集める(学習させる)ことで、人間の判断以上に正確に「この先に起こる故障」を予知・予測できるようになりました。
「計測技術」と「AI」がPHMの進化に大きく寄与したと言えるでしょう。
では、産業界におけるPHMの適用例を一つご紹介します。
ある建設機械メーカー様では、大型のダンプトラックを世界各地に輸出しています。その多くは鉱山など、厳しい環境で酷使されています。万一故障が起きて道の真ん中で立ち往生した場合、全体の生産に大きな影響を与えて多大な損失となります。そのような故障を防ぐため、そのメーカーではPHMの技術を導入しました。
車両の重要箇所にセンサを配置し、データをリアルタイムに収集します。取得した大量のデータ(インダストリアル・ビッグデータ)を素早く分析し、故障の予兆をとらえて故障箇所を絞り込みます。
故障の予兆をとらえることができれば、故障前に点検が可能となり、大きな損失を防ぐことができます。
なお、PHMの導入事例については、「PHMデザインツール MADe」のリンク先ホームページに掲載しています。ご興味のある方は、ぜひお立ち寄りください。
それでは、切削加工・射出成型におけるPHMの活用例をご紹介いたします。
切削加工におけるPHM
まず、工作機械で金型部品を切削加工する場面でのPHM適用をご紹介します。
切削加工におけるPHM適用で考えられる例としては「刃具の摩耗」があります。刃具が摩耗すると当然加工物の精度が下がりますが、寿命よりも短いスパンで交換すれば刃具のコストがかさみ、交換作業も増えます。
交換作業を極力減らすためには、刃具の寿命を的確に予測し、ベストなタイミングで交換することが重要です。
これを実現するためには、刃具が摩耗する過程のデータを数多く集める必要があります。同時に、刃具の摩耗の過程において、工作機械からどのような信号が発信されているかも時系列に取得します。
例えば、下の【図1】のように、工作機械から取得可能な信号データと、刃具の摩耗量が計測できているとします。
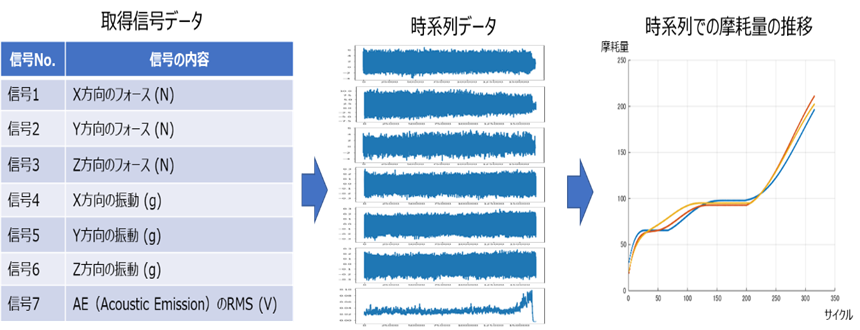
【図1】工作機械取得信号データと刃具摩耗の関係
このデータから、刃具があるサイクルを超えると、急激に摩耗量が上昇する傾向があることが分かります。
このようにAIに取得信号データと刃具摩耗を学習させることで、AIは「このような信号の傾向であれば、摩耗が一気に進行するはずだ」というように「未来の状態を予知」できるようになります。
後は、システム構築することでAIの予知結果からアラームを出すようにすれば、実際に加工物に影響が出る直前のベストなタイミングで刃具を交換することが可能です。
上記の例では学習データとして機械にかかる力、振動等を取得していますが、有効な学習データは、これだけとは限りません。
音、画像、切りくずの量など、時系列のデータをより多く取得し、AIに与えることで、予測の精度を高めていくことができます。
以上は、刃具への適用例でしたが、もちろん工作機本体の劣化もPHMの対象となります。
スピンドルやベアリングの劣化・摩耗による性能低下、テーブルの位置決め精度など、問題が起きてからでは取り返しがつかないような故障を、工作機械が発信するバイタルデータから未然に防ぐ仕組みです。
ここ数年、工作機メーカー様から私たちに「PHMを適用したい」という問い合わせが非常に多く頂いており、この流れはますます加速するものと推測されます。
射出成成形におけるPHM
次に量産時の射出成形工程におけるPHMについて考えます。
量産成形における金型の劣化に起因する「故障」には、どのようなものがあるでしょうか。
例えばキャビ・コアの型合わせ部の劣化により樹脂が漏れ、バリが発生する成形不良が起き始めたとします。
当然、成形を止めて問題の原因追及と対策を行いますが、一定時間成形を止めることは、生産計画に大きく影響します。この問題もPHMで未然に防ぐことができます。
このような成形不良を予測するための情報としては、型締め部に圧力センサを取り付け計測、金型の表面形状をカメラ式の3Dスキャナでショットごとに撮影して点群処理で平面度を計測、さらに、高解像度のカメラで表面のキズ・色の変化を常に画像処理して数値化するなどが考えられます。
こうした情報をAIが学習することで、「こういう波形が発生したら、金型の摩耗が始まっているぞ」などの診断ができるようになります。
ただし、どのような成形不良を予測するのか、その予測に適したセンサ種類は何か、計測場所をどこにするか、故障した状態をどのように再現してAIに学習させるか、など技術課題が多いのも事実です。
しかし、近い将来、量産成形の分野でもPHM技術が当たり前になることでしょう。
PHMの進め方
今までご説明させて頂いましたPHM適用ですが、どのようなステップで取り組むべきかご紹介していきます。
大きく2つの取り組みに分けられます。
一つは「PHMデザイン / シミュレーション」です。こちらは機器やシステムのつながりをモデル化し、故障に至るまでの因果関係を解くことで観測(センサ)位置を明確化する取り組みです。
もう一つは「BigData分析PHM」です。こちらは過去に取得したビッグデータを利用し、故障の特長を分析し、健康状態の悪化をとらえて故障を予知する取り組みです。
PHMと聞くと、後者の「BigData分析PHM」の方をイメージされるのではないでしょうか。こちらは「機械学習」「AI」といった、今風の言葉で語られることが多いからだと思います。
しかし、闇雲に多数のセンサを取り付け、膨大な「ビッグデータ」を集めても、コストだけがかさみ、PHMの実現には至りません。「データは取っているのにPHMが進まない」というケースでは、そもそも対象の機器やシステムの理解が不十分な可能性があります。
もし、データ分析が進まないのであれば、今の製品やシステムの可視化・分析をするPHMデザインを実施してみてはいかがでしょうか。
PHMデザインにより、対象の製品やシステムの構成要素の因果関係と故障のメカニズムを明らかにします。
以下にPHMデザインの流れとアウトプットを図示します。【図2】
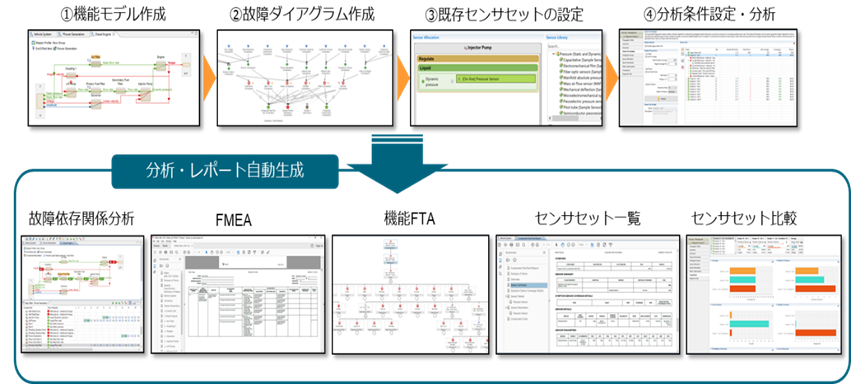
【図2】PHMデザインの流れとアウトプット
PHMデザインをご支援する「PHMデザインツール MADe」の詳細は、リンク先ホームページに掲載しています。ご興味のある方は、ぜひ、お立ち寄りください。
PHMの重要な取り組みである「PHMデザイン / シミュレーション」と「BigData分析PHM」とは別に「自社に最適なPHMを構築するための計画を立案したい」「PHM技術者を育てたい」などのご要望を頂くケースもあります。
そのような要望にお応えしつつ、PHMの取り組みを希望される方には、以下4つのアプローチのいずれかからスタートして頂いています。【図3】
【図3】PHM活動のアプローチ
1.PHMデザイン/シミュレーション
前段でご紹介しましたが、システムの構成要素の因果関係と故障のメカニズムを明らかにします。
機器やシステムの整理、分析、センサの検討からはじめるケースです。
2.BigData分析PHM
こちらも前段でご紹介しましたが、実際に取得したデータを機械学習・AI技術を用いて、故障の予知、診断、寿命予測を行う手法を構築します。
ある程度データは取得できており、まず分析してみてPHMの実現性検討からはじめるケースです。
3.PHMグランドデザイン
PHMを実現し、効果を出していくためには、どのようなワークフローで進めるべきかを事業環境を確認しつつ、リソース計画や実施計画を立てていきます。実現に必要なツールの導入や、システム開発計画も策定します。
PHM実現までの全体計画を先に策定するケースです。
4.PHM人材育成
社内にてPHMの必要性、有用性、基本的な技術の社内教育を実施します。
まずはPHMを社内に浸透させ、多くの技術者に理解を深めてもらうことからはじめるケースです。
PHMの実現には、PHMデザインから、データ分析のためのアルゴリズム開発、また利用しやすい環境にするためのシステム構築など、多くの取り組み課題があります。
弊社は、それぞれの企業状況に応じて、POC(実現性検証)や教育などのポイント的なご支援から、グランドデザインのような統合的なPHM環境の構築に向けた技術支援まで、幅広くご支援させて頂いております。
次回は、ものづくりのリードタイムを短縮のため、「IT活用した加工効率化」についてご紹介いたします。
ぜひ、次回の記事をお楽しみに!