ステンレス(SUS)とは、その名の通り「Stain=錆」が「less=少ない」材料です。鉄系素材の一種ではありますが、耐食性に優れているので、錆を気にせずそのまま使える材料として、様々な場所で活用される汎用的な材料と言えます。
ステンレスの加工について
ステンレスには以下のようなメリットがあり、建築・土木、産業機器・プラント、食品製造など様々な分野で使用されています。
・耐食性や耐熱性に優れた部品が製作可能
・塗装やメッキが不要で、メンテナンス性が良い
・清潔で美しい外観が得られる
私たちの身の回りには多くのステンレス製品があり、その製造にはステンレス加工が不可欠です。
ステンレスの加工には主に切削加工、板金加工、製缶加工の3つの方法があります。
切削加工
切削加工では、旋盤やフライス盤などの工作機械を使用して、ブロック材や丸棒材から必要な形状を削り出します。ステンレスは鉄に比べて加工時の切削抵抗が大きく、工具の摩耗も早いため、適切な切削条件の設定が重要となります。
また、ステンレスは靱性(ねばり)があるため、ハンディタイプの電動工具では加工が困難です。
板金加工
板金加工では、レーザー加工機やタレットパンチプレスなどを使用して板材を所定の形状に切断・曲げ加工します。ステンレスは加工硬化が大きく、スプリングバックも大きいため、曲げ加工時には鉄よりも大きな曲げ半径が必要です。
製缶加工
製缶加工は、パイプ材やアングル材を溶接して立体構造物を製作します。ステンレスはTIG溶接が一般的で、溶接部の変色防止のため、裏面までシールドガスを施す必要があります。また、溶接後に酸洗いを行うことも有効です。
今回は鉄と同様に設備部品でよく使われる「ステンレス」について、特徴や規格などをご紹介していきます。
目次
ステンレス(SUS)の特徴とは?
ステンレスはそれなりの強度がありながら、加工がしやすく、何よりもメッキや塗装の必要がないという点が魅力です。
塗装やメッキ処理は、使用中に剥離してしまう可能性があります。不純物などが認められない食品や医療・製薬、半導体関連の設備部品には塗装やメッキが前提となる鉄よりも、ステンレスが多用されますね。
ただし、鉄(SS400など)と比べると材料費が高く、加工しにくい素材のため加工賃も高くなりがちです。
ステンレスは、SUSという表記から“サス”と呼ばれることが多いですね。海外の図面では“SS”(Stainless Steelの略)と表記されている場合もありますので、SS400などと混同しないように注意が必要です。
ステンレスで最も一般的なのは、SUS304(サンマルヨン)です。切削性はそれほど良くありませんが、溶接性が良く、耐食性に優れ、多様な規格形状があって最も流通量の多い汎用的な材質です。熱伝導性が良くないため、薄肉形状は溶接や加工応力等によって反りなどの変形を生じやすいので注意が必要です。
切削性を重視する場合は、材料費が割高になりますがSUS303(サンマルサン)が選ばれることが多いですね。材料費はSUS304に比べて割高ですが、加工費は下がるため、部品のトータルコストが下がりやすい材質です。
ベテランの設計者さんは、切削加工部品にSUS303を指定するケースが多いと思います。逆に溶接性は良くないので、溶接が必要な場合はSUS304を選択してください。
耐食性を更に重視する場合は、SUS316(サンイチロク)やSUS316L(サンイチロクエル)が選ばれることが多いですね。
SUS316やSUS316Lは、SUS304と比べるとモリブデンの含有量が多く、海水を始め各種触質に対する「耐食性」に優れています。
更にSUS316LはSUS316よりも炭素成分が少なく、「耐粒界腐食性」を付加したものになります。溶接性も良い材料です。
他にも、析出硬化処理により強度を高められるSUS630や、熱処理可能なSUS420J2なども比較的よく使われる材料です。
代表的なステンレス素材の機械的性質を下表にまとめておきますので、参考にしてみてください。
表1 ステンレス材料の機械的特徴
材質 | 耐力 N/mm2 |
引張強さ N/mm2 |
伸び % |
硬さ | ||
SUS303 SUS304 SUS316 SUS310S |
固溶化熱処理 | 205以上 | 520以上 | 40以上 | HV200以下 | |
SUS316L | 175以上 | 480以上 | 40以上 | HV200以下 | ||
SUS430 | 焼き鈍し | 205以上 | 450以上 | 22以上 | HV200以下 | |
SUS420J2 | 焼入焼戻し | 540以上 | 740以上 | 12以上 | HV220以上*1 | |
SUS440C | – | – | – | HRC58以上 | ||
SUS630 | 固溶化熱処理 | – | – | – | HRC38以下 | |
析出硬化処理 | H900 | 1175以上 | 1310以上 | 10以上 *2 | HRC40以上 | |
H1150 | 725以上 | 930以上 | 16以上 *2 | HRC28以上 |
*1 焼きなまし状態の硬さはHV247以下
*2 厚さ15.0mmを超えるもの
「JIS G 4303」より抜粋
ステンレスの表面仕上げについて
今回は、最も汎用的なSUS304を重点的にご紹介していきます。
ステンレスの場合、必ずと言っていいほど材質や加工方法と考えなければいけないのが、表面仕上げや溶接の仕上げです。切削加工部品は加工してそのまま使用されるケースが多いですが、板金加工や製缶加工品では表面仕上げが重要な要素となります。
ステンレスは材料自体に耐食性があるため、通常メッキや塗装は施しませんが、その代わりバフ研磨などの処理を施すことが一般的です。
特に板材、フラットバー、パイプ材、アングル材などを利用する際には、No.1(ナンバーワン)と呼ばれる表面の材料を使用することが基本となります。
図2-1に基本的なステンレスの表面仕上げのサンプルを示します。
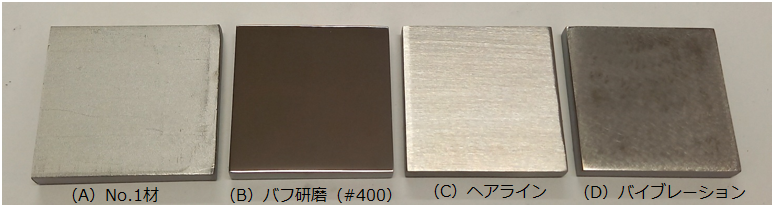
図2-1 ステンレス素材の表面仕上げ例
(A)がNo.1材の状態です。
No.1材は表面がざらざらしていて光沢もない状態で、「酸洗材」とも呼ばれます。表面の微細な凹凸により汚れが若干落ちにくいですが、表面処理をしていない分材料費が安く済みます。
何も指定せずにフラットバーなどを購入すると、このNo.1の状態で驚く設計者さんも多いようです。外観を気にせず安価に済ませたい場合は、特に表面処理を指定せずNo.1のままでも良いと思います。
(B)がバフ研磨仕上げの状態です。
アングル材や板材、パイプ材などは、素材の状態でこのバフ研磨仕上げの材料が多く流通していますね。この場合は、基本的には片側(外側)だけ研磨面となるのが標準的です。
#400(ヨンヒャクバン)というのは、バフ研磨の番手を表します。数字が大きいほうがピカピカと表面がきれいに磨かれている状態です。#800や#240などという指定も可能です。
基本的には#400が最も一般的で、安価に済みますので、特別な理由がない限りは#400とするか、番手不問としておくと良いと思います。
バフ研磨仕上げだと傷が目立ちやすいので、(C)のヘアライン仕上げや、(D)のバイブレーション仕上げとする場合も多いですね。
ヘアライン仕上げは、一方向に筋の入った研磨仕上げの状態です。
ヘアライン仕上げも、板材、パイプ材などの規格によっては素材の状態で入手することが可能です。元々ヘアラインの筋が入っているので、使用中の傷なども目立ちにくく、意匠性のある仕上がりとなります。
バイブレーション仕上げは、少し粗目の磨き目をランダムに入れたような状態です。
ヘアライン同様、予め表面に筋を入れておくことで傷を目立ちにくくします。溶接で組み立てる製缶品などに良く活用される仕上げ方法ですね。
また、ステンレス材料では、ホット材やコールド材という区分けがされます。ホット材は材料製造の際に熱間圧延された材料で、表面がざらざらしたNo,1の状態が基本となります。
コールド材は熱間圧延後に、冷間圧延を経た材料で、ホット材よりも表面が滑らかで光沢のある状態(2B)が基本となります。
ホット材に比べるとコールド材のほうが残留応力が多く残っているため、切削加工などの素材として使用する際には変形が生じやすく注意が必要と言われます。
ステンレスの溶接と仕上げ方法について
ステンレスは溶接とその後処理との兼ね合いが、強度や外観に影響するためとても重要となります。「溶接方法と後処理」については、設計者が図面で指示するようにしてください。
図3-1がステンレス素材の溶接後処理のサンプルです。2つのフラットバーを隅肉溶接で接合したものになります。
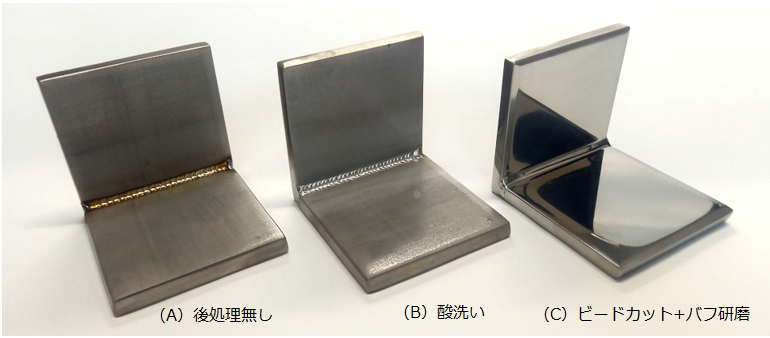
図3-1 ステンレス素材の溶接後処理例
通常肉盛り溶接をすると、溶接ビードと呼ばれる鱗状の凹凸が生じます。鉄の場合は、基本的に塗装やメッキをするので、溶接ビードはそのままにして表面処理を施すことが多いですね。
ステンレスの場合は塗装やメッキなどの表面処理をしない場合が多いので、溶接後の処理まで設計で考えておく必要があります。基本的には、(A)後処理無し、(B)酸洗い、(C)ビードカット+バフ研磨のいずれかを選ぶことになると思います。酸洗いの代わりに、電解研磨を施すケースもありますね。
(A)は肉盛り溶接したままの状態です。
溶接ビードは溶接の熱で変色したままとなります。サンプルの素材はNo,1の状態です。
(B)は溶接ビードを酸洗いしたものです。
変色が消えて、きれいな母材の色が出てきますが、鱗状の凹凸は残ります。
(C)は溶接ビードを、滑らかに処理しバフ研磨加工を施したものです。
このように溶接ビードを滑らかに仕上げることを「ビードカット」と呼んでいます。サンプル素材もバフ研磨仕上げにしています。
このように、同じステンレスの製品でも、表面仕上げや溶接の後処理で仕上がりが異なります。特にSUS304は溶接が多用されますが、開先や脚長などの指示とともに、仕上げ方法についても明確な図面指示を心掛けてください。
ステンレス材料のうちブロック材の特徴
ステンレス材料のうち、切削加工に良く使われるブロック材の特徴について解説します。
ステンレス材料のブロック材は、基本的に6面フライス加工(6F)を施した材料として入手するのが一般的です。
主にフライス系の加工方法などにより、ブロック形状部品の製作に使用されます。
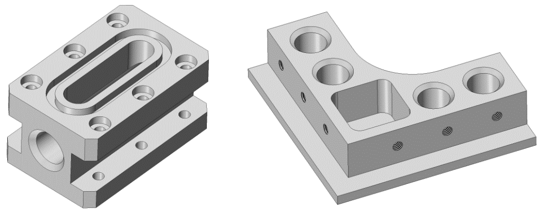
図4-1 ブロック形状部品の例
厚み(6面体の最小寸法)が200mm程度までは、一般的な6F材料として流通しているようです。それ以上の材料が必要な設計の場合は、入手性について製造現場や材料業者と確認をしておいたほうが良いでしょう。
6F材の代わりに、フラットバーや板材を切り出して、切削加工用の素材として使用することも多いですね。
ステンレス材料のうち丸棒材の特徴
ステンレス材料のうち、シャフトなどの軸形状部品に良く用いられる丸棒材の特徴について解説します。
ステンレスの丸棒材は、主に旋盤加工などで精密加工部品として利用されます。特に食品機械や医療関連、半導体関連などの装置のシャフトなどとして活用されることが多いようです。
また、インペラやスクリュー形状部品など、高速で回転するような回転体部品も、多くは丸棒から製作されます。
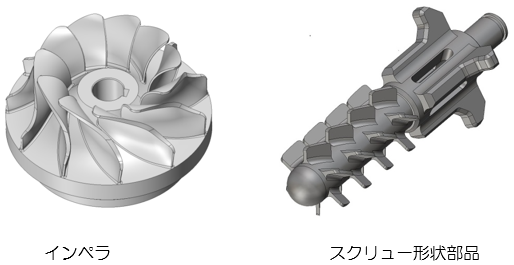
図5-1 回転体部品の例
ステンレスの丸棒材は、鉄系材料と同様に、ピーリング材、酸洗材、冷間引抜き材、センタレス研磨材があります。
材料メーカーや卸問屋で取り扱っている材質や寸法規格が異なりますので、自社の商流を確認した上で、入手可能な規格寸法等を確認すると良いと思います。
参考までに、一般的な材料寸法表を下表に示します。
表5-1 ステンレス材料 丸棒材の標準寸法
※ ターニング加工品:Φ165~Φ400詳細は材料業者にお問い合わせください
※ 表はSUS304のもの、SUS303、SUS316、SUS316も類似のラインナップ
材料業者提供情報より、筆者にて作成
(後編へ続く)
※ステンレス材料のうち丸パイプ材、板材、平鋼、角パイプ材、アングル材、チャンネル材の特徴と選び方は「ステンレス(SUS)の特徴や設備部品での選び方を解説(後編) 」をご覧ください。