私は、お正月休み中、製造業のDXをどうやって浸透させていくことができるのかをじっくり考えてみました。
これまでも、インダストリー4.0、IoT・IIoT、デジタルツインといったITの新しい言葉が使われるたび「開発設計製造の現場の人たちは違和感を持っているのでは?」と感じていました。これだけ普及してきている3D CAD導入でさえ抵抗されることもあるので、DX推進ではその苦労が予想できます。
目次
1.デジタル化用語のおさらい
これまで、また今もよく耳にする用語についておさらいをしましょう。
インダストリー4.0([英]Industry 4.0)
製造業におけるオートメーション化およびデータ化・コンピュータ化を目指す技術的コンセプトの名称で、”第4次産業革命”ともいわれている。
IIoT([英]Industrial Internet of Thing)
IoTが「モノのインターネット」として、モノにセンサーを取り付けて、その情報をインターネットからモニターすることやコントロールすることで、付加価値を得ることを目的としていることに対して、製造に特化したものとして製造業におけるモノのインターネットとしています。
デジタルツイン([英]Digital Twin)
日本語では「デジタルの双子」です。現実世界の製品や製造設備の情報などをリアルタイムに収集し、仮想世界に送って、仮想空間と現実空間とまったく同じ状態を再構築し、仮想空間上でのシミュレーションなどを行うこと。IoT・IIoTがあるからこそできるものです。
2.3Dで仕事のやり方を変える
DX([英]Digital Transformation)ですが、いまだデジタル化だと思っている人も多いかもしれません。しかし、そうではありません。その目的は「進化するデジタル技術によって仕事のやり方を変える」ことです。最近の技術・ソリューションについては前回の記事「As-IsとTo-Beとは?今、3Dでできること」で、ほんの一部ですがお話ししました。
3Dプリンタによる造形もそのひとつにあります。その製作事例も紹介させてください。下図の事例はデモ展示用に液晶パネルを組み込むための部品を3Dプリンタにより製作したものです。
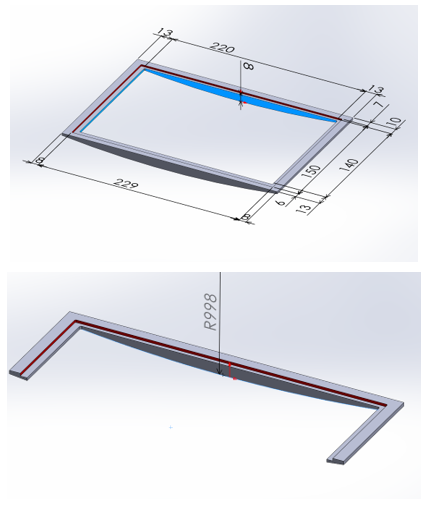
3Dプリンタ作成用3D部品図
このような形状の部品を2個だけ製作する必要がありました。R形状で、しかも開口部の大きな部品を切削加工することはコスト・品質ともに、また量産するわけではないので、金型を作って成形するというのも、現実的ではありません。そこで3Dプリンタで製作することにしました。
3Dプリンタでは、ASA(対候性ABS)を使用しています。ASAは基本特性がABS樹脂と似ていますが、耐光性・耐候性・美観に優れていて、屋外で使用されることが多い材料です。
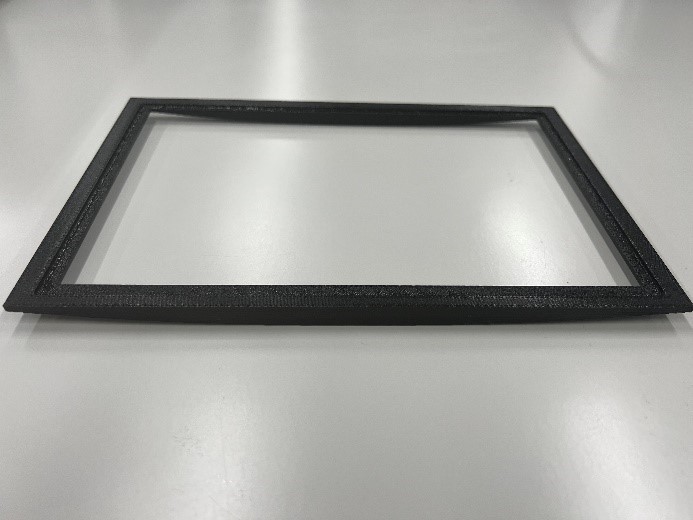
3Dプリンタによる部品製作 協力:スワニー(長野県伊那市)
この部品は、有限会社スワニー(長野県伊那市)に製作依頼をしました。3D CADデータ(SOLIDWORKSデータ/STLデータ)の送付から納品までの期間は実働で5日間でした。高品質でしかも2つしか製作しない部品としては低コストで済みました。切削加工では、コストも品質も確保できなかったことでしょう。
デモ用の部品でしたが、小ロットの部品を短納期・低価格で調達する上で3Dプリンタの活用は効果的です。その材料も樹脂だけではなく、カーボンや金属も可能になりました。これにより本番で使用する部品にも使えそうなので、その活用用途はさらに広がることでしょう。
3Dデータは従来の切削加工だけではなく、アディティブマニュファクチャリングといわれる新しい加工方法と密な連携ができます。3Dプリンタは3D CADなしでは語れません。
3.製造業のDXを俯瞰してみる
3D CADで何ができるのかを理解すると、現在抱えている問題とその課題から、「何ができそうなのか」が見えてきます。As-Is(現状)からTo-Be(理想のあるべき姿)がわかります。To-Beのハードルは高いかもしれませんが、イメージしてみましょう。
私のイメージを次の図に表してみました。
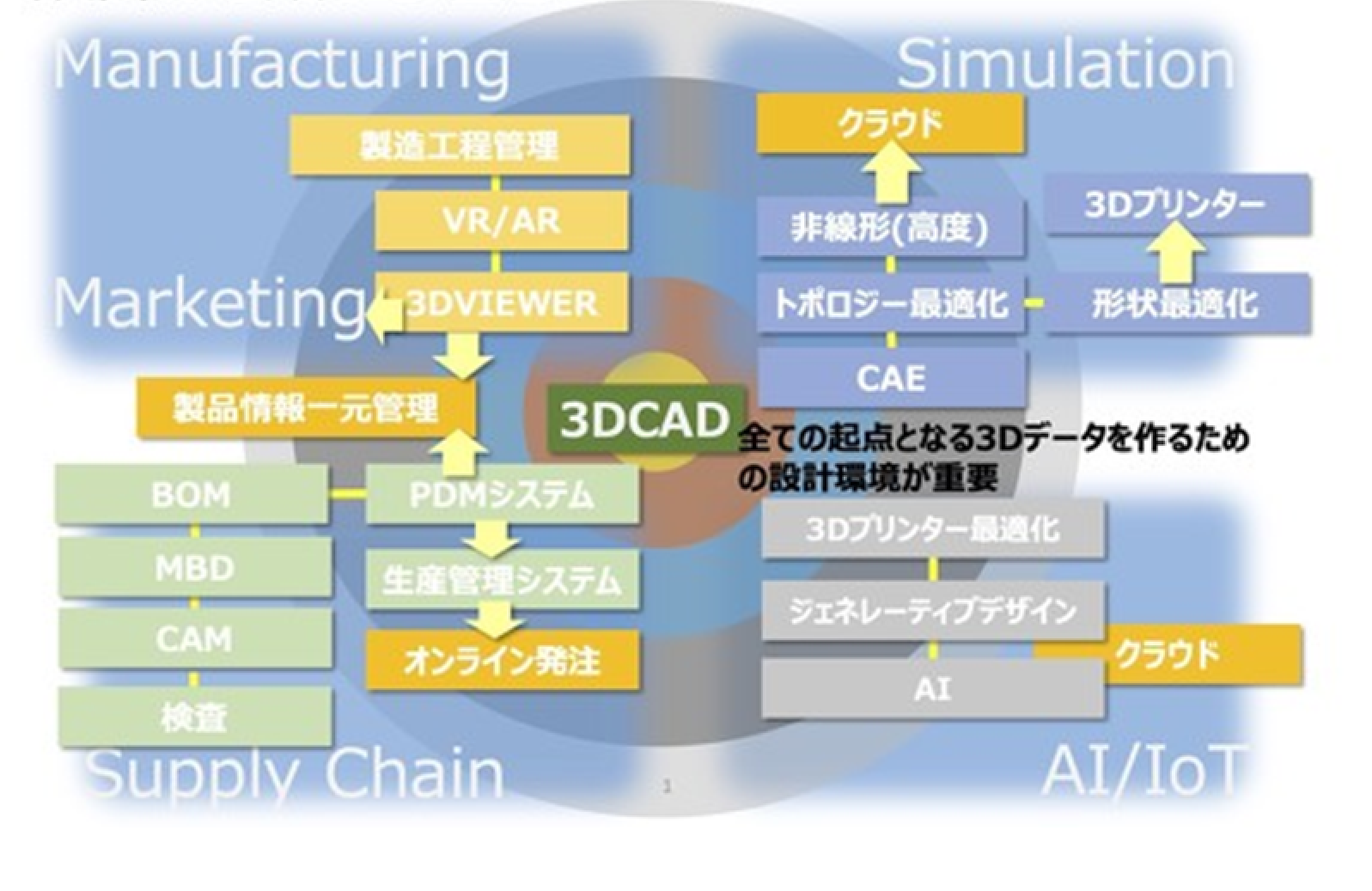
3Dから始まる理想のゴール
部品単体が製品になる会社もあれば、部品が組み立てられたものが製品になる会社もあります。どちらも最小単位を考えれば、部品です。元になった3D部品を中心に置いて、そのデータをどのように活用していくのかをイメージしました。
「3Dから始まる理想のゴール」について解説します。
Simulation領域
3Dデータによる部品図、組み立て図はCAEにより検証が行われ、最適化が仮想検証されます。この検証では、線形解析・トポロジー・非線形解析などが使用されます。
今日ではクラウド上で解析を行うことも可能になったので、いつでも、どこでも、どのようなデバイスを使用しても解析を実行することも可能になりました。最適化された形状を3D プリンタで出力することも可能なので、仮想検証だけではなく実物のモノとして手に取ることも可能です。
Supply Chain領域
3D部品図、3D組立図はPDM(Product Data Management System)で管理します。PDMは設計の最終成果物の更新履歴や派生する製品を効率的に管理することができます。PDMから最終成果物としての部品表(BOM)を作成し、調達部門の手配を行うことが理想的です。
さらにはMBD([英]Model Based Definition:モデルベース定義)によって、図面データを3Dモデルに取り込み図面レスにて製造工程へ渡すためのデータもこのPDMによって管理できたらよいでしょう。加工用のCAMデータも製造情報のひとつとして、この仕組みで管理することが可能だと私は考えます。
最近では3DA([英]3D Annotated Model)という名称で、3Dモデルに構造特性(寸法、注記、数量など)を加えたモデルを利用していこうという動きがあります。PDMで作成したBOMデータは生産管理システムなどの基幹システムに受け渡され、受注情報、原価情報、実績情報が付加されて社内を流通していきます。その中で、EDI([英]Electronic Data Interchange:電子データ交換)によって、サプライヤとの間で、見積依頼・注文処理・請求処理を行います。
これもまたさかのぼれば、PDMにより管理され、BOMとして出力された一品一品に対して行われるものです。
Manufacturing領域
製造(組立)現場では3D CADデータから作成された3D Viewerデータにより製造が行われます。これまでフラットパネル上や3Dメガネにより立体的に見ていた画像は、VR/MR技術により、さらに没入感のある3D形状として見えるので、製造前の設計審査レビューにおいてもより認識性の高い検証ができます。
他には、デジタルスキャン技術により現物から3D デジタル化を行うことが可能です。リバースエンジニアリング([英]Reverse engineering)のひとつです。加工により修正を加えたモノをデジタル化することや、3D CADデータと実物の比較検査もできます。
3D Viewerを利用することで、設計終了段階から組み立て作業指示書や取り扱い説明書も作成することができます。
AI/IoT領域
定型的な設計領域では、AIを使用しなくても設計パラメータをいかに駆動させるかによって自動設計ができますが、今日では非定型な設計に対して、AIを使用した自動設計ができるようになりました。設計者は必要とする設計の値を入力し、これにより出力される複数の形状データから設計案を検討します。
IoTでは、IoTを利用してユーザーが付加価値の高い利用をできる製品を提案することができます。また構造解析など、実物からのデータをリアルタイムに求め、これをCAEにインプットすることで、より信頼性の高い解析を行うことができます。
次回もDXについて深堀していきましょう。
前の記事へ
次の記事へ