製品の安全性と信頼性を確保するには、材料挙動を示す「応力ひずみ曲線」の理解が欠かせません。応力ひずみ曲線からは、ヤング率や降伏点、引張強さといった材料固有の特性値を読み取ることができ、適切な材料選定や構造設計、安全率の設定に役立ちます。
本記事は、応力とひずみの基礎から材料特性と設計応用までを解説します。
目次
応力とひずみの基礎
機械部品や構造物に外部から力(荷重)が加わると、部材内部にはその力に抵抗しようとする内力が発生します。この内力を部材の断面積で割った値が「応力(σ:シグマ)」です。
また、一定の荷重が加わると材料は変形します。元の長さに対する変形量の割合を「ひずみ(ε:イプシロン)」といいます。
応力とひずみの単位と計算式は以下のとおりです。
|
応力 |
ひずみ |
単位 |
N/mm² |
なし |
計算式 |
σ(N/mm²)=F(N)/A(mm²) F:外力、A:断面積 |
ε=ΔL(mm)/L0(mm) |
それぞれの計算例を次に示します。断面積78.5mm²のボルトに1000Nの引張荷重が作用する場合の応力は
となり、元の長さ100mmのシャフトが荷重により0.05mm伸びた場合、ひずみは
と算出されます。
応力ひずみ曲線とは
応力ひずみ曲線は、材料に引張荷重を加えていった際に生じる応力とひずみの関係をグラフ化したものです。S-Sカーブとも呼ばれ、縦軸に応力(σ)、横軸にひずみ(ε)を取り、材料試験機で試験片が破断するまでのデータをプロットして作成されます。
応力ひずみ曲線を見れば、材料がどのくらいの力でどのように変形し、最終的にどのように破壊されるのかがわかります。
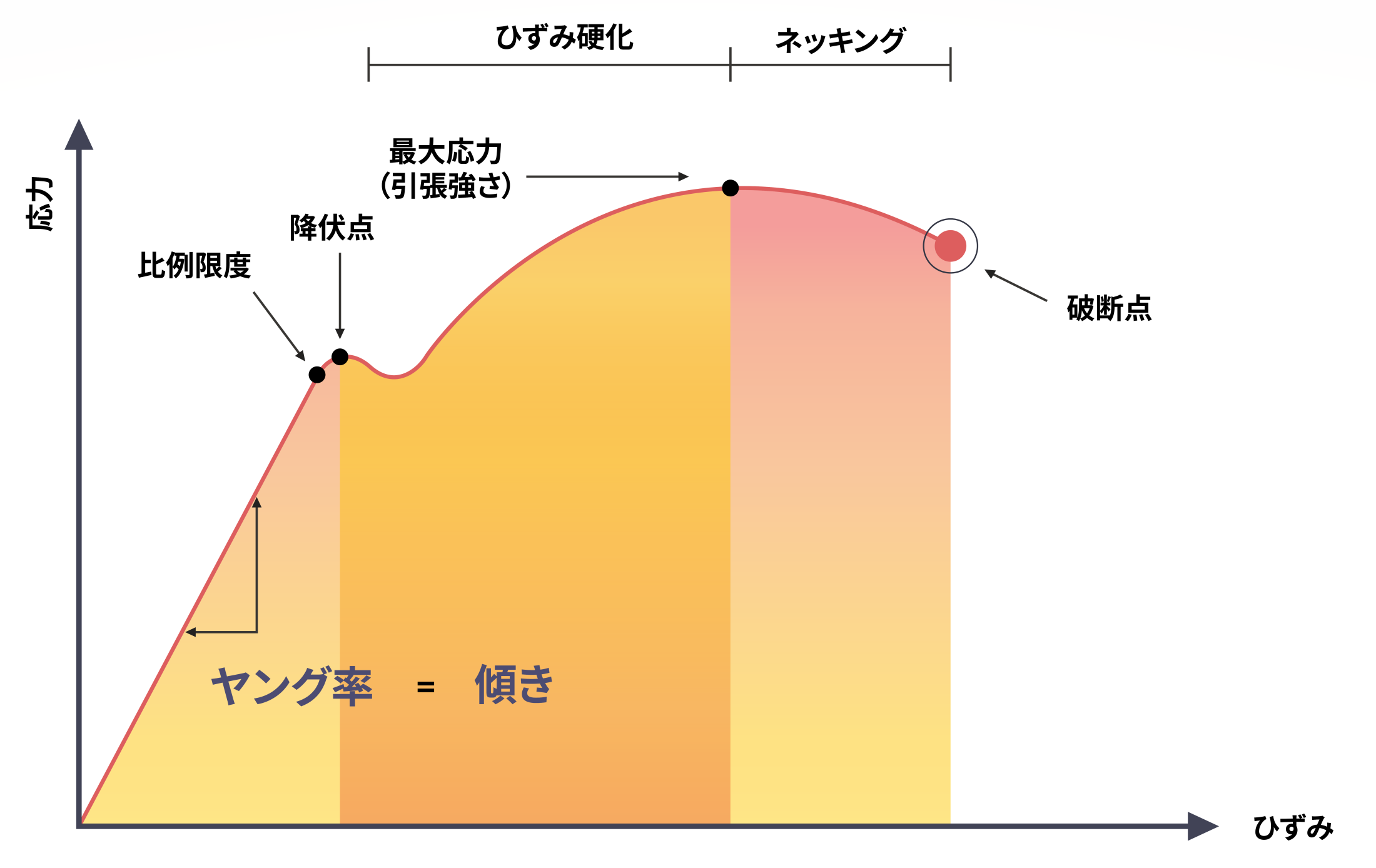
図1 応力ひずみ曲線の例
図1の応力ひずみ曲線を例にすると、荷重を加え始めた当初は直線的な線が引かれています。この部分では応力とひずみが比例していることを示しており、その勾配がヤング率E(後述)です。
荷重が一定に達すると、ある点を境に曲線が折れ曲がります。この点が降伏点です。降伏点を過ぎると材料は塑性変形に入り、ひずみの増加とともに応力が再上昇して、最大応力(引張強さ)に達します。その後、試験片にネッキング(くびれ)が生じ始め、応力は減少に転じて最終的に破断に至ります。
応力ひずみ曲線の書き方(引張試験)
ここでは「引張試験」によって求められる応力ひずみ曲線について見ていきましょう。金属材料の場合は、JISなどの規格で定められた形状・寸法の試験片を準備してください。この試験片を引張試験機に装着し、両端から一定速度で徐々に引張荷重を加えていきます。
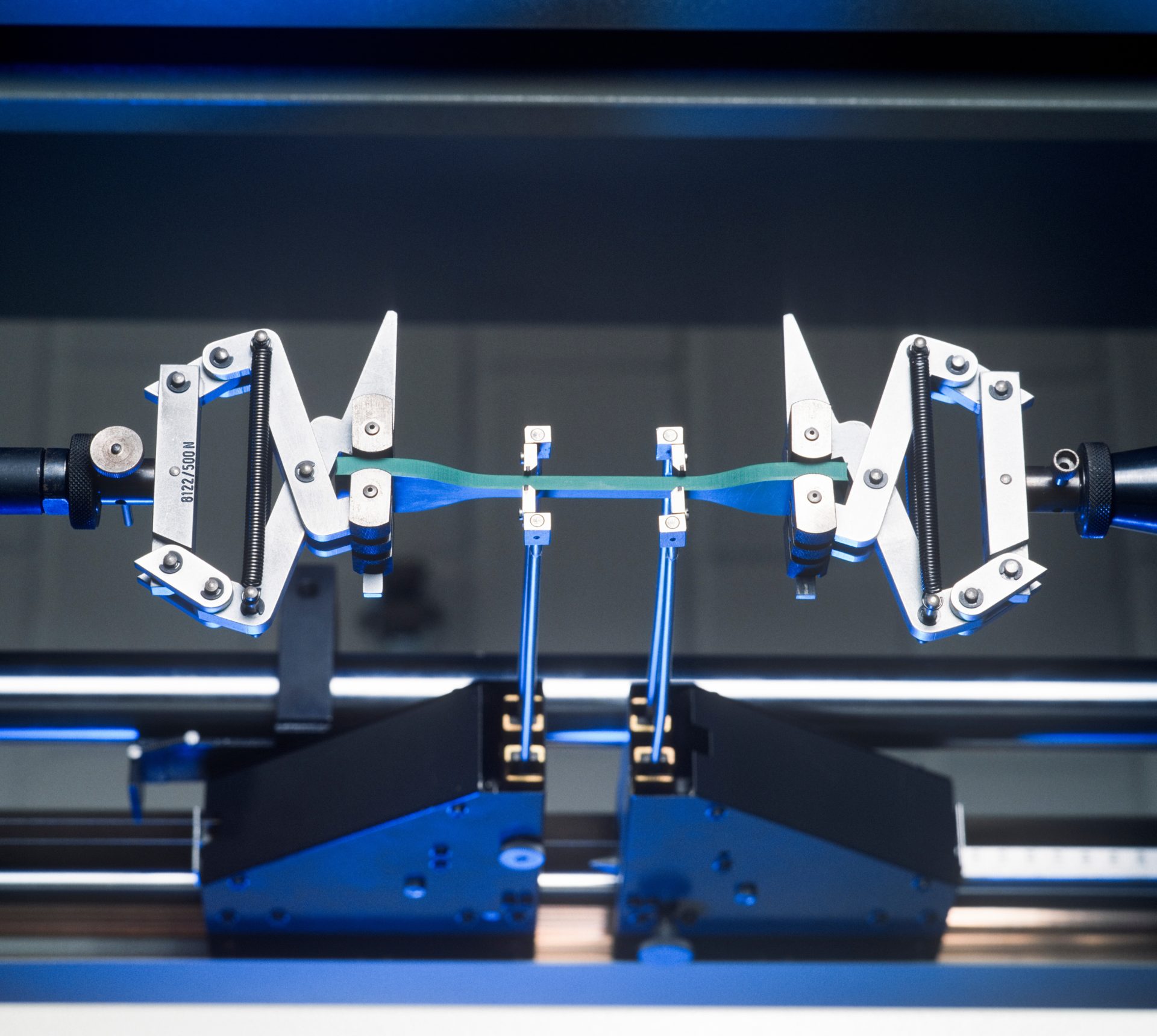
図2 引張試験
試験中は荷重(N)と伸び量(mm)を計測し、工学的応力σ=F/A₀(初期断面積で算出)と工学的ひずみε=ΔL/L₀(初期標点距離で算出)を逐次求めます。これらの値を、縦軸に応力、横軸にひずみとしてプロットしたものが応力ひずみ曲線です。
なお、金属材料の引張試験方法は『JIS Z 2241』に詳しく規定されています。
参考:金属材料引張試験方法(JIS Z 2241:2022)
応力ひずみ曲線から得られる材料特性
応力ひずみ曲線から得られる主な材料特性は以下のとおりです。
材料特性 |
主な特長 |
ヤング率(縦弾性係数) |
材料の変形しにくさ(剛性)を示す指標 |
比例限度・弾性限界 |
応力とひずみが比例し、力を除けば変形が元に戻る限界点 |
降伏点 |
材料が弾性変形から塑性変形へと移行し始める応力 |
0.2%耐力 |
降伏点が不明瞭な材料で、実用的な降伏強さの代用とされる応力 |
引張強さ(抗張力) |
材料が耐えうる最大の応力 |
破断点と伸び |
材料が最終的に破壊する点と、そこに至るまでの変形のしやすさ(延性)を示す指標 |
各特性について詳しく見ていきましょう。
ヤング率(縦弾性係数)
ヤング率(E)は、材料が弾性変形する範囲での応力とひずみの比例定数で、材料の「変形しにくさ(剛性)」を表します。値が大きいほど、同じ応力を加えてもひずみが小さく、変形しにくい材料といえます。
たとえば、構造物の剛性を確保したい場合や、精密な位置決めが求められる部品では、ヤング率の高い材料を選定するとよいでしょう。単位はPa(パスカル)で、鋼材は約200GPa、アルミニウム合金は約70GPaが一般的な値です。
比例限度、弾性限界
応力とひずみが比例関係にある限界を比例限度といいます。また、外力を取り去っても塑性変形が残らない応力の上限を弾性限界と呼び、両者は一致する場合が多いものの、比例的だが非弾性的な領域が存在する材料では差が生じる場合もあります。
この限界点を把握することは、製品が使用中に意図しない永久変形を起こさないようにするために極めて重要です。特に繰り返し荷重を受ける部品や、寸法精度が求められる部品では、応力が弾性限界を超えない設計が求められます。
降伏点
降伏点は、材料に荷重を加えていくと応力があまり増加しないのに、ひずみだけが大きく増加し始める点の応力値です。材料が弾性変形から塑性変形(元に戻らない変形)へと移行する明確な境界を示す点です。
降伏点は材料がその機能を失い始める限界点であるため、安全設計を行ううえで最も基本的な基準の一つです。部材に生じる応力が降伏点を超えないように、安全率を考慮して許容応力を設定しましょう。
0.2%耐力
アルミニウム合金などの明確な降伏点を示さない材料では、塑性ひずみが0.2%生じたときの応力を「0.2%耐力」と定義し、実用上の降伏強さとみなします。
降伏点が不明瞭な材料でも、この0.2%耐力を基準にすることで、降伏点を示す材料と同様に塑性変形を避ける設計が可能です。許容応力の設定や材料選定において、降伏点と同様に重要な指標です。
引張強さ(抗張力)
引張強さは、応力ひずみ曲線上で材料が示す最大の応力値です。材料が破断する前に耐えられる最大の荷重レベルを示し、加工硬化によって降伏点よりも高い値をとります。
通常、設計では降伏点や0.2%耐力を基準にしますが、万が一の過大荷重に対する安全性の評価や、材料が破壊に至るまでの余裕度を把握するうえで参考になります。
破断点と伸び
破断点は、応力ひずみ曲線の終点であり、材料が完全に分離・破壊した瞬間の応力とひずみを示します。引張試験後の試験片の伸びの度合い(破断伸び)や、断面積の減少率(絞り)は、材料の「延性」つまり粘り強さを示す重要な指標です。
延性が高い材料は、予期せぬ過大荷重がかかった場合でも急激な破壊を避け、ある程度の変形を伴いながら破壊に至るため、破壊の兆候を事前に察知しやすい利点があります。
鋼材とアルミニウムにおける応力ひずみ曲線の違い
金属材料はその種類によって応力ひずみ曲線に顕著な違いが現れます。機械部品の設計で多用される代表的な材料として、鋼材(特に軟鋼)とアルミニウム合金を比較してみましょう。
軟鋼の応力ひずみ曲線は、明確な降伏点を示すのが大きな特長です。弾性限界を超えると、一時的に応力が低下する上降伏点と、その後ほぼ一定の応力でひずみが進む下降伏点が現れます。この降伏現象の後、加工硬化により再び応力は上昇し、引張強さに達した後、ネッキング(くびれ)を生じて破断に至ります。
参考:ミスミ技術情報>金属材料と鉄(LCA:ローコストオートメーションを支える機素材料の基本-7)
アルミニウム合金の応力ひずみ曲線には、軟鋼のような明確な降伏点は現れないため、降伏の基準として0.2%耐力が用いられます。弾性域を過ぎると、曲線はなだらかに上昇し続け、塑性変形が進行するのが特長です。鋼材に比べてヤング率が低く(約1/3程度)、同じ応力でも変形しやすい傾向があります。
材料によって応力ひずみ曲線の形状や特性値は大きく異なるため、設計者は使用する材料の特性を正確に理解し、目的に応じた材料を選定しなければなりません。
応力ひずみ曲線の設計への活用
応力ひずみ曲線から得られる材料特性は、機械部品や構造物の設計において不可欠です。部材の剛性に関わるヤング率は、部材のたわみや振動特性を評価する際に活用されます。
また、降伏点や0.2%耐力を基にした許容応力の設定も重要です。これらの値に安全率を考慮して許容応力を決定し、部材に発生する応力がこれを超えないように寸法や形状を設計します。部品の永久変形や破壊を防ぎ、安全性を確保するためです。
さらに、材料の靱性や脆性にも注意が必要です。靱性が高い材料を選択すれば、万一の荷重超過時にも破断までの猶予が得られるため、製品や構造物の安全性が向上します。逆に脆性材料を使用する場合は、大きめの安全率を設定するか、他の素材と組み合わせるなどの工夫が求められます。
まとめ
応力ひずみ曲線は、材料が荷重に対してどのように応答し、変形し、最終的に破壊に至るかを示す、設計者にとって最も基本的な情報源の一つです。本記事では、応力ひずみ曲線の基礎から、ヤング率・降伏点・0.2%耐力・引張強さといった重要な材料特性、そしてそれらの設計への活用法までを解説しました。
材料選定から強度計算や安全率の設定に至るまで、応力ひずみ曲線の知識は設計業務のあらゆる場面で役立ちます。本記事で解説した内容を参考に、正しく理解し、そこから得られる特性値を適切に扱いましょう。
材料・材質関連記事
アルミニウムとは?素材の特徴や使用上の注意点、他金属との比較など
ステンレス鋼(SUS)とは?種類や特徴と注意点
樹脂材料にも色々ある。樹脂材料の性質
六価クロムとは?用途・規制・設計時の注意点まで解説
金属関連記事
金属材料の性質とは?金属加工や機械設計の重要なポイント
鉄の比重はなぜ重要?製造業の設計者が知っておくべき基礎と計算方法
設計者必見!金属比重データ活用術~製品性能向上のための材料選定~
チタン加工の難しさを乗り越える3つの対策─設計から最適な加工会社選定まで
靱性(じんせい)とは?製造業の設計担当者が知っておくべきポイント