設備部品の設計をおこなう場合、その部品の機能から求められる形状や材質と共に、表面処理を適切に選択することも重要です。
今回は、設備部品でよく用いられる表面処理の中でも「メッキ」と「塗装」について解説していきます。
目次
1. よく用いられる表面処理とは
部品の要素は、切削加工や板金加工によって形作られる「形状」と共に、「強度」や「硬さ」といった物理的特性と、「平滑さ」、「耐腐食性」などの表面状態や化学的な特性が考えられますね。それぞれの利用シーンに応じた材料や加工方法の選定はとても重要ですが、後から表面の特性を付加することのできる「表面処理」はとても強力な手段です。
設備部品で良く用いられる表面処理は、「メッキ」、「塗装」、「バフ研磨」、「アルマイト」といったあたりではないでしょうか。
表面処理の主な目的として、「防錆」、「平滑性」、「装飾性」、「耐摩耗性」、「硬度」の向上といったことがあげられます。
それぞれの特性や相性の良い材料などもありますので、設計目的に合わせて選定するようにしてください。
「バフ研磨」は主にステンレス材料に用いられる表面処理です。
錆びにくいというステンレスの特性を生かし、表面を磨いて平滑に仕上げる処理です。鉄やアルミ材料の表面処理前の下加工としても用いられます。ステンレスについては第14回「ステンレス(SUS)の特徴や設備部品での選び方を解説」で詳しく取り上げました。
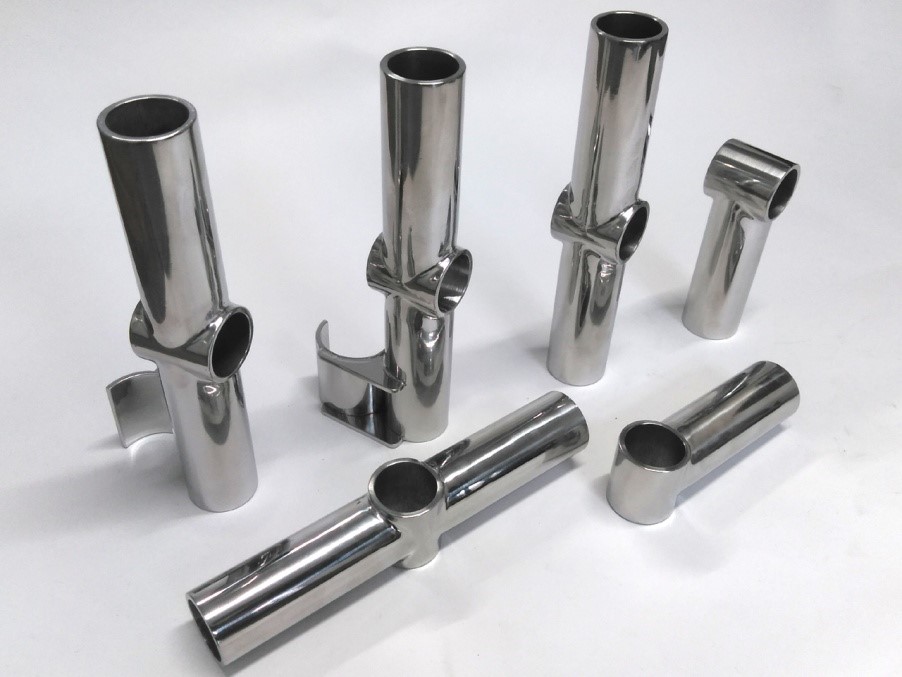
バフ研磨(#400)例
また、サンドブラストによる「梨地処理」も良く利用されます。
ガラスビーズやアルミナなどの微細な粒を表面に吹きかけて、ざらざらとした艶消し状態にします。バフ研磨の代わりに、メッキやアルマイトの下地処理として利用されることが多いです。
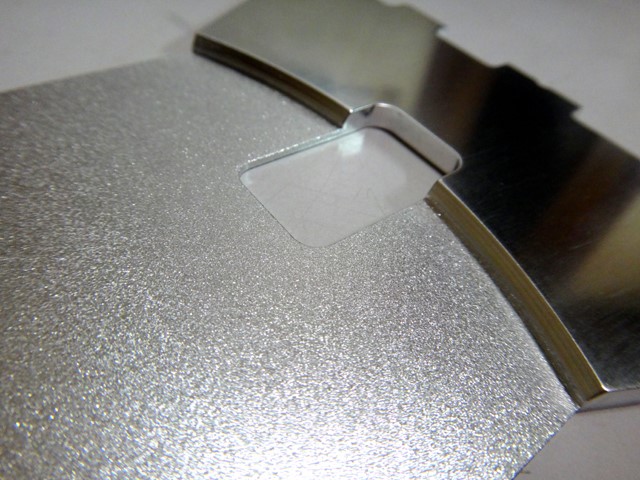
サンドブラスト例
「アルマイト」はアルミ材特有の表面処理です。
母材表面を酸化アルミの被膜で覆うことで、耐食性の向上や着色が可能となります。一方で導電性の喪失など、注意点もあります。アルマイトについては第15回「アルミ合金の特徴や設備部品での選び方を解説」で詳しく取り上げました。
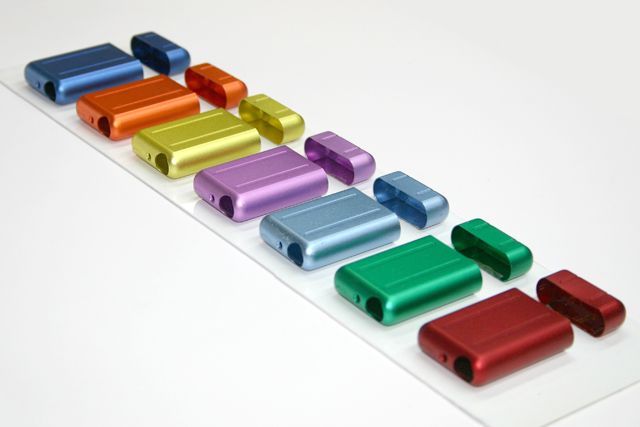
アルマイト(カラー)例
「塗装」は塗料を塗って外観を整える処理です。
主に鉄系部品の防錆や装飾目的で利用されますが、製缶部品など大物の部品に施されるケースが多いですね。装置の躯体やカバーなどに良く用いられます。
「メッキ」は亜鉛やニッケルなどの金属を、部品表面に析出させて母材を保護する処理です。
アルミ合金などに利用されるケースも多いですが、やはり鉄系部品の防錆目的で利用されるケースが多いですね。比較的小物の精密部品に多く用いられます。
今回は、「メッキ」と「塗装」にフォーカスしていきたいと思います。
表1-1 各種表面処理の特徴
特徴 | 寸法変化 | 導電性 | 剥離可能性 | 相性の良い材質 | バリエーション |
バフ研磨 | -0.2mm~ゼロ | 有り | 無し | ステンレス (鉄鋼、アルミ合金の下磨き) |
#400、鏡面、バイブレーション、ヘアライン 他 |
アルマイト | ゼロ~10μm程度 | 無し | 無し | アルミ合金 | 白アルマイト、カラーアルマイト、硬質アルマイト 他 |
メッキ | ゼロ~10μm程度 | 基本有り (メッキ種類による) |
有り | 主に鉄鋼 | 亜鉛メッキ、ニッケルメッキ、クロムメッキ、金メッキ 他 |
塗装 | 0.1~0.5mm程度 | 基本無し | 有り | 主に鉄鋼 | 焼付塗装、自然乾燥 |
2. メッキの特徴と選び方のポイント
メッキ処理は非常に多くのバリエーションがあります。
ここでは、とりわけ使用頻度が高く、単発の処理でも対応可能な代表的な処理をご紹介します。メッキはその手法によって大きく「電気メッキ」と「無電解メッキ」に分かれます。
「電気メッキ」は、電解質溶液中に金属イオンを溶かしておき、その中に部品を入れて通電することで、部品表面に金属イオンを析出させてメッキ層を形成する処理です。
「無電解メッキ」は、溶液中に還元剤を混ぜて金属イオンを還元析出させる方法で、通電が不要な処理です。複雑な形状でも均一にメッキ層を形成することが可能です。
設備部品などの少量製造などで一般的に用いられるのは、亜鉛メッキ(クロメート処理)、無電解ニッケルメッキ、硬質クロムメッキ、金メッキです。
2.1 亜鉛メッキ
手軽なメッキ処理の代表格が「亜鉛メッキ」です。
「電気亜鉛メッキ」が良く用いられ、膜厚は10μm前後が一般的です。メッキの中で比較的安価で、導電性の良いメッキ処理になります。亜鉛自体は腐食するため、メッキ後に化成処理である「クロメート処理」をおこなって耐食性を向上させるのが一般的です。
クロメート処理は、「光沢クロメート(ユニクロ)」、「有色クロメート」、「黒色クロメート」、「三価クロメート」の種類があります。
クロメート被膜中に六価クロムが含まれるため、環境に配慮して六価クロムを含まない三価クロメートへの代替が進んでいます。
また、以前は手軽な防錆処理として多用されていた「四酸化鉄被膜」(いわゆる黒染めメッキ)の業者が減る中で、代替手段として黒クロメート処理が選択されることも多いようです。
表2-1 亜鉛メッキの一般な特性
項目 | 電気亜鉛メッキ |
硬さ | 60~90HV |
膜厚 | 10μm前後 |
コスト | 安価 |
設備部品を設計する際には、亜鉛メッキは安価で手軽な手段と考えておけば良いと思います。厚い被膜の「溶融亜鉛メッキ」も身近な亜鉛メッキですが、量産用途で用いられることが多く、多品種少量部品ではほとんど用いられません。
2.2 ニッケルメッキ
部品表面にニッケル被膜を析出させるメッキ処理です。
電気メッキによる「電気ニッケルメッキ」と、無電解メッキによる「無電解ニッケルメッキ」が良く用いられます。
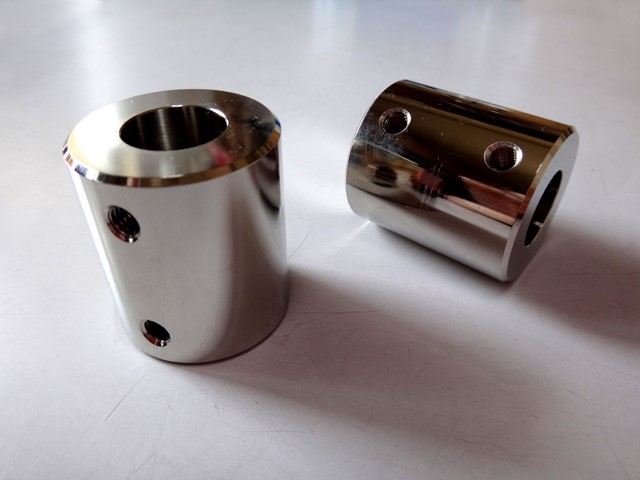
無電解ニッケルメッキ例
「電気ニッケルメッキ」は銀白色の装飾性の高いメッキです。耐食性や硬度に優れているため、「光沢ニッケルメッキ」や「半光沢ニッケルメッキ」として工業部品に多く利用されています。メッキ処理としてはバランスの取れた一般的なメッキ処理と言えます。
また、他のメッキ処理のための下地メッキとしても利用されます。膜厚は5~15μm程度です。
「無電解ニッケルメッキ」は、複雑形状でも均一な被膜を形成できることが特徴です。
実際には若干のリン成分も含まれるので、無電解ニッケル-リンメッキや、Ni-P系などとも表記されます。「カニゼンメッキ」とも呼ばれています。
メッキ処理時に電気を通さないため、金属以外にもプラスチックやセラミックスへのメッキも可能です。耐食性に優れ、硬度が高いことも特徴ですが、焼き入れ処理により更に硬度を高めることも可能です。また、メッキの膜厚を細かく制御することができるのも特徴です。
表2-2 ニッケルメッキの一般的な特性
項目 | 電気ニッケルメッキ | 無電解ニッケルメッキ |
硬さ | 光 沢: 400~500HV 半光沢:300~350HV |
450~600HV 焼入処理:800~1000HV |
膜厚 | 5~10μm程度 | 5~10μm程度(制御可能) |
コスト | 標準的 | やや高価 |
比較的精度が必要で、耐食性や硬度が必要な場合は、無電解ニッケルメッキを指定するのが良いと思います。
2.3 クロムメッキ
部品表面にクロムの被膜を析出させるメッキ処理です。
美観に優れた「装飾クロムメッキ」と、硬さに優れた「硬質クロムメッキ」が良く用いられます。耐食性や耐摩耗性に優れた高品質なメッキ処理で、光沢のある美しい外観が特徴です。
「装飾クロムメッキ」は、バフ研磨の後、ニッケルメッキを下地メッキとして、その上に薄いクロムメッキを施します。クロムメッキ自体は1μm未満と非常に薄いですが、装飾性と耐食性を兼ね備えた特性を得られます。鉄鋼、銅、ステンレス、アルミ合金など様々な材質に適用可能です。下地メッキと合わせて5~10μm程度の膜厚となります。
「硬質クロムメッキ」は、10~30μmと、厚い被膜を形成するメッキ処理です。
基本的にはメッキ前とメッキ後にバフ研磨を行い、装飾性も高い処理です。特に硬度と耐摩耗性が高く、シリンダ等の摺動部品によく用いられます。膜厚のコントロールは難しく、形状によっては被膜が薄いところと厚いところができてしまいますので、設計の際には注意が必要です。
環境への配慮から、徐々に六価クロムから三価クロムへの代替が進んでいるようです。
表2-3 クロムメッキの一般的な特性
項目 | 装飾クロムメッキ | 硬質クロムメッキ |
硬さ | 700HV | 800~1000HV |
膜厚 | 5~10μm(クロム被膜は1μm以下) | 10~30μm |
コスト | やや高価 | 高価 |
クロムメッキは、ややコストが上がっても硬度や耐摩耗性が必要な場合に選択すると良いと思います。
2.4 金メッキ
高い装飾性と優れた特性が得られるのが「金メッキ」です。
金は装飾性だけでなく、耐食性が高く、電気伝導性が良いなど優れた特性が得られます。
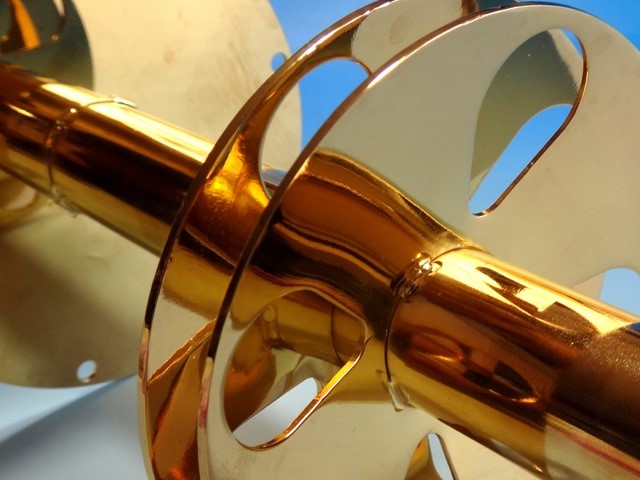
金メッキ例
装飾性を重視した「装飾金メッキ」と、機能性を重視した「工業用金メッキ」があります。装飾金メッキの中で、下地メッキ(主にニッケルメッキ)の上に0.1μm程度の薄い被膜をつける薄メッキ(フラッシュメッキ)が一般的です。5μm程度までの厚メッキもありますが、薄メッキと比較すると非常に高価となります。
工業用金メッキは、純度の高い純金メッキや、異種金属を混入して機能を付加した硬質金メッキがあります。
純金メッキは、電気伝導性やボンディング性などの金の優れた特性を利用してタッチプローブやコネクタなどに利用されます。
また、ニッケルやコバルトを混入することで、被膜を硬くし、摺動性や耐摩耗性を向上させる硬質金メッキなども用いられます。
金メッキは他のメッキと比較すると高価になりますので、装飾性や機能面で特にこだわりがある場合に選択すると良いと思います。
2.5 その他のメッキ
今回ご紹介した以外にも、銀メッキ、銅メッキ、錫メッキなど比較的多用されるメッキもあります。
四酸化鉄被膜(黒染めメッキ)や、溶融亜鉛メッキなど、以前は多く用いられてきたものの、メッキ業者が減少することで対応が難しくなってきている処理や、大量生産に向いていて多品種少量だと対応が難しい処理もあります。
また、各メッキ業者でオリジナルのメッキ処理を用意している場合もありますので、設計内容によりマッチしたメッキ処理を探求してみるのも良いのではないでしょうか。
3. 塗装の特徴と選び方のポイント
塗装は部品表面に塗料を密着させて、耐食性や装飾性を向上させます。特に製缶部品など、メッキ処理が困難な大物部品に多用されます。色や艶を任意に選択できるほか、ハンマートンやレザートンなど装飾性の高い処理も可能です。
一方で、膜厚のコントロールは難しく、導電性も期待できません。精度の要求される部位や、接合の合わせ面などは塗膜が乗らないように「マスキング処理」をします。基本的には精度要求の厳しくない部品や、外装用の表面処理と割り切って利用すると良いと思います。
スプレーガンや刷毛で塗料を塗布後、自然乾燥させるものと、高温の炉で焼く焼付塗装に分かれます。
「焼付塗装」は、塗膜の密着性が向上し、硬度が向上するため、設備部品でも積極的に利用されます。「メラミン樹脂焼付塗装」や「アクリル樹脂焼付塗装」が一般的に利用されます。「フッ素樹脂焼付塗装」、「シリコン樹脂焼付塗装」、「粉体塗装」などもあります。
また、自然乾燥では「ウレタン樹脂塗装」が良く利用されます。特に装置の躯体や、架台など大きくて焼付塗装用の炉に入らないものは、ウレタン樹脂塗装による自然乾燥で代替されます。
塗装を依頼する際には、「色」を指定することはもちろんですが、「艶あり」、「半艶」、「艶消し」など艶についても指定が必要です。艶の指定がない場合は、一般的には「半艶」で塗られることが多いようです。
「色」の指定には、「マンセル値」や「日塗工番号」等で具体的に指示するようにしましょう。目で見て色を決めたい場合は、塗料メーカーのカタログや、塗装業者の持つ「色見本」などで確認すると良いと思います。
取付面や摺動面、公差穴、ネジ部など塗装されたくない箇所があれば、図面等で範囲を図示し「塗装不可」などの指示をしてください。塗装不可の箇所には、マスキングなどにより塗料が塗布されないように処置することが可能です。
小物部品などは、穴形状などに吊り金具を挿して、吊った状態で塗装するのが一般的です。吊り部分付近には塗料が乗らない部分ができやすいので、吊り用の穴を敢えて別に設けるなどの工夫をするとスムーズな依頼ができると思います。逆に公差穴など、吊り用の穴として利用されたくない形状がある場合には、その旨を図面で明記してください。
また、一般的なスプレーガンによる塗料の塗布では、奥まった部分に均一に塗布することが難しい場合があります。このような場合は「静電塗装」などで、均一に塗装することができることもあります。塗装現場でどこまでの塗装が可能か、事前に確認しておくと良いと思います。
3.1 メラミン樹脂焼付塗装
塗料にメラミン樹脂を用いた焼付塗装です。
メラミン樹脂焼付塗装は低温で硬化し扱いやすく、様々な金属に塗装できるため、広く使われている塗装方法です。加熱温度は、アクリル樹脂焼付塗装よりも低温(150℃程度)です。
厚塗りも容易で、装飾性も高くメリットが多い反面、紫外線で劣化しやすいというデメリットもあります。長期間野外で使用する場合には、経年劣化により色褪せが発生する可能性があるため不向きです。
アクリル樹脂焼付塗装よりも安価です。後述のアクリル樹脂焼付塗装と比較した上でメリットが大きければ選択すると良いと思います。
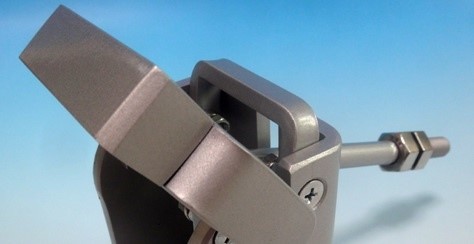
メラミン樹脂焼付塗装
3.2 アクリル樹脂焼付塗装
塗料にアクリル樹脂を用いた焼付塗装です。
アクリル樹脂焼付塗装はメラミン樹脂焼付塗装よりも高価ですが、メリットも多い方法となります。通常は、メラミン樹脂焼付塗装よりも高温(180℃前後)での加熱となります。メラミン樹脂焼付塗装に比べると、対候性や耐食性に優れています。特にメラミン樹脂焼付塗装で問題となる紫外線で劣化しやすいというデメリットはありませんので、屋外での使用などにも向いています。
また、メラミン樹脂焼付塗装と比べると、表面が硬くて傷が入りにくい、密着性が高く剥がれにくいというメリットもあります。アルミ素材の焼付塗装などにも用いられます。
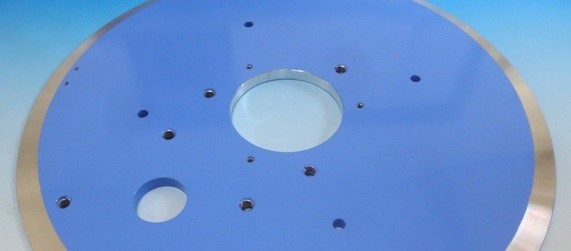
アクリル樹脂焼付塗装例 (アルミ部品・マスキング有り)
3.3 その他の焼付塗装
焼付塗装には他にも、フッ素樹脂焼付塗装、エポキシ樹脂焼付塗装、シリコン樹脂焼付塗装などが利用されます。
フッ素樹脂焼焼付塗装は、アクリル樹脂焼付塗装よりも対候性が高く、耐水性、耐薬品性などにも優れています。長期間の使用に耐えられる優れた塗装と言えますが、その分塗装費用も高価になります。
エポキシ樹脂焼付塗装は、高い密着性により剥がれにくく、加熱して硬化した際の寸法変化が小さいという特徴があります。防錆目的で大型構造物の塗装などに用いられます。太陽光で劣化するため、主に下地用の塗装として用いられるようです。
シリコン樹脂焼付塗装は、高い耐熱性が特徴です。調理器具などに利用されます。
3.4 ウレタン塗装
焼付塗装と異なり、常温での自然乾燥で硬化させる塗装方法です。
加熱しないため、金属だけでなく樹脂などの塗装にも用いることができます。焼付塗装と遜色のない仕上がりや、対候性が得られますが、硬化時間が長時間かかるため、埃などが付着するリスクがあります。焼付塗装用の炉に入らないような大物の製缶部品などに主に用いられます。
3.5 その他塗装
その他にも「ハンマートン塗装」や「レザートン塗装」など、塗装面に凹凸をつけた装飾性の高い塗装もあります。
ハンマートン塗装は、ハンマーで表面を無数に打ち付けたような模様を生じる塗装です。レザートン塗装は、皮革のような表面を得られる塗装です。
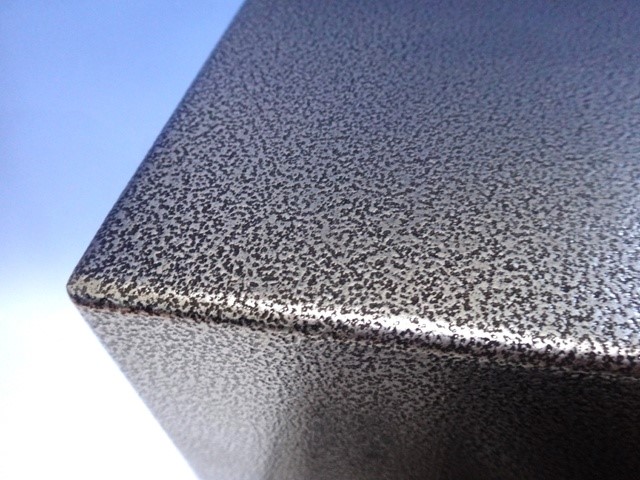
ハンマートン塗装
他にも、シボ塗装など様々な特色ある塗装手法がありますので、塗装でより特殊性を出したい場合はぜひ自分でも調べてみてください。
4. まとめ
今回は設備部品を考えるうえで重要な、「表面処理」について解説しました。
特に代表的な「メッキ」「塗装」にフォーカスしてご紹介してきました。これらは一般的に利用されている表面処理ですが、それぞれ特有の特性や注意ポイントがありますので、ぜひ要点を抑えて図面などの指示に盛り込んでいただければと思います。
部品の材質、大きさ、要求精度、表面処理の目的(防錆、装飾性など)、予算、数量等から最も適切な表面処理を決めてください。小物部品や寸法精度が必要なものはメッキ、製缶部品(躯体やカバー)等で大きなものは塗装を選択すると良いと思います。「膜厚」や「マスキング」の有無・箇所を明確に指示するようにしましょう。
また、表面処理は寸法の変化を伴いますので、図面中の寸法(特に公差部)が表面処理前なのか後なのかを明記することも重要です。注記などで「図面寸法は表面処理後の寸法を示す」などと記載しておくと良いと思います。
他にも本記事で触れた「バフ研磨」と「アルマイト」に加え、「化成処理」や「溶射」、「蒸着」などの処理方法などもありますので、興味があれば調べてみてください。
今回ご紹介したように、後から様々な特性を付加できるのが表面処理の良いところですね。安価な反面錆びやすいという欠点を持つ鉄系材料を活かす手段としても活用できます。
うまく使いこなして設計の幅を広げてください。
前の記事へ
次の記事へ