軸受けブラケットの悪い図面、良い図面
前回は特殊加工のうちレーザー加工できる板物の図面を使い、図面の改善点をビフォー・アフター形式で解説しました。
今回は板金プレス加工する薄板物の部品図に着目して解説します。薄板部品の特徴や製図のルールを理解しましょう。
meviy 2D|PDF図面アップロードで簡単操作
かんたん見積もりはこちらから >
目次
1)板金プレス加工の特徴
板金プレス加工とは、材料を金型に当てて圧力を加える加工のことです。「打ち抜き加工」「曲げ加工」「絞り加工」「圧縮加工」に分類でき、一般的に使われるのは「打ち抜き加工」と「曲げ加工」です。
打ち抜き加工(パンチング)
打ち抜き加工は、パンチ(凸型)とダイ(凹型)の間に板材を置き、パンチを上から下向きに打ち抜いて任意の形状に穴あけをする加工のことで、パンチングとも呼ばれます。一般的には、汎用金型である様々なサイズの丸穴や長穴、角穴用パンチを組み合わせて抜き形状を打ち抜きます。
汎用金型の形状以外にも、金型を専用に設計すれば様々な形状を打抜くことが可能です。専用設計した金型の例を示します(図5-1)。
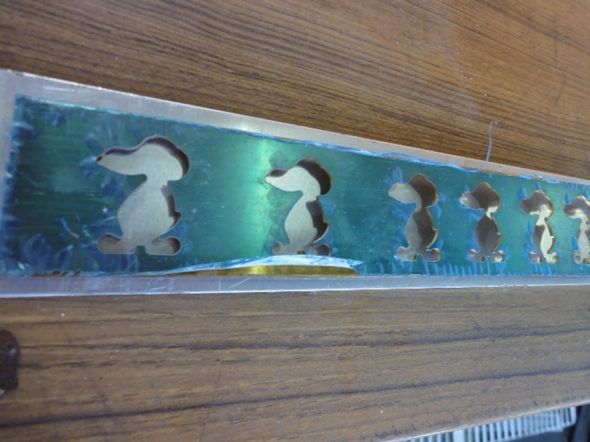
図5-1 専用金型(パンチとダイ)と打ち抜かれた後の穴
曲げ加工(ベンディング)
曲げ加工(ベンディング)とは、薄板材料をパンチとダイで挟み込み、加圧して曲げます。90°曲げが最も多く、曲げ回数が多いものは手順を決めて加工をする必要があります。
一般的に使われるプレスブレーキのパンチとダイ、作業の模式図を示します。バックゲージに板材を押し当てて加工の基準とします(図5-2)。
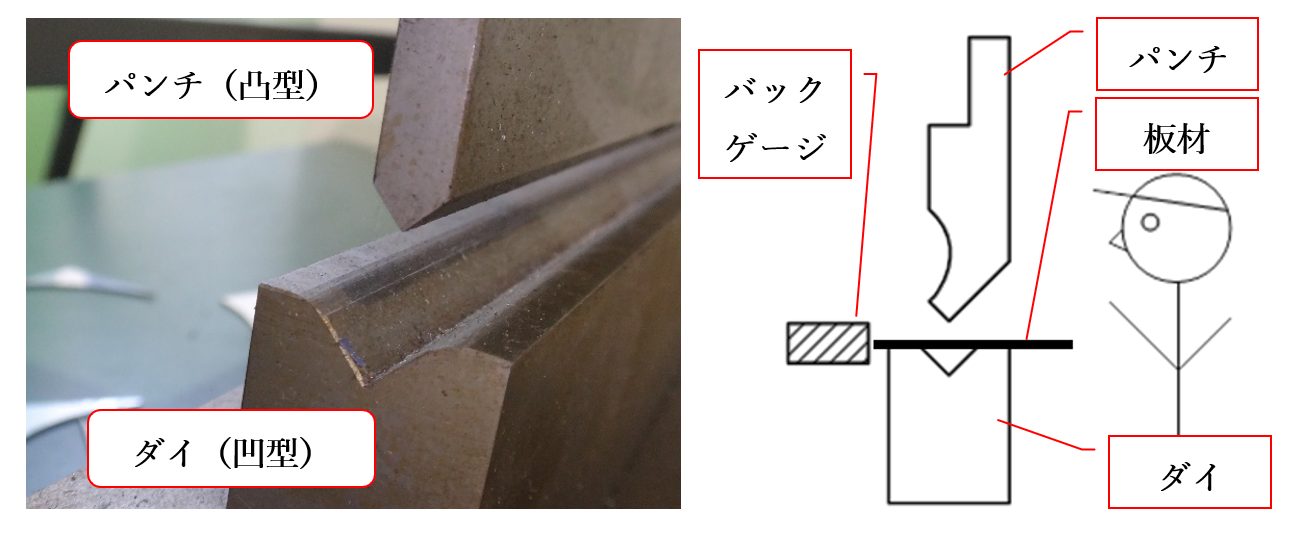
図5-2 プレスブレーキのパンチとダイ、作業の模式図
2)参考とする図面のビフォー・アフター(軸受ブラケットの例)
今回事例として取り上げる図面は、薄板板金をコの字形に加工した「軸受ブラケット」という名称の部品になります(図5-3)。
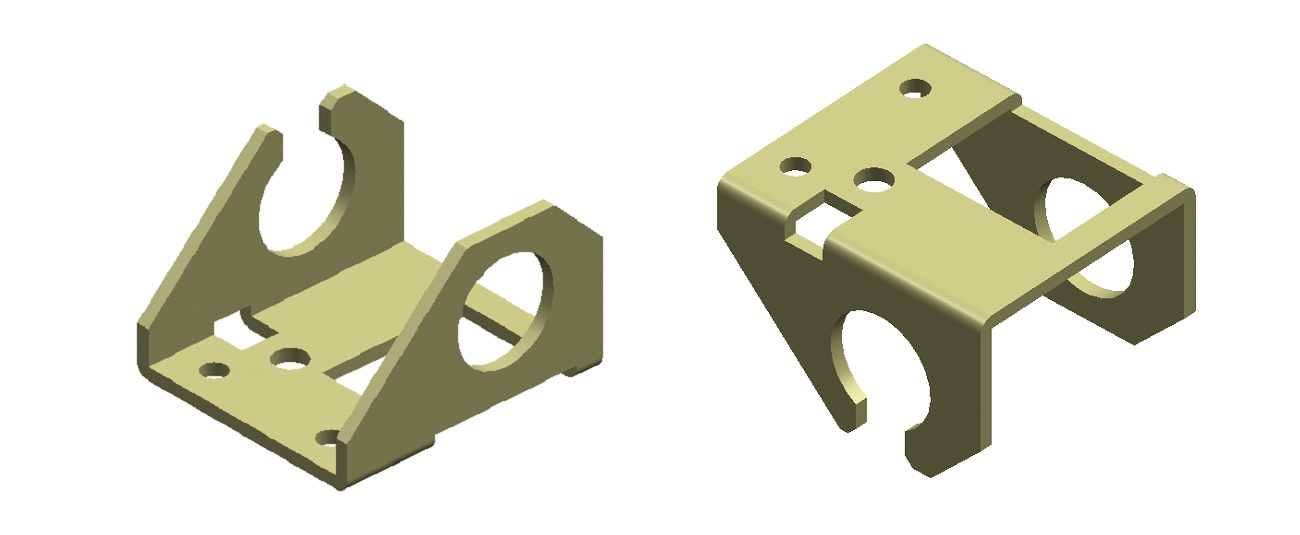
図5-3 軸受ブラケットの3Dモデル
軸受ブラケットのビフォー図面
それでは現状の軸受ブラケットの図面の悪さを、事実として列記していきます。
なお解説の前提条件として、下図における右側の図を正面図、左側の図を左側面図と呼びます(図5-4)。
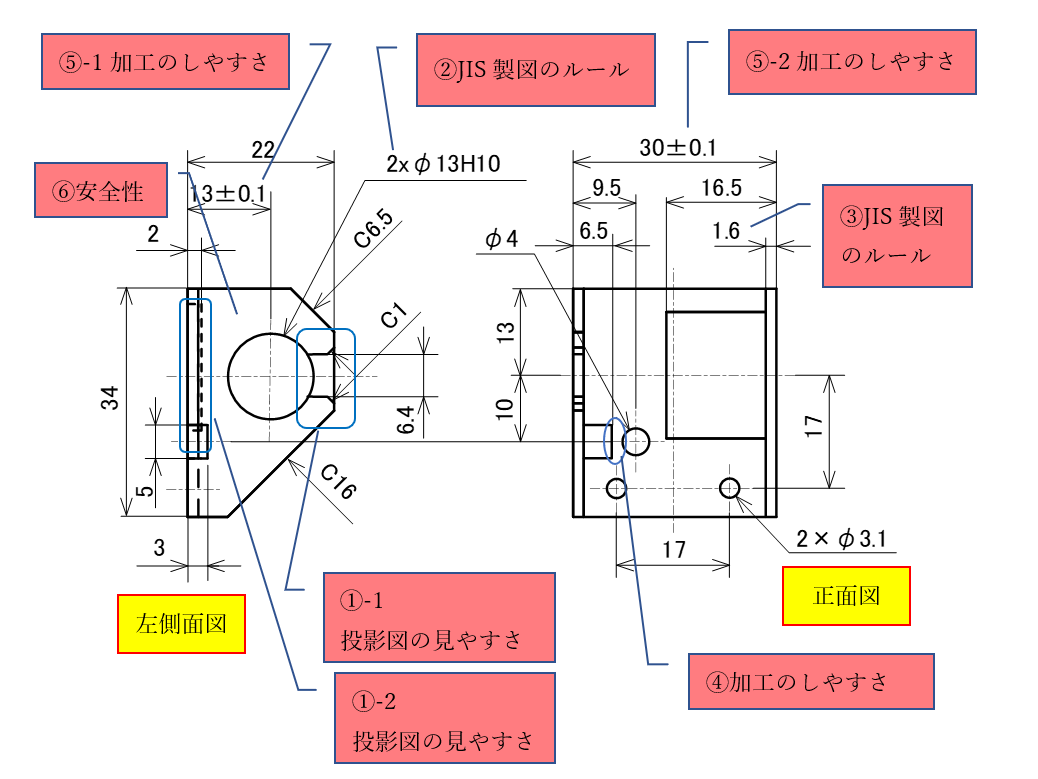
図5-4 軸受ブラケットのビフォー図面
① 投影図の重なり(投影図の見やすさ)
- 左側面の後ろに見える右側面の投影面が重なって描かれているため、理解が難しい図になっています。
- 右側面図と左側面図の抜き穴形状が違っており、右側面図の穴がかくれ線で描かれているため見づらくなっています。
② 一つの投影図で表記できる数(JIS製図のルール)
左側面には穴が1つしかありませんが、穴の個数を「2×φ13」として右側面の穴まで数に含めています。しかし、JIS製図のルールでは奥の面に見える穴の数までは数えません。
③ 板金部品の板厚表記(JIS製図のルール)
投影図に板の厚みを1.6と寸法線で指示しています。問題なく理解はできますが、材料を手配する際に板厚の寸法を探す必要があって時間がかかります。板金部品では寸法補助記号「t」を使用し、見やすい位置に表記することが一般的です。
④ 最小肉厚(加工のしやすさ)
丸穴と角穴の隙間の肉厚が、寸法から逆算(9.5-6.5-半径2)すると1mmしかありません。しかし、板厚が1.6mmであるためパンチで打ち抜いた際に穴の変形や破れが生じる可能性が高くなります。
⑤ 公差要求の難しさ(加工のしやすさ)
- 左側面図を見ると、左の端面から手前と奥の2つの穴の位置に公差がついています。これ自体は、加工的に問題がありませんが、⑤-2項で問題が生じます。
- 加えて正面図の曲げ幅にも公差がついています。
⑤-1と⑤-2の寸法と公差は、それぞれ独立して付与されているので問題ないように見えます。しかし、加工工程を知ると精度を出すことが難しい指示になっています。
⑥ 抜きダレ・カエリの考慮(安全性)
板金を打ち抜く際、材料の粘りによって“ダレ”と“カエリ(バリとも呼ぶ)”が相対する面に生じます(図5-5)。
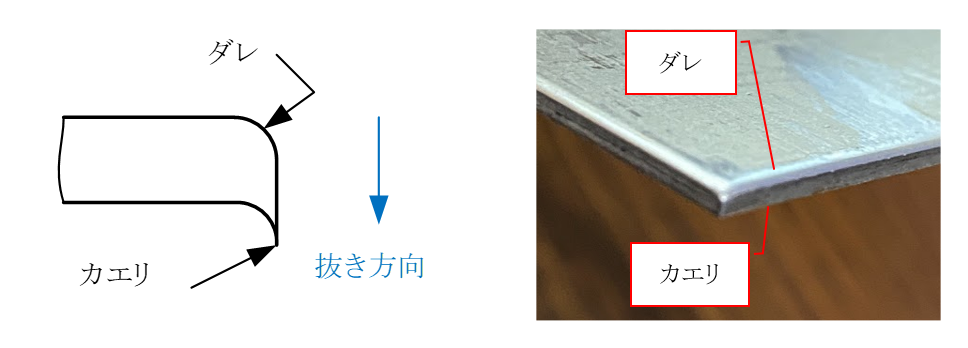
図5-5 打ち抜き加工によるダレとカエリ
カエリ面はシャープなエッジがあり、ここに接触すると怪我や配線の被覆が破れてショートするリスクが高くなります。逆にダレ面は丸みがついているため、接触による怪我や配線の被覆破れのリスクは低くなります。
軸受ブラケットのアフター図面
次に改善した図面例を確認しましょう。
なお解説の前提条件として、下図における中央の図を正面図、左側の図を左側面の部分投影図、右側の図を右側面の部分投影図と呼びます(図5-6)。
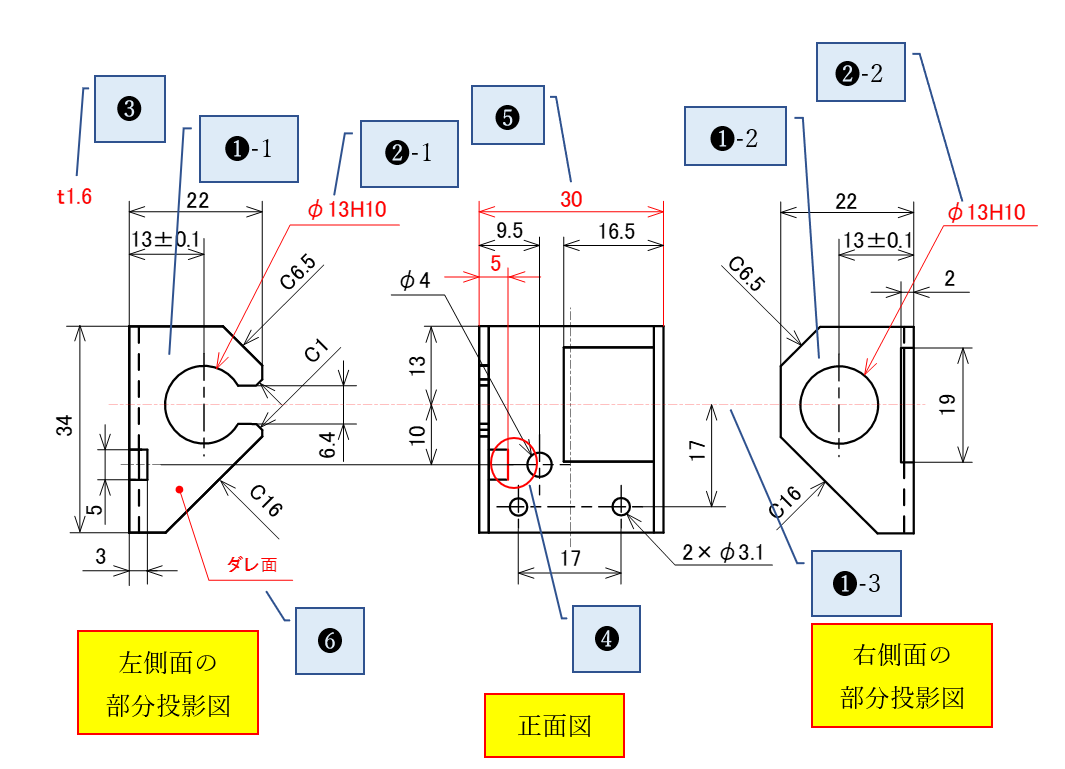
図5-6 軸受ブラケットのアフター図面
❶投影図の分散
- 左側面図の後ろに見える右側面の投影面が重なって見づらかったので、左側面に見える面だけを部分投影図として表現することで後ろに見える右側面を省略しました。
- 正面図右側に右側面に見える面だけを部分投影図として追加しました。❶-1と同様に部分投影図として表現することで、後ろに見える左側面を省略しています。
- 部分投影図の場合はJIS製図のルール上、主たる投影図と中心線(または細線)をつなぐことで関連性を示さなければいけません。
❷一つの投影図に見える穴の数
- JIS製図では、1つの投影図に見える穴の数しか指示できません。左側面の部分投影図に見える1つの穴の寸法だけを記入しました。
- 同様に、右側面の部分投影図に見える1つの穴の寸法だけを記入しました。
❸寸法補助記号を使った板厚の表記
投影図の近辺の見やすい位置に板厚として「t1.6」と単独で指示すると、一目で板厚を確認することができます。そのため、ビフォー図面の正面図右上にあった1.6の寸法線は削除しています。ちなみに記号「t」は、英語のthickness(厚み)の頭文字です。
❹打ち抜きの最小肉厚の確保
板金を打ち抜く場合、隣り合う穴は変形や破れを防止するために最低でも板厚の1~1.5倍以上の肉厚が必要です。丸穴と角穴の隙間を2.5mmになるよう角穴端面の位置を変更しました。
❺加工上の逃がし寸法の設定
曲げ部品の高さや幅のサイズ精度を要求する場合、展開した際に直列に配置される部分に公差を記入すると加工が難しくなります。
例えば、図5-7「直列する3つの部位に精度を要求した際の加工が難しい理由」の左側のような指示は、寸法精度を出すことが難しくなります。
曲げ加工前のブランクの展開長さには、打ち抜き加工によって±αのばらつきが生じます。そのため、寸法「50」と寸法「20」の3か所ともに高い寸法精度を狙いたくても、ばらつきαが邪魔をするためてすべての寸法精度を満足させることができません(図5-7)。
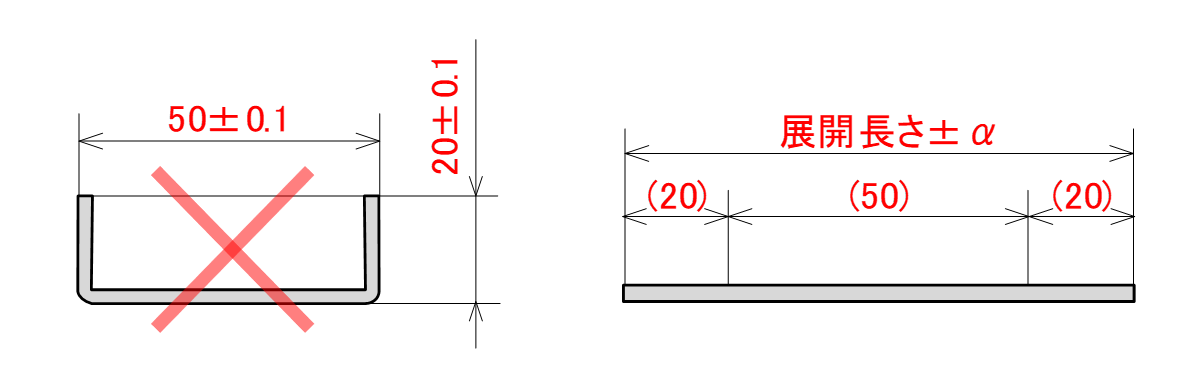
図5-7 直列する3つの部位に精度を要求した際の加工が難しい理由
板金加工においても、切削加工でいう“逃がし”の寸法が必要です。公差をどの部分に要求するかによって加工手順が変わります。
プレスブレーキの場合、板の端面を当てるバックゲージが加工基準となります。バックゲージへ当てる位置と順序によって、寸法精度が出せる場所と出せない場所が決まります。
両端の高さの寸法精度を要求する場合
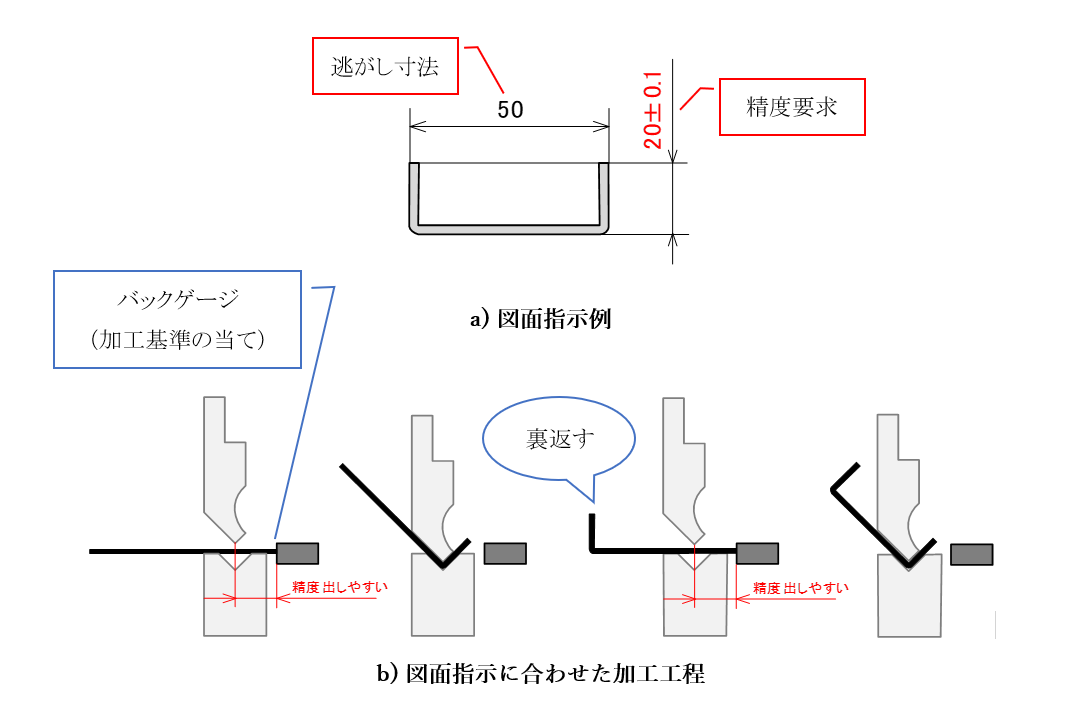
図5-8 両端の高さのサイズ公差を満足させるための曲げ順
① 展開長さの一端をバックゲージに当てることで、寸法「20」の精度が出るように曲げる
② 材料の向きを変えてもう一方の端面をバックゲージに当てることで、寸法「20」の精度が出るように曲げる
③ 最後に残った寸法「50」が、展開ばらつきを吸収する逃がし寸法となる
中央の長さの寸法精度を要求する場合
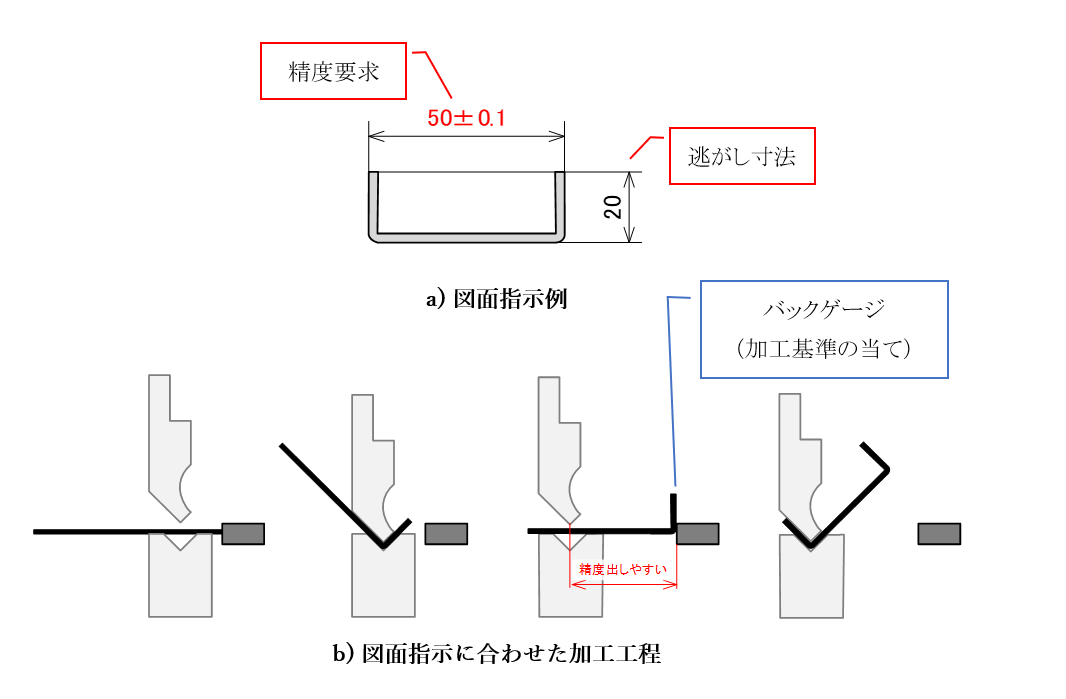
図5-9 曲げ幅のサイズ公差を満足させるための曲げ順
① 展開長さの一端をバックゲージに当てて寸法「20」を曲げる
② 曲げた面をバックゲージに当てることで、寸法「50」の精度が出るように曲げる
③ 最後に残った残りの寸法「20」が、展開ばらつきを吸収する逃がし寸法となる
プレスブレーキで、ブランクの端面をバックゲージに押し当てて板を曲げる工程を動画で確認してみましょう。
【プレスブレーキ】薄板を直角に曲げるよ!
バックゲージが加工基準となり、寸法精度を保証している様子がわかったと思います。
❻抜き方向の指示による安全性の保証
JIS製図には、打ち抜き方向を指示する記号は存在しません。そのため、注記として抜き方向がわかるように指示しました。
アフター図面では、「ダレ面」という引き出し線付きの注記で指示をしましたが、裏の面に指示するのであれば「カエリ面」という文言も使うことができます。
もし安全性の関係でカエリ面があっては許されない場合、注記として「全周のカエリ無きこと」「〇〇部はカエリ無きこと」のように指示するとよいでしょう。
3)投影法の間違い‐ワンポイントレッスン
板金図面に限りませんが、第三角法と第一角法を間違えて製図する人が散見されます。
万が一、投影法を間違えて作図しても製図の知識のある人であれば、第一角法で描かれていると違和感を持つため、誤って加工することはありません。なぜなら、第三角法でも第一角法でも正面図を見ると、曲げ部が紙面の手前に向かって立ち上がっていると判断できるからです(図5-10)。
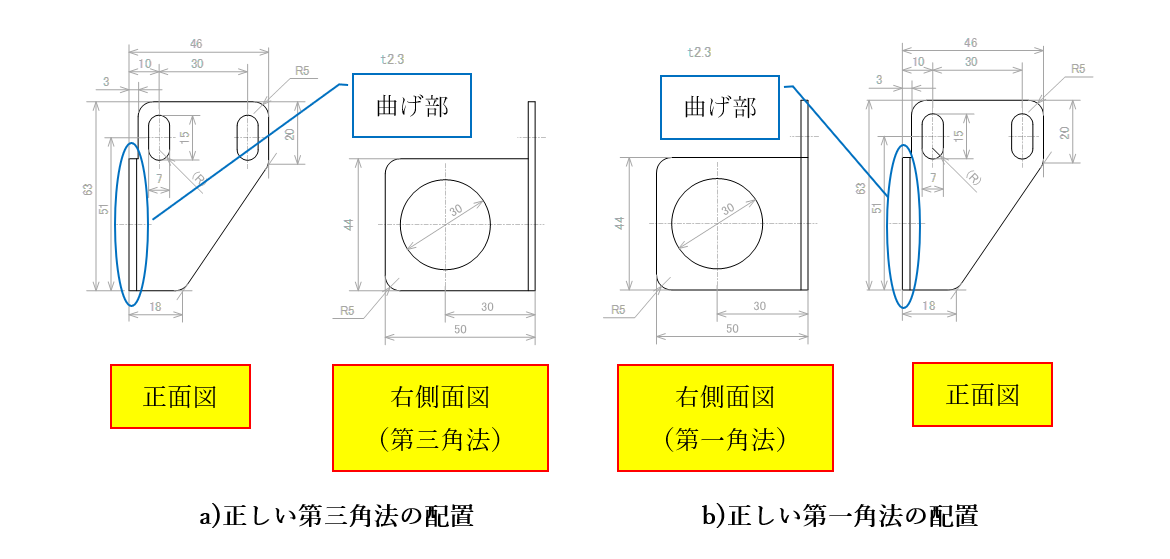
図5-10 投影法別の投影図の配置
しかし、加工者の思いこみによって形状を誤って判断してしまい、曲げ方向を間違えた部品を製作してしまうことがあります。
加工者が投影図を誤認する思考過程として、次のことが想定されます(図5-11)。
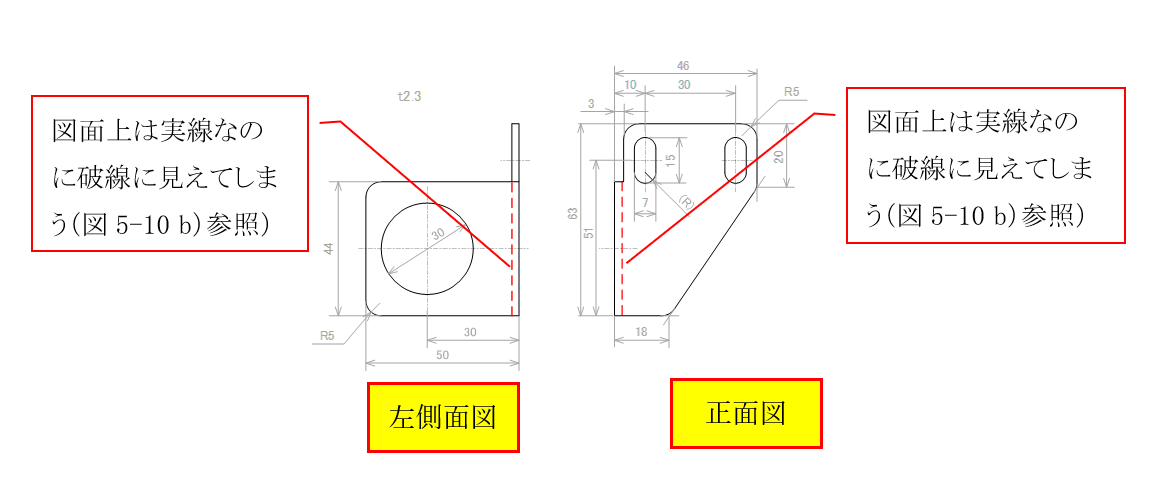
図5-11 勝手反対に曲げてしまう投影図の読み取り思考
|
板金部品の工程上、ブランク形状までは正しく製作したのに、最終工程で曲げる方向を間違える可能性があります。日本国内では第三角法を使用しますので、間違えないように気をつけてください。
※投影法に関するルールは、バックナンバー【温故知新!図面の本質と基本】投影図の⽬的と種類、選択肢から図面の本質を理解する をご確認ください。
まとめ
板金加工は切削加工に比べて、部品の形状精度(直角度や平行度など)と寸法精度(いわゆる寸法公差)を満足させることが難しく、比較的ばらつきの大きな部品ができ上がります。
また、抜き形状同士の最低肉厚などの制約や寸法精度を保証するための手順などが必要になります。
薄板板金用の寸法補助記号の使い方、JISには記号が存在しない抜き方向やカエリ方向の指示の仕方もわかりました。
今回で、テーマ「風林火山!製図の4つの心構え(見やすい投影図、加工の容易さ、関連する寸法、公差や粗さの使い方)」(全5本)は完結です。
テーマを通し、投影図を選択する際に加工のしやすさなどを考慮して向きを決定すること、寸法補助記号や表面の粗さ記号の使い方、寸法を記入する際のルールに加えて、加工の知識が必要であることを理解してもらえたと思います。
今回のシリーズの図例を参考にして、今後も設計製図を行う人は、加工しやすく読みやすい図面を提供することを心掛けてもらいたいと思います。
次回からは、板金プレスに特化したシリーズとして、板金部品を設計する際に必要な知識である材料の種類と加工法、形状設計テクニック、接合技術、べからず(禁止事項)集、寸法記入法などを解説します。ご期待ください!