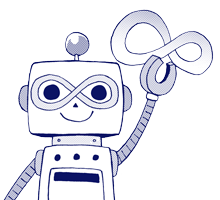
インフォメーション
meviyの新着情報、お客さま事例、役立つ連載記事などをお届けします。
上記のメニューよりお好みのページに移動してください。
新機能・製品情報
meviyの上手な使い方
-
【切削角物】熱処理サービス開始!高硬度部品を短納期でお届け (2025/05/12)
切削角物サービスにおいて熱処理サービスを開始いたしました。これにより対応領域が拡大し、高硬度部品の手配にも対応可能となりました。対象の材質は、SKD11、SCM...
-
プロジェクト共有機能で設計業務をもっと効率的に (2025/05/12)
2025年5月12日より、プロジェクトとフォルダを社内外のユーザーに共有できる「プロジェクト共有機能」が利用できるようになりました。 「複数人でのプロジェクト管...
-
meviy(メビー)のセキュリティ体制、安心して使える理由 (2025/04/16)
「部品の設計データは機密情報なので、アップロードするのが心配」 「設計データが外部流出したらどうしよう」 設計データを大切にする設計者だからこそ、meviy(メ...
-
まとめ買いでさらにお得!加工部品が最大70%OFFで購入できます (2025/03/27)
板金加工は21個以上で最大40%OFF、切削角物は21個以上で最大35%OFF、切削丸物は101個以上で最大70%OFFにてご提供します。 まとめ買いでさらにお...
メディア掲載情報
-
ソケット取り付け開始 板金溶接加工 漏れ試験対応
日刊産業新聞 (2025.03.27)
-
豊田自動織機、機械部品調達AIプラットフォーム「meviy」導入 工数を大幅削減
日本ネット経済新聞 (2025.03.25)
-
豊田自動織機、ミスミの機械部品調達支援サービス「meviy」を採用
LOGI-BIZ online (2025.03.24)
-
機械部品調達「メビー」/ミスミ、クリーン洗浄対応/板金部品/半導体・光学機器で需要
日刊産業新聞 (2025.03.24)
-
豊田自動織機、部品調達向けサービス「meviy」導入
ZDNet Japan (2025.03.21)
-
豊田自動織機、ミスミの部品調達AIシステム導入
LOGISTICS TODAY (2025.03.19)