みなさんこんにちは!
電通総研の金型ソリューションチーム“Mold Planner”です。
私たちは金型設計製造を行われている製造業のみなさまに、30年以上にわたりCAD/CAM/CAEなどのITツールをご提供し、業務改革をお手伝いしています。
今回は、多くの企業が抱えている「加工効率化」の課題をテーマにIT活用の視点でお伝えしていきます。
これからお話する内容は、次の通りです。
- ITを活用して加工効率化を実現する
- 加工効率化を実現ができない原因とその解決策
- まとめ
ITを活用して加工効率化を実現する
一般的に加工効率化の活動と聞くと、新しい工具を試したり、新しい段取り方法を考えたり現場で検討している様子を想像しますが、加工準備段階からITを活用することで加工を効率化できるアプローチも増えています。
そこで、加工効率化を実現できない原因を幾つか取り上げながら、解決可能なIT施策をご紹介していきます。
加工効率化を実現ができない原因とその解決策
加工効率化を実現できない原因は数多く存在しますが、分類すると3つに集約できるのではないでしょうか。【図1】
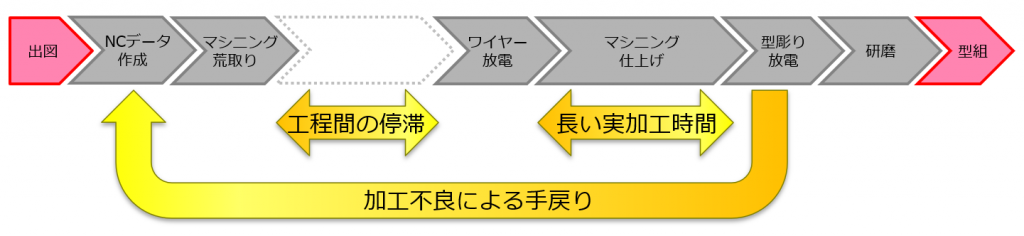
【図1】加工効率化を実現できない原因
- 工程間の停滞
- 長い実加工時間
- 加工不良による手戻り
それでは、この3つの原因を一つずつ確認していきましょう。
工程間の停滞
加工現場に並ぶ工作機の前にワークが置かれていますが、工作機が稼働していない場面をよく目にします。
工程間でワークが停滞している状態は、リードタイムを大きくロスすることになります。
その事象をなくすためには「NCデータ待ちの解消」「計画精度の向上」「段取りロスの低減」などが考えられますが、この事象を引き起こす要因が特定できない場合もあります。
「NCデータ待ちの解消」については第5回“3Dモデルの有効活用によるツールパス生成の効率化”、「計画精度の向上」については第8回“3Dモデルベースによる金型設計と工程管理の情報連携”にIT施策事例を記載していますので、ご一読ください。
段取りロスを低減するには、内段取りから外段取りへの変更や、ロボットによる段取り自動化などの設備による改善も有効ですが、ITを活用することで改善できることもあります。
通常、金型部品を製作する場合、バーチャル環境で「工程計画の立案」「NCデータ作成」などの加工準備を進め、リアルな現場で実際に加工します。
しかし、現場の進捗を考慮せずに工程計画を立案し、現場の最新設備と合致しないNCデータを作成しては、段取り時にロスが発生します。
例えば、CAM担当者が現場で利用できる工具を把握せずにNCデータを作成した場合、加工するタイミングで工具がないことに気が付き、その時点で工具を発注するか、在庫のある工具でNCデータを再作成するか、どちらにしても大きなロスとなります。
そのようなロスをなくすため、現場で利用できる工具とCAMの工具ライブラリを一致させる必要があります。
工具管理データベースにより現場の工具の在庫状態やロケーションを可視化し、その情報を元にNCデータを作成すれば、上記の事象を防ぐことができます。また、発注システムと連動させることで在庫切れを防ぐこともできます。
このように、リアル環境の正確な情報を利用し、バーチャル環境でシミュレーションを含めた加工準備を行うことで、手戻りを削減したものづくりを実現できます。
そのためには、工程計画、工具、加工条件、NCデータ、加工実績などの情報を紐づける必要があり、弊社では「工程管理データベース」「CAMデータベース(工具管理含む)」「加工実績データベース」を連携させるインテグレーションをご支援しています。【図2】
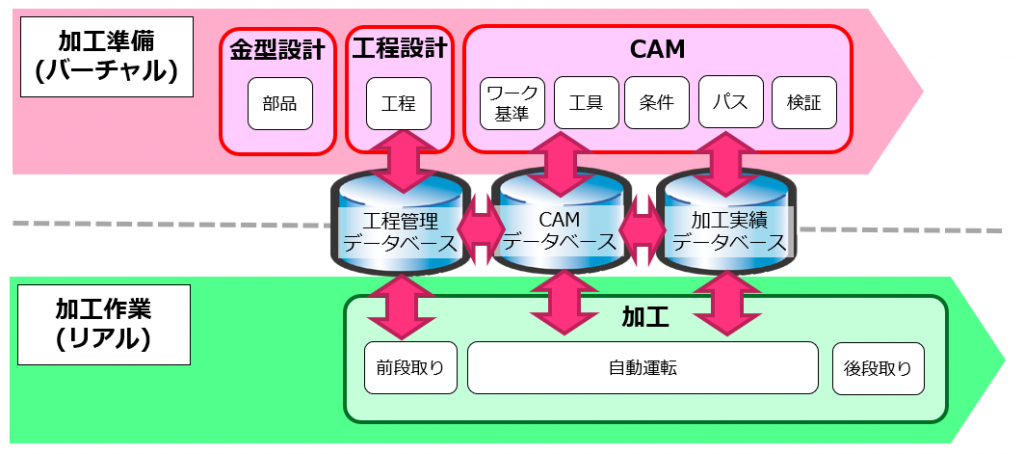
【図2】リアルとバーチャルを紐づけるデータベース連携
このように原因が明確になっていれば対策を立てられますが、そもそも何故停滞しているか分からないケースもあります。
最近では、工作機をネットワークに接続すれば、稼働状態の詳細な情報を容易にコントローラからPCへ取り込むソフトウェアがあります。
それらの情報を活用し、加工実績とアラームを突き合わせて分析すれば、チョコ停などの原因を可視化することができます。【図3】
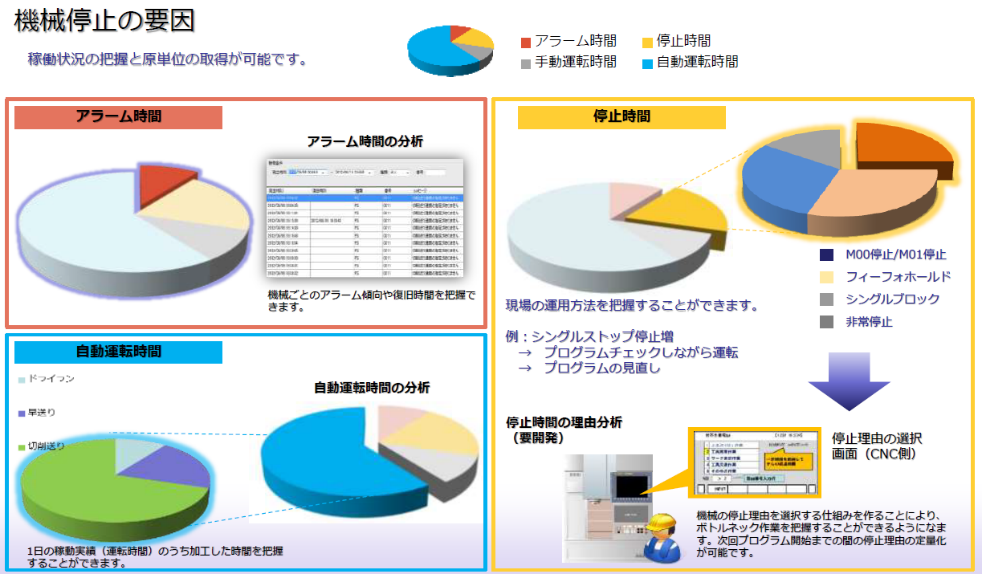
【図3】加工実績とアラームによる機械停止要因の分析 (出展:株式会社シーイーシー)
次は、自動運転などの実加工時間についてです。
長い実加工時間
金型製作リードタイムで最も高い割合を占めるのが、実際に加工している時間です。
このような段取りを除く、実際に加工している時間を「実加工時間」とし、この時間をいかに短縮することができるか掘り下げていきます。
実加工時間を短くするには、「1工程当たりの自動運転している加工時間を減らす」か「工程そのものをなくす」かのどちらかのアプローチになります。
自動運転する加工時間は、利用している工作機や工具などの設備とCAMが生成するNCデータによって決定します。
CAM担当者は、工作機の性能をフルに発揮できるようにNCデータを作成したいと考えていますが、CAM機能の制約により実現できていない場合もあります。
例えば、特定の加工形状に対するパスの動きにより部分的に切削体積が大きくなった場合、工具負荷が高くなり工具破損などの加工不良を起こします。
そのような事象を防ぐため安全をみて加工条件を下げて加工しているケースはないでしょうか。
工作機の性能をフルに発揮させるためには、最適な「パス(工具の動き)」と「加工条件」のアプローチが重要です。
パスの動きとして切削負荷の変動を抑えたパスを生成するため、CAMには様々な機能があります。【動画1】
【動画1】切削負荷の変動を抑えたパス
CAM選定をする際には、詳細にパスの動きを検証されることをお勧めします。また、最新CAMや切削シミュレーションでは、工具負荷に応じて「加工条件」を最適化する機能があります。
切削体積が大きい箇所は工具負荷がかからないように送り速度を落とし、工具負荷が少ない箇所は送り速度を上げることができ、結果、加工時間を短縮することができます。【動画2】
【動画2】工具負荷を考慮した送り速度最適化
今まで工具破損を恐れ、安全をみて設定してきた加工条件を最新CAMやシミュレーションにより「パス」と「加工条件」を最適化することで工作機の性能を十分に発揮できるNCデータを出力できるようになります。
また、実加工時間を更に短くするには、加工方法を見直し、工程集約することで効率化できます。
割り出し加工は多くの企業で実現されている工程集約の例だと思います。
先程お伝えしたように工具負荷がかからないような「パス」や「加工条件」であれば、工具突き出し長さを伸ばすことができ、今まで放電加工でしかできなかった凹形状をマシニングで加工することもできます。
元々放電していた箇所をマシニングで加工するため多少加工時間は長くなりますが、電極設計・電極加工・放電加工の工程をなくすことができる効果はご認識の通りです。
その他の工程集約として、できる限り磨き作業を減らすアプローチもあります。
製品意匠を鏡面仕上げするため、金型を磨く作業は手間がかかります。
磨き作業を短くするにはマシニングによる仕上げのパスが重要であり、NCデータの制御点出力に注目する必要があります。
CAMにより定義する加工オペレーション種類によって、計算処理方法を変えているものもあります。
荒取り加工は、計算時間を短縮するため対象形状を近似ポリゴンに変換してパスを生成し、高精度面を仕上げるには曲面形状に工具を接触させてパスを生成させることにより制御点を整列させ、滑らかな仕上がりを実現します。【図4】
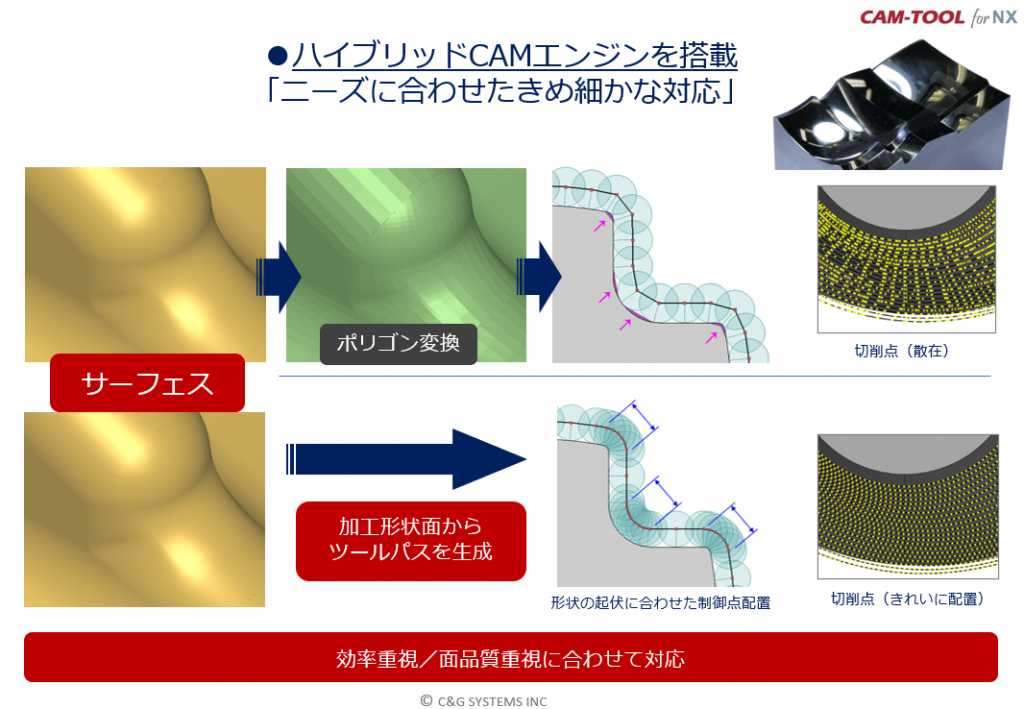
【図4】NCデータ制御点の整列
加工不良による手戻り
最後に、加工不良による手戻りについて掘り下げていきます。
加工不良を全くなくすことは困難なため、手戻りを最小限にするには、「工程内保証」のアプローチが重要です。
既に、3次元測定機を利用しながら工程内保証をされている企業も多いのではないでしょうか。
ただし、加工の間に3次元測定機により測定作業を挟むことは非常に手間であり、効率的に作業できなければ工程内保証の効果も薄れます。
測定作業を効率化するには、「3次元測定機のオフラインティーチング」や「機上測定」が有効です。
「3次元測定機のオフラインティーチング」については第6回“3Dモデルの有効活用による測定業務の効率化 ”に施策事例を記載していますので、ご一読ください。
3次元測定の作業が効率化できたとしても、測定結果がNGの場合、再加工するために工作機での再段取りが必要です。
以下のように、「機上測定」することができれば、測定作業だけではなく、問題発生時の修正再段取り作業を大幅に軽減することができます。【動画3】
【動画3】機上でのオフラインティーチング測定
また、加工不具合として最も多いのは、仕上がり寸法の誤差ではないでしょうか。
加工誤差の要因は様々ですが、仕上げの追い込み量と工具のたわみなどの影響が大きいのではないでしょうか。
もし、そのような要因が多いのであれば、機上測定を利用して残し代を確認した上で仕上げ加工することも重要です。
このような加工実績を積み重ねることで、個別に加工実験をすることなく、ノウハウを蓄積していくことができます。
まとめ
各社の「ものづくりノウハウ」を会社の資産として積み上げていくには、人材育成とITの活用が重要であることは、皆様のご認識の通りです。
弊社では、幅広くITを活用することで、多くの企業の「ものづくり革新」をお手伝いさせて頂いております。ご興味のある方は、ぜひ、「部品製造の効率化」ホームページにお立ち寄りください。
以上、ITを活用した加工効率化についてご紹介しました。
次回は、金型工場をITにより刷新するための活動の進め方についてお伝えさせて頂きたいと思います。
ぜひ、次回の記事をお楽しみに!