ここまでの回で、切削加工の特徴や工程、得意な形状や苦手な形状などについてフォーカスし解説してきました。
今回は、切削部品形状の効果的な設計のコツについてまとめます。8つのコツを詳しく解説した後には、一段上の設計ポイントについてもご紹介します。
過去の連載記事はこちらからご覧いただけます。
目次
1.切削加工の特徴を考慮した設計を考えよう!
これからご紹介していくポイントやコツは、製造現場目線からすると、最低限設計者さんに踏まえておいて欲しい基本事項でもあります。この点を押さえておけば、製造現場からも褒められることが増えるのではないでしょうか。
①工具は回転するものなので隅アールを意識しよう!
フライス系の切削加工の特徴は、何と言っても回転工具を使用することで生じる、隅アールです。
隅アールについては、以下の記事をご参照ください。
第3回 「隅アール」を理解しよう!
工具によって、3面壁に囲まれた隅部には、必ず1か所アール形状がつきます。この隅アールをどこに付けるのか、意識して設計しましょう。
例えば、図1-1のように6面体に窪みを付けた部品を設計したとしましょう。この形状は隅アールがどこにもついていないので、切削加工では製作不可能です。コストは高くなりますが、形彫放電加工等で製作可能です(それでもR0.2程度はつきます)。
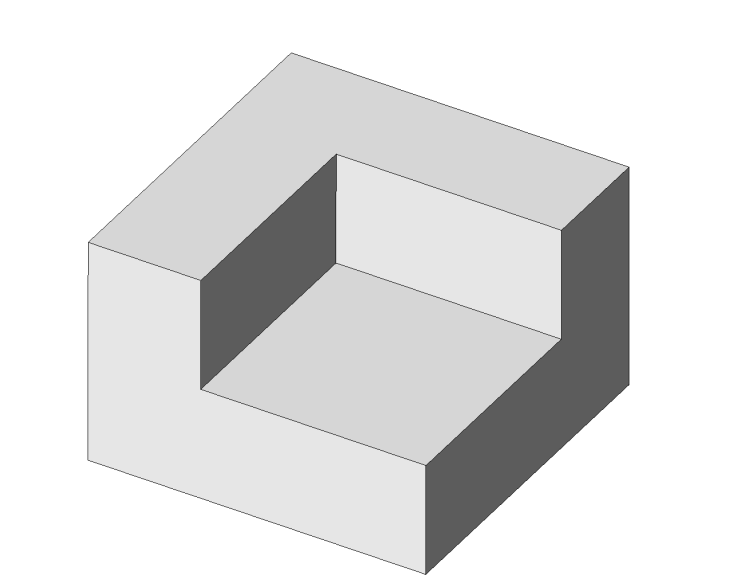
図1-1 設計NGの例(隅アールがない)
図1-2が隅アールの例です。このように、基本的にはどこか1辺にはアール形状が必要となります。
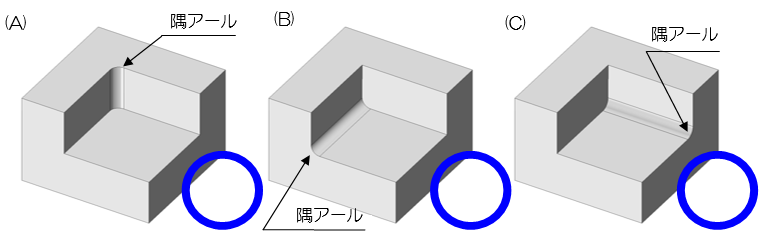
図1-2 隅アールの例
場合によっては、ニガシ形状を付けることも考えてみましょう。
例えば相手方の部品と組み合わさる場所で隅アールが許容されない場所などは、ニガシ形状を入れるのが一般的です。図1-3がニガシ形状の例です。
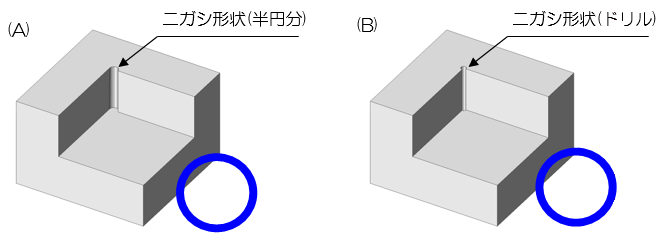
図1-3 ニガシ形状の例
一般的なのは(A)のように、エンドミルの半径分だけ切り込みを入れる方法ですね。更にニガシ形状を小さくしたい場合には、(B)のように小径のドリルによる穴あけを隅部分に入れるという選択肢もあります。
エンドミルによる加工は工具直径と加工の深さに制約を受けますが、ドリル加工はその制約が比較的緩いためです。
ただし、(B)の場合のニガシ形状は、窪みの底面よりも深くなりますのでご注意ください。
②深すぎる加工に注意しよう!
エンドミルの直径をD、突き出し量をLとした場合に、一般的にはL / D ≦ 5程度にしなければいけません。
あまりに細くて長いエンドミルで加工しようとすると、エンドミルが振れて加工面が綺麗に仕上がりません。それどころかエンドミルが折損して加工NGになったり、最悪の場合機械にダメージを与えたりすることにも繋がります。
エンドミルの直径は、隅アールの大きさによって決まります。隅アールがR5であれば、使用できるエンドミルの直径は最大でΦ10という具合ですね。
エンドミルの突き出し量は、加工する形状の深さによって決まります。突き出し量≒加工深さと考えていただければ結構です。ただし、隅アールの向きによって加工深さは変わりますので、ご注意ください。
図2-1の(A)は深さ50に対して隅アール4です。L/Dが5より大きくなりますので、隅アールが小さすぎて設計としてはNGです。(B)は隅アールをR5として、L/Dがちょうど5なので問題のない設計ですね。
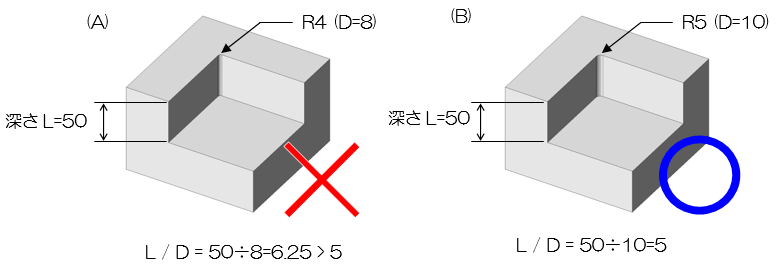
図2-1 隅アールの例1
図2-2は隅アールを付ける向きを変えた場合の例です。この場合は、隅アールの向きを変えたことで、加工深さが変わってしまいました。
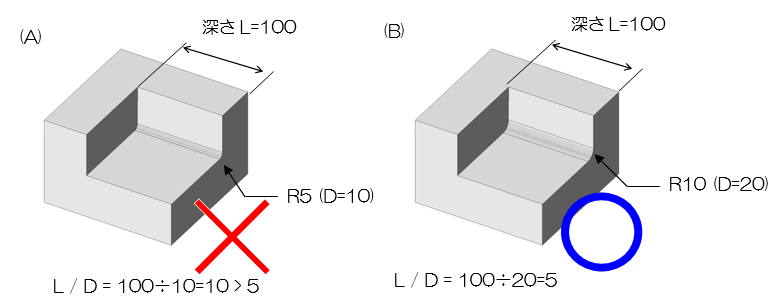
図2-2 隅アールの例2
(A)はR5にした場合ですが、図2-1と同じアールにしてもL/Dが大きくなりすぎて設計NGとなります。この場合は、深さが100mmになったのに合わせて、(B)のように隅Rも大きくするべきですね。
③段取り替えをなるべく減らす工夫をしよう!
比較的簡単な形状だと、切削加工で最も加工費や精度に影響を及ぼすのは、「段取り」になります。機械のオペレータが、ワークや工具をセットすることを段取りと言いましたね。
段取りについては、以下の記事をご参照ください。
第2回 切削加工を疑似体験してみよう(前編)
第2回 切削加工を疑似体験してみよう(後編)
切削加工は基本的に、エンドミルと正対する面しか加工できません。別の面を加工する場合には、ワークをひっくり返して改めて加工する面を工具に正対させる「段取り替え」が生じます。
加工する面が増えるほど、段取り替えの回数が増えて、加工費が増大します。例えば、図3-1の(A)と(B)を見比べてみましょう。
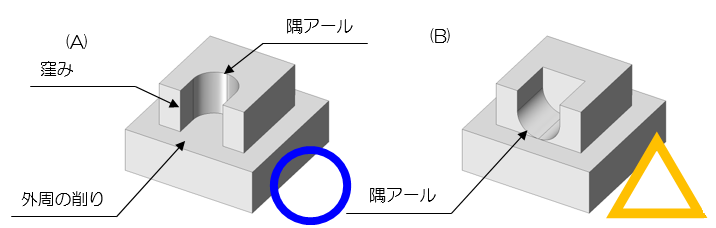
図3-1 加工の隅アールの付け方例
どちらも一見同じような形状に見えますが、隅アールを付ける方向が異なります。
(A)は外周の削りと窪みについた隅アールの向きが同じなので、1回の段取りで両方とも加工できます。
(B)は外周の削りと窪みについた隅アールの向きが異なりますので、段取り換えが必要になります。
一見同じように見える形状でも、隅アールの付け方で加工の工程に影響が出る例ですね。できる限り、加工の向きを揃えることで、段取り回数を減らすことを意識すると良いと思います。
どのような形状であれば段取り回数を減らせるか、という観点は忘れがちですが重要なポイントです。
④アンダーカットに注意しよう!
切削加工は、様々な形状を加工することができて、汎用性の高い加工手法です。その切削加工でも、加工できない形状の典型例がアンダーカットですね。エンドミルから見ると、加工すべき形状の手前にワークの一部が重なってしまう形状です。
アンダーカットについての詳細はこちらの記事をご参照ください。
第5回 切削加工の苦手なカタチとは?
図4-1が典型的なアンダーカット形状の例です。内面側の窪みを加工するには、手前の形状が壁になってエンドミルが届きません。このような形状は切削加工では加工不可能となります。
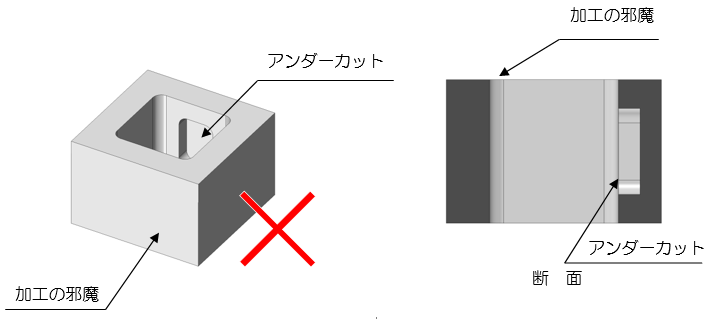
図4-1 アンダーカットの例
形彫放電加工や溶接を組み合わせる方法、3Dプリンタ等で造形する方法が考えられますが、多くの場合極端に製造コストが上がります。
このように製造側で工夫することもできますが、設計側で工夫することで解決できればそれに越したことはありません。
まず、本当にこの形状のアンダーカット形状が必要かどうかを考えていただきたいのです。もし設計変更の余地があれば、次のようなことを検討してみてください。
図4-2は設計変更の例です。
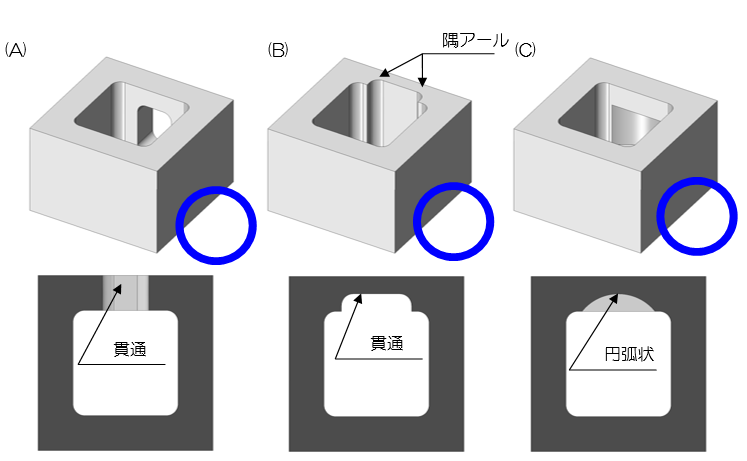
図4-2 アンダーカット形状の設計変更例1
(A)はアンダーカット形状をそのまま外側まで貫通させた形状です。こうすれば、外側からエンドミルで削ることができます。
(B)は上下方向に貫通させた形状です。これもエンドミルで加工可能ですが、前述のL/D≦5になるような隅Rが必要ですね。
(C)はアンダーカット形状を円弧状に変更した形状です。このような形状であれば、Tスロットカッターで加工できますね。ただし、製造現場で所有していないサイズだと、工具を新しく用意する必要が出てきます。
アンダーカット形状の変更ができない場合には、次のアイディアも考えてみましょう。
図4-3は、アンダーカット形状を変更せずに部品を製作するためのアイディアです。
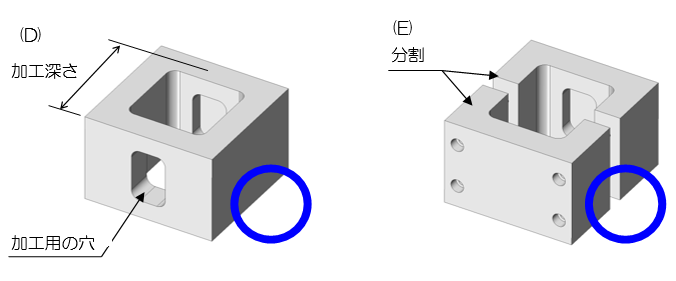
図4-3 アンダーカット形状の設計変更例2
(D)はアンダーカット形状を加工する際に邪魔になる手前の壁に、エンドミルを通すための穴をあけておく形状です。当然L/Dの制約を受けますので、加工深さと隅アールの関係には気を付けましょう。また、エンドミルを通す穴は、アンダーカットのポケット形状よりも一回り大きくしておくと良いですね。
このように、本来の部品の役割には必要ないけれど、形状を追加することで加工を容易とするような設計を、ここでは「加工フレンドリーな設計」と呼びます。加工フレンドリーな設計の他の例については、後述します。
(E)は部品を分割して、締結する方法ですね。部品数は多くなりますが、切削加工のみで製作可能で、結果的に製作費用を抑えられる場合もあります。精密な位置合わせが必要な場合は、位置決めピンを利用すると良いと思います。
アンダーカット形状があると、どうしても加工の難易度が上がってしまいます。ぜひ設計の際に、アンダーカット形状の要否について吟味してみてください。
⑤薄モノに注意しよう!
切削加工で注意が必要なのは、ワークの除去や固定による応力によって生じる変形ですね。特に薄モノの加工は変形が生じやすく注意が必要です。
薄モノ加工の変形についてはこちらの記事もご参照ください。
第6回 加工による変形に気を付けよう!
図5-1のように、加工深さが深く、薄い形状は注意が必要です。(A)のような形状を意図しても、(B)のように変形してしまいます。
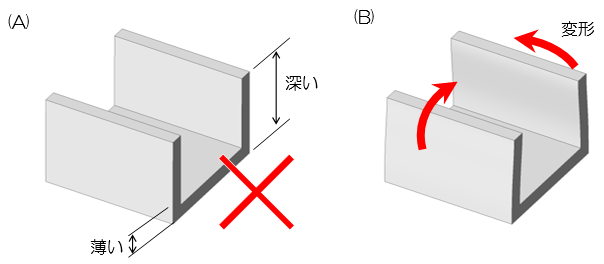
図5-1 薄モノ部品の例
加工の工夫により、できる限り変形を少なくすることはできますが、工数が大きくかかります。
歪み取りをしながら荒加工を何度も繰り返す、ワイヤーカットなど別な手法を組み合わせる、切削液や加工条件を変える、等と言った加工側の工夫が考えられます。ただ、加工側でいくら頑張っても変形をゼロにはできません。
やはり設計側で工夫する方が効果的であることは言うまでもありませんね。
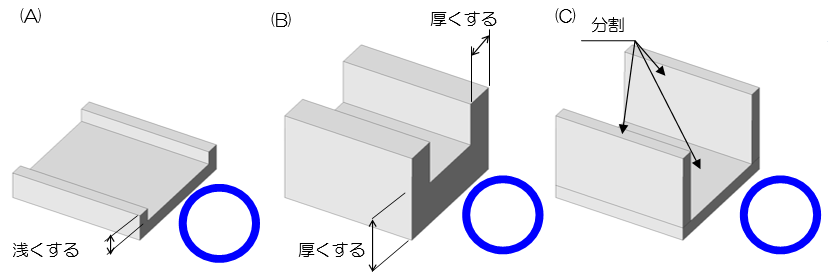
図5-2 薄モノ部品の設計変更例
(A)はなるべく全高を低くし、除去部分を浅くする変更例です。除去部分が少ない方が変形しにくくなりますね。
(B)は全体的に肉厚を厚くする変更例です。当然重量は嵩みますが、変形は抑えられます。
(C)は元の形状を維持しつつ、部品を分割して精度を確保する例です。強度の面などで設計上許容されれば、このように部品を分割して、ボルト等での締結としても良いのではないでしょうか。
⑥穴加工には余裕を持たせよう!
「穴」も意外とトラブルが多い加工です。特に「下穴」の存在を忘れがちだと思いますが、下穴をあけないとネジ穴などはあけられません。
穴加工については、こちらの記事もご参照ください。
第8回 穴加工の基本と設計のポイント
図6-1のように、下穴の考慮されていないネジ加工の図面をよく見かけます。ネジ加工やリーマ加工は、まず下穴をあけますし、工具の先端部分は完全な形には仕上がりません。
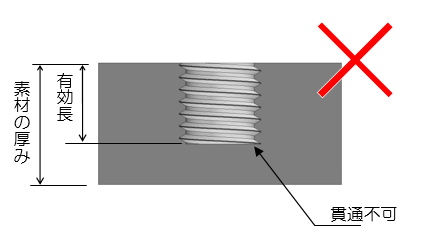
図6-1 ネジ設計のNG例
図6-1のような加工を実際にしようとすると、現実的には図6-2のいずれかを選ぶことになります。
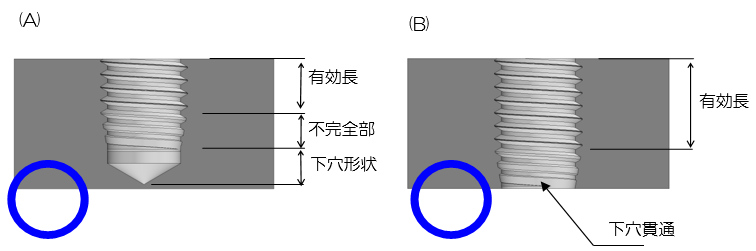
図6-2 実際のネジ加工
(A)は貫通しないギリギリの下穴深さでネジ加工する場合です。当然ネジの有効長は要求よりも短くなります。
(B)は有効長を優先した場合です。下穴や不完全部が反対側に貫通してしまいますね。
切削加工で穴をあける場合には、必ず下穴の存在を考慮に入れて、肉厚方向に余裕を持たせる設計が必要です。
特に気にしない場合は「下穴貫通可」等と図面に記載していただけると、加工現場も戸惑わずに済みますので親切ですね。
また、壁際に穴をあける際にも注意してください。特にネジ穴は壁際にあけようとすると、壁が盛り上がってしまいます。
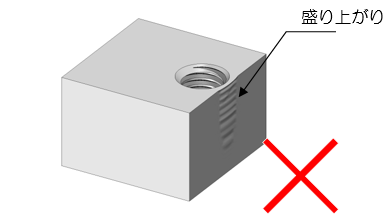
図6-3 壁際の穴加工の例
壁際とのクリアランスや穴同士のピッチにも余裕を持った設計を心掛けましょう。
⑦3次元形状は適切に指示しよう!
切削加工は平面や円弧などの幾何学的な形状だけでなく、自由曲面や複雑形状も作り出せることが魅力でもありますね。
特に高さ方向に対しても変化のある3次元形状加工は、設計者としても心惹かれるものがあるのではないでしょうか。
3次元加工についてはこちらの記事もご参照ください。
第4回 3次元加工の世界へようこそ!
3次元形状の加工は、基本的にボールエンドミルを使用します。平面的な形状を加工する場合と、ボールエンドミルで3次元形状を加工する場合では、加工時間が圧倒的に異なります。
何故ならば、ボールエンドミルの切削によって生じる段差(カスプハイト)が指示された表面粗さ以内に入るように、細かく形状をなぞるように動かさなければいけないからですね。
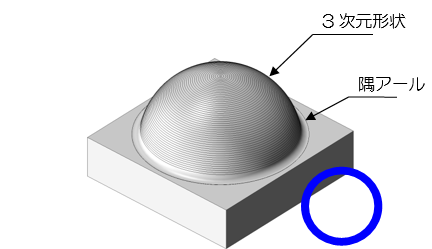
図7-1 3次元形状の例
加工側としては、ぜひ3次元形状を活用していただきたいと願っていますが、設計にあたってのポイントを踏まえておきましょう。
当然ボールエンドミルも回転工具ですので、隅アールが必要です。隅アールからエンドミルの直径が、部品の高さから突き出し量が決まります。
基本的には隅アールは許容される限り大きい方が、加工が楽になります。この時にも、L/D≦5の基本は忘れずにチェックしましょう。
もちろん、形状によってはこの隅アールの付ける向きによって加工難易度が変化します。隅アールの向きは常に意識して設計しましょう。
3次元形状面はボールエンドミルを細かくずらしながら加工していきます。
この時、3次元形状に指定された「表面粗さ」と、「ボールエンドミルの半径(R)」、「1加工あたりにずらす量(P)」との間に関係ができます。
それぞれ図7-2のような関係ですね。
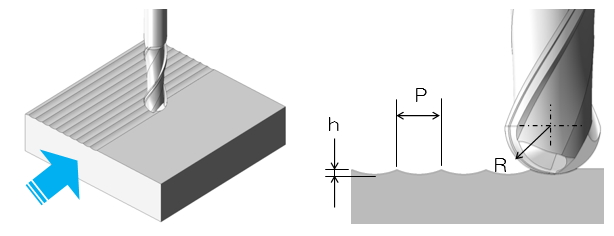
図7-2 加工条件とカスプハイト
近似式としては、h = P2 / ( 8 x R )です。
“h”はカスプハイトと呼ばれ、理論加工面粗さです。加工面粗さは、ピッチの2乗に比例し、エンドミルの半径に反比例する関係と言うことですね。
面粗さを小さく指定してしまうと、それだけピッチを細かく加工しなければいけません。ピッチが細かいと、それだけ加工時間が長くなりますので、加工賃が増大します。
3次元加工は、球体のような単純な形状だけでなく、図7-3のような複雑な形状も加工することができます。
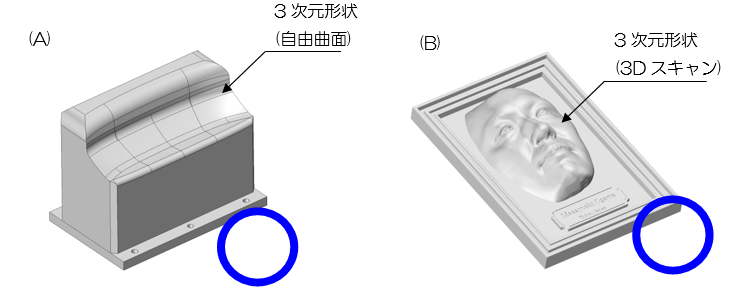
図7-3 3次元形状の例
ポイントを押さえながら、是非積極的に3次元加工もご活用いただきたいと思います。
⑧5軸加工を意識して設計の幅を広げよう!
現在のところ、最も進んだ切削加工の1つが「5軸加工」ですね。X、Y、Zの3軸に、ワークや主軸を回転させる2軸が加わって5軸加工となります。
1回の段取りで様々な方向から加工できるので、複雑形状や傾斜部を持つ部品の加工に威力を発揮します。
5軸加工についてはこちらの記事もご参照ください。
第7回 5軸加工を上手に活用しよう!
もし、設計しようとしている部品が、多方面からの加工が必要な形状であれば、積極的に5軸加工を活用してみるのも良いと思います。
例えば図8-1のように、それほど複雑でなくても、多面に加工が施されたような部品は、5軸加工だと段取り替えを省略できて低コストで製作できる可能性があります。
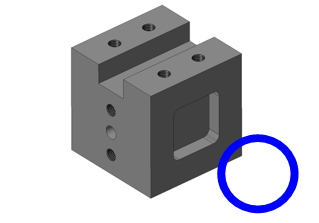
図8-1 多面形状の例
依頼しようとしている加工現場が5軸加工に対応しているならば、積極的に1部品に形状を集約して多機能な部品とするのも良いのではないでしょうか。
もちろん、図8-2のように傾斜面があったり、斜めからの穴が開いていたりするような複雑形状は、5軸加工が得意とするところです。

図8-2 5軸加工に向いた部品形状
もしこのような5軸加工部品を検討することがあれば、次のポイントを押さえておきましょう。
- 構造上、重切削に向いていない(場合により3軸加工機や旋盤との併用が必要)
- 加工機の大きさに対して、取り扱えるワークサイズが小さい
- 必ずしも加工精度が良いわけではない
- 加工賃は割高となりがち
- 必ず1面は加工できない部分があるため別工程での加工が必要
2.「切削加工フレンドリーな設計」で一段上の設計をしよう!
次にぜひ考えていただきたいのが、「加工フレンドリーな設計」です。つまり、加工の都合を考えて、段取りなどがしやすいように形状を工夫しておく、と言うことですね。
加工フレンドリーな設計は、次のようなものが考えられます。
- 加工困難箇所の加工を容易にするための付加的形状
- 平行出しや基準点出し用の付加的形状
- 固定用の付加的形状
① 加工困難箇所の加工を容易にするための工夫
前述の図4-3で示した、アンダーカット部加工用の穴のような例ですね。他にも、逆テーパ溝加工用の、カッターの出入り口なども、この部類に入ると思います。
逆テーパ溝は、Oリングなどを嵌めて相手方と密着させ、水密構造にするとき等に使いますね。逆テーパ溝の加工には、逆テーパエンドミルが必要になります。
逆テーパエンドミルは図9-1のような形をしています。刃が先端に行くほど広がっている面白い形状ですね。
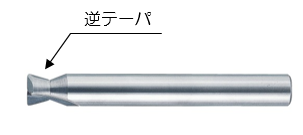
図9-1 逆テーパエンドミルの例
※参考:ミスミ SBTEM
このエンドミルで溝を掘ると、Oリング用の逆テーパ溝(いわゆるアリ溝)を作ることができます。
ただ、逆テーパになっているので、溝の入り口の方が狭くなります。逆テーパの溝だけの設計をしてしまうと、そもそもエンドミルが入らなくて加工できないのです。
このようなときに、図9-2のように、逆テーパエンドミルの出入り口を設計に盛り込んでいただきたいのです。こうすれば、エンドミルがここから入って、1周回った後に同じところから出ることができますね。
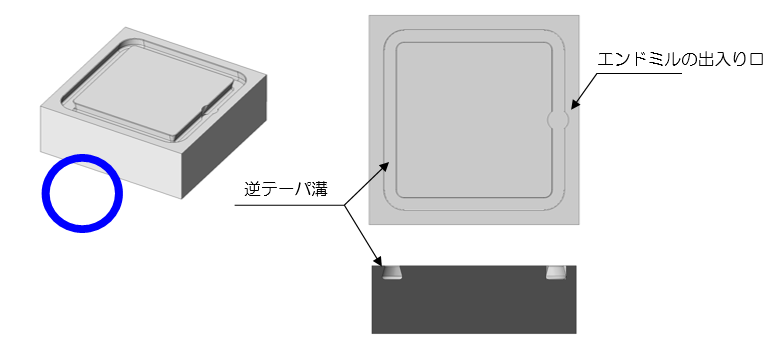
図9-2 逆テーパ溝の設計例
このような設計も「加工フレンドリーな設計」と言えると思います。
もちろん、幅の広い逆テーパ―溝であれば、細いエンドミルで外周側、内周側と削ることで、このような出入り口がなくても加工できる場合もあります。どの程度の溝幅であれば加工できるのか、加工現場に確認したり、エンドミルのリストを眺めたりして検討してください。
② 平行出しや基準点出し用の付加的形状
次に、(2)平行出しや基準点出し用の付加的形状の例についてもご紹介しましょう。複雑形状部品などでは、特に段取り替えをする際に、原点や平行出しをするための基準が必要となります。
例えば図9-3のような形状を考えてみましょう。底面以外は全て自由曲面で、横から穴が開いている形状です。
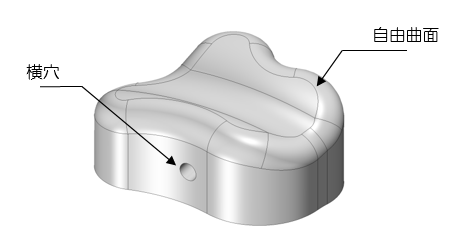
図9-3 基準が必要な形状例
こういった形状こそ5軸加工の出番なのですが、5軸加工機がない加工現場も多いと思いますので、通常のマシニングセンタ等の3軸機で加工する場合を考えましょう。
図9-4のように、1工程目で外形形状は加工できます。
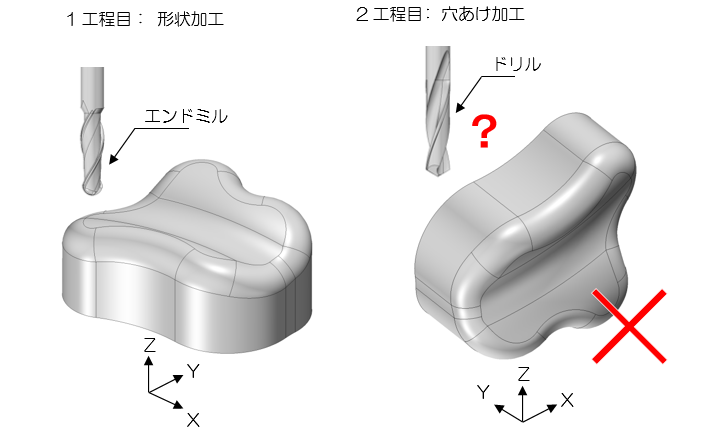
図9-4 加工段取り
横穴をあけるためには、一旦ワークの向きを変えて、段取り替えをします。(この場合はイケールと呼ばれるブロックに横向きに取り付けるイメージです)
この場合、段取り替えをして、原点の設定や平行出しをするための基準となる面がありません。この基準がないと、穴あけ加工するための正確な位置を割り出すことができませんね。
(注:このようなケースでも、ワークを取り付ける治具板で基準を取るなどの工夫はできます)
このようなとき、図9-5のように少しだけ平面を付加することで、段取り替えの際の基準面として活用でき、加工がスムーズになる場合があります。
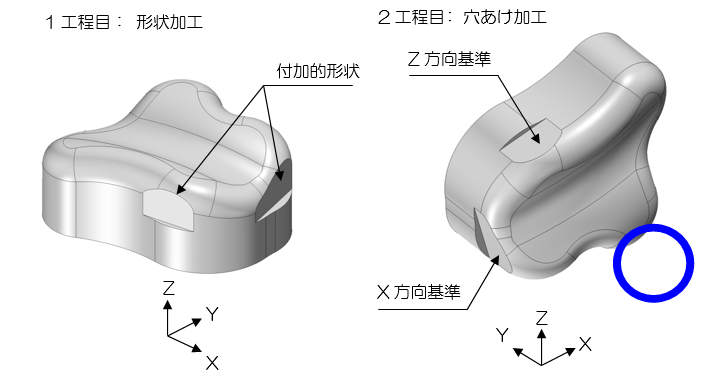
図9-5 形状改善例
1工程目で、この付加的形状も加工しておきます。そうすると、2工程目ではこの付加形状を、X方向、Z方向の基準として利用できるということですね。段取り替えの際の、平行出しや、原点の設定に利用することができます。
また、このような平面があると、3次元測定器等で寸法を測定する際にも利用できますね。もちろん、このような付加的形状は、平面だけでなく、穴や円柱(ボス形状)なども活用できます。
穴形状があれば、その中心位置を割り出せます。平面1つと、穴1つで、基準面と基準点を定義できますね。
本来の部品の用途からは必要ないけれど、形状を付加すると加工が楽になるという場合があると覚えておいてください。
③ 固定用の付加的形状
最後に、固定用の付加的形状の例をご紹介します。ワークを機械に固定する際には、いくつかスタンダードな方法があります。
- クランプ工具で固定する
- 精密バイスで固定する
- スクロールチャックで固定する(丸モノの場合)
- 治具板を利用する
大きくは上の4種類が良く用いられますね。
図9-6は(A)~(C)の固定例です。
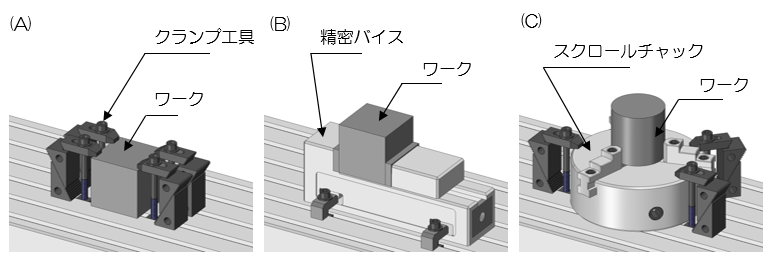
図9-6 ワークの固定例
(A)のクランプ工具は、加工面に直接クランプをかけますので、加工内容とクランプとの干渉がないように固定できるものに限られますね。
(B)の精密バイスは、ワークの下面側で固定ができます。ワークを挟む部分を「口金」と言いますが、口金を予めワークにフィットするように削っておけば、ある程度湾曲したようなワークでも固定することができます。
丸モノの場合は精密バイスの代わりに、(C)のようなスクロールチャックを利用することが多いですね。外形が丸いと、中心位置を割り出し易いので、段取りもしやすい場合があります。
設計上形状的付加を伴う可能性のある固定方法が、(D)の治具板を使用する方法です。もし底面にネジ穴を付加しても構わないような場合は、積極的に検討しても良いのではないでしょうか。
図9-7が典型的な治具板の例です。決まったピッチでザグリ穴が並んでいるような板ですね。
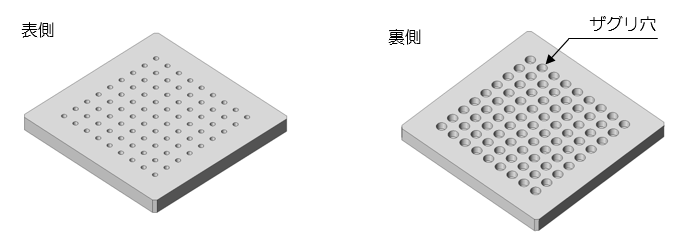
図9-7 治具板の例
裏側からキャップボルトなどでワークを固定できるようになっています。
どの加工現場でもこのような治具板を汎用的に活用していると思いますので、見かけたこともあるのではないでしょうか。このような治具板に取り付けられるような穴をワークに付加しておけば、簡単に固定できるようになります。
例えば、図9-8のように、ワークの底面に治具板の規格に合ったネジ穴をあけておくわけですね。
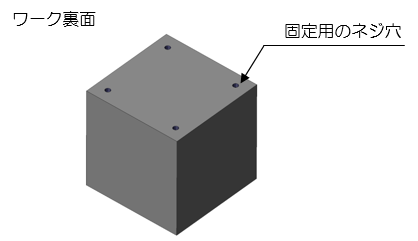
図9-8 治具板固定用の穴あけ
そうすると、図9-9にように、クランプ工具などで治具板ごとワークを固定することができます。
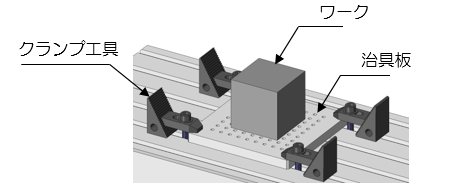
図9-9 治具板によるワークの固定
ワークの側面を下まで加工する場合などは、バイスなどが使えないケースもありますので、このような治具板を活用する方法が多く採られます。
このような治具板固定用の追加的な穴も、加工フレンドリーな設計の例と言えます。他にも色々と加工フレンドリーな設計はあると思いますが、まずは以上の事を踏まえておけば基本事項としては十分だと思います。
ぜひ、加工サイドの事情まで汲み取った「加工フレンドリーな設計」を心掛けてみてください。
3.固定できなくても切削加工の手段はある!
最後に、切削加工の奥の手とも言うべき加工方法をご紹介します。
基本的に切削加工は、固まりから不要な部分を除去して、必要な形状を削り出す加工です。したがって、6面体や円筒形状が基本となりますね。
ただ、切削加工はこのような形状だけではなく、様々な形状を造り出せる可能性を秘めています。例えば、以前ご紹介したこの形状はどうでしょうか?
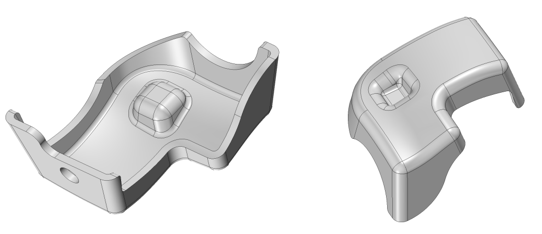
図10-1 薄肉形状の例
一見すると、全体的に曲面や傾斜面ばかりで、基準となるような面や穴もなさそうです。こういった部品は航空機部品などでも多いですね。
このような形状は切削加工“できます”!
切削加工にける最終手段は、「ジョイント」の追加です。図12-2のように、ワークをグルっと囲めるようなフレーム状の形状を定義し、そのフレームとワークとの間を繋げるようなジョイント形状を追加します。
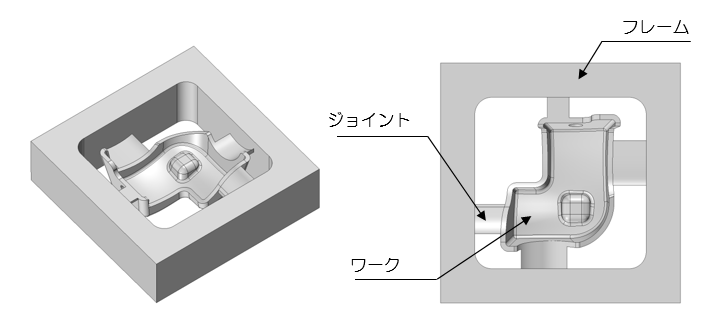
図10-2 ジョイントの追加例
プラモデルの部品のようですね。こうすることで、表面を加工したら、裏返して加工することで削り出すことが可能になります。加工の原点や平行出し用の基準面は、フレームの側面などを使うことができますね。
ジョイントの削り残し部分は、通常は鋸などを用いてハンドワークで切除します。その後もヤスリなどハンドワークで仕上げます。
精度よくジョイントを除去したい場合には、ジョイント除去用の治具を作成して、NC加工により高精度に仕上げることもできます。
例えば、ジョイント除去用の治具は図10-3のようなものです。ちょうどワークの内側を転写した形状ですね。
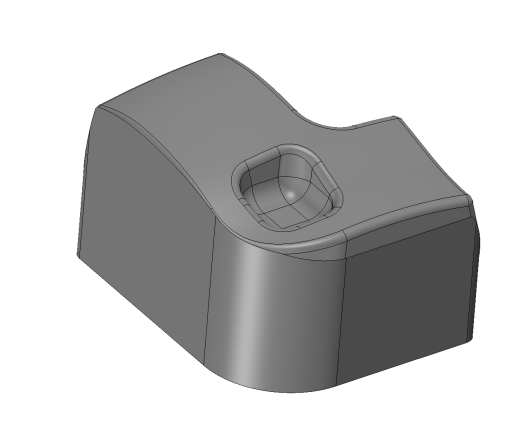
図10-3 ジョイント除去用治具の例
このような治具は、3D CADですぐに設計できますね。
図10-4が実際のジョイント除去加工のイメージです。
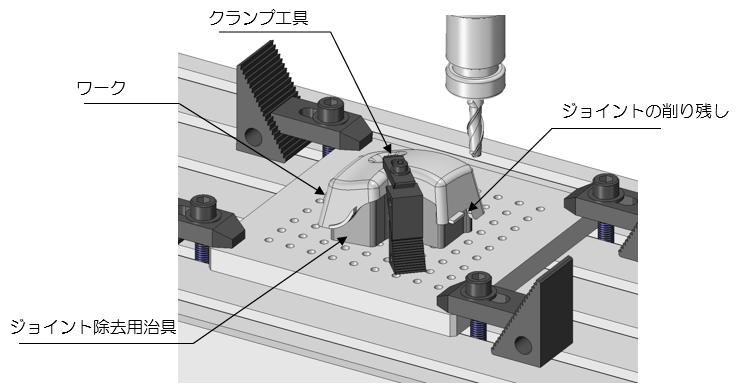
図10-4 ジョイント除去加工
ジョイント除去用の治具にワークを嵌めて、クランプ工具で押さえています。ジョイント除去用のNCプログラムを作成して、NC加工により3次元的に加工可能となります。
もちろん、実際にはいくつかの制約がありますが、場合によってはこのような形状も加工可能です。
ただし、ご覧いただいた通り、非常に工程が多くなり、その分工期もコストも増大することを覚えておいてください。
4.まとめ
いかがでしょうか、今回までで切削加工部品の形状設計に関するポイントとコツをご紹介してきました。
次のようなことについてぜひ意識した設計を心掛けてみてください。
- 工具は回転するもの→隅アールを意識する
- 深すぎる加工に注意する
- 段取り替えをなるべく減らす工夫をする
- アンダーカットに注意する
- 薄モノに注意する
- 穴加工には余裕を持たせる
- 3次元形状は適切に指示する
- 5軸加工を意識して設計の幅を広げる
- 加工フレンドリーな設計で一段上の設計をする
- 固定できなくても加工手段はある
上記のようなポイントを押さえて設計していただければ、大抵の形状は問題なく切削加工できるはずです。加工精度を高め、製作コストも抑えることに繋がりますし、何より製造現場からも大いに褒められることでしょう。
ぜひこれらの設計の秘訣を常に頭に浮かべながら、機械加工部品の設計をしていただければと思います。